Types of Manufacturing Processes – A Comprehensive Guide
Manufacturing processes can be categorized and subcategorized in many different ways. Here is a comprehensive guide into the various definitions, from processes grouped according to the scale of production up until those classified by their level of automation.
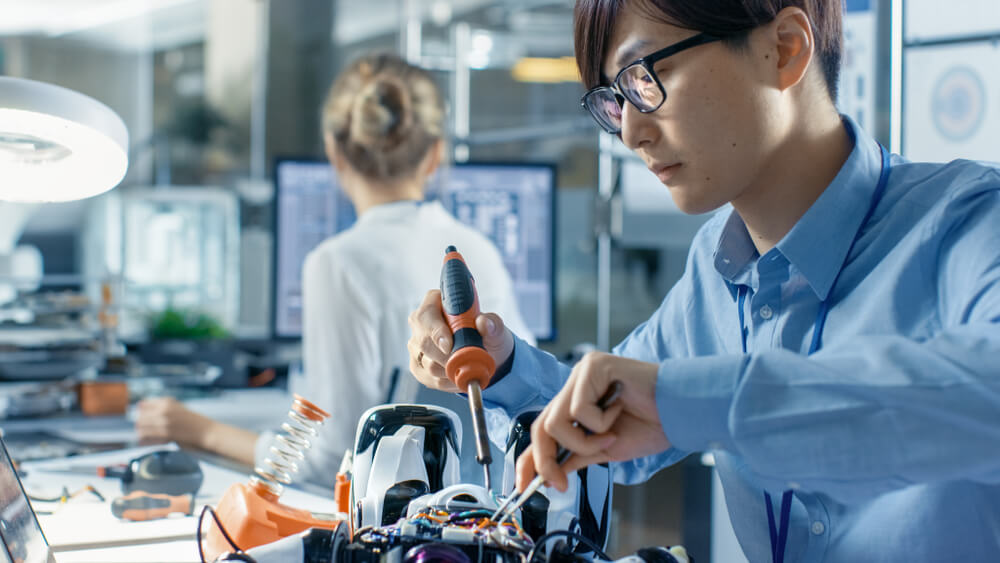
You can also listen to this article:
Without manufacturing, the world would come to a halt. Consumer goods, durable goods, commodity products, and an endless array of other items are produced every day in factories across the world.
These factories can be large multi-factory enterprises with global reach or small workshops operating in only a few square meters. They may be factories that make many different products or those that make only one item. And they may produce goods consisting of one part (such as sugar) or those with thousands of parts such as automobiles or aircraft.
What is a Manufacturing Process?
A manufacturing process is defined as using equipment, devices, or naturally occurring reactions to turn raw materials or parts into finished goods consistently and repetitively. A manufacturing process must also have established norms such as quality measurements, tolerances, and performance metrics to keep all areas of production – including machine operation, labor, material flow, and others – coordinated to achieve consistency and efficiency.
Regardless of the size of the company or the complexity of its product line, every factory has thought through and determined a manufacturing process that is optimal for their product and type of production. The process chosen is often determined by the type of product being made, as some may require a simple system while others require complicated midstream steps such as mixing or blending. But it is possible to see different manufacturing processes used in different companies or even combined in the same manufacturing company.
Different Classifications of Types of Manufacturing Processes
Manufacturing processes are categorized in various ways. The top results in a quick Google search suggest that there are five types of manufacturing processes:
- Repetitive Manufacturing.
- Discrete Manufacturing.
- Job Shop Manufacturing.
- Process Manufacturing (Continuous)
- Process Manufacturing (Batch)
This, however, seems to be a mix of different classifications because the Discrete and Process manufacturing differ in the nature of the product, while Job Shop is about the scale of the business, and both Discrete and Process manufacturing can be Repetitive.
There are several different ways to approach the classification of types of manufacturing processes:
- By the scale of production: job-shop (individual), batch (serial), and mass production.
- By the nature of the product: discrete or process manufacturing.
- By the role of the process: basic, auxiliary, serving, managerial
- By the level of automation: manual, machine-manual, machine, automated, complex (fully) automated.
As you can see, we have already determined four ways to categorize the types of manufacturing processes. These categories, however, each consist of several types.
Types of Manufacturing Processes by Scale
Job Shop Manufacturing
A job shop production process is characterized by:
- The manufacturing of products in single copies or in small series (one to two dozen per month).
