Stock Control – A Simple Guide for SMEs
Keeping a close eye on inventory levels is crucial for increasing the efficiency of any manufacturing or distribution operation. This goes doubly so for small and medium businesses where margins can be tight and profits rely heavily on keeping costs in check.
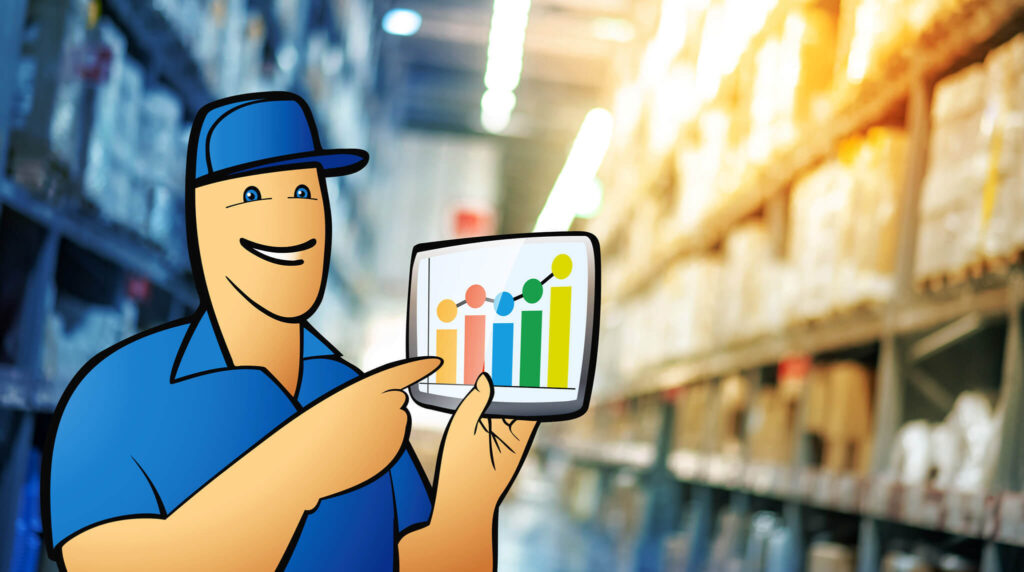
You can also listen to this article:
What is stock control?
Stock control or inventory control is the process of keeping stock at optimal levels in a manufacturing or distribution operation and throughout a product’s supply chain. It’s making sure that there is always a sufficient supply of materials or goods available for the next node in the supply chain. For manufacturers, stock control mostly revolves around minimizing standing inventory costs and avoiding excess stock as well as stockouts. Thus, a good working definition for stock control would be the process of maximizing profit through minimizing stock levels.
Stock control is a core part of inventory management. However, it bears emphasizing that inventory management is a more general term that encompasses a broader range of priorities than stock control alone.
The primary means of achieving a high level of control are implementing good traceability and ways to determine optimal stock levels. These form the root of an effective stock control system. Additionally, stock control touches on a range of other business processes from supply chain management and production and quality control, to procurements, vendor management, and even customer relationship aspects.
What is a stock control system?
A stock control system is a system designed to automate and simplify core stock control processes. Stock control management, meanwhile, is the strategic process of implementing and running such a system. The vast majority of stock control systems are digital and often come as dedicated inventory management software or are integrated into manufacturing ERPs or MRP systems.
Stock control systems incorporate one or many stock control methods, the better known of which we delve into below. A central distinction between the types of inventory control systems, however, lies in their being either perpetual or periodic.
Periodic and perpetual inventory control
In periodic inventory systems, stock levels are checked over a set period like once every quarter or financial year. The chief tracking mechanism is stocktaking which is used to compare actual inventory levels with those from receipts and dispatch notes. Stocktaking is conducted periodically with continuous tracking often not present. The majority of periodic inventory systems are manual and rely on spreadsheets. It’s a tried and tested method for achieving stock control for very small or very simple operations. However, compared to modern digital systems, it is largely outdated and very limited in scalability.
Perpetual inventory systems, on the other hand, keep tabs on stock levels and movements continuously, often in near real-time. As goods come and go through storage and the shop floor, data is fed into the inventory system via internet kiosks, scanners, RFID systems, etc. This enables the stock control software to track stock movements and help reported stock levels to conform to actual numbers around the clock. Practically all modern inventory management systems are built on the perpetual inventory model.
