Root Cause Analysis in Manufacturing – A Simple Guide
Root cause analysis is a process used to find the underlying causes of problems in manufacturing. By identifying the root cause of a problem, you can fix that problem once and for all—without having to deal with recurring issues or high costs again down the line.
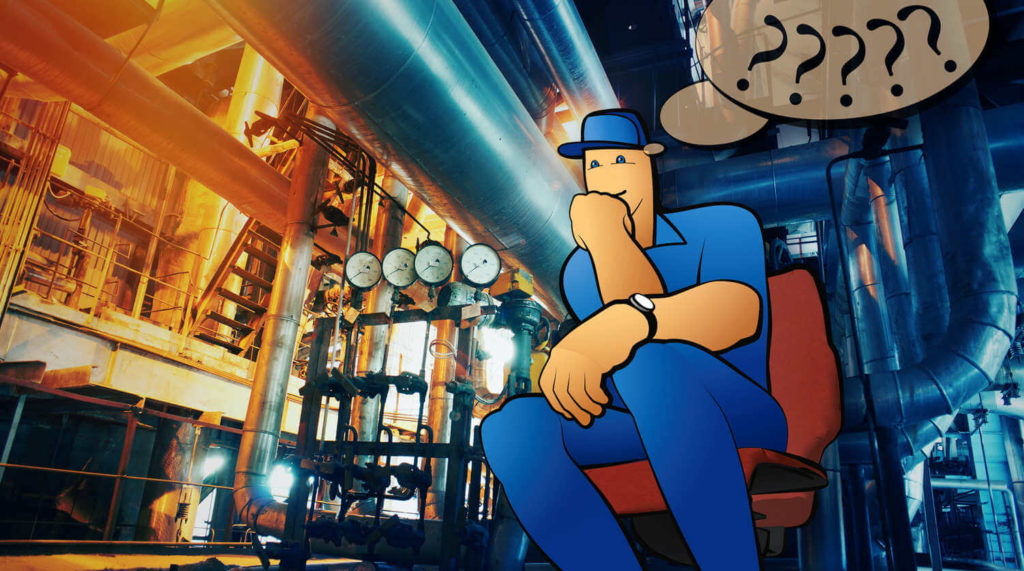
You can also listen to this article:
What is Root Cause Analysis?
Root cause analysis is the process of investigating the underlying true cause of a problem and the actions required to eliminate it. Rather than a concrete method, it is an umbrella term for a wide range of approaches, tools, and techniques that allow manufacturers to uncover the highest-level causes of problems and inefficiencies.
A root cause is therefore an issue that is the source of other issues. Visible problems or symptoms are rarely the true cause of a problem. Instead, a problem could consist of many levels of causes and effects.
For example, a manufacturer that is suffering from consistently inaccurate production scheduling mostly cannot fix the problem and stop it from reoccurring by merely scheduling better. That is because production scheduling and execution also rely on inventory management, material deliveries, work order creation, communication, and many other aspects of a business. E.g. if production schedules are perfect on paper but material deliveries are constantly late, then the cause of the delays on the vendor’s part needs to be investigated and corrected.
The 6 Basic Steps of Root Cause Analysis
There are six basic steps to follow when trying to solve a problem. These are:
- Recognize that there is a problem. Nothing will get better if you treat inefficiencies as normalcy.
- Define the problem. Make sure that everyone understands the problem in the same way.
- Analyze the problem. Try to understand the nature of the problem, the patterns involved, and the areas where the issues occur.
- Find the root cause by analyzing the causal relationships of issues until you find which possible cause contributes most to the problem.
- Eliminate the root cause.
- Monitor the symptoms to ensure that the root cause elimination was successful and removed or alleviated the problem.
These six steps are the basic framework for root cause analysis. But let us take a look at the methods used to find the root cause.
Root Cause Analysis methods
As mentioned above, root cause analysis is a collective term for an array of different approaches to problem-solving. Here are three of the best ones to use in manufacturing.
The Five Whys
The Five Whys method is a problem-solving technique that helps you to identify the root cause of a problem by asking “why” until the root cause is apparent. This method will help you gather data, understand why something is happening, and find solutions.
To use this method, begin by identifying what the problem is, then asking yourself why it occurred. For example:
Problem: Deliveries to customers are constantly late.
1. Why are deliveries constantly late? Because production finishes later than expected.
2. Why? Because raw material inventory gets depleted unexpectedly and we have to wait for another order to arrive.
3. Why? Because actual inventory levels do not correspond to the ones reported in the system.
4. Why? Because someone is not reporting material consumption correctly.
5. Why? Because John is new and he has forgotten to report material consumption.
The solution: train John to report material consumption.
Even though the method is called “The Five Whys”, the number of whys asked may vary depending on the problem. Ask as many or as few whys as it takes to identify the root cause.
Cause and Effect or Fishbone Diagram
A cause and effect diagram, also known as the Ishikawa and fishbone diagram, is a visual tool designed to graphically organize the possible causes of an issue. It is usually created by brainstorming various reasons why an error could have happened, delving into more detail as the analysis progresses.
Firstly, you will have to define the fault areas that might be responsible for the errors. In manufacturing, there can be many general fault areas that could be used as the first-level causes: measurement, materials, method, environment, suppliers, manpower, machinery, technology, management, etc. In most cases, you can exclude several of them and end up with 4-6 fault areas or branches to investigate further.
Be sure to use very short and clear descriptions when drawing the chart. After assigning higher-level causes to the branches, analyze the different groups separately, pick out the most important possible causes and try to pinpoint the root cause.
