Supply Chain Planning – A Quick Guide
Recent years have seen unprecedented disruption in the global economy. Large-scale events such as trade wars, tariffs, COVID-19, and port throughput issues have created massive pressure on the company’s supply chains.
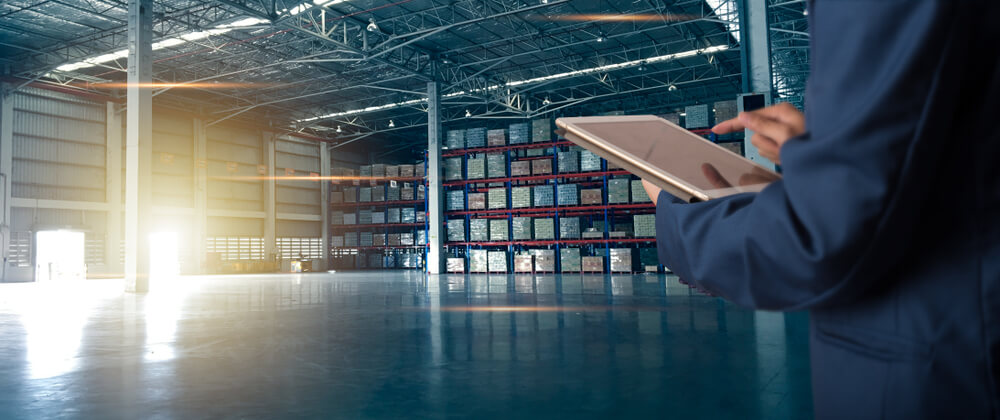
Before these events, the global economy had settled on a lean model of supply chain management that included low-interest rates, low inflation, predictable throughput, and stable transportation costs. But the past few years have shaken this model, and supply chain professionals are now forced to re-evaluate how demand and supply are forecasted.
As an integral part of this system, supply chain planning is undergoing changes that merit a refresher in basics and strategies moving forward. This guide will help manufacturers in small and medium-sized businesses understand those basics to plan a model and map out a strategy for their supply chain planning efforts.
What is Supply Planning?
Supply planning is first and foremost the anticipation of how much demand for products there is in the market. By predicting and forecasting that demand accurately, supply planners can develop a schedule to ensure that raw materials and components arrive in time to meet that demand.
Supply planning is the oversight process that keeps purchasing, operations, receiving, shipping, inventory control, and other supply chain functions coordinated and optimized. This process means that supply planning has responsibility for what happens inside the factory and for a complex web of activities outside the factory, such as vendor actions, transportation, logistics, and even inventory control.
Advantages of Supply Planning
Supply planning offers manufacturers many advantages. Small and medium-sized companies often undertake supply chain planning using spreadsheets, paper records, informal conversation, and other manual task-driven components. But as companies grow, those undergoing scale or seeking to become more competitive relative to others within their industry must move from an ad hoc, fragmented system to a more formal supply planning system.
Adopting a systemized supply planning model offers several advantages:
- More Efficient – Companies using formal supply planning systems can realize more efficiency in their operation. This efficiency includes both manufacturing operations and functional areas outside manufacturing. Tasks can be automated, records are closer to real-time, and vendor relationships, contracts, and performance are tracked accurately. Through tight coordination in supply planning, the factory can become more efficient and confident that what they need will be there in the right amounts at the right time.
- More Streamlined – Formal supply planning helps streamline manufacturing company’s operations. With informal systems, tasks may be redundant or forgotten until a crisis arises, and expensive expediting is required to get the factory back on track. With each functional area performing in a coordinated supply plan, critical areas such as inventory control, WIP, and delivery schedules can be forecasted accurately and optimized.
- Lower Costs – Supply planning makes sure that resources are not only at the factory in the correct quantity at the right time. It also uses formulas, software, and accurate market data to ensure that the flow is neither too much nor too little. This practice allows companies to control shipping and logistics costs and holding costs associated with inventory and excess WIP.
- Greater Customer Confidence – Customer loyalty and building brand reliability are critical in today’s hypercompetitive manufacturing environment. With a dependable and accurate supply plan, companies can deliver products on time and develop strategies to improve deliveries. This improvement builds customer satisfaction and drives future demand.
