What is Throughput Time in Manufacturing?
Throughput time is an important KPI in manufacturing management, helping companies to improve performance both on the shop floor and in the supply chain. Let’s take a deeper dive into the metric.
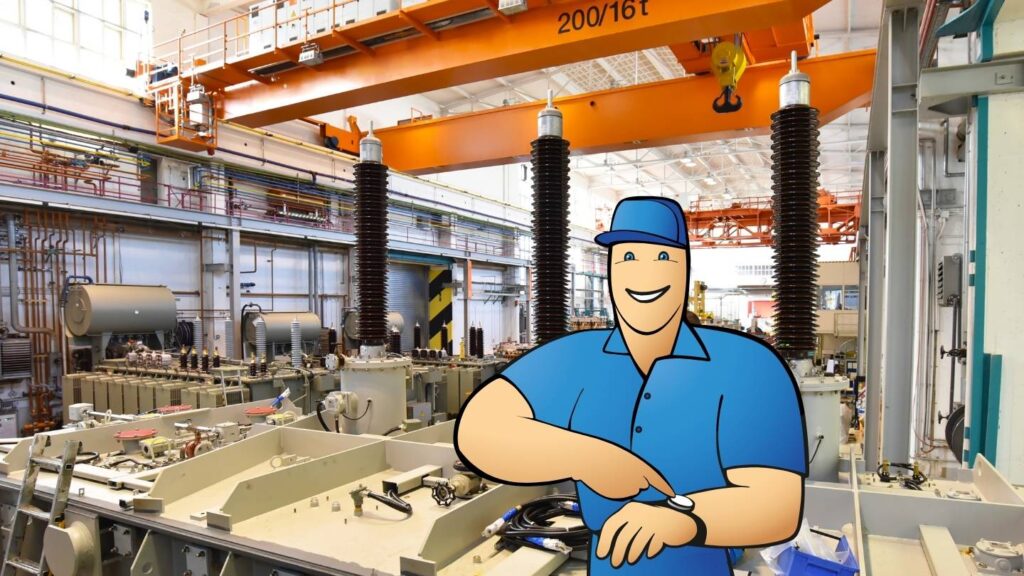
What is throughput time?
Throughput time is the amount of time it takes to manufacture a product from start to finish. Measuring throughput time starts with moving raw materials to the shop floor and ends with a finished unit or batch that is ready to be shipped. As such, it is an important metric for assessing your production efficiency and improving shop floor workflows, but also a key aspect of supply chain planning, forecasting, capacity planning, and production scheduling.
Components of throughput time
In addition to the actual time the product spends in the processing stage, throughput time also includes inspection time, moving time, and queue time. Let’s take a closer look at these four components:
1. Processing time
Processing time is the time a unit or a batch of goods takes to be processed. This includes only value-added activities such as blending, spinning, machining, assembling, etc.
2. Inspection time
Inspection time is the time taken to check a product or component for quality and compliance with specifications. It includes quality control activities such as testing, measuring, and visual inspections.
3. Move time
Move time encompasses the movement and staging of raw materials, components, work-in-process (WIP), and finished goods. This includes both the moving of goods to and from the production areas as well as between workstations.
4. Queue time
Queue time, also known as wait time, is the time a product spends waiting in line before the next step in the production process. It typically occurs due to resource constraints, such as machine unavailability, bottlenecks, or scheduling inefficiencies. While queue time does not add value to the product, it is included in the overall throughput time, as it impacts the total time required to complete the manufacturing process.
Calculating throughput time, therefore, follows the formula:
Throughput time = Processing time + Inspection time + Move time + Queue time
Throughput time vs. throughput rate
While throughput time measures the time it takes for a product to be finished, throughput rate refers to the number of units completed within a set period of time, typically per hour or per day.
Like throughput time, throughput rate is an important metric for evaluating the efficiency of manufacturing processes. A higher throughput rate indicates that the manufacturing system is operating at an optimal level, producing more output within a set period. Conversely, low throughput rates may indicate bottlenecks, inefficiencies, or capacity limitations within the production process.
