Raw Material Inventory Management Guide for SMEs (2025)
Raw materials are the substances or components used in the production of goods. Properly managing their raw material inventory allows manufacturers to ensure a smooth production flow, control costs, and respond promptly to customer demand.
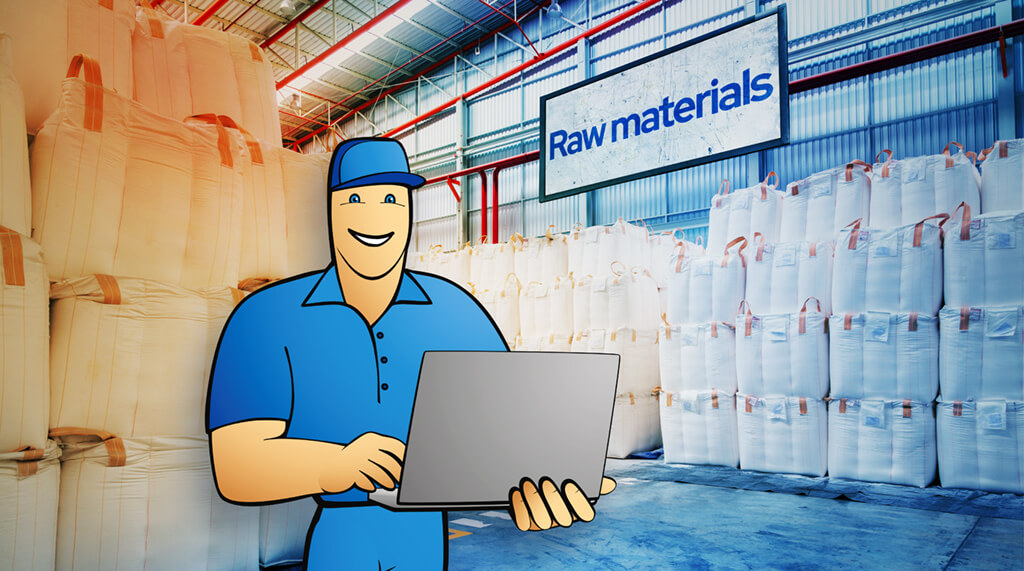
You can also listen to this article:
What are raw materials?
In manufacturing, raw materials are the basic substances or components used in the production of goods. As the foundation for creating finished products, raw materials go through processing or assembly during manufacturing, yielding finished goods in the end.
Although in a narrower sense, raw materials are unprocessed or minimally processed resources extracted from nature (such as minerals and ore, agricultural products, and wood), in manufacturing inventory management, we can use the term to signify every type of material or item that is used as a component in the bill of materials (BOM) of a finished product.
As such, a finished product made in one factory can be used as a raw material in another manufacturing facility. For example, the printed circuit boards manufactured in Company A can be used to assemble electronic devices in Company B.
Direct materials and indirect materials
In manufacturing management, the materials used in production are broadly divided into direct and indirect materials.
Direct materials
Direct raw materials are directly incorporated into the final product, i.e. they are a part of the final product’s bill of materials. For instance, in manufacturing a chair, direct materials would include the wood, fabric, and other components used to construct the chair. These materials and components should be tracked precisely to ensure accurate accounting and avoid critical stockouts or overstocking.
Indirect materials
Indirect raw materials, on the other hand, are necessary for the production process but are not directly part of the final product or do not incur a noteworthy cost. These may include tools, screws and nails, lubricants, adhesives, cleaning agents, disposable tools, or other supplies required to facilitate manufacturing operations. While they may not be part of the product, their availability and proper management are equally vital to maintain an efficient production process.
Indirect materials are often also referred to as MRO (maintenance, repair, and operations) inventory or non-inventory items.
Raw materials vs. WIP
WIP or work-in-process inventory refers to goods that have already entered the production process, constituting an intermediate step between raw materials and finished goods. WIP is therefore considered a separate type of inventory that needs to be accounted for separately from raw materials and finished goods.
Read more about WIP inventory.
What is raw material inventory management?
Raw material inventory management is the strategic process of organizing the procurement, storage, and handling of raw materials in the production of goods to ensure there is enough stock on hand to maintain a good production flow. It is a crucial aspect of supply chain management for manufacturing companies as it impacts overall production efficiency, cost control, and the bottom line of the business.
