Lens Metrology Device Manufacturer Stays Flexible with Day-One MRP Implementation
High-precision measuring device manufacturer Optimec Systems opted for a day-one MRP system implementation. For four years, MRPeasy has continued to handle all production and inventory management complexities.
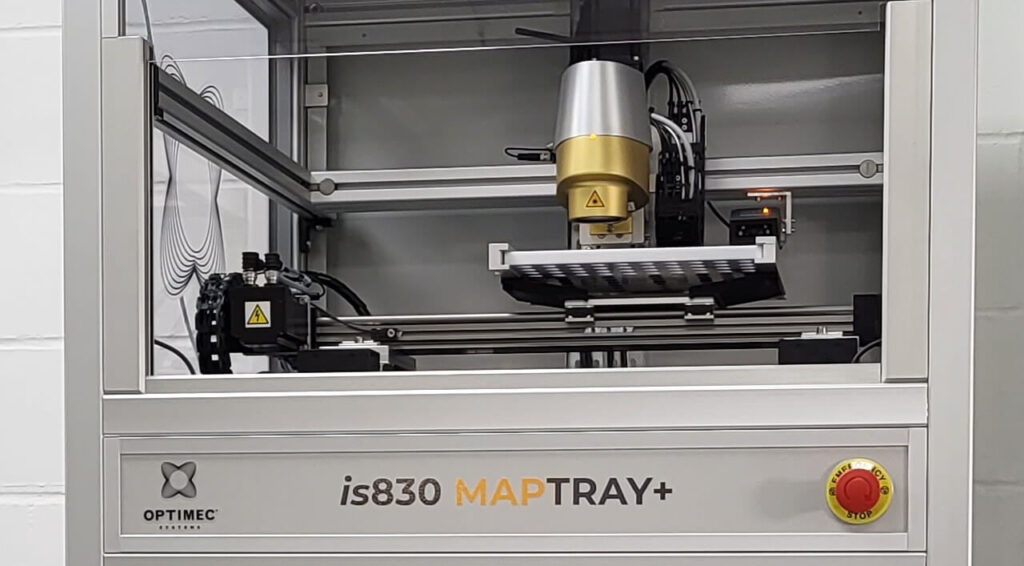
High-tech optical measuring equipment from the UK
Optimec Systems Limited (OSL) is an engineering company that produces high-precision measuring equipment for lens manufacturers. It was founded in 2020 by experienced engineers Matthew Cleere and Ben Coldrick. They had been working together at a larger engineering firm when an opportunity to acquire a part of the technology prompted the duo to go independent.
OSL develops and manufactures high-precision optical lens imaging systems. These devices, named is830, are used for taking ultra-fine measurements of contact and intraocular lenses, corneal implants, lens molds, and other similar products. They are crucial equipment for modern lens manufacturers, capable of measuring lens geometry to sub-micron precision. The equipment is used in R&D, quality control, and at multiple points during the lens manufacturing process.
OSL develops both the hardware and software for its products in-house. Today, the company has 6 employees, with a few trusted subcontractors handling certain aspects of manufacture and assembly. The is830 product line is sold domestically and to companies in European, US, and Asian markets, with a customer base that includes many key multinational lens manufacturers. OSL returns around a million dollars in annual revenue and is steadily scaling up the production effort.
Cloud-based manufacturing software was a prerequisite from the start
Director of Operations Matthew Cleere knew that production management software was a must for a starting manufacturing business with an intricate product. “We were setting the company up as a new entity, so it was a perfect opportunity to clear the decks and get something in place from the start,” he says.
With extensive experience in manufacturing and engineering, Matthew had a good idea of OSL’s requirements for production software. The first among these was a cloud-based interface since the company was founded during the height of the COVID lockdown, and the team needed to work remotely. This prompted the idea of setting up OSL’s whole IT infrastructure as web-based.
Primary among functionality requirements were efficient stock control, subcontracting, and bill of materials (BOM) management. The previous company handled inventory using spreadsheets and paper-based systems. This needed to change to boost stock traceability. “Since we outsource many of the components we use, and initially much of the assembly work was also being outsourced, we needed robust stock control to manage subcontractor work and the relatively large number of components, as we have quite complex products,” says Matthew.
Finally, a seamless Xero integration was high on the list of requirements, as OSL opted for the accounting platform from the start. There was hope that Xero’s built-in stock control system would suffice initially. However, it quickly became apparent that it lacked the flexibility to handle OSL’s complex stock requirements and Bill of Materials structures.
Implementing was simple enough to handle from home
Matthew browsed the web and looked for suitable candidates for the company’s new production software. Having had an eye on MRP systems in particular, he happened upon MRPeasy. It seemed to tick all the boxes and also promised ease of use, scalability, and a low price point. “I trialed a few other contenders, but MRPeasy’s features generally seemed easier to use, and importing data was very simple.”
The decision was made, and Matthew set out to implement the new system. The lockdown presented a good opportunity for this as production volumes were low, and there was ample time to set up. He largely managed to implement the system remotely over a month and also developed a training plan for employees.
OSL committed to MRPeasy in July 2020. At first, a few jobs were completed side-by-side with how production was managed in the previous firm. However, by September, the team had already completely switched to the new manufacturing software. “We’ve done quite well with getting people on board with MRPeasy. They’ve certainly seen the advantage of it,” Matthew comments.
An intuitive system for users with many hats
Regarding key requirements, MRPeasy’s built-in subcontracting functionality quickly proved instrumental in providing OSL with the required level of stock management flexibility. The system also helped optimize stock levels and simplify forecasting.
For small companies, especially those with complex and high-value components, optimizing stock levels is crucial for maintaining a balance between cost and lead times. Matthew Cleere explained: “We manufacture on an order-by-order basis, and some high-cost components have long lead times. So, forecasting accuracy—planning production and coming up with an accurate confirmation date, is very important to us. Having that visibility in planning and the ability to stick to quoted order dates is key.”
MRPeasy’s capability to manage complex BOMs has also made customization much easier. Matthew notes: “While we don’t have a big product line, we do produce a lot of bespoke automation and optional extras to complement our products. MRPeasy’s ability to manage complex parameterized BOMs saves us a huge amount of time.”
Another surprise benefit has been the intuitive and flexible interface. Being a small team, OSL’s employees must be able to contribute to many different tasks. Matthew lauds MRPeasy’s interface, which empowers flexibility: “MRPeasy has proved intuitive enough that any of our members can complete a wide range of actions without needing to rely on, for example, a procurement manager to book deliveries, etc.” If anyone does get stuck, MRPeasy’s extensive user manual, a special AI assistant trained on the software, or the responsive support ticket system are there to handle any questions that arise.
Understanding software requirements is key for SMEs
Recommending the course of action for other SMEs looking to implement MRP software, Matthew urges to first take time to understand the company’s needs. “The system is very powerful in the sense that it allows for many different ways to get something done and solve the same problem. Thinking carefully about your procedures is crucial,” he says.
On a company-wide level, Matthew also suggests implementing a thorough training plan for employees so they understand what they are doing and what management needs them to be doing. It’s preferable to make employees understand a system and take appropriate action than to teach them to follow crude protocols without understanding what they’re meant to achieve.
Four years on, MRPeasy continues to streamline OSL’s workflows and enhance its production management. Today, MRPeasy effectively handles all of the production and inventory side of the business.
You might also like: Marine Drone Manufacturer Navigates Business Complexities with MRP Software