Sustainable Manufacturing – 8 Best Practices for SMEs
In today’s rapidly evolving industrial landscape, sustainable manufacturing has emerged as a critical focus for businesses aiming to reduce their environmental impact while maintaining economic viability. This approach supports ecological balance while enhancing operational efficiency and brand reputation. In this post, we delve into the core aspects of sustainable manufacturing and explore its benefits and challenges.
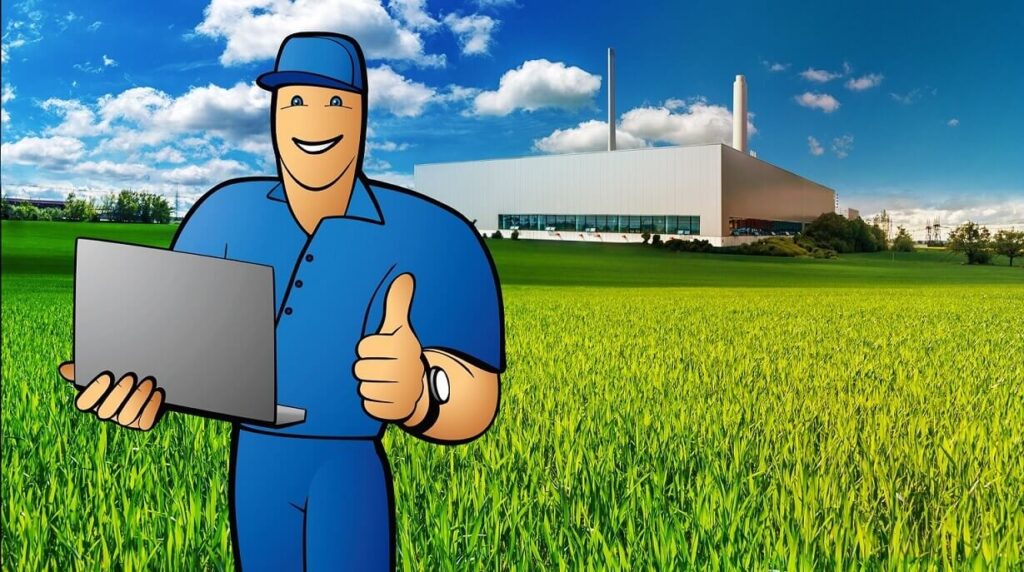
You can also listen to this article:
What is sustainable manufacturing?
Sustainable manufacturing refers to addressing and reducing the overall environmental impact of manufacturing operations. Several major areas have emerged in the past few decades that define sustainability in manufacturing practices. These include energy consumption and clean energy use, recycling and reuse in waste management, emissions reductions, cleaner product life cycles, circular economic initiatives, and more. Sustainability in manufacturing also entails adopting eco-friendly materials, reducing raw material use, and increasing the safety of employees, communities, and products.
Sustainable development as such is not limited to reducing environmental harm but also addresses social, economic, political, and cultural spheres. Sustainable manufacturing is an essential part of this global incentive to reinvent economic and social development.
A good example of this is the UN Sustainable Development Goals – 17 global priorities that range from achieving food security and accessible education to reforming consumption patterns and fighting climate change. Several of the UN goals pertain to sustainable manufacturing. For example, goal 9 emphasizes “Building resilient infrastructure, promoting inclusive and sustainable industrialization, and fostering innovation”, and goal 12 – “Ensuring sustainable consumption and production patterns”.
Sustainability goals can be applied to different organizational levels from legislation and markets to managerial or team-oriented focuses. For instance, on the institutional level, the ISO 14001 Environmental Management System helps businesses align with globally recognized environmental best practices. On a team level, a Green Team initiative may be implemented within a manufacturing plant, wherein employees from various departments form teams to work together in identifying and implementing sustainability projects like conducting energy audits or organizing recycling.
Aligning profitability with sustainability
Sustainable businesses aim for profitability just as much as conventional ones. The key difference is that “green businesses” opt to consider a wider range of economic and environmental factors in achieving their business goals.
