Production Orders and How to Use Them More Efficiently
Efficiently managing production orders is key to staying ahead in manufacturing—here are actionable tips to help you optimize the process.
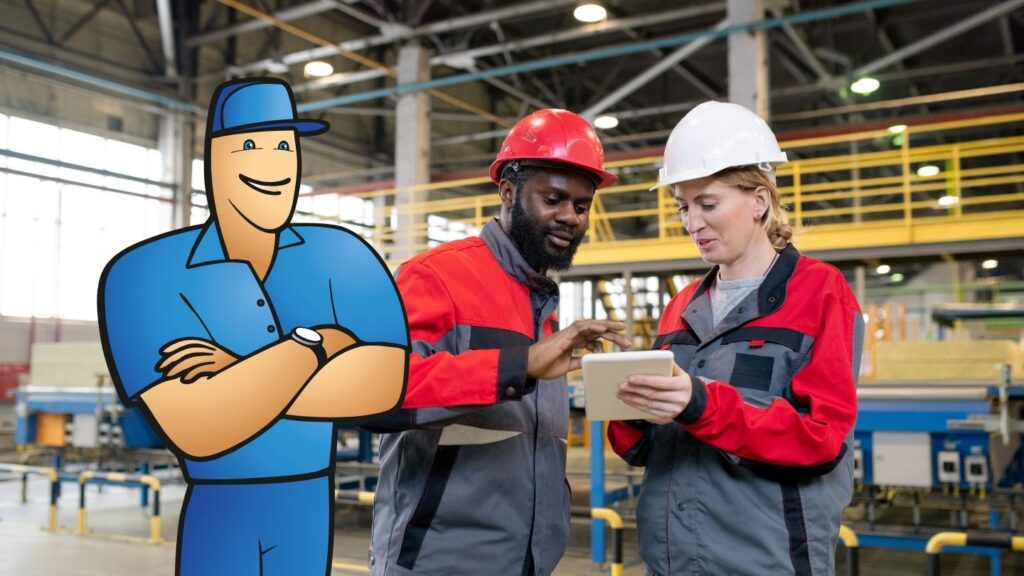
What is a production order?
A production order is a detailed document that, in its simplest form, outlines what needs to be manufactured and when it should be finished. More than just documents, production orders serve as roadmaps that guide the transformation of raw materials into finished products. They coordinate everything from material requirements and labor to machinery scheduling and quality control.
Sales orders may lay the groundwork for building profits. But production orders are the backbone of any manufacturing operation’s success.
While production orders began as simple paper-based systems, they have since evolved alongside manufacturing technology. Today’s digital solutions offer real-time production tracking, automated scheduling, and predictive capabilities—yet many small- to mid-size manufacturers struggle to balance traditional methods and modern digital approaches.
Understanding how to effectively manage production orders is key to improving efficiency, reducing costs, and staying competitive in today’s manufacturing industry. When you use production order systems effectively, your manufacturing process invariably improves.
Components and types of production orders
A production order transforms a customer order or inventory demand into actionable manufacturing instructions. Before diving into how to manage production orders effectively, it’s essential to understand their core components and different types, and how they fit into manufacturing processes.
Every production order contains several critical elements:
- Product specifications. Detailed information about what needs to be produced, including quantities, dimensions, materials, and any special requirements.
- Bill of materials (BOM). A comprehensive list of all raw materials, components, and sub-assemblies required for production, including order quantities of each.
- Routing information. Step-by-step instructions outlining the manufacturing process, including which work centers on the shop floor will be involved and in what order.
- Production schedule. Timeline for production, including start and end dates for each manufacturing stage, up to and including shipping the finished products out the door.
- Quality control requirements. Specific checkpoints and criteria to ensure the finished product meets all specifications as noted in the purchase order.
- Production order status. Modules designed to indicate where the product is in the workflow.
Production orders typically fall into four main categories, each serving different manufacturing needs.
Made-to-Stock (MTS) orders are used for standard products with predictable demand. These items are manufactured based on forecasts and stored as inventory, allowing for quick delivery when orders come in. Think of common household items or standard industrial parts. These planned orders are made in advance of sales orders received.
Read more about MTS Manufacturing Workflows
Made-to-order (MTO) represents the opposite approach—production begins only after receiving a customer order. This method is ideal for customized products or items with unpredictable demand, minimizing inventory costs but potentially requiring longer lead times. One caveat, though: Depending on the delivery due date and availability of parts and workstations, you may need to use either forward scheduling or backward scheduling.
