Top 11 Supply Chain KPIs – Guide for 2025
Understanding and monitoring supply chain dynamics is essential for maintaining efficient inventory and production operations. In this guide, we outline the top 11 supply chain KPIs to help you focus on critical areas of your supply chain performance.
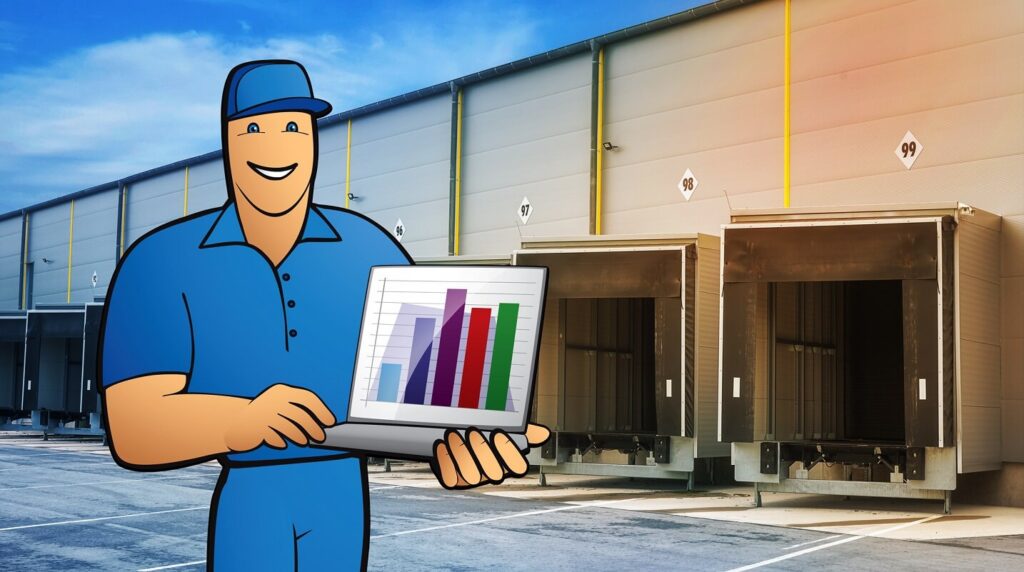
What are supply chain KPIs?
Supply chain KPIs are key performance indicators relevant to the logistics of manufacturing or distribution operations. They help measure and provide benchmarks for a wide range of supply-related processes from supplier performance and different lead times, to inventory turnover and stock quality. Tracking these KPIs is an important part of overall supply chain management.
It’s worth noting that the term key performance indicator is not synonymous with metric. A metric can be essentially any measurable process. KPIs, however, build on metrics, making them relevant in a specific context, thus providing actionable insights into the performance of processes. For example, the number of times a vendor accepts an order is a supply chain metric. However, the number of times a vendor accepts an order out of all order requests it receives within a period can be a relevant KPI.
Measuring the effectiveness of the supply chain over time is crucial for snuffing out inefficiencies. Since procurement is a key aspect of inventory and manufacturing, effective supply chain management is a prerequisite for the optimal functioning of inventory and the overall production effort.
Picking the right KPIs to measure
Supply chain key performance indicators span a wealth of different metrics. Deciding which ones to track should be thoroughly thought out to ensure they align with business goals and uncover efficiency insights. Focus on the most important questions that need to be addressed. These can vary by business strategy, type of business, or even industry or company age.
For instance, newer businesses could put more effort into gauging the customer experience, thus putting focus on quality and customer expectations. At the same time, established companies that need to increase logistics efficiency should prioritize lead time optimization or capacity utilization.
Here are some suggestions for picking the KPIs to track:
- Come up with the most important topics you need insights for. For instance, can the shipping department be further optimized; how often do we miss order deadlines, how many outgoing orders have quality issues, are our raw material suppliers up to par, etc?
