What is Bill of Materials Functionality?
A Bill of Materials is the complete list of parts, materials or ingredients required to complete a finished and sellable product.
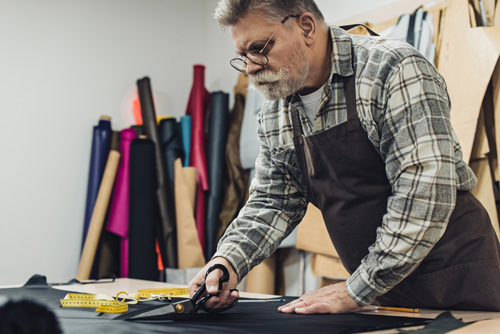
You can also listen to this article
In the world of fine dining, the experience of the chef is the lifeblood of a restaurant’s success. But regardless of the training and experience of the chef, with the flurry of constant movement and orders on a busy night, no restaurant can run without precise and accurate recipes. And even as the chef is creating new and amazing dishes, they will meticulously record the recipe to capture the exact ingredients in the exact quantities so that the dish can be recreated over and over. These recipes will also be used to order ingredients from suppliers and help to determine the cost of the item.
The same logic applies to manufacturers “recipes” for producing or assembling their products. A Bill of Materials (BOM) is the assembly instructions for discrete manufacturing and the recipe that consists of the quantities of the raw material for process manufacturing.
Bill of Material Structure
A Bill of Material may have one or several levels depending on the complexity of the product and the number of assembly or sub-processing steps required to make it.
- Single-Level BOM – A single-level BOM is the simplest list for manufacturing a product. It can be used where there are no complex processing steps or sub-assemblies.
- Multi-Level BOM – More common is the Multi-Level Bill of Materials. In a multi-level BOM, the list contains not only the final assembly items but also the materials and quantities used in each step below. This allows for the creation of parent/child relationships and can allow more complex and accurate costing down to the raw material stage.
Like the recipes in a restaurant, the BOM is the base from where all else proceeds. A well-done BOM gives manufacturers several advantages in planning and operations such as:
- Planning raw material purchases
- Establish groundwork for proper product costing
- Provide the basis for inventory control
- Assist operations in planning workflows and work centers
- Factor in measured waste
Bill of Materials Functionality
Just as the chef cannot remember all the recipes in his or her head, a Bill of Materials is almost always electronically stored and is usually the base functionality of MRP and Manufacturing ERP systems. Other areas of the company will draw data for making decisions based on orders, tracking and planning.
Key functionality tied to a Bill of Materials will include:
- Materials Planning – Managing the supply chain of modern manufacturing would not be possible without an accurate Bill of Materials. It enables a manufacturer to use established order position against accurate BOMs in the product mix to purchase raw materials in the right quantity and assure on-time delivery for production. This also helps planning departments determine which components can be ordered JIT and which must be ordered for stock. BOMs may also include materials which may be consumed during production. These items must be accounted for in the manufacturing process as well.
- Costing – Costing is also tied to BOMs and with the ability to produce both single level and multi-level BOMs, accurate costing can be applied to each component within the BOM. This includes consumables and any component not included in the final product but required for its production. This may include things such as cutting oils used for coolant, alcohols, waxes and many others. All materials used in the production of a unit must be listed at the unit level within the BOM.
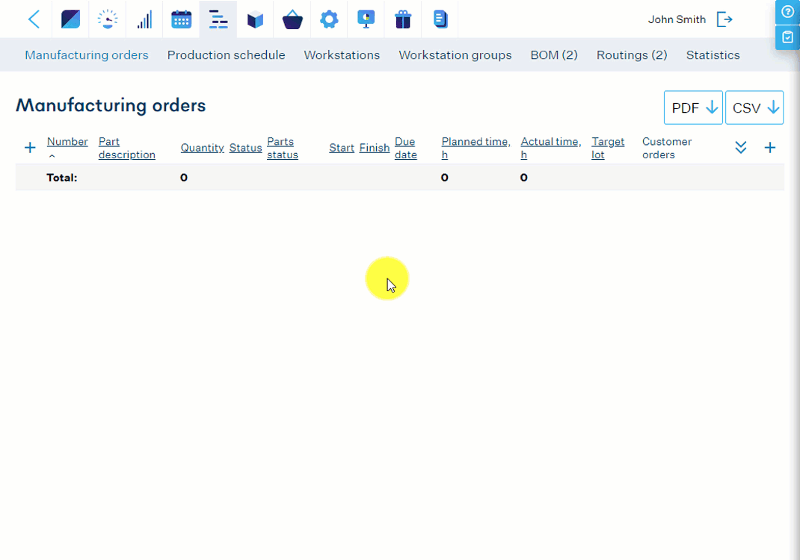
- Changes and Replacements – Flexible BOM modules may allow for the global replacement of raw materials components. As vendors often change over time, the ability to “mass replace” saves time and labor. They can also be tied to engineering change orders so that users can see the changes and when they occurred. This is especially useful when BOMs are changed with orders already in production.
- Design and Administrative Planning – As many products within a manufacturer are similar or derivative, most BOM functionality allows for cloning or “copy-from” functionality. This saves time and labour as only the added or changed materials need to be added.
Read more about Bill of Materials Software.
Things to Consider
As a base function of an MRP or ERP system, an accurate Bill of Materials is essential. And producing a BOM is more than just an exercise in making a list. Like the restaurant, it must include all parts of the recipe in the exact quantities to be producible and repeatable. If an item is left off a BOM, then the result can have ramifications for all associated functions within the system as well. For example, leaving out a consumable such as alcohol or wax that evaporates or is removed will impact costing, inventory and work center routings. It could lead to improper pricing and reduced or negative margins for that product.
Just as important is the quantity. As a recipe or list at the unit level, many multi-level BOMs, especially in process manufacturing, may only list minute amounts. Nevertheless, they must be measured and costed at the right rate as volume variance over time can also impact the cost.
Quality is also a major consideration in producing a correct BOM. Errors in components listed on BOMs within discreet manufacturing can lead to the wrong part being used over a long stretch of production. Aside from the obvious cost associated with this type of error, there is the added possibility of product failure, or worse, creating a finished product that may prove to be dangerous when the incorrect part is used.
Conclusion
In manufacturing, all functional areas are tied to the information used in its Bill of Materials. The functionality that accompanies the BOM functions can unite the factory in terms of communication and provide a common language for producing finished goods. And an accurate Bill of Materials, coupled with the right software platform with deep analytical capability and flexible and agile functionality can provide small to medium companies with a production system on par with any large company. However, it must be borne in mind that this functionality does not replace the functionality of production planning.