Production Reporting Guide for Manufacturing SMBs
For small manufacturers, having a clear understanding of what’s happening on the shop floor is paramount to meeting production goals. Efficient production reporting is an essential aspect of manufacturing, ensuring a clear view of operations.
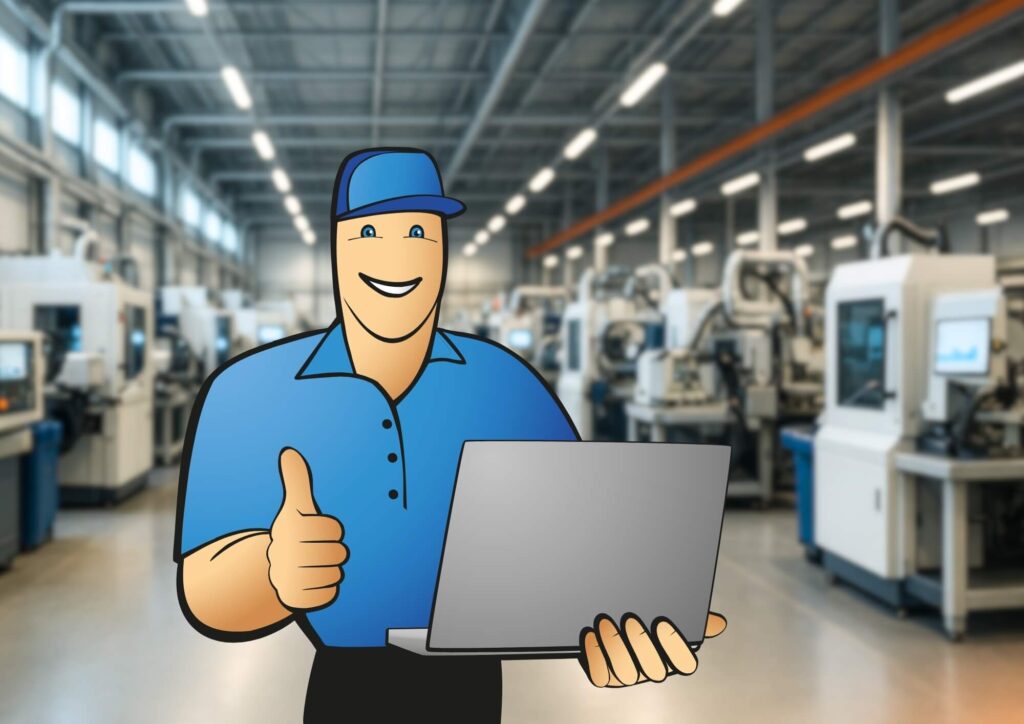
What is production reporting?
Production reporting is the task of recording and tracking the progress of manufacturing processes like the completion and speed of tasks, the quantity of materials consumed, the number of errors that occurred, etc. It’s a vital aspect of production management that ensures the manufacturing operation is running according to production plans, in a timely manner, and with a high quality rate.
Production reporting helps managers get an overview of the shop floor’s functioning, ensure alignment with production schedules, and gain insights into production efficiency, capacity utilization, and other performance metrics.
Production can be reported in various ways, depending on the production management system used and the nature of the processes that are being tracked. Reporting can thus be:
- .. fully manual, like in very simple or paper-based manufacturing systems.
- .. partially digital, for example, if basic inventory management software or spreadsheets are utilized to track material consumption, but labour processes are tracked manually.
- .. fully digital, if comprehensive production software or a manufacturing execution system (MES) is set up to track all production processes.
- .. partially or fully automated, in instances where machinery includes sensors that automatically track processes.
In each case, the outcome is production reports, which help gain an overview of production progress and provide actionable insights for analysis and visualization.
What is a production report?
A production report is a document that details and summarizes various manufacturing metrics measured within the production reporting process, with the end goal of helping maximize production efficiency. They can range from simple spreadsheets with a few formulas to detailed lists and tables that provide info on various manufacturing metrics. Modern manufacturing software compiles production reports into dashboards for easy understanding and analytics.
