SAP ERP and Oracle ERP alternatives for Small Manufacturers
Choosing a suitable ERP system for your company is not a simple task. Amongst too many options in the market, selecting the right solution is a challenge that demands time and reasonable criteria.
You can also listen to this article:
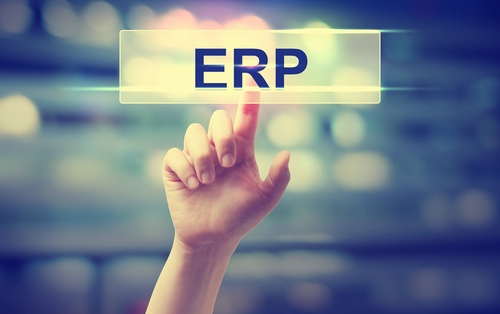
On many occasions, the most recognized systems with the highest market share, such as SAP ERP or Oracle ERP, are the chosen ones. But at the same time, there are many alternatives that can offer cost-effective solutions for small manufacturers.
Let’s see what each of these two traditional systems consists of and after explore some other alternatives.
You may also like Alternatives to MS Dynamics AX and MS Dynamics NAV for Small Businesses.
SAP ERP
SAP represents so far an undisputed trajectory in the market for several decades. It is the leader in providing Enterprise Resource Planning (ERP) software solutions. The business processes included in SAP ERP are Operations, Finance, Human Resources, and Corporate Services.
SAP ERP collects and combines information from each of the business processes to offer resource planning. It allows the global integration of the business and guarantees scalability. It also offers many languages on its products portfolio. It provides software that handles information in real-time. Thus, companies get greater efficiency at the corporate level. Their platforms are intuitive, easy to learn and secure, delimiting meticulously the roles.
The costs of its implementation can range from a few million dollars for a medium-sized company to several hundred million for large international corporations. Today SAP also offers accessible solutions for small and medium businesses. This is SAP Business One, which is specially designed for SMEs. This solution can run in both On-Premise and On-Cloud mode.
Yet, there are some disadvantages whenever SAP is selected. It is necessary to develop a large amount of custom code to adapt the system to the business model and the implementation process can take a long time. The total cost of ownership (TCO) is high; this is the cost of acquisition, implementation, maintenance, and internal and external support.
The return on investment is achieved when the amount of data, the frequency of use and the number of users is high. Otherwise, it may present implementation risks. Finally, it’s important to emphasize that there are high exit barriers when changing ERP solutions is required.
Oracle ERP
Oracle has been traditionally the leader in the database market. Over time Oracle acquired other companies that allowed them to expand in other markets, such as the ERP market. Their ERP solutions offer an intuitive user interface, easy to use and understand. They allow integrating all the data of the organization in a single environment. They also guarantee database security based on company roles. They offer solutions both on the company’s servers (on-premise mode) and executed in a network of remote servers (on-cloud mode). They also incorporate emerging technologies as competitive advantages. These technologies are machine learning, blockchain, and the Internet of things (IoT).
Hence, they also present some disadvantages such as cost, external connectivity, and layout.
Its interactivity is less attractive than platforms such as Windows. There are limitations to external database connectivity. The implementation process can take a long time. Finally, it’s remarkable that each Oracle license is expensive compared to its competitors. In turn, it can represent a significant cost in relation to the total cost of the company, especially in smaller companies.
Alternatives beyond the most known solutions
The reality is that companies have limited time and financial resources. It is also true that they need to have flexible ERP software to manage their processes. In this way, small manufacturers may not have to go to the main suppliers, such as those mentioned above. There are smaller ERP developers offering efficient, cost-effective systems and more personalized services. These solutions include flexibility and reasonable implementation time. The investment is in accordance with the dimensions of the smaller manufacturing companies.
Let’s see what the main characteristics of some of these suppliers for small manufacturers are.