To calculate your throughput rate, use the following formula:
Throughput rate = Finished units / time
For example, let’s say that a team completed 40 widgets in an 8 hour shift. The hourly throughput rate in this case would be:
Throughput rate = 40 / 8 = 5 units/hour
Throughput time vs. cycle time vs. lead time
Throughput time is often also confused with other time-based metrics, especially cycle time and lead time. Let’s take a look at what sets them apart.
Throughput time is the total time spent to manufacture a product, starting from moving the materials to the shop floor and ending with the finished item being taken into stock.
Cycle time is the time a single workstation spends processing one unit or batch of goods. When a manufacturing process consists of several subprocesses, cycle time is measured separately for each of them. For example, the production of a wooden table could consist of 1) assembly and 2) finishing. Therefore, the processing time portion of throughput time consists of all the cycle times in the production process sequence.
Lead time, however, could mean different things. Order lead time, or customer lead time, is measured from receiving a customer order to the final delivery of the full order. This includes purchasing the required raw materials as well as transportation time. Production lead time is a similar concept to throughput time, but it is measured from the creation to the completion of a manufacturing order.
Benefits of tracking throughput time
An essential manufacturing KPI, throughput time can be used to assess and improve various aspects of your operation.
Streamlining production processes
By tracking throughput time, businesses can set benchmarks and identify inefficiencies in the production process, such as delays or bottlenecks. This allows for adjustments to be made, ensuring smoother workflows and improving overall operational performance.
Improving profitability
Reducing throughput time minimizes labor and machine costs while increasing the production output. These efficiency gains lower operating expenses and improve margins, contributing to better profitability.
Aligning production planning with customer demand
Knowing the exact throughput time enables manufacturers to plan production schedules that meet customer demand without overproducing or underproducing. This ensures on-time delivery and reduces backorders or excess inventory.
Improving production planning
Accurate throughput time data allows for better scheduling and resource allocation. Production planners can set realistic goals that balance capacity and demand, avoiding overloading or underutilizing resources.
Reducing downtime
Identifying areas where machines or workers are idle helps to minimize downtime. By addressing these issues, manufacturers can keep the production line running consistently and efficiently.
Supporting inventory management
Tracking throughput time allows manufacturers to reduce work in progress (WIP) inventory by ensuring that materials and components move quickly through production. This reduces storage costs and the risk of overstocking or inventory obsolescence. In addition, knowing their throughput time enables manufacturers to create more accurate production schedules and forecast inventory requirements for specific periods, allowing them to prevent under- and overstocking.
Gaining a competitive advantage
Faster production and delivery times enable companies to respond more quickly to customer needs and changing market trends, giving them an edge over slower competitors.
Improving ROI on machinery and staff
By optimizing throughput time, businesses make better use of resources such as machinery, labor, and materials. The resulting efficiency improves the return on investment in production infrastructure and staff.
Improving quality
Well-monitored throughput times improve process consistency, which minimizes manufacturing defects and the need for rework, saving both time and resources.
Increasing customer satisfaction
Faster and more predictable production processes mean customers receive their orders promptly, which increases their satisfaction and fosters loyalty.
How to improve throughput time?
Improving your throughput time is essential for achieving higher operational efficiency and optimizing your whole business process. Here are some ways you could start reducing your throughput times:
Physically reorganize your facility
While modern factories are constructed with an optimized production flow to reduce movement and staging, many companies use older buildings or spaces not specifically designed for manufacturing. The key is to organize the layout of the space to facilitate a quicker flow of goods from inventory to production and back. Additionally, grouping related processes close to each other improves the flow rate and reduces unnecessary delays.
Improve inventory availability
Delays often occur due to missing or late-arriving inputs. By strengthening their supply chain management, manufacturers can ensure that raw materials and components are available when needed, keeping production on track.
