What is Lean Manufacturing?
The premise of lean manufacturing is rather simple: companies must strive to eliminate waste from the manufacturing process.
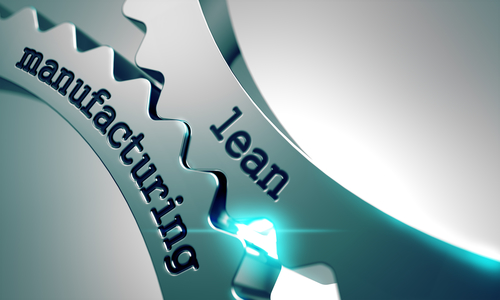
You can also listen to this article:
In this context, waste is any activity that doesn’t add value from a customer’s point of view. And studies have concluded that a shocking 60% of the production activities in the average manufacturing operation are wasted and add no value for their customers.
Here are some examples of waste you might be able to identify within your organization.
The eight most common wastes in a manufacturing operation
One of the simplest methods for recognizing waste in your company is to use the acronym DOWNTIME. It stands for:
- Defects
- Overproduction
- Waiting
- Not utilizing talent
- Transportation
- Inventory excess
- Motion waste
- Excess processing
1. Defects: Mistakes typically require additional time, resources, and money to make them right. In manufacturing, a faulty product that needs to be remade is a good example. You can minimize defects with strict quality controls and standardized work plans.
2. Overproduction: Sometimes, your workers are producing for a customer who doesn’t need your products right now. You’re tying up working capital and production hours that could be used elsewhere in the business. Establishing reasonable workflows and having the proper procedures in place can reduce the chances of overproduction.
3. Waiting: Waiting for approvals, materials, or because of a breakdown or bottleneck is expensive. Make sure you have enough workers to prevent bottlenecks and inventory controls that eliminate the wait for materials.
4. Not using talent correctly: When your workers are under-utilized or not utilized at all, it leads to a lack of engagement from them. Any company can reap the benefits of higher productivity from their people by not micromanaging them, giving them adequate training, and empowering them to work independently.
5. Transportation: When manufacturing companies move things excessively, they waste time and increase their costs. Simplified processes and efficient plant layouts are just two of the ideas for combatting too much movement.
6. Inventory excess: Too much supply and insufficient demand add up to an excess of inventory. Better monitoring systems and an end to just-in-case manufacturing will trim your inventory.
7. Motion waste: Just as with transportation, wasted motion by workers or machines adds expense—but no value—to your product or process. Make sure your plant layout incorporates shorter distance between stations and that it’s easy for workers to reach tools that they use often.
8. Excess processing: Even the best companies can be stuck with several versions of the same task or require more reports than are necessary. These extra steps are costly and usually a time waster. Understanding your customers’ needs and improving all areas of communication can help to mitigate this waste.
These eight wastes will increase your costs, time, and resources. Lean manufacturing is designed to help any manufacturing organization improve efficiency and reduce costs. The goal of lean is to eliminate waste—those components that do not add value to your operations. When it’s done correctly, lean can produce substantial improvements in efficiency, productivity, cycle time, material costs, and defects, resulting in lower costs and improved competitiveness. Here is how it works.
The five fundamental principles of lean manufacturing
Although lean has long been associated with improvements in manufacturing, the principles of lean can be applied to any business or industry. These principles can even be used, on a smaller scale, to organize your office or workspace.
These are the five steps:
1. Value: Your customers will always define value for their product. You need to ask them the right questions to determine it, such as what is your timeline for manufacturing and delivery? Are there other expectations or requirements? What is your price? Once you get these answers, you can provide value for that customer.
2. Value Stream: After you have established the value, the next step is mapping the “value stream.” This part includes examining all the processes that are involved in taking the product from raw materials to delivering it to the customer as the final product. Value-stream mapping is not complicated, but it is crucial since it identifies every action throughout the process.
On a one-page map, list the flow of materials with the goal being to find wasteful steps that do not add value and then to eliminate them. Going through this step should provide a complete understanding of the entire business operation.
3. Flow: Once the waste has been taken out of the value stream, the next step is to ensure that the remaining steps flow smoothly without interruptions, delays, or bottlenecks. This step could require breaking down the silo mentality within the organization and making an effort to become cross-functional across all departments. While it won’t be easy, doing so will probably result in substantial gains in productivity and efficiency.
4. Pull: Improved flow means you can dramatically reduce the time it takes to get products to the customer. It now becomes easier for you to deliver your products, and your customers can start to “pull” the products from you as they need them. Because of the enhanced flow of your processes, you won’t need to manufacture products in advance or have costly inventory. Both you and your customer end up saving money.
5. Perfection: While navigating the first four steps is vital, step five is the most essential of all. In this final step, you’ll be ensuring that lean thinking and process improvement become part of your company’s culture. Even as you witness the gains you’re making, you must remember that lean manufacturing requires a continuous effort to perfect. Every worker must be engaged in implementing lean. Experts in lean manufacturing stress that a process is not lean until it has been through value-stream mapping at least half a dozen times.
Every organization can improve by using lean manufacturing techniques
Every company has a tremendous opportunity to grow by putting lean manufacturing into practice. The steps will enable your business to deliver the highest quality products at significantly lower costs. And that’s something that should motivate anyone to give it a try!