Assemble-to-Order (ATO) offers a middle ground. Basic components and sub-assemblies are manufactured in advance, but final assembly waits for specific customer orders. This hybrid approach balances quick delivery times with customization options. This is often used to keep products in stock without taking up too much warehouse space. This is particularly good for bulky items such as dining room or bedroom sets in the furniture industry.
Read more about MTO and ATO Manufacturing Workflows
Engineer-to-Order (ETO) is the most specialized type, where each product is designed and manufactured specifically to meet unique customer requirements. This approach is common in industries like custom machinery or specialized equipment manufacturing. While you may have a base model you offer, customer specifications often include requirements and options not typically offered. In this case, a well-defined production order is exceptionally vital.
Read more about ETO Workflows
The production order life cycle
The lifecycle of a production order follows a clear sequence of events, each building upon the last. It begins with order creation, where customer requirements or inventory needs are translated into manufacturing specifications. Next comes raw material planning, ensuring all necessary components will be available when needed.
The scheduling phase allocates resources and sets timelines, considering current production capacity and other orders in the pipeline.
During production execution, the order moves through the manufacturing process according to its routing instructions. Quality checks occur at predetermined points to catch any issues early. Finally, the order reaches completion when the finished product meets all specifications and is ready for delivery to the customer or placed in inventory.
Best practices for efficient production order management
Efficient production order management relies on several key practices that work together to ensure smooth operations. The foundation starts with accurate demand forecasting—analyzing historical data, market trends, and customer patterns to predict future needs.
This forecasting drives both inventory management and production scheduling, helping prevent costly overstock situations or devastating stockouts.
Communication stands as another critical pillar. Clear channels between sales, production, inventory, and shipping departments ensure everyone works from the same information. Regular updates about process order status, potential delays, or quality issues help teams respond quickly to challenges before they become problems.
Real-time monitoring has become increasingly vital in modern manufacturing. Whether using sophisticated software or simpler tracking methods, maintaining visibility into order status, machine and labor availability, and inventory levels allows for better decision-making.
When issues arise, managers can quickly reallocate resources or adjust schedules to maintain production flow.
Smart inventory management ties everything together. This means:
- Maintaining optimal stock levels of raw materials without overbuying
- Tracking work-in-process inventory accurately
- Ensuring finished goods move efficiently to customers or warehouse storage
- Setting up reorder points that account for lead times and demand variations
Quality control should be integrated throughout the process, not treated as a final checkpoint. This means establishing clear quality standards, implementing regular checks during production, and maintaining detailed documentation of any issues and resolutions.
Finally, continuous improvement should be part of your management strategy. Regularly review your processes, analyze bottlenecks, and seek feedback from staff at all levels. The most efficient operations are those that consistently look for ways to improve their processes while maintaining quality standards.
Common challenges and solutions
Manufacturing operations face several common hurdles in production order management, but each has practical solutions.
Data accuracy issues, from incorrect inventory counts to misinterpreted specifications, can wreak havoc on production planning. Implementing verification systems and regular auditing processes, along with barcode scanning or RFID technology, can dramatically reduce these errors while improving tracking accuracy.
Communication gaps between departments often lead to misaligned priorities and missed deadlines. Setting up standardized communication protocols, such as daily standup meetings or shared digital dashboards, keeps everyone informed and aligned. This transparency helps prevent the “silo effect” where departments operate in isolation.
Resource allocation becomes particularly challenging when managing multiple orders with competing priorities. The solution lies in implementing clear prioritization systems and using scheduling tools that can optimize resource distribution. These tools can help balance machine capacity, labor availability, and material requirements across multiple orders.
Inventory management presents another common challenge, with manufacturers struggling to balance stock levels with demand. Real-time inventory tracking systems, combined with automated reorder points and safety stock calculations, can help prevent both stockouts and excess inventory. This approach ensures materials are available when needed while minimizing carrying costs.
Production delays, perhaps the most visible challenge, often result from a combination of the above issues. Addressing delays requires a proactive approach: implementing early warning systems to identify potential bottlenecks, maintaining backup plans for critical processes, and ensuring quick response protocols are in place when issues arise.
Modernizing production order management
While the benefits of modern production order management systems are clear—improved accuracy, better efficiency, and enhanced customer satisfaction—many small and medium-sized manufacturers hesitate to make the transition.
Understanding both the advantages and challenges of modernization can help companies make informed decisions about upgrading their systems.
Digital cloud-based solutions offer significant improvements and benefits over in-house, computer-based systems. They provide real-time visibility into production status, automate routine tasks, and help prevent common errors.
Modern systems can track inventory levels automatically, generate production schedules automatically according to deadlines and resource availability, and provide early warnings about potential problems. They also make it easier to analyze historical data and identify trends that can improve future planning.