- A wide range of products.
- The use of universal equipment, universal devices, cutting and measuring tools for general purposes.
- Grouping of workplaces according to the principle of technologically homogeneous operations.
- Lack of assignment of certain operations to individual employees.
- High qualification of employees which considers the diverse nature of the work performed.
- Lack of detailed development of the technological process of manufacturing the product.
- The fact that the object of planning, regulation, accounting is the entire product or its large units (subassemblies).
- A rather low cost of preparing the production of new products due to the presence of the last three features.
This form of a one-off manufacturing process is common in pilot plants that manufacture complex products and special-purpose systems.
Batch (or serial) manufacturing
A serial production process is characterized by:
- Production in batches that are periodically repeated. About several hundred per month – small-cut; 2-5 thousand pieces per month – large-scale.
- Limited range of products manufactured.
- Use of universal and specialized equipment, attachments, finishing, and measuring tools.
- Grouping of workplaces according to technological and organizational principles.
- A limited number of different operations are assigned to a workplace.
- Average qualification of employees.
- Detailed development of technological processes.
- Objects of planning, rationing, and accounting are the units and details of the product.
- Relatively high costs for preparing the production of new products in comparison with a single type of production.
This type of manufacturing process is common in factories that produce sophisticated products and special-purpose systems that are soon changing beyond design.
Mass production
The mass production process has the following features:
- Products are manufactured in large quantities.
- Use of specialized and special equipment, devices, and tools.
- Workstations are placed according to the course of the technological process.
- Jobs specialize in performing one operation.
- The technological process is developed in detail.
- The objects of planning, rationing, and accounting are the details and the operations.
- Workers may be of lower qualifications.
- Preparation to produce new products requires the greatest costs (in comparison with other types of production).
This type of manufacturing process is predominantly used to produce consumer goods.
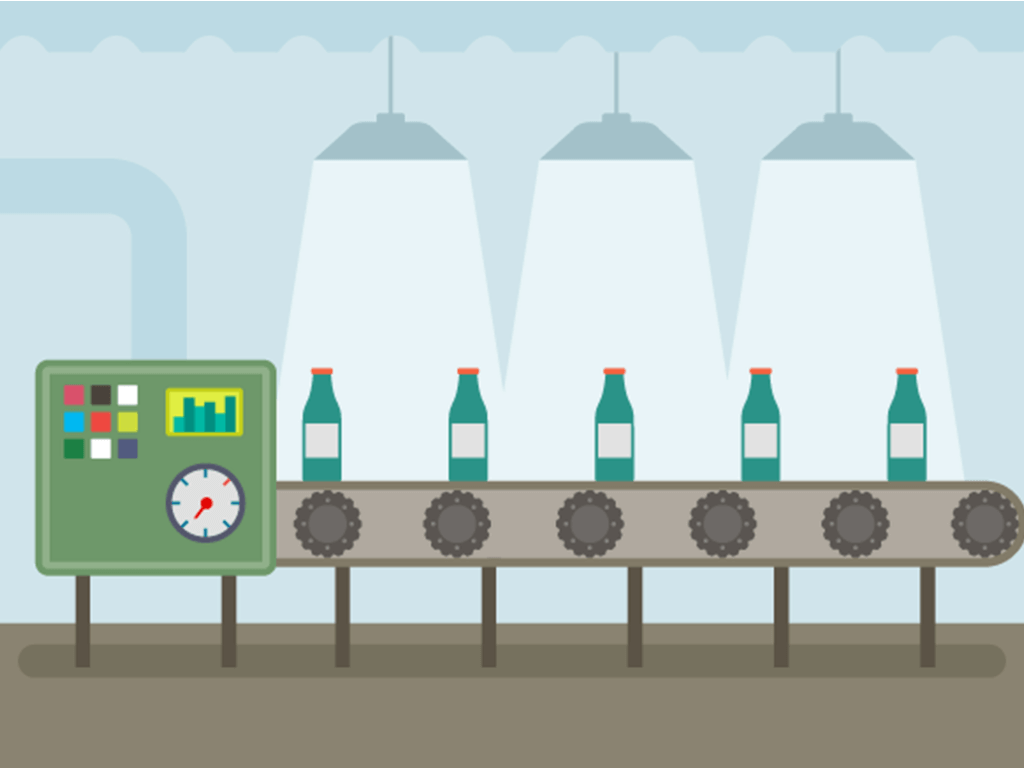
Types of Manufacturing Processes by the Nature of the Product
Discrete manufacturing
Discrete manufacturing produces specific items that are distinct from others in the production line ahead and behind. These items leave the production line as ready-to-use products that consumers and businesses can purchase.
