Top 3 Common Warehouse Management Mistakes
Running a warehouse efficiently is no small feat. From inventory management to staff training, many factors can impact your operation. One wrong move can lead to significant delays, increased costs, and even safety hazards. This article explores some of the most common warehouse management mistakes and provides practical solutions to avoid them.
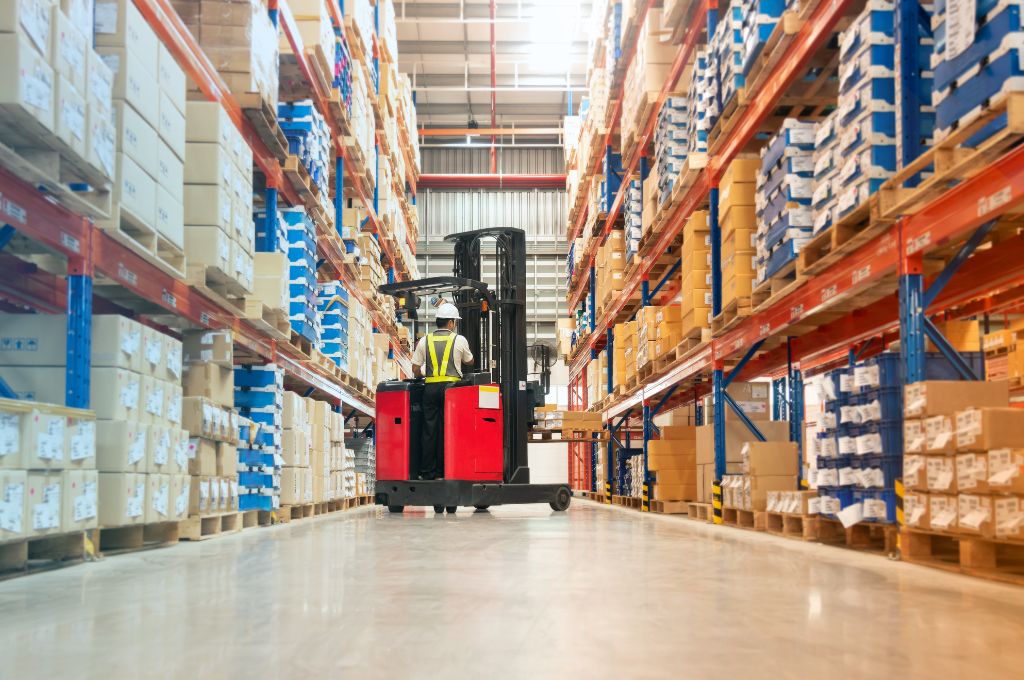
You can also listen to this article:
What is warehouse management?
Warehouse management is the process of overseeing and organizing all activities that happen within a warehouse. These activities include receiving materials and orders, storing inventory, managing stock levels, picking and packing items for shipment, and shipping out orders in an efficient manner. The number one goal of warehouse management is to keep the warehouse running smoothly.
However, this goal can sometimes be elusive. Mistakes happen, and when they do, they can slow down operations and lead to a negative customer experience with your business. Let’s take a look at the most common warehouse management mistakes and how to prevent them from happening in your business.
Mistake #1: Inventory mismanagement
Let’s start with one of the most common warehousing mistakes: inventory mismanagement. This mistake can have far-reaching consequences on warehouse operations and supply chain management efficiency.
Inventory mismanagement often arises from a lack of inventory tracking. It can also be caused by improper planning or reliance on outdated paper processes. Here’s a look at the negative impacts of inventory mismanagement:
- Ordering too much or too little. Overstocking can be a big problem. Having more stock than you need occupies valuable warehouse space and locks up funds that could be better used elsewhere in the business. Additionally, products that sit on shelves for too long risk becoming outdated or expired, especially in sectors where trends change rapidly or products have a limited shelf life. This not only wastes resources but can result in financial losses. On the flip side, you may end up with stockouts if you don’t order enough. Running out of stock can halt order fulfillment processes. The end result? Delays, backorders, and unhappy customers. This can potentially damage your reputation and lead to lost sales and broken customer trust.
- Lack of real-time tracking. It’s important to constantly monitor and update inventory levels as items move to and from the stockroom. However, many warehouses don’t use real-time tracking because they rely on outdated methods like paper-based recording. This can lead to inaccurate inventory counts, increasing the likelihood of overstocks or stockouts.
- Inaccurate forecasting. If you don’t have enough data to predict demand accurately or the tools to do so effectively, you risk overstocking and stockouts. Overstocking not only reduces available warehouse space but also ties up your resources. Stockouts translate to missed sales and disappointed customers. Neither option is good.
