Interior Trim Company Accommodates 75% Growth with MRP Software
When ABI Mouldings changed owners in 2020, one of the new management’s first priorities was to modernize the inventory management and production planning side of the business. The implemented MRP software has since proved to accommodate all of the company’s requirements and offers effortless scalability on top.
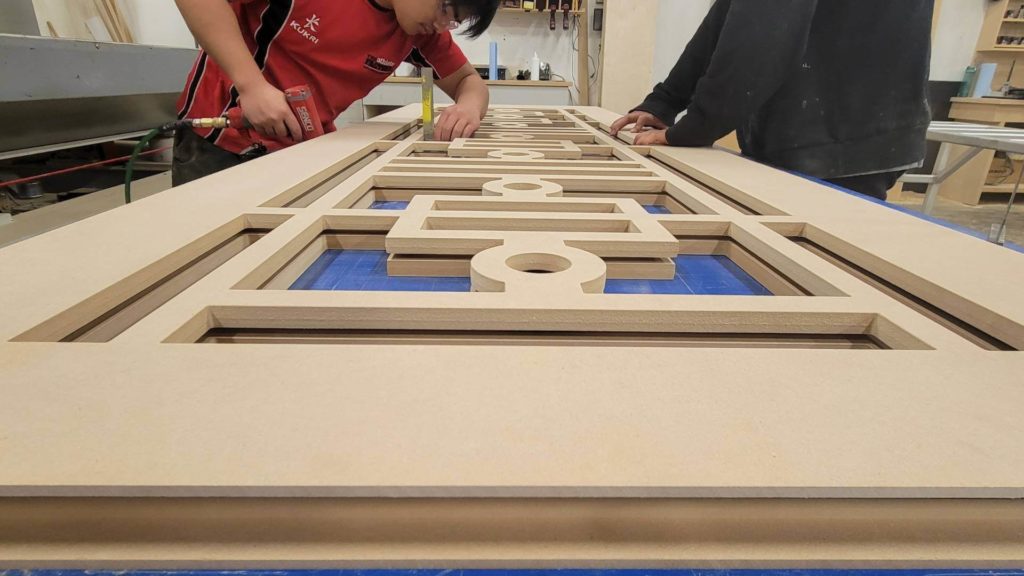
You can also listen to this article:
Finishing trims for any interior need
ABI Mouldings is a building materials company producing high-quality molded finishing details for interior use. Based in Alberta, Canada, the company employs 28 workers and utilizes a network of trusted resellers to distribute its goods throughout most of Western Canada.
Over the course of its nearly 30 years in business, ABI Mouldings has developed a wide range of interior moldings ranging from baseboards, rails, and casings, to door and window frames, profiles, cornices, etc. The company uses medium-density fiberboard, or MDF, in most of its product line. The current owners acquired the business in early 2020 and have since also purchased a door manufacturing company, successfully expanding the product line to include MDF doors.
In the 3 years under new management, the company has managed to greatly increase its production output, going from around 4 million feet of products shipped per year, to close to 7 million ft. Operations manager Ve Chao attributes a lot of this recent success to the company adopting capable manufacturing software that enabled accommodating a rapid growth in demand which occurred during the COVID-pandemic.
Need for a cloud-based production planning tool among top priorities
When the current owners took over ABI Mouldings, the production management side of the business was running on a very limited production planning tool. The software was basic in functionality, lacking routing control, bills of materials structure, and a dedicated production module as such. Additionally, it was accessible only on-site, which complicated and limited usage scenarios.
Ve Chao recalls: “It was essentially a glorified spreadsheet, only good for printing off a work order to paste on the shop floor. You had to manually fill in most of the necessary information for production. There were no materials or jobs tracked, etc., everything was manual. If you wanted to know the inventory of something, you’d have to go and physically count it. Inventory management really was a nightmare.”
It was no surprise then, that a key priority for the new management quickly became finding a suitable manufacturing planning software. One that would simplify managing the supply chain, inventory, and crucially – production planning aspects of the large and, as it turned out, soon-to-be expanding, production volume that ABI Mouldings was operating at.
Easy-to-implement manufacturing software proved a good fit from day one
Ve and his team looked at three potential candidates for the new software in early 2020. After acquainting themselves with all three, MRPeasy was promptly picked as the software of choice. It simply promised a great solution in terms of production planning functionality, a key requirement for the company, next to a seamless QuickBooks integration and a web-based interface.
Implementation began in March. In just three months, initial functionality was set up to a sufficient level to allow bringing the manufacturing plant over to the new system. In terms of implementation simplicity, MRPeasy proved to live up to its name, both in terms of getting set up fast and training the employees to use the new system. Ve Chao comments: “Building the whole system to meet our requirements was so easy that we hardly looked at the manual during implementation.”
The implementation team approached the task by focusing on one module of the software at a time and building it up, an approach that the software effortlessly accommodated. As Ve recalls: “There are many schedules that link to each other in MRPeasy but you don’t need to link them right off the bat, in order to start using the system. For us it was production planning that we started with and from there we built the BOMs and routings, etc., eventually getting to where the app is basically operating our entire business.”
New software arrived just in time to accommodate a demand surge
ABI Mouldings managed to adopt the new software just in time to meet the challenges of the COVID pandemic. Production volumes grew massively during the pandemic, much to the surprise of many at the time. On the other hand, the company was not untouched by the ensuing supply chain disruptions as material lead times stretched, often by months.
“It was really quite a beautiful alignment,” explains Ve, “Prior to COVID, we were running around a 2-week lead time for materials, but all of a sudden we weren’t getting the material to match the growth opportunity. At one point we were up to half a year behind on new orders coming in, running a 6-month lead time because of material shortages. Trying to manage that without MRPeasy would probably have broken us.”
Overall, MRPeasy helped ABI Mouldings to accommodate a roughly 75% increase in production volume over the span of around two years. The app proved to be a crucial aid in both supply chain, order, and inventory management, and for planning ahead production.
A scalable solution that grows with your requirements
Among the many benefits that MRPeasy has brought to ABI Mouldings, operations manager Ve Chao especially brings out the customer satisfaction impact: “It gives us the ability to project a much more accurate lead time. If a customer puts in a PO (purchase order), it can easily consist of 6-7 lines, each with different materials. The very moment an MO (manufacturing order) is created to fulfill the demand, the PO is booked to the MO and the lead time for each line is very accurate in terms of what we actually need.”
For anyone looking for a production planning and inventory management solution, Ve recommends first thoroughly figuring out your requirements and taking implementation one step at a time. It’s important to consider scalability, too as the software should ideally be able to accommodate more complex use cases down the line.
Ve sums it up: “It’s almost like a pencil and a notepad – how creative you get with it is up to you. There’s a lot of custom usage that we’ve been able to make work for us and we’ve yet to hit a stumbling block with MRPeasy in terms of the software’s capability.” Ve is so confident in having made the right choice in manufacturing software, he claims: “If you’re looking for a production planning tool for your manufacturing operation, test MRPeasy first before you start looking around.”
You may also like: Chemical Contract Manufacturer Cuts Administrative Overhead with MRP Software