Discrete manufacturing describes any system that produces single products. At the end of a single production process, individual products can be distinguished from each other, even if they are essentially identical.
The main types of discrete manufacturing are:
a) Mass production oriented with standard pricing
MTS – Make to Stock
The Make to Stock model is mostly used when producing consumer goods with predictable demand. However, it is also used when demand for the products is uncertain, but customers require short lead times.
It is special in comparison to the others in that it does not produce according to an order, instead following demand forecasts based on historical data. When a customer order comes in, it is fulfilled by using already existing inventory. This shortens the lead times of an MTS operation substantially, compared to other modes of production.
The MTS model also produces the most standardized products, i.e. the customer has no say in what the products should be like.
Read more about Make-to-Stock Manufacturing Process Flow and Best Practices.
b) Custom-oriented with custom pricing
MTO – Make to Order
Similarly to the MTS model, the MTO model deals with standardized products with defined Bills of Materials. However, in the case of an MTO model, products are not manufactured following demand forecasts, rather than being made according to customer orders. Production starts when a CO comes in, making the lead times longer than in the case of MTS production.
ATO – Assemble to Order
ATO means that the production line assembles products from ready-made components rather than producing everything from scratch following a customer order. This allows the company to fulfill orders quickly, and to offer a certain amount of customization options.
This model is considered very flexible and lean. It allows the manufacturer to offer the customers shorter lead times than the MTO model but is still slower than the MTS model.
CTO – Configure to Order
The Configure to Order model produces goods according to the specifications chosen by the customer. A company that employs the CTO model usually offers clients an array of product features to pick from, which makes for a large number of product variants with different feature combinations.
Like the MTO and ATO models, the CTO approach provides more leeway for the customers when choosing specs for their products. Therefore, the CTO model allows companies to offer mass customization while still fulfilling orders quickly.
Keep in mind that in the case of CTO, specification variations of the standard product are not as many as to necessitate the creation of separate part numbers for every variation. If the variation from the standard becomes too large, however, it is feasible to draw up entirely new projects for those increasingly complex orders and move over to the Engineer to Order mode of production.
ETO – Engineer to Order
The Engineer to Order mode is used to build highly customized complex products. This model creates products that have never been built before, which implies a closer, more creative collaboration with the client.
The process flow in ETO is not nearly as smooth as it is in the case of other modes of production. Apart from the production process, the ETO model also includes the whole design process with testing and implementing changes, special material procurement processes, etc., usually making the order fulfillment lead time longer than in any other production mode.
To provide customers with products that are tailored to fit their specific needs, ETO companies need to remain more flexible in their processes than those using the MTO, ATO, or CTO models. Building fully customized solutions requires more adaptability both in material sourcing as well as in production techniques.
Process Manufacturing
Process manufacturing produces goods in bulk, i.e. it uses gases, liquids, powders, granules, emulsions, or grains as raw materials. Examples of process manufacturing products are drinks, cereals, gasoline, concrete, etc.
Another thing that distinguishes discrete manufacturing from process manufacturing is the fact that in discrete manufacturing, parts in a product can still be distinguished from one another, and products can be disassembled, and broken back down to individual components. While in process manufacturing this is not possible, the ingredients become mixed and cannot be separated anymore.
Process production can be divided into two types:
- Process RPT / Batch manufacturing – Process Repeated Manufacturing
- Process Continuous Flow manufacturing – Continuous production.
Read more about Discrete Manufacturing vs. Process Manufacturing.