MRPeasy
MRPeasy began as an MRP system solution provider. Its functionality was strongly oriented towards product manufacturing processes. It includes material planning, sales order management, inventory management, and work order management. MRPeasy has migrated today towards a complete manufacturing ERP system, offering support from e-commerce to accounting and payroll.
MRPeasy can integrate with other applications. MRPeasy can be integrated with accounting software packages QuickBooks and Xero, e-commerce platform Shopify, Magento and WooCommerce (from January 2020). The small manufacturers can now expand the field of applications to solve the management challenges of the company. They don’t need to make tremendous changes anymore. They can expand the familiarity of the applications that the small company already has. The small administrative or accounting staff will avoid lost hours of learning or implementing a system from scratch. Besides, MRPeasy works on mobile devices, both Android and iOS.
Another comparative advantage that MRPeasy offers is its competitive price. Basically, it offers four packages the Starter, the Professional, the Enterprise and the Unlimited. The licenses are paid by the number of users per period. The Starter package starts from USD 49 per month per user. After the 10th user, the price drops significantly.
The main cons of this software come from the fact that it was built for providing manufacturing solutions. Thus, it’s not the best platform for those businesses offering services as the main product, or retail companies. It is neither suitable for large companies with thousands of employees in search of enterprise-class solutions.
Fishbowl
Fishbowl is a business automation and inventory management. The platform is ideal for small to midsize companies. It integrates with QuickBooks accounting and offers inventory control, material requirements planning (MRP), shop floor control and manufacturing execution.
It is an inventory-centered system, with features for bar-coding, asset and materials management. They offer cycle counting and customized reporting. The system also automates the quoting, ordering and purchasing processes. The work order system enables users to create and share work orders for a variety of tasks.
The main advantages include its integration with QuickBooks and its simple and intuitive use. Summarizing it is a great platform for an inventory management system.
The main disadvantages are the complexity to get reports and since it is focused mainly on inventory control, it needs integrations with accounting software to eliminate the need for double data entry.
Plex
Plex offers cloud computing ERP solutions for manufacturers. The Plex Manufacturing Cloud solution provides real-time visibility from the plant floor to the top floor. Plex contributes to solving typical and common small manufacturer problems:
- struggling with data silos
- manual paper-based processes
- inaccurate inventory tracking
They all represent significant ways of time and money wasted. Plex targets are manufacturing industries with rigorous traceability, quality, and food safety requirements. They focus on automotive, aerospace, food & beverage, and life sciences or medical manufacturing.
Its software offers an intuitive control panel. The software allows to track and control inventory, quality, and production in real-time. The colored coded graphics show the status of the shop floor in real-time and even wirelessly. It gets machine data in real-time and it can be connected either to any Smartphone or tablet.
It can control up to the minute production schedules. It manages maintenance work orders, work instructions, production shift operators, all of them paperless.
Data can be transmitted directly from Machinery via PLC. The maintenance team can be alerted in real-time reporting any stoppage, reducing factory downtime. With a barcode scanner, it is possible to transfer inventory into the production facility. It also contains lean manufacturing modules. For example, kanban cards applicable for example to the automotive industry.
Yet there are some disadvantages. The software can be difficult to use and requires considerable user training. The layout is not the best in regards to visual aesthetics. Too many windows, menus, screens, and searching options make the software less user-friendly.
Conclusion
An ERP full service and adaptable to the reality of the business occupies a prominent place in the priorities of small manufacturers. There are many software systems alternatives with cost-effective solutions and flexible functions.
The small manufacturing companies that wish to put in place an ERP system should pay attention to the system integration. The information flows correctly between the different components. It not only streamlines business processes but also minimizes data redundancy.
Today there are system solutions that cut the problem of the high cost of licenses. There are models that present attractive alternatives that are based on the number of users for a given period. SaaS (Software as a Service) offers a software delivery and licensing method of online access through a subscription. It’s not necessary to buy and install it on individual computers. It is an ideal option in which your growing manufacturing business requires the flexibility of computer tools.