Work in Process Inventory – What Is WIP and How To Calculate it?
We have all seen manufacturing depicted in cartoons. Basic resources are rolled into a factory, followed by loud noises and a smoking chimney. Then, shiny finished products emerge on the other side. In reality, manufacturing is a bit more complex. On their journey toward becoming final products, raw materials go through work in process inventory. In this post, we look at what WIP is and how to account for it.
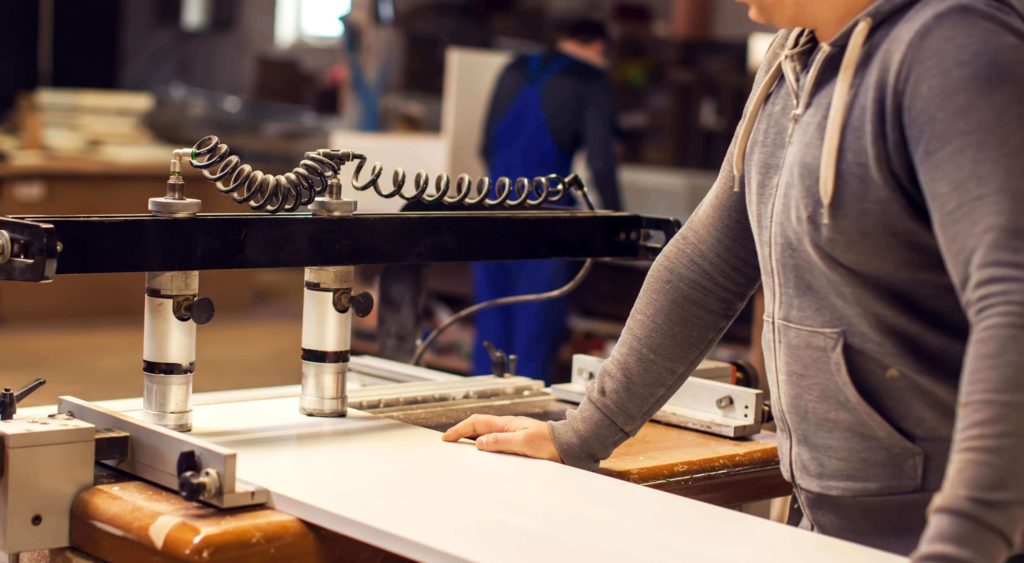
You can also listen to this article:
What is Work in Process (WIP)?
Work in process (WIP), sometimes called work in progress, is a type of inventory that lies in the manufacturing pipeline between the raw materials and finished goods inventories. In other words, WIP is the part of a company’s overall inventory that has begun being processed but is not yet finished. In accounting, WIP is an asset and designates the value of unfinished goods at the end of a financial period.
Having control over your WIP inventory is critical for two main reasons:
- Firstly, when raw materials and components are consumed and transformed in manufacturing processes, they gain value by incurring labor and overhead costs. Due to this, WIP inventory has some separate accounting considerations, tracking WIP value is crucial for a company’s financial health.
- Secondly, the processing of raw materials throughout a product’s routing transforms them into new components and sub-assemblies. These items can follow complex paths through the shop floor and undergo many processes, managing and keeping track of which is a must.
Work In Process accounting
As the name implies, WIP inventory accounting involves keeping track of the costs of unfinished goods as they move through the production process. WIP is considered a current asset in the company’s balance sheet and represents the total value of all materials, labor, and overhead of the unfinished products.
WIP essentially consists of three cost articles:
- All of the raw materials that are used in unfinished manufacturing orders become part of the WIP inventory. Their value includes the actual cost of the materials, as well as any freight or duties incurred with procuring them.
- All direct labor costs accumulated in the manufacturing process are also included. These are comprised of the wages and salaries of all employees involved directly in the production process like machine operators, skilled workers, etc., who personally handle the products.
- Finally, manufacturing overhead costs count toward the WIP account. These are all indirect costs related to manufacturing the unfinished goods, such as wages of supervisors, utilities, upkeep, insurance, depreciation, etc. Only the overheads directly related to the unfinished goods count towards WIP value. The manufacturing overhead is calculated based on an hourly rate, or in some proportion to labor costs. In either case, the rate must be obtained using financial analysis.
The WIP account is updated on a regular basis, typically at the end of each accounting period or within preset intervals like monthly, quarterly, or biannually. Or, it can be automatically kept up to date by using manufacturing software like an MRP system.