While profitability and sustainability have been oppositional in the past, sustainability has become a standard expectation in many global markets. Regulations, stakeholder interests, investment opportunities, and consumer preferences are all rapidly shifting toward sustainability. As a result, investing in sustainable practices and reducing the carbon footprint of operations are becoming top priorities in a growing number of manufacturing sectors.
Sustainable practices also make companies more resilient to environmental risks and supply chain disruptions. By reducing dependence on non-renewable resources, for example, companies may well mitigate some of the impact of fluctuating raw material prices. Embracing sustainability also fosters innovation, encouraging the development of new technologies and processes that can open up additional revenue streams and markets.
The shift towards green business models in manufacturing is a practical move to align profitability with sustainability. As the world increasingly adopts green initiatives, businesses that embrace sustainability are likely to lead the market, gaining competitive advantages along the way.
The core principles of sustainable manufacturing
Sustainable manufacturing involves various principles that help reduce environmental impact and improve efficiency along the way. Here are the core principles.
Energy efficiency and emissions
Energy efficiency is a cornerstone of sustainable manufacturing. Incentives primarily focus on using more efficient machinery and equipment to reduce overall energy consumption and implementing energy management systems to monitor and optimize energy use. Local grid and self-sustained power management are promising avenues to drive efficiency and bring down energy costs. Another prominent trend is transitioning away from fossil fuels and opting for renewable energy sources, resulting in lower carbon emissions as well as simplified compliance.
Addressing emissions is an equally crucial aspect of green manufacturing. Accurately measuring and reporting emissions helps companies identify key areas for reducing their carbon footprint and implement targeted strategies to further drive energy efficiency. For example, the Environmental Protection Agency (EPA) recommends establishing GHG inventories to help differentiate emissions sources and implement mitigation strategies.
Waste management
Waste reduction and optimized raw material usage are among the most impactful ways to increase sustainability in manufacturing. Lean manufacturing principles can minimize all kinds of waste production at different stages of the manufacturing process. Moreover, establishing systems to recycle and upcycle materials and reuse components whenever possible reduces raw material use while aligning the operation with waste reduction incentives.
Additionally, investing in R&D to develop or adopt eco-friendly materials and implement pollution control measures is crucial. These can significantly decrease waste generation and help ensure compliance with environmental regulations. By focusing on sustainable packaging solutions and reducing single-use plastics, manufacturers also contribute to environmental conservation while enhancing operational efficiency, cost-effectiveness, and aligning with customer expectations.
Sustainable supply chain management
Assessing suppliers based on their environmental practices and choosing partners who prioritize sustainability ensures the entire supply chain supports sustainable practices. Sourcing materials locally reduces transportation emissions and supports local economies, while often increasing resilience due to shorter supply chains.
Implementing production tracking systems for transparency and traceability throughout the supply chain further allows for better monitoring of environmental impacts, which fosters sustainability while also helping to build up supply chain resilience.
Circular product lifecycle
Designing sustainable products with longer lifespans reduces the frequency of replacement and the resulting waste. Planning for the end of a product’s life cycle by designing for disassembly, recycling, or repurposing minimizes waste and maximizes resource utilization. Adopting circular economy principles, wherein materials are continuously cycled back into the supply chain, reduces the need for virgin resources.
Environmentally friendly, biodegradable, or recyclable materials help reduce the negative environmental impact of products. By incorporating sustainability into the product design process, the ecological impact of manufactured goods is considered throughout their life cycle, from raw material extraction to disposal.
Optimized manufacturing processes
Continuously improving manufacturing processes to also consider sustainability goals enhances production efficiency while reducing resource consumption and minimizing waste. For example, investing in automation and advanced manufacturing technologies increases precision, reduces manual errors, and optimizes resource use at the same time.
Additionally, adopting data-driven approaches like predictive maintenance or real-time monitoring can significantly improve process reliability and reduce downtime. By utilizing IoT devices and artificial intelligence-driven analytics, manufacturers can anticipate equipment failures before they occur, preventing costly interruptions and ensuring that machinery operates at peak efficiency.
Key challenges of increasing sustainability for SME manufacturing companies
Despite complex efforts to address sustainability in manufacturing, manufacturers, especially small and medium-sized enterprises (SMEs), face numerous challenges when striving to increase sustainability. These range from financial constraints and technological limitations to a lack of local incentives and regulatory compliance. Let’s go over some key challenges faced by small and medium manufacturers in achieving more sustainable manufacturing practices.