Read more about perpetual and periodic inventory systems.
The core functions of a stock control system
As mentioned, the core elements for achieving effective stock control are twofold. On the one hand, it is essential to understand what would perfect stock levels be in any given situation. On the other, inventory visibility – reliable data on stock movements and actual inventory levels, needs to be achieved to maintain a sustainable supply flow and enable analytics.
Determining the right stock levels
Determining the right stock levels and keeping them that way is a constant balancing act between avoiding overstocking and stockouts. Excess inventory ties up precious storage space and capital. Stockouts, meanwhile, can lead to lost sales, fewer business opportunities, and a dissatisfied customer base. If left unchecked, both of these can quickly spiral a company into serious financial problems. This goes doubly so for smaller businesses with limited resources and budding customer relationships.
A crucial process for predetermining viable stock levels is demand forecasting. This involves predicting future customer demand using historical sales data, market trends, and other relevant factors. As demand forecasting relies heavily on good-quality data, the built-in analytics and reporting capabilities of modern production planning software play an increasingly crucial role in aiding the forecasting process.
Another crucial business process that involves regularly reviewing and adjusting inventory levels based on demand forecasts and supply chain variables is inventory optimization. This process is mostly about consolidating inventory costs and stock management complexity with material availability.
Inventory tracking
The other fundamental aspect of ensuring effective stock control is stock and lot tracking. Traceability is a fundamental aspect of inventory management, providing data on stock levels and movements as a company operates. This enables businesses to make informed decisions and respond swiftly to changes in demand or supply. In modern manufacturing, tracking is not only crucial for highly regulated markets like the food or pharmaceutical sectors. It’s becoming increasingly relevant in all sorts of markets where customer preferences, demand patterns, and supply logistics can shift rapidly.
Inventory tracking goes beyond simple stock-keeping unit (SKU) traceability. A much more practical level is tracking stock lots, batches, and individual items by their serial numbers. Furthermore, tracking and logging purchases, manufacturing and customer orders, and work in process (WIP) inventory enables long-term statistics, gauging a company’s financial health, and deep insights into customer relationships and opportunities.
The importance of tracking software cannot be overstated in achieving traceability. These systems enable seamless updating of inventory levels as goods are received, sold, or moved, providing a clear and current view of the stock. What’s more, tracking software also enables seamless data analytics on stock levels and movements. This helps to achieve a level of precision and efficiency impossible to reach with manual methods. Advanced solutions also often include features like automated reorder alerts and integration with other business systems.
Common stock control and planning methods
Next, let’s look at some common stock control methods. Different methods are suitable for different circumstances, and many companies opt to utilize a mix of methods. Ultimately, stock control comes down to developing a system that most benefits a company’s use case, outputs consistent data, and simplifies production, inventory, and supply chain management.
Just in Time (JIT)
The Just in Time (JIT) inventory method is a strategy where materials and products are produced or acquired only as needed for immediate use. This approach minimizes inventory costs by reducing the need to store a large amount of stock. JIT requires precise coordination and strong relationships with suppliers, as materials must arrive exactly when needed, not earlier or later. This method is particularly beneficial for make-to-order companies looking to reduce waste, enhance efficiency, and improve cash flow.
However, JIT can be risky in environments with unpredictable demand or supply chain disruptions. Successful implementation of the method hinges on reliable demand forecasting and excellent communication with suppliers, ensuring that production runs smoothly without the safety net of large inventories.
In JIT, stock control is achieved by aligning production schedules closely with customer demands, thereby reducing the need for large inventories. JIT’s emphasis on minimal inventory levels inherently supports traceability, as there are fewer items to track at any given time, making it easier to monitor and manage the flow of goods through the supply chain.
Read more about Just In Time manufacturing.
ABC Analysis
ABC Analysis is a tried and tested method of categorizing inventory and organizing the warehouse into three categories (A, B, and C) based on their importance and value to the business. ‘A’ items are the most valuable, usually comprising a small percentage of inventory but a large portion of inventory value. ‘B’ items are of moderate value, and ‘C’ items are the least valuable. This prioritization allows businesses to focus their resources and efforts on managing and controlling their most critical or best-selling items.