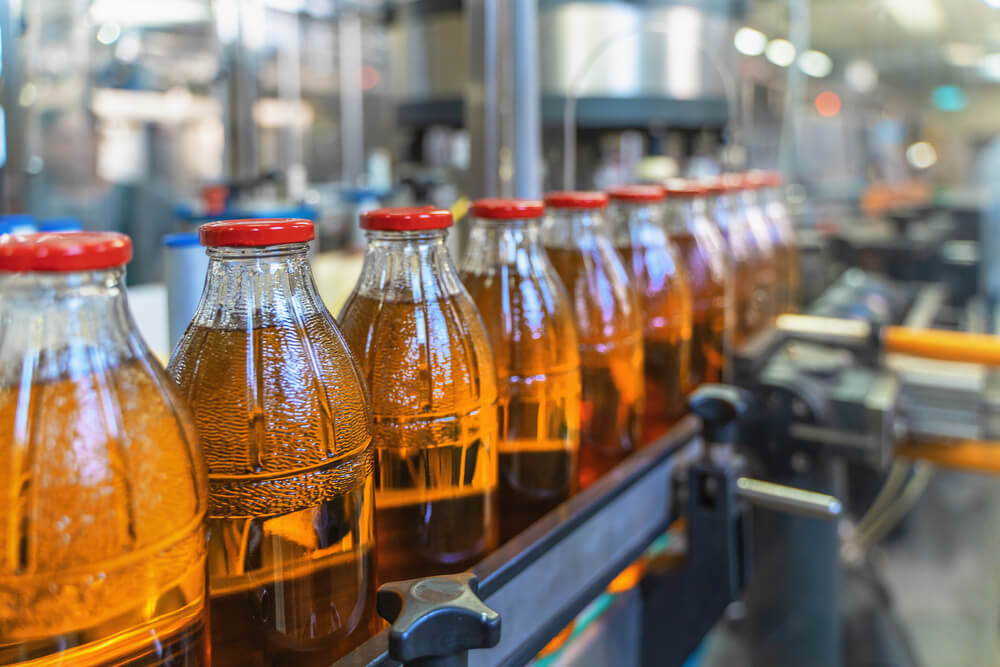
Types of Manufacturing Processes by Role of the Process
According to their role in the general process of manufacturing finished products, production processes can be distinguished in the following way:
Basic Manufacturing Processes
Basic processes are aimed at changing the basic objects of labor and giving them the properties of finished products; in this case, a partial production process is associated either with the implementation of any stage of processing the object of labor or with the manufacture of a part of a finished product.
Auxiliary Manufacturing Processes
Auxiliary processes create conditions for the normal course of the main production process (making tools for the needs of their production, repairing technological equipment, etc.).
Serving Processes
Serving processes are intended for movement (transport processes), storage pending subsequent processing (storage), control (control operations), provision of material, technical and energy resources, etc.
Managerial Processes
Managerial processes, in which decisions are developed and made, regulation and coordination of production progress, control over the accuracy of program implementation, analysis and accounting of work performed; these processes are often intertwined with the course of production processes.
Types of Manufacturing Processes by Level of Automation
According to the level of automation, it is customary to distinguish:
Manual Processes
Manual processes are performed without the use of machines, mechanisms, and power tools.
Machine-Manual Processes
Machine-manual processes are performed using machines and mechanisms with the obligatory participation of a worker. For example, processing a part on a universal lathe.
Machine Processes
Machine processes are carried out on machines, machine tools, and mechanisms with limited participation of the worker.
Automated Processes
Automated processes are carried out on automatic machines, where the worker monitors and controls the course of production.
Fully Automated Processes
In fully or complex automated processes, along with automatic production, automatic operational control is carried out.
Key takeaways
- There are not only different types of manufacturing processes but also several ways to classify them: by the scale of production, by the nature of the product, by the role of the process, by the level of automation.
- Manufacturing processes categorized by the scale of production are: job shop manufacturing, batch/serial manufacturing, and mass production.
- Manufacturing processes categorized by the nature of the product are discrete manufacturing and process manufacturing.
- Discrete manufacturing means producing single, distinguishable items while process manufacturing deals with bulk products such as gases, emulsions, liquids, etc.
- Discrete manufacturing is subcategorized as: make to stock (MTS), make to order (MTO), assemble to order or finish to order (ATO/FTO), configure to order (CTO), and engineer to order (ETO). These categories are often distinguished by their order fulfillment specifics and levels of customization.
- Manufacturing processes categorized by their role are: basic manufacturing processes, auxiliary manufacturing processes, serving processes, managerial processes.
- Manufacturing processes categorized by the level of automation are: manual processes, machine-manual processes, machine processes, automated processes, fully automated processes.
- For a manufacturing company, it is necessary to understand exactly which model they are using and to know what advantages and limitations exist for this type of production process in the planning of production and purchasing, pricing, customer relation management, etc.
You may also like: Statistical Process Control – A Manufacturer’s Guide