Test Equipment Producer Gains a New Level of Control with Manufacturing Software
With over two decades of experience in designing and manufacturing control and test systems, TBG Solutions is a trusted provider of industrial engineering solutions. A recent implementation of cloud-based MRP software has comprehensively updated the company’s internal processes.
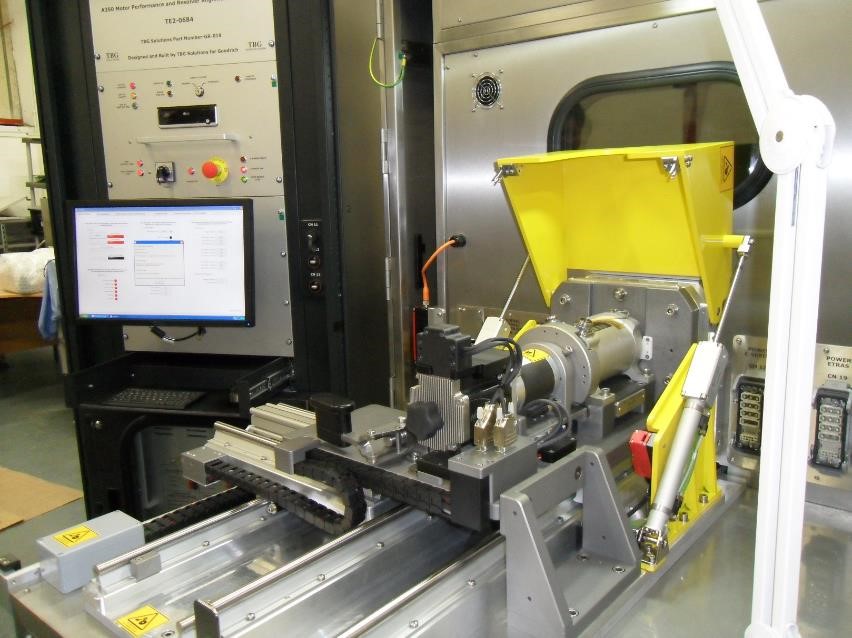
You can also listen to this article
Professionals of the trade
TBG Solutions is an engineer-to-order test, measurement, and control systems producer that has traded in one form or another for over 20 years. The UK-based company employs 30 people and has a comprehensive manufacturing operation set up in Chesterfield for the past five years.
TBG specializes in designing, prototyping, and producing bespoke test, measurement, and control equipment tailored to exact customer requirements. It caters to diverse industries including aerospace, military, energy, automotive, and others. Its customer base includes companies such as General Electric, Leonardo, and Thales, as well as universities and government agencies.
The company has a fine-tuned work process consisting of three major phases – Understand, Engineer, and Deliver. TBG Solutions designs its products from the ground up to exact customer specifications. It then prototypes and continuously improves the adopted solution before manufacturing both the project’s software and hardware in parallel.
Internal processes were in need of a refresh
When production manager Jonathan Pymm joined the company around two years ago, he noticed that while there was an effective work process in place, it was not utilizing any manufacturing or inventory management software and was largely stuck on spreadsheets. “I saw in the first few weeks that there were numerous problems that would be solved by a stock management and work orders system,” he says.
Previously, the designers would release their BOMs (bills of materials) to the office manager who handled purchasing. The company was using Xero for ordering materials but without a stock management system, there was no visibility over what was coming in. “People would take the delivery note and confirm it, without any idea of the bigger context of what it was part of, “ Jonathan comments.
This kind of “It must be around here somewhere” mentality was a high cost to the company. Lead times were stretching and parts often needed to be reordered. Having worked with ERP systems before, finding and implementing suitable manufacturing software quickly became one of Jonathan’s first tasks on the job.
Cloud-based manufacturing ERP system proved the right approach
Among TBG’s top requirements for manufacturing software were stock management, shop floor visibility, inspection functionality, and seamless integration with the company’s preferred accounting software, Xero.
Having previously used the big-ticket ERP system, SAP, Jonathan had limited knowledge of affordable cloud-based options. He looked at many different packages and talked with a number of providers. One of the directors of the company finally suggested that TBG Solutions should also look at MRPeasy, an affordable and versatile MRP/ERP system designed for small and medium manufacturers.
While it was the inspection functionality that convinced Jonathan to opt for MRPeasy over its rivals, he was also very impressed with the software’s up to 30-day trial period, extensive YouTube how-to videos, and demos that the company offers as part of its onboarding phase. Jonathan comments: “It’s important to speak with software providers and evaluate the effort they are putting in towards client acquisition. With MRPeasy, you’re actually getting demos. Not a presentation but the actual software working via screenshare, it’s very good.”
Implementation solidified the software’s benefits
It took around 8-months for the company to implement MRPeasy with its intricate manufacturing process. “We started implementing around March of last year and at first, the previous system kept on going. There was a time on the shop floor where we had projects both with the old and new systems in process.“ Jonathan adds: “Finally, we drew a line and said that every new system that gets released is going through MRPeasy.” The old system was switched off in November.
Very soon after migrating to MRPeasy, many functionalities of the new software aside from the above-mentioned key requirements, proved to simplify parts of TBG’s inner process. For example, the Custom Fields functionality got a lot of traction as the company prefers to use in-house terms for many components instead of manufacturer-provided part numbers.
MRPeasy’s excellent BOM management capabilities also proved an instrumental update. As TBG Solutions develops very bespoke equipment, product design is often not locked in, and part of the design routinely gets finalized only in the build process. When that happens, engineers are often given certain latitude in terms of deciding how to design some aspects of the product. Jonathan then highlights the necessary changes, fills in the required info, gets new parts set up, and uploads the BOM structure. Changes made during the build process are then fed back to designers who will effectively produce the master BOM.
With MRPeasy, this process is much smoother than previously. Jonathan lauds the software’s BOM capabilities: “The upload of parts is very quick. Quick to get the parts into MRPeasy and quick to do the BOM structures as well. That really stands out to me, having used SAP before. We also just started using the Matrix BOM functionality. I remember how complicated this was in SAP.”
A wholly refreshed manufacturing management process
Today, TBG Solutions is using MRPeasy primarily for shop-floor resource management and bridging the previous gaps in stock management. The firm is also fully utilizing the built-in Xero integration and is looking towards implementing other functionality in the software, like purchasing, WIP (work in process) inventory management, and production costing automation.
For other companies looking to implement MRP software, Jonathan recommends getting a clear idea of the key requirements of your particular use case, prioritizing specific functionalities, and taking it one step at a time. “Don’t think you need to bring in all modules all at once. Look at what the key requirements and challenges are for your business and make sure the providers you’re looking at tick those boxes,” he says.
He also suggests planning ahead to what might be needed in the coming years: “There’s an element of hope that the package that you end up choosing ticks all the boxes and keeps being developed down the line.” All in all, TBG Solutions has gained a lot of clarity in its internal process thanks to a flexible and scalable software partner in MRPeasy. In a short span of time, the firm has gone from constantly missing and reordering parts to near-complete stock control and shop-floor visibility.