Ideally, companies strive toward minimizing or altogether nullifying the WIP Inventory at the end of a financial period. This is because inflated WIP ties up capital and may inflate the tax burden. It’s also simply good practice to keep WIP inventory as slim and optimized as possible for overall inventory management.
How to calculate WIP?
The periodical WIP inventory calculation is informed by three important accounting metrics. These are the beginning WIP inventory value, the total manufacturing cost, and the cost of manufactured goods, also known as COGM.
These calculations are valid for the periodic inventory method, and not needed in the perpetual inventory method, where the costs of individual products and unfinished production (i.e., WIP) are tracked continuously. Whatever the case, it is useful to understand how they are related.
Beginning WIP inventory
The beginning work-in-process inventory represents the value of all unfinished goods at the beginning of the new accounting period. In other words, it is the WIP asset section of the balance sheet of the previous accounting period.
To differentiate between different financial periods, the WIP inventory value for the current period is sometimes also called the ending work-in-process inventory.
Manufacturing cost
Total manufacturing cost represents the total costs of all manufacturing activities for a financial period. It is calculated as the sum of the total costs of raw materials, labor, and overheads used in manufacturing for the period.
Total manufacturing cost is an invaluable KPI for measuring the profitability of a business and can offer a quick insight into whether to set a higher selling price.
Total manufacturing cost = direct materials + direct labor + manufacturing overhead
Cost of goods manufactured
The cost of goods manufactured, or COGM, is a crucial KPI for manufacturers that measures the total expenses incurred from manufacturing the finished products completed in this financial period.
The COGM calculation takes the total manufacturing cost as a baseline, adds in the cost of unfinished goods from the previous period (i.e., the beginning WIP inventory) that were finished in the current period, and deducts the cost of all manufacturing jobs still unfinished at the end of the financial period.
COGM = beginning WIP inventory + total manufacturing cost – ending WIP inventory
The work-in-process inventory formula
All in all, the WIP inventory calculation looks like this:
Ending WIP inventory = Beginning WIP inventory + Total Manufacturing Cost – COGM
You might have noticed a discrepancy in the above calculation: the ending WIP inventory value seems to be required to calculate COGM, which is required to calculate the ending WIP inventory.
This is why, when doing periodic inventory, it may be desirable to first finish all manufacturing orders so the ending WIP would be zero. Otherwise, the ending WIP must be calculated manually by looking up all incurred costs for the unfinished production, or by using standard costs based on the stage of the goods’ completion. Either of these methods may be a lot of work.
In practice, advanced manufacturers find the COGM and ending WIP values based on real data from their production management system. COGM is found by tallying up the real costs from manufacturing orders as calculated or estimated by the production management tool, whether it’s MRP/ERP software, spreadsheets, or a pen-and-paper approach. The accountant can then compare the real-world data with the financial metrics to make sure everything checks out.
Calculating WIP precisely can be difficult, particularly for more complex manufacturing setups. Workloads are rarely uniform from period to period, save for Make-to-Stock (MTS) or mass producers with very stable demand. This is why production management software and traceability tools can go a long way in accurately measuring difficult metrics like the percentage of manufacturing overhead costs applicable to in-process jobs.
Learn more about perpetual and periodic inventory systems.
Why is WIP accounting important?
Understandably, all companies need to be focused on their cash flow and overall financial health. While larger companies can absorb a few more errors due to scale and averaging, small and medium-sized companies often have little to no room for error. Here are five reasons why accurate WIP accounting is a must, regardless of company size.
- Production Impact. An inaccurate WIP account can lead to production errors and bad inventory levels. If WIP is incorrectly valued, it can send the wrong demand signal to procurement. They might order more materials than necessary, thus tying up cash flow with overstock and congesting the warehouse. Or they might order fewer materials than required, driving up production costs with extra overhead due to concurrent stoppages, etc.
- Cash flow and financing. Many companies, especially SMEs, use short-term financing, including WIP Inventory Financing, to address short-term cash flow issues. Applying for this type of financing requires accurate WIP accounting and valuation. Inconsistencies in the WIP valuation may lead to the discontinuation of the financing agreement. It goes without saying that all of a company’s financials need to be in shipshape also when applying for longer-term loans.
- Financial reporting. Accurate accounting is also important for financial reporting, and WIP is a crucial part of the balance sheet. Accurate WIP accounting provides a clear picture of a company’s financial health and sends the right message to investors, lenders, and stakeholders.