By implementing ABC Analysis, companies can optimize their stock control strategies, ensuring that they devote more time and resources to managing high-value items while still maintaining sufficient stock levels for less critical products.
Keep learning about ABC analysis
Vendor Managed Inventory (VMI)
Vendor Managed Inventory (VMI) is a collaborative strategy where the supplier takes on responsibility for maintaining an agreed inventory level at the buyer’s location. The supplier monitors the buyer’s inventory levels and makes periodic replenishments based on the agreed terms. This approach can lead to reduced inventory costs and improved supply chain efficiency, as suppliers can better predict and respond to demand.
VMI fosters a closer partnership between supplier and buyer, leading to more accurate inventory levels, reduced stockouts, and often, better purchase terms. However, success with VMI depends on open communication, trust, and a clear understanding of both parties’ needs and capabilities.
VMI can contribute to better stock control because one business manages both inventories. Suppliers determine the right stock levels based on agreed parameters and are often better equipped to forecast and respond to changes in demand. The method thus also enhances traceability as suppliers are directly involved in monitoring and replenishing the buyer’s stock, often using sophisticated systems to track stock levels and dynamics accurately.
Learn more about Vendor Managed Inventory
Inventory costing methods
Inventory costing methods, such as FIFO (First-In, First-Out), LIFO (Last-In, First-Out), Weighted Average, and others, are crucial for understanding the financial value of inventory. FIFO assumes that the oldest inventory items are sold first. A variant of this system, popular among food and pharmaceutical manufacturers, is the FEFO (First Expired, First-Out) method which reduces spoilage by sorting stock by its perishability. Next up, LIFO assumes that the newest items are sold first, useful for tax benefits in environments with rising prices. Meanwhile, the Weighted Average method smooths out price fluctuations by averaging the cost of goods.
While these methods revolve around inventory costing, not inventory levels, they also play a significant role in stock control by providing insights into the financial implications of inventory decisions. These methods help in determining the right stock levels by influencing purchasing decisions and managing inventory turnover. They also support traceability by offering a systematic approach to tracking how inventory is bought and sold, crucial for understanding inventory flow and its financial impacts.
Continue reading about inventory costing methods
Material requirements planning
Material Requirements Planning (MRP) is increasingly vital for effective inventory control among manufacturers or distributors that add any type of value to their stock before selling it off. MRP integrates material requirements and production data with stockroom information, offering powerful insights into material needs.
By accurately forecasting and scheduling the purchase of materials based on production schedules, MRP systems help avoid critical components going out of stock. These software systems often come with advanced tracking features built in, enabling businesses to closely monitor both the stock levels and movements of raw materials, finished goods, work in process, and even pipeline inventories. The comprehensive nature of MRP systems makes them an essential tool for effective stock control, especially in complex manufacturing environments where precision in material planning is key to operational efficiency.
MRP mostly achieves stock control by integrating production planning, scheduling, and inventory control. It determines the right stock levels by precisely forecasting material requirements based on production schedules, thus avoiding overstocking or stock shortages. MRP systems enhance traceability through real-time tracking of materials and components across various stages of production, ensuring a clear view of inventory status at all times.
Read our comprehensive guide on material requirements planning
Economic Order Quantity (EOQ)
Finally, the Economic Order Quantity (EOQ) model is a fundamental method in inventory management, used for optimizing order quantities. It’s a formula that calculates the ideal order quantity by minimizing the total costs associated with purchasing, holding, and ordering inventory. EOQ considers the demand rate, ordering costs, and holding costs, thus providing businesses with a quantifiable approach to making cost-effective inventory decisions. EOQ is particularly valuable in environments where demand is relatively stable and order and holding costs are predictable.
The EOQ model aids stock control by providing insights into the optimal order quantity that minimizes costs while meeting demand. It’s a particularly powerful method when used in tandem with safety stock and reorder points. Its only real weakness is a heavy reliance on highly accurate demand data.
Read more about Economic Order Quantity
Best practices for achieving effective stock control
Effective stock control is crucial for small and medium enterprises to maintain profitability and efficiency. Next, we look at some of the most important things to note when planning out stock control.
- Cycle counting goes a long way. Whether using inventory management software or relying on spreadsheets, regular inventory counts are essential for maintaining accurate stock records. Cycle counting, a method where a subset of inventory is counted at regular intervals, can be especially beneficial. This approach is less disruptive than a full inventory count yet still allows for ongoing accuracy checks. By consistently monitoring stock levels, discrepancies can be identified and corrected quickly, ensuring that inventory records are always up-to-date.