Multi-Level Supply Planning
It is crucial for small and medium-sized manufacturers to understand that supply planning doesn’t consist of a single linear approach. The best and most sophisticated supply planning models recognize three distinct categories of planning that must be considered.
These categories look at the supply plan from both a macro and micro level to develop a comprehensive plan covering both short- and long-term demand.
These categories include:
Strategic Planning – Manufacturers must look at their long-term supply challenges and make decisions over a more extended period. Strategic planning means seeing the big picture. This big picture includes facility location, outsourcing versus in-house warehouse management, long-term vendor selection and contracts, Capex planning on supply chain infrastructure, and performance metrics. The strategic supply planning function drives the more focused categories of the supply plan.
Tactical Planning – While the strategic planning level answers the “W” questions of where, when, and why of the supply chain, the tactical level addresses the “how” of things. How will these tasks be accomplished? How will work be delegated and tasks be completed? This means managing factory capacity and production schedules, and it also means evaluating software that best suits the factory and its products. Tactical planning also involves contingency planning and metrics for how the functions will be carried out.
Operational Planning – With the why and how mapped out into a formal supply planning system, manufacturing companies can proceed with operational planning. This is where the details and execution of everyday tasks in production are done. This includes daily, weekly, and monthly forecasts and schedules for process and labor. It also means day-to-day oversight of the flow of goods and materials and the performance of vendors to established contract terms. Operational planning also involves resolving the everyday issues that pop up as bottlenecks (missed delivery, off-quality raw materials, etc.). And it means managing the metrics used to measure performance and auditing daily functions such as inventory control, WIP, quality fallout, shipping, and receiving.
Elements of Supply Planning
With an understanding of the supply planning categories, it will be time to put this knowledge into action. There are several components in a robust and effective supply planning system.
- Demand Planning – Demand planning is essential in any supply plan. Demand planning requires information and data from sales and marketing, historical analysis of sales, or sophisticated demand sensing tools and software. By understanding the demand and creating a reliable demand forecast, planners can design an accurate supply plan to meet demand.
- Sourcing – Given today’s volatile supply environment, sourcing is a critical component and one that is changing most supply planning models. Previous sourcing strategies have relied upon far-flung suppliers from across the globe. Now, many manufacturers are moving to reshoring or nearshoring their sources to bring them closer to the point of production. They are also re-evaluating their stance on minimum order quantities, given the strain on transportation and logistics.
- Inventory Control and Optimization – During the disruptions that affected most of 2020, as high as 28% of businesses saw shortages on critical components. Supply plans must utilize accurate software native to their MRP or ERP system to help manage this quickly evolving environment. Many companies have moved slightly away from lean inventory management and have re-evaluated their stance on buffer stocks and vendor-managed inventory.
- Production and Scheduling – Factories depend upon material being where it is needed when it is required, and in the right quantities. Again, the software can aid supply planners to help them keep track of WIP and raw material and component transactions as they make their way through production. This visibility is critical to making the right decisions and purchasing materials needed to meet the schedule.
- Quality and Returns – No manufacturer wants off-quality or returned finished goods. But the reality is that it happens. These two categories represent waste and must be adjusted within the supply plan. Again, best-in-class ERP and MRP software will have quality and return auditing and management functionality that will allow automatic adjustments to supply plans based on the material that needs to be replaced.
- Standardized SOPs – Standardized operating procedures help supply planners make the correct decision. By documenting processes within the supply chain, many supply planning tasks become automated, eliminating the bias and ambiguity that may occur from buyer to buyer or from different interpretations of fast-moving data between team members. Standardized SOPS also helps coordinate with other supply chain elements such as demand planning, marketing, sales, inventory control, and others.
- End-to-End Visibility – Today’s supply chains are increasingly complex, and it is virtually impossible to manage them manually. With robust, best-in-class software, companies can achieve end-to-end visibility of the entire supply chain. With unsiloed data, supply chain planning can be executed more accurately and planners can respond to real-time challenges more effectively. This helps align demand, supply, operations, and S&OP planning so that the supply chain works seamlessly for everyone.
With increasing complexity and a shifting supply and demand environment, supply planning is more challenging than ever. By incorporating the components above into a standardized supply chain strategy across all categories, manufacturers can develop a plan that fits their industry. And when augmented by software, supply planning can be further streamlined to reduce costs, optimize processes, and improve visibility and supply plan performance.