- Make sure the selected KPIs are actionable. The S.M.A.R.T methodology helps ensure the relevance of selected metrics. SMART stands for, Specific, Measurable, Achievable, Realistic/Relevant, and Time-bound. The selected KPIs should all clearly meet SMART criteria.
- Don’t track too many KPIs. Monitoring too many KPIs can be overwhelming and counterproductive, especially at the beginning. Start with a few critical metrics and consider expanding only as your capacity for data analysis grows.
- Track KPIs regularly and diligently. Tracking performance needs to be consistent and periodic. More volatile performance metrics such as production capacity or picking efficiency can be tracked daily, while for others, a weekly or bi-weekly period might suffice.
- Compile KPI dashboards. Performance dashboards provide an excellent wide-perspective view for managers for gaining insights into business health and dynamics. Dashboards not only simplify compiling and categorizing metrics, but they might also unlock deeper insights into data and help uncover interrelations. Many good logistics or traceability software include built-in KPI dashboards.
- Choose a manufacturing software with automated reporting. When picking a production or inventory management tool, ensure the software supports tracking diverse metrics. This helps streamline data collection and analysis, providing insights on various performance metrics through automated reports, thus enhancing data-based decision-making. For example, MRPeasy includes over 70 automated reports on a range of metrics from cost and order data to component traceability, lead times, etc.
- Regularly review and adjust KPIs. Business environments are dynamic, this goes doubly so for supply chains and logistics. What works today might not be relevant tomorrow. Periodically assess your KPIs to ensure they remain aligned with your strategic objectives and make adjustments as necessary.
Top 11 supply chain KPIs for small manufacturers
Here are the 11 most important supply chain KPIs we suggest looking into in compiling your performance dashboard, divided into four groups, based on type.
Delivery performance KPIs
On-Time, In-Full (OTIF)
Achieving timely and error-free deliveries is perhaps the most important task of effective supply chain management. This goes both for purchase orders as well as sales. In this regard, OTIF, or On-time, In-full, is probably the most important KPI in supply chain management.
OTIF consists of two basic metrics – the on-time delivery rate and the in-full delivery rate. Achieving both is crucial from a customer satisfaction point of view. Keeping to promised delivery times is far from ideal if they’re incomplete. In the same vein, dispatching complete packages but missing deadlines can hurt the business. OTIF, therefore, combines these metrics to stress the importance of both.
OTIF is calculated by dividing the number of orders that are delivered in full and on time by the number of total deliveries.
OTIF = On-time deliveries fully delivered / Total deliveries
Perfect order rate
An even more complete version of the above KPI is the Perfect order rate, sometimes also called the Order accuracy rate. This KPI additionally takes into account damage-free deliveries, which tracks the rate of deliveries completed without any damage from shipping or handling, as well as accurate documentation of the order fulfillment process.
Perfect order rate can be calculated by subtracting the number of orders with errors in them (whether not on time, not in full, damaged, or missing documentation) from the total number of orders, divided by the total number of orders. This is then multiplied by 100 to provide a percentage value.
Perfect order rate = ((Total number of orders – Number of orders with errors) / Total number of orders) × 100
Fill rate (FR)
Fill rate is another KPI for gauging the success rate of your business’s logistical operation. It tracks the percentage of outgoing orders that were fulfilled out of all incoming orders you received for a time period.
Fill rate = (Total number of orders fulfilled / Total number of orders placed) × 100
For example, suppose you received 50 orders last quarter and managed to successfully fulfill 42 of them. This makes the Fill rate 42 / 50 × 100 = 84%.
Different versions of the Fill rate KPI are in use. The order fill rate measures the success rate of all outgoing orders, while the line fill rate measures the percentage of line items shipped, and the item fill rate does the same per SKUs (Stock keeping unit).
Inventory-centric supply chain KPIs
Inventory turnover rate
The inventory turnover rate KPI measures the number of times inventory is cycled through – used and replenished over a period of time. In other words, ITR returns the inventory-to-sales ratio of a company. It’s calculated by dividing the cost of goods sold (COGS) by the average inventory (beginning inventory value added to the ending inventory value, divided by 2), thus indicating the level of synchronization between purchases and sales.
