What is a Warehouse Management System?
As warehousing becomes more complex, there is a need to automate all processes to align them with automation already taking place in supply chain management (SCM). Modern Warehouse Management System can help.
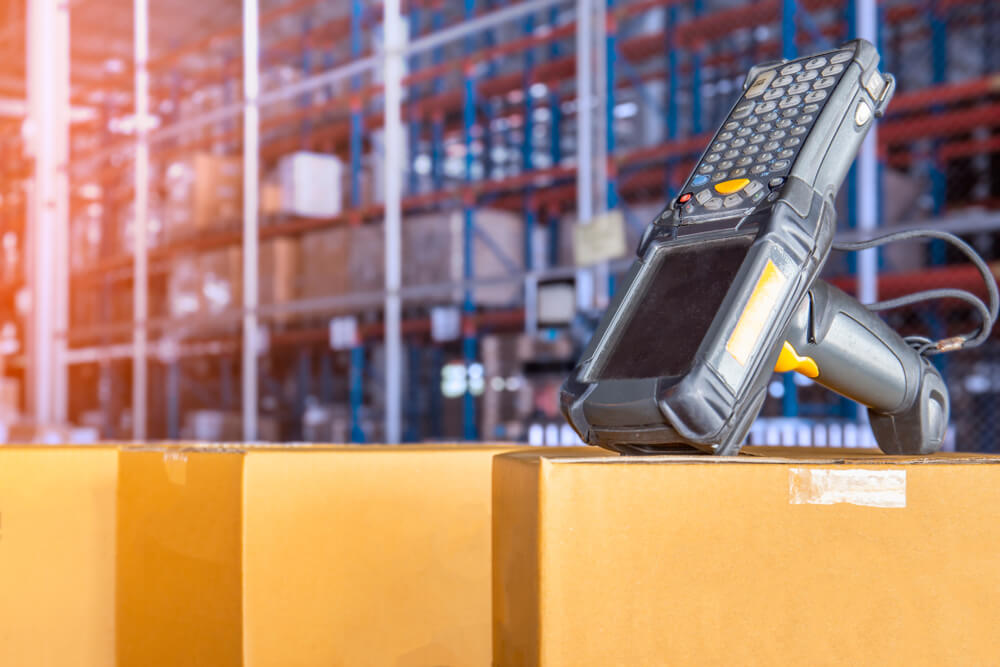
You can also listen to this article:
In the age of increasingly complex global supply chains and manufacturing cycles that produce and deliver goods to customers faster than ever, warehouse management has found itself caught between the two. As these two trends continue, warehousing systems, whether they are 3PL or traditional warehousing operated by manufacturing and distribution companies, has looked to software automation in the form of Warehouse Management Systems (WMS) to improve their processes, hold goods more efficiently and pick and deliver them faster.
One driver of the adoption of WMS is complexity. As consumer’s expectations and e-commerce play an increasingly important role in setting delivery times, warehouses today may not simply pick and ship whole pallets. Today, only 9% of distribution centers and warehouses are pallet only, with 46% handling pallets, cases, and single-piece orders.
Warehouse Management System Software
But what is warehouse management software? A Warehouse Management System (WMS) is a software platform that lets companies control their warehouse operations by automating their processes to form an end-to-end solution (E2ES). They can administer control of those operations from the time goods and materials enter until they ship out.
Many companies have already moved to implement software solutions in supply chain management and in manufacturing management with platforms such as cloud-based, modular ERP systems. Now, they are looking to improve efficiency in warehouses that can tie that increased productivity together to improve overall operating efficiency. And by adopting a WMS, studies show that a company can increase its warehouse efficiency by as much as 25% while regaining up to 30% of its available space.
Types of Warehouse Management Systems
There are many types of Warehouse Management Systems software solutions available, depending on the size and resources available. And there are still many companies that manage their warehousing operations manually by using spreadsheets, notes, and manual counting systems. However, today’s WMS software is flexible and scalable to be used by small and medium-sized businesses through large enterprises.
WMS software may be a traditional, standalone, on-premise system with no other system or data in or out of the software itself. It is deployed only on the company’s internal network. WMS may also be modular software systems that can integrate through API with an existing ERP system or with a supply chain management system. They may also be cloud-based, always providing the most up to date version to the customer.
Of these types, those that can integrate with ERP and SCM systems and those that are cloud-based are more versatile. They are scalable and can be tailored to meet the “right-size” needs of any company. By allowing companies to choose functionality based on need, learning curves are reduced and staff do not feel overwhelmed by features they don’t need.
Features of Warehouse Management System
While products may vary, there are many common features included in today’s Warehouse Management System software platforms. These features include:
- Workflow Design – Customers can create a customized workflow that includes advanced picking logic. Past warehouse practices often grouped products by type or category. However, as holding costs rise and space becomes more expensive, using a WMS with the capability to slot bins to maximize storage space allows more efficient use of that space.