- Track everything. Tracking should encompass all kinds of different stock, including raw materials, Work in process (WIP), finished goods, and even consumables. It’s important not just to track stock-keeping units (SKUs) but also batches and stock lots for better traceability. More comprehensive tracking enables small businesses to monitor the whole lifecycle of products, manage expiry dates effectively, maintain a clear picture of inventory health, and provide crucial insight into a company’s performance over time.
- Inventory management KPIs. Key performance indicators (KPIs) are vital for assessing the effectiveness of stock control strategies. Essential inventory management KPIs for SMEs include inventory turnover rate, which measures how often inventory is sold and replaced; stock-to-sales ratio, offering insights into how well stock levels align with sales; carrying cost of inventory, highlighting the costs associated with storing unsold inventory; and demand forecast accuracy, essential for optimizing stock levels. Regularly reviewing these and other KPIs helps you to stay informed and simplify decision-making.
- Warehouse management. Far more than simplifying the life of the stock clerk, warehouse management is a cornerstone of effective stock control. This includes optimizing and organizing the warehouse layout for easy access and efficient movement of goods, implementing robust labeling and tracking systems, ensuring proper training for warehouse staff on how to collect, move, and handle goods, etc. Good warehouse management practices help minimize errors, reduce handling time, and reduce warehousing costs, all of which contribute to better stock control.
- Develop a holistic approach. As mentioned, effective stock control comes down to creating an integrated system that covers all the bases and takes into account a company’s specific requirements. Consider adopting the right mix of methods, conducting regular ABC analyses and performance reviews, and staying mindful of supply chain dynamics and vendor relationships that the flow of goods relies on.
- Leverage software solutions: Utilize inventory management software to automate, integrate, and streamline a lot of stock control processes. These technologies provide near real-time inventory updates, automate ordering processes, generate insightful reports, incorporate traceability, and help bind the whole production effort into a unified business ecosystem.
- Contingency planning: Optimized inventory is an absolute prerequisite for manufacturing. Prepare for unforeseen events like supply chain disruptions or sudden demand spikes by having a well-thought-out contingency plan. This can include identifying alternative suppliers, keeping emergency stock for critical items, and staying as informed as possible of relevant supply chain dynamics.
Stock control with a manufacturing ERP system
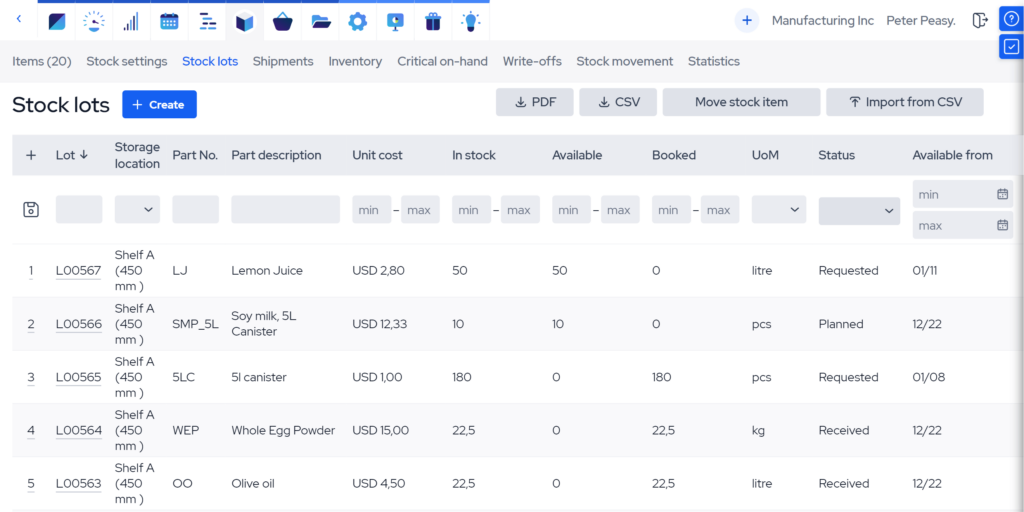
Implementing a manufacturing Enterprise Resource Planning (ERP) system can revolutionize the way small and medium enterprises (SMEs) handle stock control. These systems integrate various aspects of business operations, providing a comprehensive solution for managing inventory efficiently. Here’s a closer look at how manufacturing ERPs like MRPeasy facilitate effective stock control:
Centralized data management
A manufacturing ERP system centralizes all business data, including inventory, procurement, production, and sales. This ensures that stock levels are automatically updated as materials are received, products are manufactured, and sales are made. The real-time visibility into inventory levels and movements that the software enables helps maintain accurate stock records, essential for efficient stock control.
