What is Reorder Point and Reorder Point Formula?
Keeping optimal stock levels in order to avoid stockouts is an integral task of inventory management. One of the most fundamental ways in which to ensure this is setting and maintaining the right reorder points.
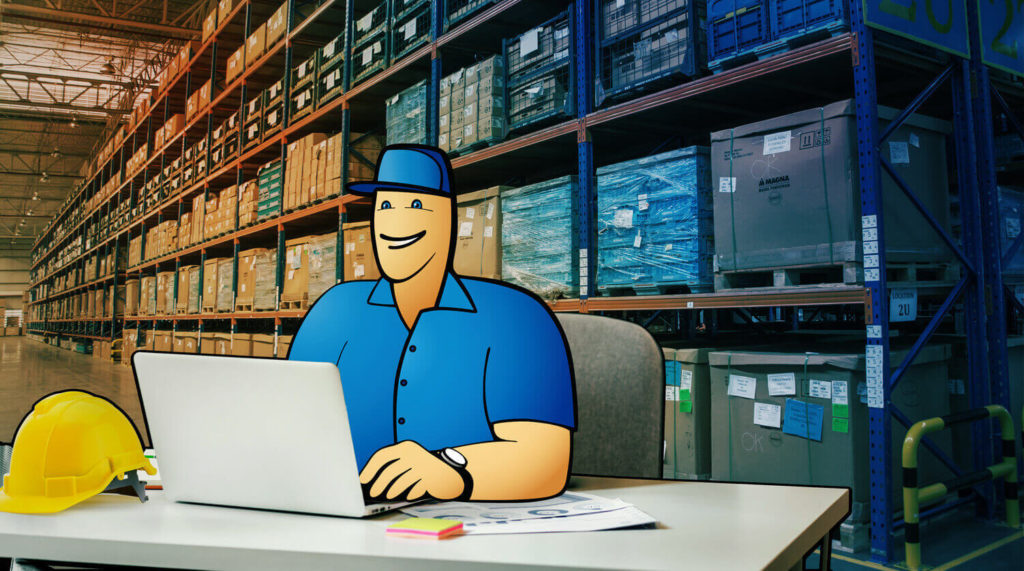
You can also listen to this article:
What is a reorder point (ROP)?
A reorder point, or ROP indicates an inventory item’s minimum stock level at which new stock should be ordered in order to avoid a stockout. In other words, the reorder point is the lowest number of units of an SKU that a company needs to have in stock to make sure it can keep fulfilling orders. ROP is a function of quantity over time. It can thus also be viewed as the last time to replenish stock to avoid a stockout.
ROPs are always calculated separately for each individual item. The calculation consists of an item’s delivery time, demand or consumption rate, and, if applicable, its safety stock level. Since all of these are dynamic variables, the ROP of an item can vary greatly depending on changes in the supply chain, market circumstances, selected suppliers, etc. The ROP model is based on analyzing historical consumption and lead time data to predict consumption rates.
Reorder points can be calculated and maintained using pen and paper or spreadsheets programs like Excel. However, modern inventory management systems usually have various degrees of ROP functionality built-in that automatically trigger parts of the stock replenishment process. Modern solutions often use ROPs in conjunction with constraints management and other advanced forecasting methods, enabling deeper insights into stock consumption.
The reorder point formula and calculation
The basic formula for calculating a reorder point is quite straightforward:
Reorder point = (lead time x demand rate) + safety stock
To get a better grasp on the ROP model, let us look at the individual parts that make up the formula in a bit more detail.
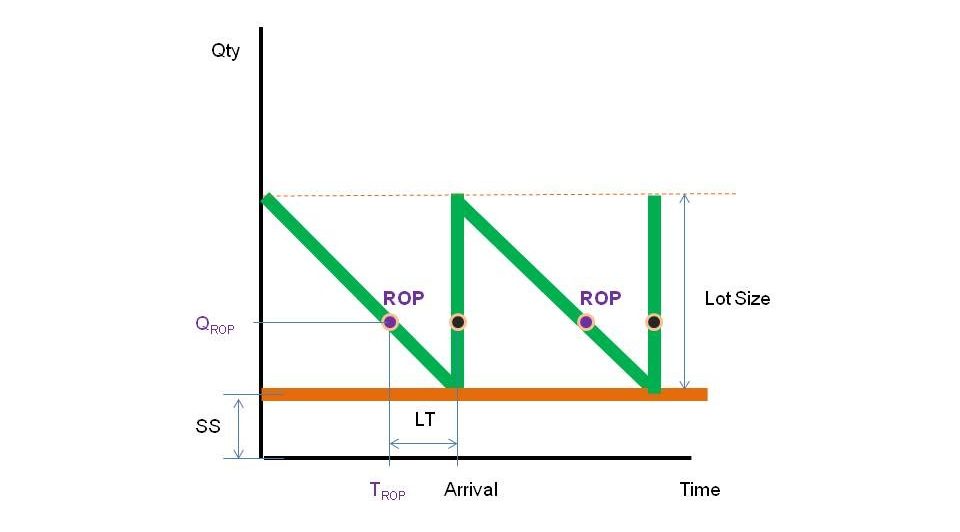
Lead time
As the above graph visualizes, lead time represents the amount of time in days it takes for items to become available from the moment they are ordered. It is thus an instrumental part of the ROP calculation and helps to avoid inventory levels falling below the safety stock line.