Data for production reports is gathered at different points within the manufacturing process. Reports are then compiled manually or automatically from the data. Advanced MRP systems include many different reports, from shop floor labor reports and material consumption to quality control, finished goods counts, write-offs, and more.
What should production reports include?
As mentioned, the information gathered in reports can vary largely depending on the manufacturing and production management system utilized. Reports can include information on various metrics such as:
- Finished goods count – the total number of completed products.
- Production rates – output measured over specific time periods (e.g., per shift, day, or batch).
- Order statuses – progress on individual customer orders, including delivery timelines (on-time or delayed).
- Machine efficiency – performance data for equipment, including metrics like Overall Equipment Effectiveness (OEE).
- Work-in-process (WIP) levels – the quantity of unfinished goods and their stage of completion.
- Quality control metrics – inspection results, quality checkpoints passed or failed, etc.
KPIs for gauging production efficiency
Production reports are actionable documents that help managers gain in-depth overviews of the production process, all with the ultimate goal of increasing production efficiency. The data they collect is used to calculate various manufacturing key performance indicators (KPIs).
While there are dozens of production-centric KPIs, deciding which ones to track should be a weighted decision. KPIs relevant to your operation should be actionable, easily attainable, and aid in achieving the company’s strategic goals.
Here are some of the key metrics used for measuring production efficiency.
- Overall Equipment Effectiveness (OEE) – Measures how effectively equipment is being used. OEE combines availability, performance, and quality into a single percentage score.
- Total Effective Equipment Performance (TEEP) – Expands on OEE by factoring in all available time, including planned downtime, to reflect the full potential utilization of equipment.
- Capacity Utilization – Measures the percentage of total production capacity that is actually being used. It’s useful for determining whether you’re maximizing resources.
- Production Downtime – Tracks the time that production equipment is not operational, usually categorized by maintenance, breakdowns, or material shortages.
- Cycle Times – the time taken for each process, often compared against standard rates for efficiency tracking. These further inform Throughput Time, which sums the time a product spends in the manufacturing process into a single metric.
- First Pass Yield (FPY) – Calculates the percentage of products manufactured correctly without the need for rework or repair, reflecting process quality and efficiency.
- Scrap Rate – Tracks the percentage of materials wasted during production. It complements FPY by giving more insight into waste.
Continue reading about manufacturing KPIs.
Implementing production reporting
So, how do you implement a production reporting system for your manufacturing operation? A suitable approach depends on several factors, including the manufacturing setup, what is being produced, and the type of production management system in use. Roughly speaking, production reporting can be done either manually, on paper or a spreadsheet, or automatically using digital tools. However, manufacturers often opt for a mix-and-match solution, blending elements of both depending on specific needs.
Manual production reporting
Manual production reporting involves recording production data by hand or using simpler tools like Excel. This method is often used in smaller operations or in environments without centralized management software. It can also offer flexibility in non-standard environments, such as custom jobs or prototyping, where automation isn’t always feasible. However, while it is often a practical starting point, manual reporting has limitations.
For one, manual input increases the risk of human error, and since reports have to be compiled after the fact, actionable insights are often delayed. Additionally, manual methods offer little to no real-time visibility into production performance, making it harder to respond quickly to issues. Data consolidation also becomes more challenging, especially when information is gathered from multiple teams or shifts, which can hinder accuracy and lead to inconsistencies.
But despite its drawbacks, manual reporting can work for simpler setups or when the cost of automation isn’t justified. Still, more timely and accurate data becomes critical as operations scale in size and complexity.
Automatic production reporting
Automatic production reporting relies on manufacturing software to aid in the collection and processing of production data. These systems integrate directly with the shop floor and stockroom, allowing for seamless data entry and automatic analysis. Because the software is connected to the entire manufacturing operation, data from reporting also integrates with other processes such as maintenance scheduling, procurements, or quality control, ensuring a more cohesive operation.