Implement continuous improvement practices
Continuous improvement practices such as Six Sigma and Lean Manufacturing help identify inefficiencies and eliminate waste. They ensure that production processes are optimized, quality is maintained, and throughput time is consistently reduced.
Introduce automation
Automating repetitive tasks speeds up production and ensures consistent quality. Automation allows manufacturers to reduce manual errors and ensure timely delivery of the finished product.
Conduct regular maintenance
Preventative maintenance ensures machines operate efficiently and prevents unexpected breakdowns that disrupt processes and increase production time.
Implement real-time monitoring
Utilizing real-time data systems such as a manufacturing ERP software enables manufacturers to track production progress, identify bottlenecks, and address delays immediately. This helps maintain a steady flow of materials and ensures smoother transitions between processes.
Manufacturing ERP and throughput time
While most manufacturing ERP systems do not directly track throughput time, they do support various processes associated with it. By integrating key functionalities like production planning, inventory management, and shop floor management, ERP systems indirectly help monitor and reduce throughput time. Here’s how:
- Optimized production scheduling. Manufacturing ERP systems enable precise production planning and scheduling by balancing capacity and customer demand. This minimizes delays and reduces queue time, ensuring a smoother production process.
- Real-time monitoring. ERP systems provide real-time updates on production progress, helping manufacturers identify and address bottlenecks or downtime quickly. This ensures consistent workflows and shorter production cycles.
- Improved inventory management. By ensuring the timely availability of raw materials and components, ERP systems reduce waiting times and keep production running smoothly. This prevents unnecessary delays in throughput time.
- Better quality control. Manufacturing ERP systems track quality metrics and help discover issues that could lead to rework or delays. Efficient quality control processes maintain a steady throughput time while ensuring the finished product meets specifications.
- Streamlined business processes. ERP systems consolidate workflows and data, enabling manufacturers to streamline operations. By integrating multiple functions—like procurement, production, and delivery—ERP systems reduce manual errors and improve overall operational efficiency.
- Support for continuous improvement practices. Many ERP systems offer tools to implement lean and Six Sigma methodologies. These help manufacturers analyze data, identify inefficiencies, and implement improvements that reduce throughput time.
While ERP systems may not directly measure throughput time as a standalone metric, their ability to integrate and optimize business processes makes them a powerful tool for improving throughput time and achieving greater productivity.
Key takeaways
- Throughput time is the total time required to manufacture a product, from moving raw materials to the shop floor to creating a finished unit. It is crucial for evaluating production efficiency, improving workflows, and optimizing supply chain planning.
- Throughput time includes four components: processing time (value-adding work), inspection time (quality control), move time (transportation of goods), and queue time (waiting due to constraints or inefficiencies).
- Tracking throughput time helps streamline workflows, reduce downtime, align production planning with demand, minimize inventory costs, and improve profitability, ROI, and customer satisfaction.
- Companies can reduce throughput time by reorganizing production layouts, ensuring timely inventory availability, implementing Lean and Six Sigma practices, automating tasks, maintaining equipment, and utilizing real-time monitoring tools.
- Manufacturing ERP systems indirectly improve throughput time by optimizing production scheduling, managing inventory, enhancing quality control, streamlining operations, and supporting continuous improvement initiatives like Lean and Six Sigma.
Frequently asked questions (FAQ)
Businesses can use manufacturing execution systems (MES) or ERP software with real-time monitoring capabilities. These tools provide data on individual process times, help identify delays, and allow for tracking key metrics directly from the shop floor.
Metrics like throughput rate, overall equipment effectiveness (OEE), and lead time can be used alongside throughput time. Comparing these metrics with industry standards or historical data for similar processes helps identify if improvements are needed.
Companies should perform a bottleneck analysis to identify which component has the most significant impact on total throughput time. Factors like frequency of delays, cost implications, and alignment with production goals will help prioritize improvement efforts effectively.
You may also like: What Is a Production Cycle and How to Streamline It?