When calculating ROP, lead time is mostly approximated using historical averages, in-depth analysis of the supply chain, supplier performance, etc. For fresh suppliers or in case of many unknowns, it might be a good idea to buffer this number higher by a small amount until the new supplier performance is determined.
For raw materials or finished goods incoming from suppliers via purchase orders, lead time is usually referred to as delivery or material lead time. For items or sub-assemblies that are manufactured in-house, lead time is referred to as factory or production lead time.
Read more about Lead time.
Sales or manufacturing rate
The sales or manufacturing rate, or demand rate, also differs per item and is a function of consumption over time. It is usually the average daily usage or average sales per day of an item. In the above graph, the demand rate of an item is represented by the stock level’s (green line) angle. The steeper the angle, the greater the consumption rate.
The value of the sales or manufacturing rate also needs to be as accurate as possible to ensure the reorder point calculation is reliable. A thorough analysis of consumption rates is a must. Capable manufacturing ERP software can simplify this process by way of automatic reports of sales and manufacturing data.
Lead time and the sales or manufacturing demand are often grouped together into a unifying metric called lead time demand or average consumption during lead time. This is the lead time of a product multiplied by its average consumption rate. The ROP formula using lead time demand would simply be ROP = lead time demand + safety stock.
Read more about Demand forecasting.
Safety stock
Finally, safety stock is the number of items that companies keep in stock to guard against stockouts that may occur due to sudden shifts in supply and/or demand. If the delivery of an item is delayed or the consumption rate increases rapidly and unpredictably for any reason, the safety stock will cover the shortage of items.
Calculating basic safety stock is quite a straightforward affair that involves multiplying the average demand for items with a preset value of safety days. Many advanced formulas exist, however, that enable arriving at more accurate and efficient safety stock levels. Here too, competent MRP systems can decisively simplify the process.
For companies not utilizing any safety stock, the reorder point for an item is determined simply by the lead time demand value. In these cases, maximum lead time and consumption values are often used. This means that the demand rate may be slightly exaggerated to alleviate the risk of a stockout.
Read our detailed entry on Safety stock.
ROP calculation example
Let us look at an example. Suppose your manufacturing company consumes 100 units of raw materials per day to produce goods. The average delivery lead time for the raw materials is 3 days and since the supplier has had some shipping issues lately, you keep a safety stock of 400 units.
The average consumption during lead time (a.k.a lead time demand) is thus 100 units/day x 3 days = 300 units. The reorder point calculation is 300 + 400 = 700 units. Note that this is not the lot size, but the point at which replenishment should be triggered. An ROP should be set at 700 units on your replenishment system for this item and supplier.
Benefits of using reorder points
The ROP model is a simple decision-making tool that can help keep inventory levels optimized and avoid stockouts. Next to the obvious utility, this can also translate into other benefits. Some of the potential advantages of implementing reorder points include:
- Money saved. ROPs help to keep stock levels close to their optimal levels and alleviate the risk of stockouts. In this, they also help lower the chance of accidentally overstocking items. Overstocking can be detrimental to a business for many reasons, chief among which are mounting carrying costs and funds unnecessarily tied up in standing inventory.
- Time saved. Effective reorder points allow manufacturers and distributors to automate parts of the stock replenishment process. This minimizes the need for constant reorder requests and shortens other manual checklists, resulting in an overall faster purchasing process. Naturally, stable inventory levels also mean a logistics chain or shop floor running closer to the optimum.
- Data-driven replenishment. It almost never makes sense to reorder stock on a whim. The accuracy of the ROP model is dependent on the quality of analysis for purchasing trends and stock consumption rates. Taking into account other factors like supply chain peculiarities, shifting legal norms, market requirements, changes in a product’s bill of materials, etc., can all help to more accurately predict real-world utilization and replenish accordingly.
- Increased business opportunity. More available resources mean an increased ability to respond to new ventures or make critical infrastructure updates as needs arise. A reliable replenishment and fulfillment process can therefore lead to increased business opportunities.
Limitations of reorder points
As beneficial as a well-implemented ROP setup may be, it is not applicable in all circumstances. Reorder points attempt to predict the future by using historical data. In that, they have some fundamental disadvantages compared to more advanced systems like Material Requirements Planning. Here are some limitations of reorder points:
- Rigid methodology. The reorder point approach does not, in itself, utilize advanced forecasting methods or take into account production constraints other than material availability. They can also be a lot of work to maintain as they require constant re-evaluation when changes occur in supply chains or customer demand.