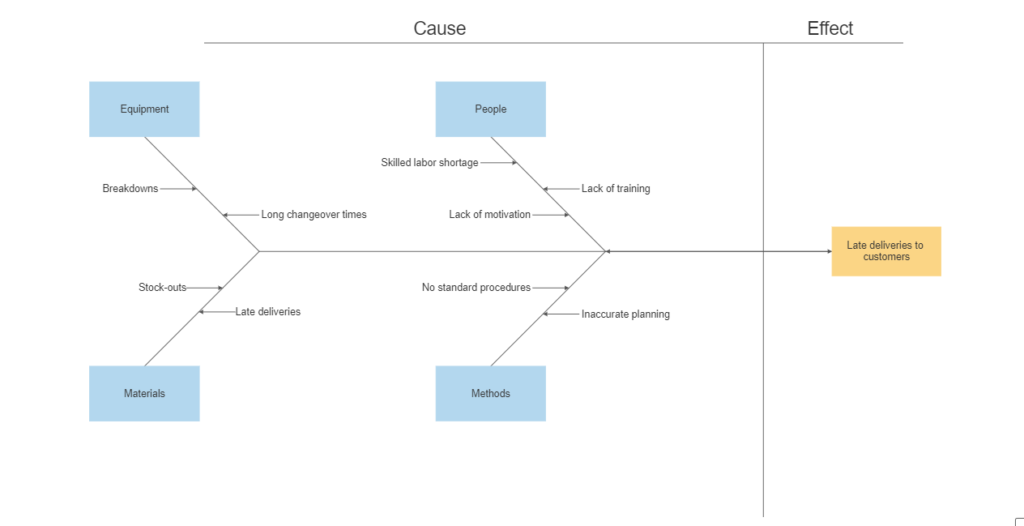
Matrix Diagrams
Matrix diagrams are a great way to investigate a number of causes and to conclude which of them has the greatest impact on the problem.
To draw a Matrix diagram, you will have to first brainstorm the characteristics of the problem and upper-level causes of the problem, then plot them on the diagram and indicate how big of an impact the upper-level causes have on the lower-level ones. Weak impact gets 1 point, medium impact 3 points, and strong impact 9 points. Then you should add the scores of possible causes together and investigate the one with the highest score first.
According to the example above, you should likely first deal with problems in the planning department and provide extra training to your employees.
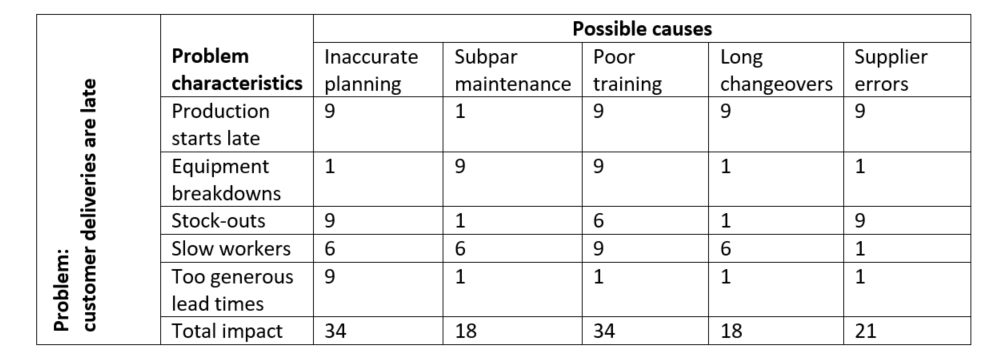
The Role of ERP/MRP in Root Cause Analysis
As ERP/MRP software is designed to collect data across the whole operation, it can be a tremendous help in detecting issues, understanding the problems, and finding their root causes. Seeing the trends and anomalies that take place in the company is easy when the data is presented clearly and when inconsistencies can be traced back with just a few clicks.
Besides looking at trends, ERP/MRP allows for the quick reviewing of individual cases. Pick any customer delivery that was delayed, and scan through the data to see where things went wrong. Was the cause due to miscommunication, unexpected breakdown, or something else? Label each case appropriately and soon enough you will have collected enough data to know the important issues to work on – and which should be analyzed even deeper.
But apart from helping to detect inconsistencies and find their underlying causes, ERP/MRP systems also directly and indirectly eliminate many root causes, if they are well implemented. Automatic collection of data across the enterprise, simple reporting of activities, elimination of double-entry, and easy generation of reports all minimize human error, but also provide immediate visibility of developing issues before they can wreak havoc in your supply chain (see also the “Bullwhip effect”).
When this kind of software is correctly implemented and the inputs it is given are correct, inaccuracy in production planning and scheduling, lead time and production cost estimation, and inventory management can be largely eliminated, as can many other causes of inefficiency. As an example, the users of MRPeasy report a 42% increase in on-time deliveries on average after implementing the system.
Key takeaways
- Root cause analysis is an umbrella term for the various methods and processes of investigating the underlying causes of problems and the actions required to eliminate them.
- There are six defined steps in problem-solving: 1) recognize that there is a problem; 2) define the problem; 3) analyze the problem; 4) find the root cause; 5) eliminate the root cause; 6) monitor the symptoms.
- Some of the simplest root cause effect methods are the Five Whys, the Fishbone Diagram, and the Matrix Diagram.
- Implementing an ERP/MRP system can help you quickly identify problems and their root causes, and eliminate them.
You may also like: Quality Control in Manufacturing – An Introduction