Methods of automatic reporting include:
- Shop floor reporting: Operators input production data directly into the system via internet-connected terminals. Cloud-based manufacturing software also allows reporting with mobile devices and tablets through dedicated apps.
- Barcode scanning systems: Barcodes are scanned at different stages of production to update progress automatically.
- IIoT devices and sensors: Machinery equipped with sensors or RFID technology tracks production metrics without manual input. Manufacturing Execution Systems often act as a central hub for these methods, coordinating data collection across different sources and integrating production reporting with higher-level planning and control systems.
Production reporting best practices for SMEs
Let’s look at six tips for implementing a coherent production reporting system.
1. Map out the production process
Begin by thoroughly mapping out your manufacturing process. Identify each stage, task, and key data point. This provides the foundation for effective production reporting, as it ensures that all activities relevant to you are accounted for from start to finish. A clear process map helps pinpoint where data should be collected and highlights any gaps or inefficiencies that could affect reporting accuracy.
2. Define and document data collection procedures
Once the production process is mapped out, develop Standard Operating Procedures (SOPs) to define and document how production data should be collected, recorded, and reported. SOPs are a practical guide for employees that detail the specific methods, tools, and reporting frequencies to follow. They promote consistency, help reduce variability, and ensure that data management aligns with the overall operational strategy.
3. Train employees on data management
It’s vital that employees involved in production monitoring understand both how to collect data and why accurate reporting matters. Training should cover data entry methods, the importance of timely reporting, and how this data supports broader operational goals. Assigning clear accountability for reporting tasks ensures that data collection and review are consistently carried out.
4. Track and report relevant data
Focus on only capturing data that’s necessary to reach your business objectives. Identify the KPIs relevant to your operation and ensure your reporting process is tailored to track them. Avoid overwhelming the system with unnecessary data points that don’t contribute to actionable insights.
5. Automate production reporting where possible
Where feasible, leverage technology to automate data collection and reporting. This can include using barcode scanners, shop floor terminals, or integrating with IIoT devices. Automation is sure to reduce manual input, minimize errors, and provide real-time data on production performance.
6. Review and refine regularly
Production reporting processes should not be static. Regularly review the data being collected and the reporting workflows to ensure they remain aligned with business objectives. Continuously improving and refining operations helps maintain relevance and effectiveness as operations evolve.
The benefits of efficient production reporting
Well-thought-out (and at least partially automated) production reporting allows managers to make informed decisions and respond to issues faster. Here’s a closer look at core benefits.
- Real-time visibility on production status. Efficient reporting gives you a real-time pulse on what’s happening across production. When connected through an MES or MRP system, this data becomes instantly accessible to the whole team, making it easier to spot when something’s off track and keep progress aligned with your production goals, all while the shop floor keeps moving.
- Reduced production downtime. Up-to-date reporting helps detect patterns that can lead to unplanned downtime. Insight from accurate reports enables timely adjustments that prevent problems from snowballing. Reporting also helps identify the root causes of issues, such as equipment failure, supply chain delays, or staffing issues.
- Easily spot bottlenecks. Production reports can also help highlight areas where workflows slow down or stall. They allow managers to pinpoint bottlenecks and implement targeted improvements to increase production output and reduce lead times.
- Enhanced traceability and digital thread. Production reporting creates a digital record of production activities and is a core component of end-to-end traceability. Traceability supports quality control, helps uncover the root causes of issues, and is often an essential requirement for entering regulated markets. A complete digital thread also simplifies compliance and makes audits far less stressful.
- Strategic decision-making. This all boils down to the fact that reliable access to accurate production data enables strategic long-term planning and decision-making. Big decisions need to be based on accurate data to ensure profitability. So, whether adjusting capacity, investing in new equipment, or shifting production schedules, production reporting done right is a short path to more effective management choices.