Unlike finished goods inventory management, which deals with the stock of completed products awaiting sale, raw material inventory management focuses on the purchasing and storing of materials at various stages of the production cycle. In this process, manufacturing companies must optimize their inventory levels to strike the right balance as overstocking of raw materials ties up working capital and leads to higher inventory costs, while insufficient raw material inventory may cause production delays and negatively affect customer satisfaction.
Effective raw material inventory management involves tracking and measuring key metrics related to inventory, such as the inventory turnover ratio, inventory costs, spoilage, etc. These metrics aid in decision-making and highlight areas for optimization.
Manufacturing costs, in turn, are heavily influenced by raw material inventory management. By implementing efficient inventory control measures, businesses can reduce carrying costs and minimize the risk of obsolete or expired materials. This, in turn, positively impacts the company’s bottom line, enhancing profitability and competitiveness.
Why is raw material inventory management important?
Efficient raw material inventory management plays an essential role in the overall success of any manufacturing business. Here are some key reasons why you should be mindful of your raw material inventory:
- Ensuring an uninterrupted production flow. Adequate raw material inventory levels ensure a steady flow of inputs into the production process, reducing the risk of shortages and avoiding costly disruptions. By accurately forecasting demand and setting appropriate reorder points and safety stocks, businesses can maintain a consistent supply of raw materials and avoid delays or production stoppages.
- Cost control. By monitoring and managing raw material inventory, businesses can optimize their procurement and avoid over- or understocking. Overstocking ties up valuable capital and leads to increased inventory costs, while understocking results in missed opportunities and dissatisfied customers. Effective raw material inventory management helps strike a balance, reducing waste and maximizing the cost-effectiveness of the manufacturing process.
- Meeting customer demand. Maintaining optimal raw material inventory levels allows businesses to meet customer demand promptly. By understanding customer demand patterns and implementing effective forecasting techniques, businesses can align their raw material inventory with market needs, ensuring a healthy production flow and achieving higher customer satisfaction levels.
- Supply chain efficiency. Effective inventory management enables streamlined coordination across the supply chain, reducing lead times and improving overall operational efficiency. By sharing real-time inventory data with suppliers, manufacturers can ensure timely replenishment, minimize stockouts, and avoid disruptions in the production process.
- Accurate accounting. Precise tracking of raw material quantities and values is crucial for financial reporting and cost analysis. Properly managing inventory levels ensures that the balance sheet reflects the true value of raw materials on hand, affecting the company’s current assets. Additionally, raw material costs directly impact the cost of goods sold (COGS), which affects the company’s profitability.
Raw material inventory management challenges faced by small manufacturers
Small businesses face unique challenges in managing their raw material inventory due to limited resources, smaller production volumes, and less sophisticated inventory systems. Some common challenges include:
- Limited capital. Small businesses may have limited capital to invest in large quantities of raw materials, leading to difficulties in bulk purchasing and taking advantage of volume discounts.
- Inventory space. Small businesses may have limited physical space to store large quantities of raw materials, necessitating careful space management and just-in-time inventory practices.
- Supplier dependence. Relying on a few suppliers for raw materials can lead to supply chain disruptions if a supplier faces issues with production, delivery delays, or price fluctuations.
- Cash flow constraints. Balancing inventory costs with cash flow constraints can be challenging for small businesses, as holding excess inventory ties up capital that could be used for other essential business expenses.
- Quality control. Ensuring consistent quality of raw materials from suppliers can be challenging for small businesses, affecting the final product’s quality and customer satisfaction.
Addressing these challenges requires strategic planning, effective inventory management practices, building strong supplier relationships, and adopting appropriate inventory management systems or software tailored to the specific needs of small businesses.
10 essential raw material inventory management tips
Here are some of the best practices you can use if you want to start properly managing your raw material inventory:
- Create an SKU system. Stock-keeping units (SKUs) are the basis of effective inventory management. Provide each type of raw inventory item a unique code that helps you track their movements and current inventory levels.
- Keep materials physically organized. Draw up a detailed layout scheme of your warehouse, with a designated area allocated for raw materials. Make sure that the raw materials are close enough to the production floor to ensure quick access. Store fast-moving items closer to the picking area.
- Forecast demand. Utilize historical data and market trends to predict future demand accurately. This allows businesses to plan inventory levels accordingly, accounting for seasonality, avoiding stockouts or excess inventory, and leading to improved customer satisfaction and cost efficiency.