Financial constraints
One of the most significant challenges for SMEs in adopting sustainable practices is the financial burden. Transitioning to greener technologies often requires substantial upfront investment, which can be prohibitive for smaller firms with limited capital. This includes costs associated with purchasing energy-efficient equipment, integrating renewable energy systems, and implementing waste reduction technologies. While long-term savings and efficiencies are a benefit, the initial costs can deter companies from making necessary changes. Securing the necessary funding to make these investments can be challenging due to limited access to financial resources and investment opportunities.
Another limiting factor is that the return on investment (ROI) for sustainable practices may not be immediate, making it harder for smaller companies to justify the expenditure. SMEs often operate with tight profit margins and short-term financial goals, complicating the allocation of funds for projects that do not offer quick returns. This is compounded by the need for ongoing investments in maintenance, training, and continuous improvement to sustain the benefits of sustainable practices.
Technological barriers
Implementing advanced technologies that support sustainability, such as energy-efficient machinery, manufacturing automation, and renewable energy systems, can be challenging. SMEs often lack the technological infrastructure and expertise needed to integrate these solutions effectively. The rapid pace of technological advancements requires continuous investment in both equipment and training, which can be daunting for smaller firms.
Here too, the initial cost of acquiring and implementing new technologies can be prohibitive, and the integration process disruptive to existing operations. Companies may also face difficulties in sourcing reliable suppliers and partners who can provide the necessary technology and support. This gap often hinders the ability of small manufacturers to compete with larger companies with more resources to invest in state-of-the-art solutions.
Regulatory compliance
The regulatory landscape for environmental compliance is complex and constantly evolving. Manufacturers face a myriad of local, national, and international regulations. Understanding and adhering to these regulations requires resources that many SMEs struggle to allocate, especially as navigating through regulations can be cumbersome without dedicated compliance teams.
Moreover, failing to comply with these regulations can limit freedom to operate and result in legal penalties, damaging the company’s reputation. SMEs may also find it challenging to stay updated with the latest regulatory changes and implement the necessary adjustments promptly. This regulatory burden is further intensified by the need to meet the sustainability expectations of larger companies in their supply chain, which often impose stringent environmental standards.
Supply chain complexity
Achieving sustainability is not limited to internal practices, it extends to the entire supply chain. Producers often need to ensure that their suppliers also adhere to sustainable practices, which can be difficult to monitor and enforce. Smaller companies often have less leverage over vendors as compared to larger corporations. Ensuring transparency and traceability in the supply chain is crucial for sustainability but this too requires significant resources and coordination.
Global supply chains can be complex and fragmented even without sustainability goals, complicating consistent sustainability practices across vendors. Variations in environmental regulations and standards across different regions can further complicate efforts to implement uniform practices.
Employee engagement and training
Engaging employees in sustainability initiatives and providing the necessary training is another hurdle. Changing the organizational culture to prioritize sustainability requires concerted effort and commitment from management. Employees need to be educated about the importance of sustainability and trained in new practices and technologies, which can be time-consuming and incur extra costs.
Furthermore, sustaining employee engagement in sustainability initiatives can be challenging, especially when the benefits are not immediately visible. Providing continuous training and development opportunities is essential to keep employees updated on the latest sustainability trends and practices.
Lack of standardized metrics
Finally, another significant challenge in increasing sustainability is the lack of standardized metrics. Unlike well-established financial metrics, sustainability metrics can vary widely, complicating consistent reporting. Standardized metrics are crucial for benchmarking performance, setting goals, and ensuring transparency. Without them, it becomes challenging to compare progress against industry standards or peers.
The lack of consistency can hinder communication with stakeholders like investors, customers, and regulatory bodies, who increasingly demand clear and comparable sustainability reports. SMEs often struggle to identify which data to collect, how to interpret it, and how to report it effectively. Moreover, the inconsistency complicates integrating sustainability into overall business strategies. This misalignment can lead to inefficiencies and missed opportunities for improving environmental performance and gaining competitive advantages.
