Things to look at when shopping for MRP software
If you are constantly thinking of the ways to improve your business efficiency and profitability, one thing to look into is the implementation of automated MRP system in your manufacturing operations. In this post we will explain why that will be such an important step and what to look for when choosing MRP software solution for your operations.
What does MRP mean?
MRP or MRP II, is also known as manufacturing resource planning – a system, which combines manufacturing, finance, marketing, engineering, purchasing and distribution together. Through the years, MRP has evolved from a method largely based on material inventory levels (MRP I) to a much more advanced planning methodology of manufacturing processes.
One of the main characteristics of Manufacturing Resource Planning is that the operating and financial system are the same. The financial figures are merely extensions of the operating numbers. The implementation of MRP systems also allows companies to simulate reality and make predictions to the future.
MRP is a whole company system, involving every facet of the business because the things that Manufacturing Resource Planning is concerned with – sales, production, inventories, schedules, cash flow, etc. – are the very fundamentals of planning and controlling a manufacturing or distribution business. The chart below illustrates this the best, showing how all the processes are connected with each other.
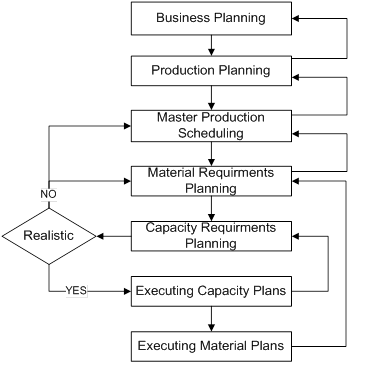
History of MRP software evolution
The development and increased interest of Manufacturing Resource Planning has become possible with the increased use of computers and their availability to the general population and businesses.
While the MRP II predecessor Material Requirements Planning (MRP I) was introduced in the 1960-s, it wasn’t until 1980-s, when the methodology has evolved into the MRP as we know it today. During the 1970-s the expansion of hardware and introduction of early PCs allowed to include some accounting functions and focus more on a business process as a whole. By 1975 there were around 700 manufacturing companies in the US employing the system.
Closed-loop business processes arrived in the 1980s and IBM was the major hardware vendor. During this period, the popularity of Manufacturing Resource Planning really took off. The business of the biggest manufacturing software vendors, like SAP and Epicor, has seen a sharp increase in demand.
Many smaller software companies, developing automated tools for manufacturers and other type of businesses have been established during that period as well. A small data sample below shows
1985 was a record year, with the highest number of new companies founded.
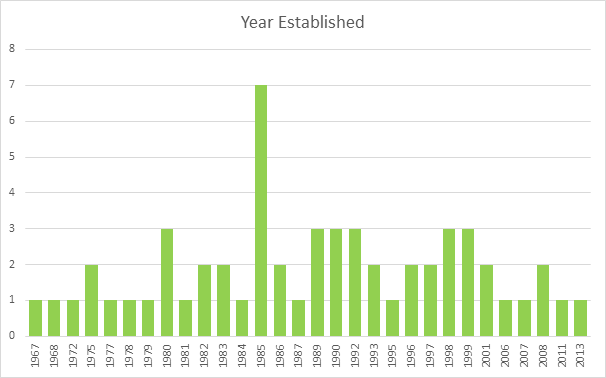
The 1990s witnessed a rapid growth in both hardware and MRP software systems with an emphasis on business process integration across and within all functional areas. The number of software and hardware options exploded. In the early 2000-s, after the
Today, the market of the different manufacturing and business software has seen an increased number of participants once again. The main role here played the introduction of new programming technologies that made creation of new software solutions much cheaper than before. In addition, the rising number of talented programmers has been helping as well.
While all this has a positive impact on the software industry, the increased number of offers on the market makes the job of a manufacturer is selecting the right software much more challenging.
You might also like – 10 Things You Need to Know Before Buying Manufacturing Software.
The use of outdated methods
Small businesses around the world start to understand the importance of a systematic approach in manufacturing. Still, many companies are using outdated methods for that.
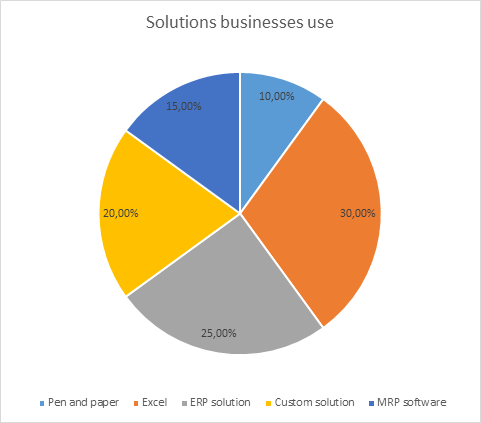
Despite the fact that the use of manual methods could result in the loss of valuable time, data and money, about 30% of businesses use either pen-and-paper methods or multiple Excel spreadsheets.