- Use safety stock and reorder points. Set safety stock levels to handle unexpected demand fluctuations and establish reorder points to trigger timely replenishment orders. These techniques help avoid production delays and stockouts, ensuring seamless operations.
- Optimize your production schedules. Align production schedules with raw material availability to reduce idle time and streamline production processes. This minimizes inventory holding costs, enhances resource utilization, and improves overall operational efficiency.
- Perform ABC analysis. Classify raw materials based on value and usage frequency using ABC analysis. Prioritize high-value items for more stringent control, helping allocate resources effectively and focus on critical inventory management areas.
- Build strong supplier relationships. Collaborate closely with suppliers to ensure timely and reliable deliveries. Strong supplier relationships reduce lead times, minimize supply chain disruptions, and improve overall inventory management efficiency.
- Implement just-in-time inventory. Adopt a JIT strategy to receive raw materials as needed for production, minimizing holding costs. This approach optimizes cash flow, reduces inventory carrying costs, and fosters lean inventory management.
- Ensure traceability. Use inventory tracking systems to monitor and trace raw materials throughout the supply chain. This provides real-time visibility, allowing businesses to locate materials, detect potential issues as well as their root causes, and ensure compliance with quality and safety standards.
- Adopt software. All of the steps above can be much more easily achieved by implementing manufacturing ERP software. These systems are designed to automate time-consuming administrative tasks, calculate material requirements, streamline inventory control, and facilitate data-driven decision-making, improving inventory management as well as the overall effectiveness of manufacturing companies. It is advisable to implement a manufacturing ERP suite rather than just an inventory management software in order to integrate raw material management with production, procurement, sales, finances, etc.
Raw material inventory valuation
Determining your raw material inventory value is essential for accurate financial reporting and understanding the true value of your inventory. There are several methods to calculate the value of your raw material inventory, and the choice of method depends on accounting principles, company policies, and applicable regulations. Here are the commonly used methods for determining your raw material inventory value:
- FIFO (First-In, First-Out). This method assumes that the first batch of raw materials purchased is the first to be used or sold. As a result, the cost of the most recently acquired raw materials is assigned to the ending inventory, and the cost of the raw materials purchased earlier is assigned to the cost of goods sold (COGS). FIFO is commonly used when prices have a tendency to become higher.
- LIFO (Last-In, First-Out). LIFO assumes that the last batch of raw materials purchased is the first to be used or sold. Therefore, the cost of the most recent purchases is assigned to the cost of goods sold, and the cost of the oldest raw materials is assigned to the ending inventory. LIFO is often used in times of inflation to reduce taxable income by matching higher costs with revenue.
- Weighted Average Cost (WAC). This method calculates the average cost of all similar raw material units available during the accounting period. The average cost is then used to value both the ending inventory and the cost of goods sold. Weighted average cost smoothens out fluctuations in prices and can be helpful in stable price environments.
It’s important to note that the chosen method of raw material inventory valuation should be consistent and in accordance with generally accepted accounting principles (GAAP) or the accounting standards in your country that apply to your company. Accurate raw material inventory valuation ensures that your financial statements provide an accurate representation of your company’s assets and financial performance. Additionally, consult with your accounting or financial team for guidance on which valuation method is most suitable for your business.
Calculating raw material inventory value
Calculating the raw material inventory value involves determining the total cost of the raw materials currently held in stock. You can do it by following the following steps:
- Gather inventory data. Begin by collecting all relevant information about the raw materials in your inventory. This includes the quantity of each raw material SKU on hand and the unit cost of each material.
- Identify the valuation method. Determine the method of inventory valuation you will use. As mentioned earlier, common methods include FIFO, LIFO, and Weighted Average Cost.
- Calculate the total value for each raw material SKU:
- For FIFO, determine the unit costs of the raw material lots remaining in your inventory at the end of the accounting period (these are from the most recent purchases) and multiply the purchases’ unit costs by the number of units left in the corresponding stock lot. Then add the results together.
- For LIFO, determine the unit costs of the ending raw materials (in LIFO, these should originate from the earliest purchases as the last purchases are the first to be consumed) and multiply the purchases’ unit costs by the number of units left in the corresponding stock lot. Then add the results together.