- Ineffective for complex manufacturing operations. Reorder points do not consider the dependencies between different items or production workflows. ROPs are thus unsuitable as the only method for accurately determining reordering or production schedules for multiple items, parallel production lines, and complex operations.
- Unsuitable for fluctuating demand. ROPs are reasonably reliable in triggering stock replenishment for items with stable demand rates and supplier lead times. For example, they can work well for make-to-stock manufacturers or when demand fluctuations are limited to easily predictable seasonality. Engineer-to-order manufacturers and companies operating in fluctuating markets, however, need to look elsewhere.
- No utilization capacity. Reorder point systems do not take into account the capacity of production facilities. This needs to be carefully factored in manually or by supplementing methodology. If capacity constraints are not taken into account, this can lead to troubles down the line that are often not just limited to overproduction or stockouts and corresponding financial issues.
5 recommendations for setting up reorder points
Finally, let us look at some best practices to consider when setting up and managing reorder points.
- Prioritize SKUs. In the perfect world, it would naturally be best to maintain perfect ROPs for all of a company’s goods. Realistically, however, analyzing supplier performances, demand fluctuations, and other variables for each SKU can be a very time-consuming task. It makes sense to prioritize creating and managing effective reorder points for the most popular or otherwise applicable SKUs with stable demand. Find a good balance between effort and gain.
- Avoid using fixed ROPs and update regularly. It might seem tempting to apply a seemingly meaningful ROP to all similar items in hopes of a perfectly optimized inventory. In most markets, though, change is a constant. Supplier conditions or market trends can shift at any time and in myriad ways. Keep reorder points frequently updated and adjusted for relevant changes. Replenishment for Items with constantly fluctuating lead times or demand should be calculated using other methods.
- Play it safe. It might not be possible to always put in new purchase orders at precisely the right time. The supplier might be unavailable to ship goods on certain weekdays, for example. Or perhaps the minimum order quantity is a bit larger than the ideal ROP value. If the order cannot be put in at the right time or in the right quantity, it usually makes sense to do it sooner rather than later and order a bit more to ensure you always have enough stock. Stockouts are generally much worse than a small amount of excess inventory, after all.
- Do not overprioritize ROPs. As effective as it can be, it pays to stress once more that the ROP model is not the be-all and end-all of inventory management. Reorder points have their limitations and do not eliminate the need for sufficient communication with suppliers or gaining deeper insights into the supply chain. There are other stock-level optimizations that can be used instead or in tandem with ROPs. For example, consider calculating the Economic Order Quantity (EOQ) for important SKUs.
- Invest in inventory management software. Implementing dedicated inventory management software or an MRP system gives companies access to a host of advanced tools and functionalities, including but not limited to setting reorder points. These solutions hugely simplify and elevate data-driven decision-making and give manufacturers and distributors the tools to decisively increase overall efficiency.
Modern manufacturing ERP systems utilizing forecast-based MRP methodology are generally much easier to use, and more reliable than setting up effective ROPs for your whole manufacturing or distribution enterprise. For example, MRPeasy is a cloud-based solution for small and medium companies that calculates material demand and purchase-delivery timing using a production plan that is built against a sales forecast and/or confirmed orders. MRPeasy not only automates and simplifies stock replenishment, but also tracks and manages many other aspects of inventory, helps in scheduling and planning production, includes integrated cost accounting, and much more. Naturally, MRPeasy also allows setting reorder points.
Key takeaways
- A reorder point (ROP) is the lowest number of units of an item that a company needs to have in stock to make sure they do not run out and can keep fulfilling orders.
- The ROP calculation takes into account an item’s average lead time, its demand rate, and its safety stock level if a company utilizes safety stock.
- The reorder point formula is ROP = (lead time x demand rate) + safety stock level. Lead time and sales velocity or consumption are sometimes grouped together into a metric known as lead time demand.
- Recommendations for implementing reorder points include prioritizing SKUs with which to set them up, keeping your ROPs regularly updated, not overprioritizing their importance, and investing in capable inventory management software.
- Modern MRP-systems can largely supplement or totally replace the ROP method. Which method to use and when should be considered carefully as per use case.
Frequently asked questions
What is the purpose of a reorder point?
The purpose of a reorder point is to find and set the lowest stock level for an inventory item at which a new order should be put in, in order to avoid a stockout.
How do you calculate reorder points?
Calculating reorder points involves finding and the item’s lead time and daily consumption rate and multiplying them to arrive at the lead time demand value. If safety stock is utilized, the safety stock value is then added to arrive at the ROP value.
What is the difference between safety stock and reorder point?
Safety stock is the level of emergency inventory that is kept to reduce the risk of stockouts caused by shifting supply, demand, or both. A reorder point, however, is a stock value at which new stock should be ordered in order to avoid the stock level falling below the safety stock value.
You may also like: ABC Analysis in Inventory Management – A Quick Guide