The advantages of using MRP software
There are several advantages of using MRP software solutions over manual tools.
Manufacturing is a complex process. Many things have to be taken into consideration, like inventory levels, logistics, distribution, sourcing, human and financial resources.
Connecting all these steps together manually will be very difficult and time-consuming. At the same time for a manufacturer, it is very important to be able to make necessary calculations and estimates of these factors very precisely, and in short period, on regular basis. The use of MRP software helps to reach this goal. Some of the benefits of using the software solution include:
- Lower inventory levels (25% decreases reported) while removing risk of stock-outs
- Reduction in lead times
- Better use of capacity
- Lowered risk of obsolete production
In comparison, the use of paper-based information systems and non-integrated computer systems that provide paper or disk outputs result in many information errors. This includes:
- Missing and redundant data
- Numerical errors that result from being incorrectly keyed into the system
- Incorrect calculations, based on numerical errors
- Bad decisions based on incorrect or old data
The biggest challenge
Companies that continue using outdated manufacturing planning methods are in clear disadvantage to their competitors that utilize modern software solutions. If your business is not using any MRP application it may be the right time to think about one, but how would you chose it?
Today over 200 different software packages advertise themselves as an MRP software suitable for small business. The reality, however, could not be further from the truth.
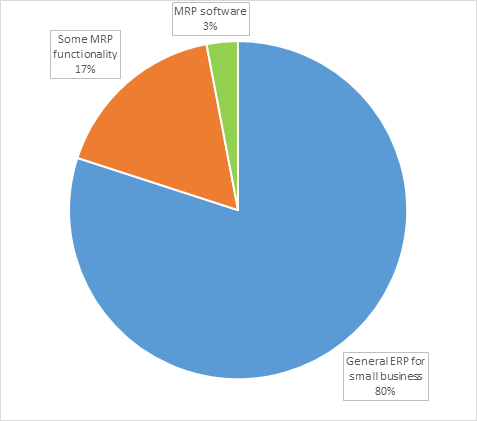
The majority of products available online, claiming to be MRP applications, can be used by manufacturers, like they can be also used by retailers, farmers, wholesalers, transporting companies and any other business – these are general ERP solutions. The problem with these products is that they are not designed specifically for manufacturers, thus they cannot perform all the important cycles of the MRP system, making it basically useless. About 80% of software packages claiming to be MRP applications fall under this category.
About 17% of programs available on the market right now are more suitable for the manufacturers, as they come with the BOM functionality – a possibility to divide a final product into components, thus creating demand for all material needed in production. While it is important functionality, it is not what MRP stands for today – Manufacturing Resource Planning (MRP II). Ability to get BOM makes possible to do material planning, but it is only one small part of the whole MRP II system.
Finally, the remaining 3% of software packages can be regarded as the true MRP software solutions, suitable for small manufacturer needs. Such applications combine the following special functionalities, making them much more useful that any general business software product out there:
- Inventory control and forecasting.
- Supply chain management.
- Production planning and control.
- Cost control.
- Equipment capacity planning and management.
- Workforce control, including payroll accounting.
- Extensive managerial statistics.
- Dynamic rescheduling.
- Serial numbers support for materials, subassemblies and final products.
- Matrix BOM – ability to set parameters for a product.
Conclusion
Selecting the right MRP software for your organization is like choosing a partner in your life – it is an important decision that will shape the way your business will develop in the future. When making decision, which MRP application to adopt a person responsible for this needs to take many things into account – implementation costs, ROI, whether the software is suitable for his business, etc.
Until now, the majority of software packages were suitable only for big and medium-sized companies, as they demanded a higher installation and maintenance costs. Some smaller companies continued to use outdated methods, putting them into clear competitive disadvantage. Others were opting for a cheaper and simpler general ERP solutions, that were not suitable for the
The good news is this situation is changing. To fill this gap, some software development firms, including MRPeasy, have started offering affordable and multifunctional SaaS manufacturing production solutions designed especially for small manufacturer’s needs. These products respond to the high requirements of the manufacturing industry and can easily compete with more established applications by functionality, as well as price.
You might also like MRP vs. ERP: Which Solution is Right for You?