Inventory turnover rate = COGS / Average inventory
The inventory turnover ratio is one of the most important overall inventory management KPIs. Tracking it can provide insights into a business’s financial health as well as its supply chain and inventory management efficiency. Most companies strive for a higher ITR value as it generally indicates healthy cash flow and lower carrying costs. A very high ITR value, however, indicates an increasing stockout risk as purchases can’t keep up with sales.
Inventory days of supply (IDS)
Next up, the Inventory days of supply (IDS) KPI measures the number of days that a company’s stock would last if it stopped being replenished. It’s an important metric that provides the timeframe a company has available to replenish stock in case of a sudden supply chain disruption or temporary financial difficulties.
Calculating IDS is also derived from the yearly COGS and average inventory values. However, the COGS value needs to be divided by 365 to return the cost of goods sold per day. A simple way to calculate IDS is:
Inventory days of supply = Average inventory / COGS per day
For example, imagine a furniture manufacturer has an average inventory value of $120,000 and the annual COGS is $1,480,000. This makes the daily COGS value roughly $4,054.80. The IDS is therefore 120,000 divided by 4,054.80, which equals roughly 29,6 days.
IDS is practically identical to the days sales in inventory KPI. The difference lies in whether it’s used to disseminate financial performance or provide insights into supply chain performance.
Bear in mind that when using COGS to calculate the Inventory days of supply, the KPI does not take into account stock that was consumed but not sold, such as defects or botched manufacturing jobs. This means that to mitigate stockout risk, defect rate should also be considered in evaluating the number of days that stock would last.
Lead time KPIs
Cash-to-cash cycle time
The cash-to-cash cycle time (C2C), also known as the cash conversion cycle, is a comprehensive financial KPI that measures the time it takes for a company to convert its inventory expenditures into cash flow from sales. It encompasses the entire cycle from the initial outlay for raw materials to the collection of accounts receivable. Calculating C2C involves three main components: Days sales outstanding (DSO), Days inventory outstanding (DIO), and Days payables outstanding (DPO).
- Days sales outstanding (DSO) measures the average number of days it takes to collect payment after a sale. A lower DSO indicates faster collection.
- Days inventory outstanding (DIO) indicates the average number of days that finished goods inventory is held before it is sold.
- Days payables outstanding (DPO) reflects the average number of days a company takes to pay its suppliers.
Cash-to-cash cycle time = DSO+DIO−DPO
Supply chain and Customer order cycle time
Two more cycle times are highly relevant for gauging supply chain efficiency. These are the supply chain cycle time and the customer order cycle time.
Supply chain cycle time tracks the total time it takes to complete an entire supply chain cycle, from the moment a purchase for raw materials is placed to when the finished goods are delivered to the customer.
Supply chain cycle time = Supplier order time + Manufacturing time + Delivery time
Customer order cycle time measures the time from a customer placing an order to receiving the product. This KPI is crucial for assessing the efficiency of order processing and fulfillment operations. It’s sometimes also called the Manufacturing lead time.
Customer order cycle time = Order placement date − Order delivery date
Quality-centric and financial supply chain KPIs
Supplier quality performance (SQP)
Supplier quality performance is a multi-level KPI that comprehensively evaluates the performance and reliability of providers based on the quality of their supplied materials. It helps ensure that suppliers meet the required standards and specifications and adhere to regulations, critical for maintaining overall product quality and customer satisfaction.
SQP can be based on several metrics, such as:
- Defect rate – the percentage of defective items out of all received materials.
- On-time delivery rate – the percentage of orders delivered on or before the agreed-upon date.
- Compliance rate – the percentage of orders that meet all quality and specification requirements.
Including this KPI in your supply chain dashboard allows for early detection of supply problems and can be a powerful tool for managing supplier performance.