Best practices for implementing sustainable manufacturing practices
Successfully implementing sustainable manufacturing practices requires a holistic approach to operation management. Here are 8 best practices to guide manufacturers, especially SMEs, in their sustainability journey.
1. Take a long-term perspective
Focusing on long-term gains is crucial for sustainable manufacturing. Companies should stay proactive about economic opportunities that align with sustainability goals. This means looking beyond immediate financial returns and considering the broader impact of sustainable practices on operational efficiency, brand reputation, and market positioning.
Being proactive involves staying informed about emerging trends and technologies in sustainability. This stance allows companies to adapt faster to changing market demands and regulatory requirements, ensuring they remain competitive and compliant while capitalizing on economic opportunities.
2. Consult with local and regional governing bodies
Engaging with sustainability organizations and other governing bodies can provide valuable support and open up new possibilities for sustainable practices. By signaling a proactive stance, companies gain access to resources, incentives, and guidance that might not be available otherwise. Local government programs often provide efficiency incentives, grants, and other forms of assistance to businesses that commit to sustainability initiatives.
Consultation can also help companies stay ahead of regulatory changes and align their practices with local sustainability goals. This collaboration fosters a positive relationship with regulators and the community, enhancing reputation and facilitating smoother project implementations.
3. Environmental project management
Investing in environmental project management is essential for navigating the complexities of sustainability initiatives. Depending on their capabilities, manufacturers should consider hiring consultants or compliance experts to help identify challenges and uncover opportunities. These professionals can provide valuable insights and strategies for achieving sustainability goals efficiently and effectively.
Environmental project management ensures that sustainability projects are well-planned, executed, and monitored. This approach helps companies avoid common pitfalls and maximize the benefits of their sustainability investments, fostering beneficial environmental and economic outcomes.
4. Leverage existing solutions
Increasing the efficiency of existing production processes can be a huge leap toward sustainability without requiring large capital investments. For example, relatively simple energy-saving measures like optimizing equipment usage or enhancing maintenance routines can constitute significant leaps toward cost and energy savings. Furthermore, adopting just-in-time manufacturing principles can greatly help reduce waste and improve overall efficiency.
Another example is using digital tools and software to streamline operations and reduce resource consumption. Many affordable and scalable solutions, such as cloud-based manufacturing software, can help SMEs manage their processes more efficiently and sustainably.
5. Adopt continuous improvement workflows
Continuous improvement (CI) initiatives are particularly beneficial for SMEs as they focus on incremental changes that can lead to significant improvements over time. Using methodologies like the Plan-Do-Check-Act (PDCA) cycle helps companies systematically identify areas for improvement, implement changes, monitor results, and make continuous adjustments.
Adopting CI initiatives fosters a culture of ongoing enhancement, enabling companies to stay proactive in their sustainability efforts. Next to raising efficiency, this also helps ensure that sustainability becomes an integral part of daily operations and long-term strategy.
6. Invest in manufacturing software
Investing in production efficiency is a cornerstone of sustainable manufacturing. Implementing a manufacturing system like an MRP/ERP system can significantly enhance efficiency and control costs. Solutions like MRPeasy, which are purpose-built for SMEs, offer affordable and scalable options to effectively manage inventory, production, and supply chain processes.
By optimizing production, companies can reduce waste, improve resource utilization, and increase overall operational efficiency. This investment, too, pays off in both environmental and economic terms.
7. Incorporate sustainability practices with HR
Integrating sustainability practices within human resources is vital for fostering a culture of sustainability. This includes training employees on sustainable practices, encouraging participation in sustainability initiatives, and aligning performance metrics with sustainability goals. By making sustainability a part of the company’s ethos, employees are more likely to engage and contribute to environmental efforts.
Promoting a sustainable workplace can also attract new talent who value environmental responsibility, further enhancing the company’s reputation and employee satisfaction. This alignment ensures that sustainability is embedded in all aspects of the business, from operations to workforce.