Integrated manufacturing software with real-time shop-floor reporting
Manufacturing ERP systems take production reporting to the next level by connecting the shop floor directly with the wider business management process. MRPeasy offers built-in production reporting tools that simplify data collection, improve visibility, and provide real-time insights into manufacturing operations for SMEs.
Simplified production reports
MRPeasy integrates production reporting straight into core manufacturing functionalities like inventory management, procurement, and scheduling. Production data flows directly from the production line into the ERP system without the need for disconnected spreadsheets.
MRPeasy’s production reporting tools enable easy progress tracking on production orders, monitoring resource usage, overseeing worker operations, and capturing production volumes. It also allows businesses to generate detailed reports on work order statuses, labor time, material consumption, and finished goods, supporting both daily operations and long-term planning.
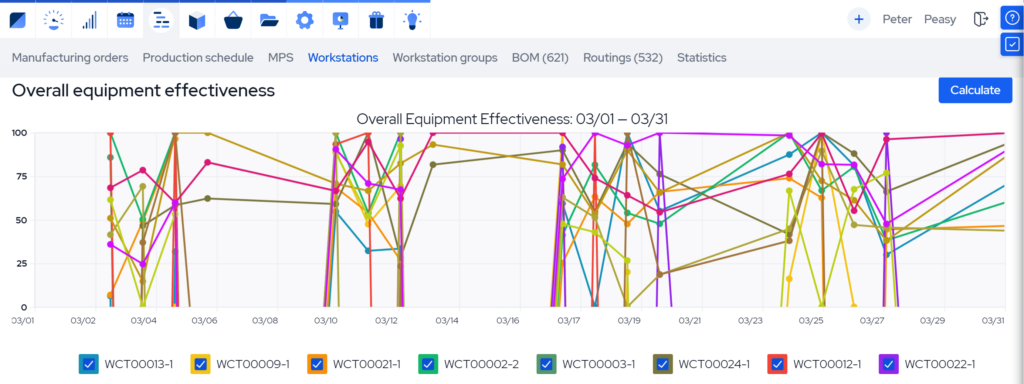
Turn data into insights with dashboards and analytics
Integrated manufacturing software also compiles production data into dashboards. MRPeasy’s production dashboards present easy-to-grasp summaries on production progress, efficiency, and downtime. This allows stakeholders to get fast insights and highlight trends and anomalies in the production process.
MRPeasy also supports advanced analytics integrations like Microsoft Power BI, allowing you to go beyond basic data analysis. Through connecting production data with analytics tools, small businesses can uncover deep insights into their operations, from identifying long-term efficiency trends to predicting potential bottlenecks before they occur.
Key takeaways
- Production reporting is the process of tracking and recording manufacturing activities like task completion and material usage to ensure that operations align with production plans.
- Accurate production reporting is essential for small manufacturers to monitor shop floor activities, gain a tactical overview of operations, and usher in data-based decision-making.
- Production reporting can be conducted manually using spreadsheets or automated through integrated systems like manufacturing ERPs and manufacturing execution systems (MES) for real-time data collection.
- Guidelines for implementing efficient production reporting include mapping out your processes, defining how and when data should be collected, and training your team to follow these standards.
- Reporting should be automated wherever possible, with regular reviews and tweaking to keep it aligned with business goals.
- Manufacturing software offers the best solution for production reporting. It integrates reporting with core business functions like stock, finances, and production, and provides real-time dashboards and advanced analytics for added insights.
Frequently asked questions (FAQ)
A production report summarizes key manufacturing data, such as production output, resource usage, and process efficiency, to help production managers optimize operations and identify issues by tracking manufacturing progress.
A production report typically includes metrics like finished goods count, production rates, order statuses, machine efficiency (OEE), work-in-process levels, and quality control results. The exact data depends on the operation’s goals and the production system in place.
The frequency of production reporting depends on the complexity and pace of your operation. For many SMEs, daily or shift-based reporting provides timely insights, but real-time reporting using automated systems provides up-to-the-minute visibility for much faster decision-making.
You might also like: Batch Tracking – A Simple Guide