Freight bill accuracy
The Freight bill accuracy KPI measures the correctness and accuracy of freight invoices. It helps manufacturers ensure that they are billed correctly for their shipping activities, helping to avoid overpayments and carrier disputes. The KPI tracks any kinds of errors in the shipping orders like whether the right items are listed, in the right quantities, and with agreed-upon prices.
Freight bill accuracy = (Number of correct freight bills / Total freight bills) × 100
Freight cost per unit
Freight cost per unit, also known as Freight expenses per unit shipped (FEPS) is a KPI that measures the average cost of shipping a single unit of product. In other words, it sums the total costs incurred from shipping for a time period, and divides it by the total number of units shipped for the time period. The KPI helps companies understand and manage their shipping expenses and can be useful in identifying cost-reduction opportunities.
Freight cost per unit = Total freight cost / Total units shipped
Gross margin return on investment (GMROI)
Finally, the gross margin return on investment (GMROI) KPI measures the profitability of inventory by comparing the gross margin to the average inventory cost. It measures the amount of gross profit a company earns for every dollar it invests into inventory.
Gross margin return on investment = Gross margin / average cost of inventory
GMROI is particularly valuable in supply chain management as it helps businesses determine the effectiveness of their inventory investments. A high GMROI indicates that a company is generating significant profit from its inventory. A low value may signal overstocking, slow-moving inventory, or issues with selling prices. By monitoring it, companies can make informed decisions about inventory levels, purchasing strategies, and pricing policies to maximize profitability.
Tracking GMROI also provides insights into the supply chain. For instance, a declining GMROI might indicate the need to renegotiate supplier terms, optimize order quantities, or improve demand forecasting to reduce excess inventory. Additionally, it can help identify high-margin products that should be prioritized in marketing and sales efforts, as well as low-margin items that may need cost-reduction strategies or discontinuation.
Key takeaways
- Supply chain KPIs are essential metrics that help measure and evaluate the efficiency and effectiveness of supply chain operations. They provide actionable insights into various aspects of the supply chain, from procurement to delivery, enabling businesses to optimize their performance.
- Tracking KPIs is crucial for maintaining efficiency within the supply chain, identifying bottlenecks, and making informed decisions. Regular monitoring ensures that the supply chain operations align with business goals and can quickly adapt to changes in the market or internal processes.
- Supply chain KPIs include inventory, financial, and quality-related metrics, as well as delivery performance and lead time metrics. These diverse categories ensure a comprehensive overview of supply chain health, covering critical areas from stock levels to supplier reliability.
- Top supply chain KPIs to track include On-Time, In-Full (OTIF), Perfect order rate, Fill rate, Cash-to-cash cycle time, Inventory turnover rate, Gross margin return on investment (GMROI), and others. Together they provide a balanced view of supply chain performance, focusing on timely deliveries, order accuracy, inventory management, and profitability.
Frequently asked questions
Supply chain metrics provide measurable data that helps businesses understand the efficiency and effectiveness of their supply chain operations. By tracking these KPIs, companies can identify areas of improvement, optimize processes, reduce costs, and enhance customer satisfaction. They enable data-driven decision-making and help ensure that supply chain strategies align with overall business objectives.
Supply chain performance drivers include factors such as supplier reliability, inventory management, transportation efficiency, and demand forecasting accuracy. Effective communication and collaboration across the supply chain, along with the integration of technology and data analytics, also play significant roles in driving performance. These drivers ensure that the supply chain operates smoothly to meet customer demand and adapt to market changes.
Supply chain KPIs are crucial for inventory management because they provide insights into how effectively a company is managing its stock levels and turnover. KPIs such as Inventory turnover rate and Inventory days of supply help businesses understand their inventory usage, optimize stock levels, and reduce carrying costs. By monitoring these KPIs, companies can avoid stockouts and overstock situations, ensuring a balanced and efficient inventory management process.
You might also like: 11 Most Important Inventory Management KPIs in 2024