- Compliance. Manufacturers must accurately report the cost of goods sold (COGS) and all inventory values, including WIP, to comply with tax regulations and meet requirements like the Generally Accepted Accounting Principles (GAAP). Failure to comply with these regulations can result in penalties, fines, audits, and other legal consequences.
- Taxation. As a current asset, WIP may be a taxable entity. Inaccuracies in accounting can lead to a host of issues and unwanted attention. Underestimating WIP in accounting can result in hefty fines. Overestimating it, on the other hand, can be equally detrimental as it creates unnecessarily high tax responsibilities.
Managing and tracking WIP inventory
To end this article, let’s take a look at why effectively managing and keeping WIP inventory as slim as possible is also good from a production and inventory management viewpoint.
One of the central tenets of inventory optimization is maintaining the right stock levels at all times. This also holds true for WIP inventory. If it grows too large, extra storage space needs to be allocated. This can congest the shop floor, complexify routings, and introduce extra costs due to needless transportation. If WIP is too small, bottlenecks and stoppages arise, stretching lead times.
WIP inventory should be kept at “just the right size” – big enough to ensure consecutive processes can flow optimally and small enough to avoid it piling up and tying up extra cash. To achieve this, WIP needs to be continuously managed and tracked throughout the manufacturing process. Designing optimized storage and shop floor layouts and considering WIP inventory volumes already in the production planning phase is also a must.
Managing WIP inventory with manufacturing software
WIP inventory is usually calculated periodically or at the end of the financial year for accounting purposes. While this ensures balanced books, it doesn’t go a long way toward actual control over the WIP inventory throughout the manufacturing process.
Tracking the status of in-process goods and work orders is crucial to ensure efficient production processes and optimal stock levels. Doing this with spreadsheets or pen-and-paper is possible for very small or simple operations. However, a much more comprehensive solution for companies of any size lies in manufacturing software.
The chief advantage of these systems lies in unified access to real-time production data. Manufacturing software continually tracks the location, status, and progress of all work processes, automatically aggregates material, labor, and overhead costs, and allocates them to individual manufacturing orders. This enables deep insight into the actual cost of each product and helps to spot bottlenecks and identify areas for cost reductions and workflow optimizations.
Key Takeaways
- WIP or work-in-process inventory is the part of a company’s overall inventory that has begun being processed but is not yet finished.
- Managing WIP inventory is crucial for two chief reasons. Firstly, as raw materials are processed, they incur added labor and overhead costs, which need consideration from an accounting point of view. Secondly, WIP inventory can quickly grow too large and accrue needless costs if not properly controlled and optimized.
- WIP inventory accounting involves keeping track of the costs of unfinished goods as they move through the production process. WIP is considered a current asset in the company’s balance sheet and represents the total value of all materials, labor, and overhead of the unfinished products.
- WIP inventory can be calculated by adding together the values of raw materials, labor, and overhead applicable to unfinished goods.
- Manufacturing software is essential for efficiently managing and tracking the status and location of in-process goods, calculating their real costs, and helping to keep WIP at just the right size.
Frequently Asked Questions
WIP stands for work in process and is used to refer to the manufacturing term work in process inventory. WIP may also abbreviate to work-in-progress inventory but the two phrases are generally used intermittently in manufacturing and accounting.
WIP inventory constitutes all materials that work has started on that are not yet finished in manufacturing operations. The goods are no longer raw materials as they have accrued labor and overheads, but neither are they finished goods yet. Thence the name – work in process. In accounting, WIP is an asset designating the combined value of all unfinished goods.
In accounting, the value of WIP inventory for a financial period is calculated by adding together the beginning WIP inventory (the value of unfinished goods at the beginning of the period) and the total manufacturing cost (the total cost of all raw materials, labor, and overhead used in manufacturing), and then subtracting the cost of goods manufactured, or COGM (the total value of all finished goods).
Let’s say your company produces tables. Your raw materials inventory consists of table legs, varnish, and tabletops. When a manufacturing order comes in and a forklift driver is sent to fetch the table legs and tabletops, these materials become part of the WIP inventory because they have met with labor. Next, the assembled table is sent to varnishing, whereupon the required amount of varnish also becomes part of WIP, along with the now assembled table. The value of the WIP inventory consists of the values of raw materials, labor, and manufacturing overhead costs accrued within manufacturing it until the table is finished and ready for shipment.
You may also like: Inventory Valuation Methods – Finding the Right Approach