8. Pinpoint and monitor performance metrics
Identifying key performance indicators (KPIs) that correlate with sustainability simplifies tracking the environmental impact of operations alongside productivity. Transparent reporting of sustainability metrics enhances credibility and accountability, building trust with customers, investors, and regulators. It also provides a clear framework for setting and achieving sustainability goals, driving continuous improvement and innovation in sustainable manufacturing practices. Relevant examples include:
- Overall Equipment Effectiveness (OEE) measures the efficiency of manufacturing equipment. By improving OEE, companies can reduce downtime and increase production efficiency, which in turn reduces energy consumption and waste. Monitoring OEE helps identify areas where energy and resource efficiency can be improved, leading to a lower environmental footprint.
- Inventory turnover measures how often inventory is sold and replaced over a specific period. High inventory turnover indicates efficient inventory management, reducing excessive storage and minimizing waste. As such, efficient inventory management helps decrease energy usage associated with storage and reduces the risk of obsolete inventory.
- Scrap Rate measures the amount of material wasted during the production process. By minimizing scrap, companies reduce raw material consumption and waste generation. Lower scrap rates contribute to more sustainable manufacturing practices by helping to conserve natural resources.
- Cycle Time. Cycle time measures the time it takes to complete one production cycle. Shorter cycle times indicate more efficient production processes, leading to lower energy consumption and reduced emissions. Optimizing cycle time can also improve overall production efficiency, further contributing to sustainability goals.
Key takeaways
- Sustainable manufacturing is the process of producing goods in a way that minimizes environmental impact, conserves energy and natural resources, and is safe for employees, communities, and consumers. It aims to balance economic viability with ecological responsibility and social well-being.
- The core principles of sustainability in manufacturing include energy efficiency, waste management, sustainable supply chain management, circular production lifecycles, optimized manufacturing processes, and green product design.
- Several key challenges hinder the implementation of sustainable practices with financial constraints, technological barriers, and regulatory compliance issues remaining most prominent. Supply chain complexity and lack of standardized metrics are also significant obstacles. Addressing these challenges requires strategic planning, investment, and collaboration across the industry.
- SMEs particularly face unique challenges as limited resources, lack of technological infrastructure, and difficulties in navigating complex regulatory environments make it harder for smaller companies to adopt sustainable practices. Additionally, SMEs often have less influence over their supply chains, further complicating sustainability efforts.
- Best practices for SMEs to implement sustainable manufacturing include taking a long-term perspective, consulting with local and regional governing bodies, investing in environmental project management, adopting continuous improvement initiatives, investing in manufacturing software, and pinpointing relevant performance metrics.
Frequently asked questions
Sustainability in manufacturing often depends on the specific industry and context, but generally, methods that incorporate lean manufacturing principles, energy efficiency, waste reduction, and the use of renewable resources are considered highly sustainable. For example, lean manufacturing minimizes waste by optimizing processes and resource use and techniques such as Just-In-Time (JIT) production help reduce excess inventory and improve efficiency. Adopting circular economy principles, recycling, and reusing materials further enhances sustainability. Utilizing renewable energy sources and implementing automation and real-time monitoring also contribute to sustainable manufacturing practices.
Sustainable manufacturing involves several key elements. Energy efficiency and a focus on reducing waste through recycling and using eco-friendly materials are crucial. Sustainable supply chain management practices help ensure that suppliers adhere to environmental practices. Designing products with longer lifespans and planning for recycling to support a circular product lifecycle is also important. Finally, an important and cost-effective avenue toward sustainability is adopting continuous improvement in manufacturing processes.
Sustainable manufacturing is vital for process plants because it reduces environmental impact by lowering waste and emissions, and ensuring compliance with regulations. It also enhances economic efficiency through cost savings from improved processes and reduced energy consumption. Sustainable practices boost market competitiveness as consumers increasingly prefer environmentally responsible brands. Additionally, sustainable practices enhance resilience to environmental risks and supply chain disruptions.
Measuring ROI involves assessing both the direct and indirect benefits of sustainable initiatives. Direct benefits include cost savings from reduced energy and raw material use, lower waste disposal fees, and compliance cost savings. Indirect benefits may include improved brand reputation, increased customer loyalty, and access to new markets. Sustainability reporting methods and production software can help track these metrics and quantify the financial gains from sustainability efforts. SMEs can also compare baseline metrics before and after implementing sustainable practices to gauge improvements and ROI.
You might also like: What Is Distributed Manufacturing?