- For Weighted Average Cost, add up the total cost of all similar units of raw material in stock and divide it by the total quantity to find the average cost per unit. Multiply this average cost by the quantity of each raw material SKU.
- Sum the total value. Add up the calculated values for each type of raw material to obtain the total raw material inventory value.
- Reconcile with financial records. Ensure that the calculated value aligns with your accounting records and financial statements.
You can also use a manufacturing inventory management system such as a manufacturing ERP to automatically calculate your inventory value according to your preferred valuation method.
Example 1: FIFO (First-In, First-Out)
Assume you are a furniture manufacturer that made the following purchases of table tops during a specific accounting period:
Purchase 1: 100 units at $5 per unit
Purchase 2: 150 units at $6 per unit
Purchase 3: 200 units at $7 per unit
At the end of the accounting period, you have 250 table tops in stock. That means you consumed 200 units.
As we use the FIFO inventory valuation method, the 200 units have to come out of the first purchases. Meaning that 50 of the 250 units left came from Purchase 2 and 200 from Purchase 3.
The ending inventory is therefore:
50 units (from Purchase 2) at $6 per unit = $300
200 units (from Purchase 3) at $7 per unit = $1400
Total Ending Inventory Value = $300 + $1400 = $1,700
Example 2: LIFO (Last-In, First-Out)
Using the same purchases for table tops as in Example 1, we are left with 250 units, 100 of which are from Purchase 1 and 150 from Purchase 2.
100 units (from Purchase 1) at $5 per unit = $500
150 units (from Purchase 2) at $6 per unit = $900
Total Ending Inventory Value = $500 + $900 = $1400
Example 3: Weighted Average Cost (WAC)
Assume you have the following purchases of table tops during a specific accounting period:
Purchase 1: 100 units at $5 per unit
Purchase 2: 150 units at $6 per unit
Purchase 3: 200 units at $7 per unit
At the end of the accounting period, you have 250 table tops in stock.
Total cost of all similar units in stock:
Total cost of Purchase 1 = 100 units x $5 per unit = $500
Total cost of Purchase 2 = 150 units x $6 per unit = $900
Total cost of Purchase 3 = 200 units x $7 per unit = $1,400
Total cost during the accounting period = $500 + $900 + $1400 = $2800
Total quantity during the accounting period = 100 units + 150 units + 200 units = 450 units
Weighted Average Cost per Unit:
= (Total Cost of all similar units in stock) / (Total Quantity)
= $2,800 / 450 units
= $6.22/unit
The ending inventory value is therefore:
250 x $6.22 = $1,555
Using MRP/ERP software for raw material inventory management
Although raw material inventory can be managed (to some degree) with spreadsheets, it is a terribly inefficient way to do it. Especially considering that designated manufacturing management solutions have become so easy to use and affordable that even the smallest manufacturer can utilize them.
In a manufacturing ERP or MRP software, a bulk of the aspects of raw material inventory management is either entirely automated or made exceedingly simple. This way, small business owners do not need to fret about hiring highly specialized staff members, e.g. compliance managers or material planners, to achieve those specific gains.
Within this designated software, each inventory movement is recorded, which sets the basis for demand forecasting, cost control, KPI monitoring, traceability, inventory valuation, and many other aspects of effective raw material inventory management.
Key takeaways
- Raw materials are the foundational components used in manufacturing goods.
- Direct materials are integral to the final product, while indirect materials facilitate production but aren’t part of the end product. Both, however, require effective tracking and management.
- Raw material inventory management involves procuring, storing, and utilizing materials for production. Balancing inventory levels is vital to prevent overstocking, stockouts, and production disruptions.
- Efficient management ensures a steady production flow, cost control, customer satisfaction, and supply chain efficiency, all influencing the bottom line.
- Valuation methods such as FIFO, LIFO, and Weighted Average Cost are crucial for accurate financial reporting and asset evaluation.
- Utilizing manufacturing ERP software streamlines raw material inventory management, automates processes, ensures compliance, and enhances overall efficiency.
Frequently asked questions
An example of raw material inventory is steel sheets used in an automotive manufacturing facility.
To calculate raw material inventory, total the cost of all units of raw materials on hand based on the chosen valuation method (e.g., FIFO, LIFO, WAC).
Yes, raw materials inventory is reported as a current asset on the balance sheet.
Yes, raw materials are a key type of inventory item used in production processes.