However, the concerns of small manufacturers are legitimate. Depending on the software, initial costs can be significant, including not just software and hardware but also training and potential production disruptions during implementation.
Integration with existing systems often presents technical challenges, and staff may resist changing familiar processes.
A practical approach to modernization starts small and scales gradually. Companies might begin with a single aspect of production management, such as inventory tracking or scheduling, and expand as they see results. This approach allows organizations to:
- Manage costs by spreading investments over time
- Train staff gradually without overwhelming them
- Test and refine processes before full implementation
- Build confidence through early successes
The key is choosing solutions that fit your operation’s size and complexity while providing room for growth. Modern cloud-based systems often offer the flexibility to start with basic features and add capabilities as needed, making them particularly suitable for smaller manufacturers looking to modernize gradually.
The future of production order management
The future of production order management is shaping up to be both exciting and practical. New technologies are making previously complex processes more accessible to manufacturers of all sizes.
Artificial Intelligence, for example, is moving beyond basic automation to help predict maintenance needs, optimize production schedules, and even suggest improvements to workflow patterns and production processes based on historical data.
The industrial internet of things (IIoT) is transforming how we track and manage production orders, with smart sensors providing real-time data about everything from machine performance to inventory levels. This increased connectivity means manufacturers can spot and resolve issues faster than ever, often before they impact production.
Integration capabilities continue to expand, allowing production order systems to work seamlessly with other business tools. Cloud-based platforms are making these advanced features more affordable and accessible, especially for smaller manufacturers.
The trend is clear: production order management is becoming more intelligent, connected, and user-friendly.
Looking ahead, the focus will be on systems that can grow and adapt with your business. The goal isn’t just automation for automation’s sake. It’s creating smarter, more efficient operations that help manufacturers stay competitive while maintaining quality and reliability.
Production order management comes down to this
Efficient production order management is essential for manufacturing success in today’s competitive marketplace. Whether you’re using traditional methods or considering a move to digital cloud-based solutions, the key is finding an approach that fits your operation’s unique needs while providing room for growth.
When evaluating production order management solutions, focus on these key factors:
- Look for systems that offer free trials or demonstrations – this hands-on experience is crucial for determining if a solution truly fits your needs
- Ensure robust technical support is available, particularly during the initial setup and training period
- Verify the system can scale with your business, adding features and users as you grow
- Check that the solution integrates with your existing business tools
- Confirm that training resources are readily available for your team
- Helpful planning templates can help you shortcut the production schedule process
Long-term considerations paint a clear picture of what’s at stake. Manufacturers who successfully implement cloud-based production order systems often see significant improvements in efficiency, with reduced errors, better inventory control, and improved customer satisfaction.
Many report being able to take on more complex orders and larger clients that were previously out of reach.
On the flip side, those who stick with outdated systems may find themselves increasingly at a disadvantage. Manual errors, communication gaps, and inefficient processes can lead to lost opportunities and declining competitiveness.
As more manufacturers embrace digital cloud-based solutions, those who don’t risk falling behind in both efficiency and capability.
The future belongs to manufacturers who can adapt and grow. The good news is that with today’s scalable, cloud-based solutions, taking that first step toward modernization of your production orders doesn’t have to be overwhelming or cost-prohibitive.
It just might be the easiest and simplest way to safeguard your bottom line.
Key takeaways
- Production orders are essential for turning customer demands or inventory needs into actionable manufacturing instructions, ensuring smooth operations.
- There are various types of production orders, including Make-to-Stock (MTS), Make-to-Order (MTO), Assemble-to-Order (ATO), and Engineer-to-Order (ETO), each suited to different manufacturing workflows.
- Efficient production order management relies on accurate demand forecasting, real-time monitoring, and effective communication between departments.
- Modern cloud-based production order systems enhance accuracy, streamline workflows, and provide real-time insights, making them indispensable for competitive manufacturing.
- Gradual modernization of production order management allows manufacturers to balance costs, train staff, and adapt processes without disrupting operations.
Frequently asked questions (FAQ)
Start by identifying pain points in your current system, such as delays or errors. Implement a small-scale digital solution like inventory tracking or scheduling software, then gradually expand to more advanced features. Ensure staff training and data migration are part of the process.
Many cloud-based systems are affordable even to microcompanies. Look for free trials, starter packages, or open-source solutions to minimize initial costs and test functionality before committing.
Frequent delays, inventory shortages or excesses, communication gaps, and quality control issues are common indicators. If these problems persist despite manual efforts, it’s time to explore more efficient, automated solutions.
You may also like: What is Production Downtime?