- Too infrequent stocktakes. Stocktakes, or physically counting all of the items in your warehouse, is a necessary practice to ensure inventory accuracy. But, infrequent stocktakes can lead to discrepancies between what’s actually in stock and what’s recorded in your system. These discrepancies can cost you money and result in unfulfilled orders and excess inventory.
- Using manual methods. As mentioned above, manual inventory management methods, like keeping paper records or using spreadsheets, are prone to human error. These outdated methods are also slower and less reliable than automated systems.
Best practices to prevent poor inventory management
How do you combat inventory mismanagement? Implement a warehouse management solution (WMS). A WMS automates inventory tracking and provides real-time data on stock levels. This reduces the risk of human errors and enhances overall productivity, providing an all-in-one warehouse management solution.
Conducting regular audits is another best practice. Inventory auditing helps maintain inventory accuracy and identify discrepancies early. This practice prevents overstocking and stockouts by ensuring that the actual inventory matches the recorded levels. Using barcoding and warehouse automation tools further reduces errors and increases stock accuracy. Regular stocktakes or even partial counting of only the most critical goods is another effective way to address these issues.
Proper planning is also key. Accurate demand forecasting and planning are crucial for keeping stock optimized. Analyzing historical sales data, market trends, and seasonal variations allows you to predict customer demand and stock requirements and adjust inventory levels accordingly.
Mistake #2: Poor warehouse layout
A poor warehouse layout can easily become a nightmare for warehouse management. Let’s take a closer look at why.
- Decreased productivity. The first significant issue is decreased productivity. When the warehouse floor is not optimized, your employees will spend more time navigating longer picking paths to locate and retrieve items. This inefficiency not only slows down order fulfillment but also increases labor costs as more time is required to complete tasks that should be quicker and simpler. An inefficient layout can turn what should be a straightforward process into a time-consuming ordeal.
- Increased error rates. Another critical consequence is an increased rate of error. In a poorly organized warehouse, items are not stored logically, which can confuse your employees during the picking process. Confusion often leads to mistakes such as picking the wrong items or incorrect quantities, which inevitably results in inaccurate order fulfillment. But your employees won’t be the only ones who are confused. When a customer receives the wrong order, they’ll be confused, too. And that confusion will quickly turn to dissatisfaction and distrust.
- Increased labor costs. Increased labor costs are closely linked to the inefficiencies caused by a poor layout. When workers have to spend extra time finding and picking items, the overall labor required to fulfill orders rises. This inflates operational costs, which is bad news by itself, but additionally impacts the overall efficiency of the warehouse. It also impacts your profitability. Instead of focusing on productivity-enhancing tasks, employees are bogged down by the basic inefficiencies of a suboptimal layout.
- Safety. Then there’s the matter of safety. Safety risks are an often overlooked but critical issue arising from a poor warehouse layout. Cluttered or poorly organized spaces can create numerous safety hazards, such as blocked aisles, poorly stacked items, and unsafe pathways. These hazards increase the risk of accidents and injuries, which can disrupt your operation and lead to costly worker compensation claims and potential legal issues.
Best practices to improve warehouse layout
To combat these issues, take time to organize the warehouse floor. Organizing will minimize travel time and optimize workflows.
High-demand items should be kept in more accessible storage locations to speed up order picking, put-away, and material handling. Maximize the space in your warehouse by taking advantage of vertical storage solutions like shelving and pallets. This will keep the floor space clear and improve inventory accessibility.
Consider implementing the 80/20 rule, also known as the Pareto principle or ABC stock management. In the 80/20 rule, first, identify the 20% of items in your inventory that generate 80% of sales. Then, place these items in the most accessible location in your warehouse to save time and effort.
Create unobstructed paths for forklifts and staff to move through the warehouse. This will reduce the risk of accidents as well as optimize workflows. Implement zoning in your warehouse by dividing the space into specific areas based on different functions. For example, you can have separate areas in your warehouse for receiving, storage, picking, packing, and shipping. Doing this will streamline processes and reduce confusion.
Using a warehouse management system can further help you monitor inventory locations in real-time as well as provide valuable insights into the most optimal warehouse layouts based on the flow of goods. A WMS analyzes data on inventory movements and order fulfillment and identifies patterns to optimize storage. It also tracks movements and suggests layout adjustments to reduce travel times and improve space utilization.
It’s also a best practice to regularly review and adjust the warehouse layout. As your business needs change, these periodic assessments will ensure that your setup remains efficient. By adapting to new products, seasonal changes, and shifts in order volume, you can keep your warehouse running smoothly.
Mistake #3: Lack of training
Insufficient training is one of the most common mistakes that can undermine warehouse operations. This may be the result of a business’ desire to reduce labor costs. However, it’s often due to high employee turnover, with few employees available to train new hires. There may also be an unfair assumption that new hires can learn on the job without formal training. Whatever the cause, lack of training leads to inefficiencies, increased human errors, and compromised safety.