- Inventory Tracking – A traditional headache for warehouse managers, inventory tracking is optimized in a WMS to allow ease of locating goods when they need to be transferred or shipped. By using barcode scanners, workers can find goods via radio-frequency identification (RFID) or automatic identification and data capture (AIDC).
- Receiving and Location – WMS programs provide a variety of advanced locating features such as pick-to-light or pick-to-voice systems for accurate locating of goods.
- Pick and Pack – On average, warehouses are almost a third larger than a decade ago. Because of this, sending workers out on long and winding order picking runs is very inefficient. WMS software allows companies to implement advanced picking systems that take advantage of the power of the WMS analytics. This includes zone, wave, and batch picking methods. Workers can be guided on the most efficient physical path for the picking of their goods to reduce time and fatigue.
- Shipping – By tying into the company ERP or SCM software or through cloud-based capability, WMS software allows companies to be proactive in the administrative side as well. Bills of Lading (BOL), packing lists, invoices, and advance ship notices can be generated and sent to the customer automatically.
- Labor – As much as 65% of warehouse operations consist of labor. By giving managers the ability to monitor KPIs on worker performance, labor utilization can be optimized.
- Dock Management – Known as “Traffic” in many warehouse operations, WMS may be utilized to guide truckers to the right locations at the dock and provide them with optimized dock times.
- Reports – Since WMS software provides data and analysis in real-time, managers can choose from a variety of reports to monitor the health of their operation and make decisions with current data at their fingertips.
Using an Optimal WMS Software Platform
So, what is the best type of Warehouse Management System platform to use? As always, that answer depends on size, scale, scope, complexity, and other factors unique to each company. However, there are benefits and tradeoffs.
- Standalone: Standalone systems can help manage a warehouse today. And as a replacement for manual or spreadsheet-based systems, they can certainly improve warehouse performance. But standalone systems have several disadvantages. For one, they must be updated periodically. This can be costly and disruptive to the operation. It is also problematic to scale a standalone system as the new version again must be purchased and installed and training may be extensive.
- ERP-Based WMS: ERP-based WMS software has many advantages. It helps unsiloed data and standardizes data across the organization as part of an integrated ERP system. By doing so, warehouse data can be used for functionality such as embedded EDI, tying directly to sales orders, integration, and analysis in MRP for a more holistic view of the operation and advanced shipping management.
- Cloud-Based WMS: Cloud-based WMS is a software as a service (SaaS model that uses cloud technology to manage the WMS inputs. It can be used by any sized enterprise, but it is especially useful for small and medium-sized businesses (SMB) that need flexibility and modularity in their system. Cloud-based systems always offer the most up to date version of the software with no upgrading necessary. It also allows smaller, less complex operations to turn features on and off as needed so that the system is nimble to the needs of staff. It is scalable as a company grows and provides disaster-proofing for company data in the event of a crisis.
Of the three types of systems, ERP-based and Cloud-based systems are the best option for almost any sized company. In addition to benefits such as reduced fulfillment time, improved inventory accuracy, better space utilization, and lower costs with higher productivity, these two systems provide flexibility and scalability at a lower cost not found in standalone systems.
Using a WMS
To deploy and using the modern Warehouse Management System, companies must decide on what their needs are. Size, scale, growth over time, complexity, average delivery time, efficiency improvements and other factors must be answered to determine what type of system is needed. Once done, a few simple steps can have a new WMS up and running with good results. These steps include:
- Map out Needs – Remember to consider issues such as complexity of the operation, size of the current warehouse, critical areas needing improvement, etc.
- Decide on System Type – Based on needs, determine which type of system is needed. If you already have an ERP system in place, does it allow integration? If your staff is small and wears many hats, cloud-based options may reduce training time. System type selected may also be a function of the size and capability of your in-house IT skillsets.
- Install the System and Upload Current Data – Any system is only as good as the data inputs. If installing a new WMS system, a hard stop for a complete and accurate inventory and reconciliation may be needed before use. This gives you the confidence that the data inputs are correct from the start.
- Train Staff – This doesn’t just mean system interfaces. A WMS software system is far-reaching and requires training on system interfaces, the use of barcode scanners, and training on the correct physical systems (such as walking the path indicated in the workflow) to take advantage of all available functionality. It is a system that helps manage digital and physical processes.
- Tailor Functionality to Need – Size matters in manufacturing. And small and medium-sized businesses may not need the functionality of a large enterprise. By analyzing initial results, you can decide what functionality to turn off and what functionality to run on to customize the user experience to your staff and your company’s unique needs.
As warehousing becomes more complex, there is a need to automate all processes to align them with automation already taking place in supply chain management (SCM) and in enterprise management through use of advanced ERP systems. By adopting a WMS, companies can complete the loop and optimize their processes end-to-end.