Improved inventory accuracy
ERP systems offer sophisticated tools for tracking all types of stock from raw materials to WIP and finished goods. Features like QR-code or barcode scanning and internet kiosks for per-employee reporting enhance inventory accuracy, significantly reducing the chances of errors that can occur with manual tracking. This is vital for avoiding overstocking or understocking situations due to human error.
Streamlined production planning
Manufacturing ERPs and MRP systems comprehensively integrate stock control and production planning. This allows businesses to align their production schedules with inventory levels, ensuring they have the necessary materials for production without overstocking. It helps in reducing carrying costs and improving cash flow management.
Enhanced demand forecasting
A single source of data, built-in analytics, and advanced reporting tools all point toward increased accuracy in demand forecasting. Historical sales data, market trends, and other relevant factors enable more accurately predicting future demand. This is crucial for determining optimal stock levels and planning for seasonal fluctuations or market changes. The built-in reports and analytics include details on stock movements and aging, the inventory turnover rate, etc.
Automated reordering and safety stock levels
Many ERP systems feature automated reordering functionalities based on predefined thresholds. For example, when inventory falls below a certain minimum stock level, the reorder point, MRPeasy automatically generates alerts based on which you can create pre-filled purchase orders with a single click, ensuring continuous availability of necessary items. This automation saves time, reduces the need for manual intervention, and helps prevent stockouts. The reorder point levels can be adjusted in a similarly convenient fashion.
Supplier and purchase order management
The stock control system in a manufacturing ERP streamlines a large part of the supplier management and purchase order process. With this, companies can manage supplier information, track purchase orders, and coordinate deliveries all within the same ERP system. This centralized approach improves communication with vendors and provides a wider grasp of the whole supply chain.
Scalability and flexibility
As businesses grow, their stock control needs evolve. Capable manufacturing ERP systems are scalable, meaning they can adapt to increased complexity in operations. They offer the flexibility to adjust stock control processes as the business expands, ensuring that the system remains effective over time.
In conclusion, a manufacturing ERP system like MRPeasy is a powerful tool for SMEs looking to optimize their stock control. By integrating various business processes, providing real-time data, and offering advanced analytical tools, ERPs enable SMEs to manage their inventory more efficiently, all while reducing operational costs and improving overall operational efficiency.
Key takeaways
- Stock control, also known as inventory control, is the process of managing stock levels and movements of a company’s products throughout its supply chain. The primary means of stock control are achieving sufficient traceability and determining what the optimal stock levels are at any given time.
- A stock control system is software that integrates all facets of stock control into a single unified system. Stock control systems come as dedicated inventory management software or as integrated into manufacturing ERP or MRP systems.
- Common stock control and planning methods include the Just In Time (JIT) method, Vendor Managed Inventory (VMI), Economic Order Quantity (EOQ), Material requirements planning (MRP), and others.
- Manufacturing ERP systems incorporate sophisticated stock control functions that enable easily determining stock levels through advanced forecasting and reporting tools, automating reorder points and stock replenishment, helping increase stock accuracy, and much more.
Frequently asked questions
Stock control is managing the stock levels and movements of a company’s inventory throughout its supply chain. Primarily, effective stock control is achieved through traceability and determining what optimal stock levels are via analytics and forecasting.
Inventory control systems are crucial for enabling companies to manage their stock levels efficiently, reducing the risk of overstocking or stockouts. These systems provide real-time insights into inventory, facilitating accurate demand forecasting, optimizing storage costs, and ensuring timely fulfillment of customer orders.
The best way to improve stock control management is by implementing a capable manufacturing ERP system. This centralizes inventory data, automates stock level tracking, and unifies various business processes, leading to more accurate demand forecasting, enhanced traceability, and efficient inventory handling.
You might also like: Vendor Management – An Essential Guide for SMEs