Here’s how a lack of training can negatively affect your business:
- Operational inefficiencies. When employees are not properly trained, they may not fully understand their roles or how to perform tasks efficiently. This leads to delays and bottlenecks in warehouse operations.
- Higher error rates. Inexperienced employees are more likely to make mistakes in inventory management, order picking, and other critical tasks. As a result, your business will struggle with inaccurate inventory levels and incorrect order fulfillment. These errors can lead to dissatisfied customers and additional costs for correcting mistakes.
- Safety risks. Without proper training in safety protocols, the risk of accidents and injuries will increase. Not only will this disrupt your production, but it may also result in higher health and safety costs and a higher rate of incidents. Untrained staff may not be aware of the correct procedures for handling equipment or materials. Unsafe practices can harm your employees and even put your customers at risk of injury. For example, improper handling of materials might lead to damaged goods, resulting in faulty or unsafe products reaching customers.
- Reduced customer satisfaction. When orders are not fulfilled accurately or on time, customer trust and loyalty can be severely impacted. These mistakes or delays can lead to dissatisfied customers and lost business.
Best practices to implement effective training programs
To combat the above issues, develop comprehensive and effective training programs. These are not just nice-to-haves but an essential part of effective warehouse management. A thorough onboarding program should cover all aspects of warehouse operations, from inventory management to safety procedures. With this in place, your new hires will understand their roles and responsibilities from day one.
Training shouldn’t stop after onboarding. Implement ongoing training programs to keep staff updated on the latest technologies, procedures, and best practices.
When possible, cross-train employees to perform multiple roles within the warehouse. Cross-training is a smart move for most businesses because it provides flexibility and helps maintain productivity during staff shortages or peak periods. Also, prioritize health and safety training to ensure that all employees understand and adhere to safety protocols to reduce the risk of accidents.
Leverage different forms of training, including live sessions, online training modules, video tutorials, and interactive simulations. This variety of training presentations can make your training more engaging and effective. Real-time feedback and assessments help track progress and identify areas for improvement.
By investing in comprehensive and continuous training programs, you can improve overall productivity, reduce errors, and enhance safety. Well-trained staff are crucial for maintaining efficient warehouse operations and ensuring customer satisfaction.
Final thoughts
Avoiding common warehouse mistakes is crucial for maintaining a streamlined and safe operation. By focusing on proper inventory management, optimizing your warehouse layout, and ensuring thorough staff training, you can significantly enhance productivity and reduce errors. Remember, a well-organized and efficient warehouse improves your bottom line while also boosting employee morale and customer satisfaction.
Implementing proper warehouse management software or a manufacturing ERP (Enterprise Resource Planning) system can be among the most efficient means of enhancing the warehouse management process. Modern cloud-based systems are cost-effective and feature-rich, providing advanced inventory control, end-to-end traceability, and scalability on top.
Key takeaways
- Proper inventory tracking prevents overstocking and stockouts, improves warehouse efficiency, and reduces production and holding costs.
- A well-designed warehouse layout minimizes travel time, reduces labor costs, and enhances safety.
- Continuous and thorough training for staff minimizes errors, boosts productivity, and boosts safety.
- Implementing a Warehouse Management System (WMS) aids in real-time inventory tracking and layout optimization.
- Regularly reviewing and adjusting warehouse processes and layouts can address inefficiencies and ensure that you adapt to changing business needs quickly.
- Ensuring all staff are trained in safety procedures reduces the risk of accidents and protects both your employees and your customers.
Frequently asked questions
Warehouse management involves overseeing and organizing all activities within a warehouse, including receiving, storing, and shipping inventory. It is crucial for maintaining efficient operations, preventing delays, reducing costs, and ensuring customer satisfaction.
To improve warehouse layout, organize the floor to minimize travel time and optimize workflows. Use vertical storage, implement the 80/20 rule, create unobstructed paths, and regularly review and adjust the layout. A WMS can also help optimize layouts by analyzing inventory movements.
Inventory mismanagement can lead to overstocking, stockouts, and inaccurate forecasting. These issues can occupy valuable space, tie up funds, halt order fulfillment, and result in financial losses, ultimately leading to customer dissatisfaction.
To ensure scalability in warehouse management, invest in a flexible Warehouse Management System (WMS) that can adapt to your growing inventory and operational needs. Additionally, regularly review your processes and warehouse layout to accommodate increased volume and complexity. Cross-training employees and implementing continuous improvement practices can also help your warehouse operations scale smoothly as your business grows.
You might also like: Lean Warehouse Management Guide for SMEs