What is Production Downtime? Key Terms Explained
Unplanned downtime is more than just lost production–it’s a race against time to stop excessive damage to a company. This post explores downtime in manufacturing, ways of mitigating it, and the crucial difference between unplanned and planned downtime.
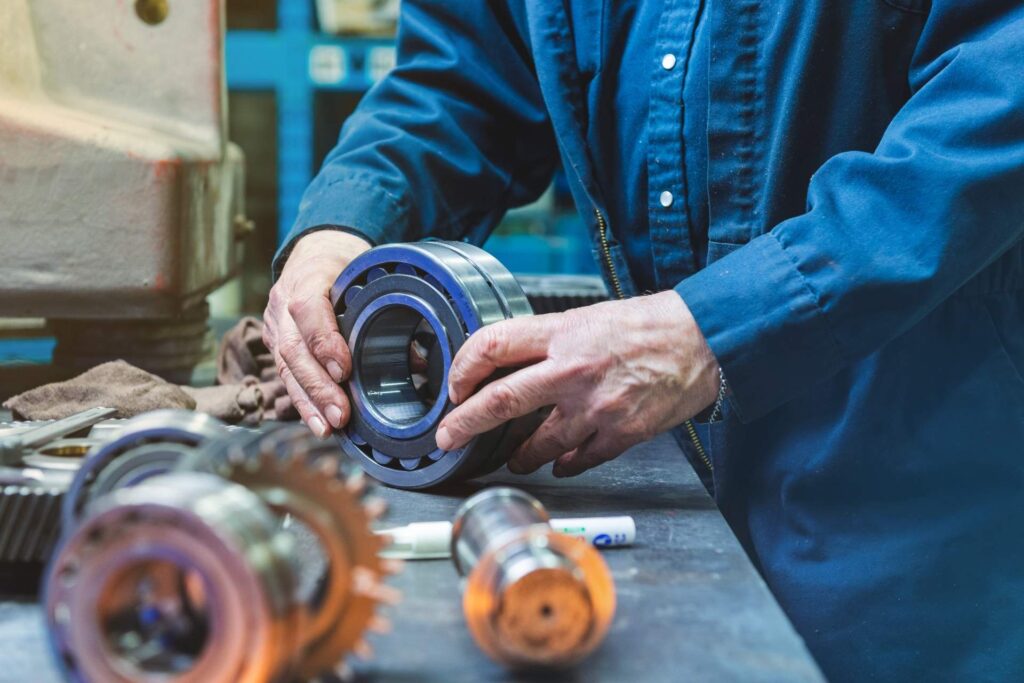
What is production downtime?
Production downtime refers to any period in time during which a manufacturing process is halted, causing a disruption in the normal flow of operations. Downtime can occur due to many reasons, from equipment failures or employee strikes to scheduled maintenance or supply chain disruptions. Regardless of the cause, downtime hinders meeting production goals, thereby threatening customer satisfaction rates and profitability.
Broadly speaking, downtime can be categorized into two types–unplanned and planned downtime. Unplanned downtime is the unexpected and often costly halting of production caused by equipment failures or other unforeseen issues. Planned downtime, conversely, is a proactive and intentional pause in production, scheduled to allow for maintenance or upgrades.
Let’s look at these two in some more detail.
Unplanned downtime is the costly sound of silence
Simply put, unplanned downtime is any unexpected or unscheduled stop in production that affects or disrupts normal operation. For a small- to mid-size manufacturer (usually between 10-200 employees), the costs associated with downtime could easily become crippling, eating deeply into a company’s bottom line.
The direct costs of unplanned downtime
For a small manufacturer, the average cost in lost production time averages between $1,000 and $3,000 per hour. For mid-sized companies with 50 to 200 employees, that cost rises to between $4,000 and $10,000.
Using the mid-size manufacturer’s potential direct downtime costs, if it happens 20-30 times a month, downtime can take a staggering chunk of change out of profits to the tune of $80,000-300,000.
Besides machine repair costs, there are other factors to consider because of the machine failure. Emergency maintenance and repairs often run 3 to 5 times the planned maintenance cost. If parts aren’t on the parts room shelves, rush shipping of replacements must be added in.
Then, there are the labor costs involved. Each production team member standing around doing nothing is still earning an hourly wage. Additionally, the lost production output needs to be made up, often incurring overtime wages. Overtime is normally charged at 1.5 times the regular hourly wage. Consequently, the labor cost for each item just went up.
In short, unplanned downtime expenses can generate a huge bill that affects the company’s cost per unit and contributes to a lower OEE (overall equipment effectiveness) score.
Indirect costs of unplanned downtime
First, there may be quality control issues during a restart of production. Repairs may have changed the alignment and other measurements used for precise control. This often means the first parts made or products processed are not up to the proper specifications or within acceptable parameters.
So, off to the waste pile they go.
Manufacturing productivity may also be thrown off schedule enough that there’s the potential for missed deadlines and possible associated penalties. This raises the possibility of customer dissatisfaction, canceled orders, and even loss of crucial business contracts.
Unplanned equipment failures cost so much because the immediate “fix” is reactive maintenance. It’s a knee-jerk reaction to a problem that shouldn’t have happened.
Following any major unplanned downtime, management should perform a root cause analysis of the breakdown. A proper downtime analysis will start to unearth the reasons how and why there was an equipment failure. All findings should be documented, with close attention to the causes and tracked by machine.
In fact, every machine should have an ongoing paper trail that tracks its operational and output efficiency. A downtime history of each machine can include the KPIs (key performance indicators) that determine if a machine should be replaced rather than constantly repaired.
The real key to avoiding and reducing downtime events is to adopt a proactive approach to equipment maintenance. This reduces the amount of unexpected downtime and promotes a lean manufacturing process.
Planned downtime is the sound of operational efficiency
The flip side of the machine maintenance coin is planned downtime. Unlike unplanned and unscheduled downtime, planned downtime is scheduled for and even budgeted, and it’s a part of the normal manufacturing process.
It’s a hard fact of manufacturing life that any machine—even all machines—will eventually show signs of wear and tear. Enter planned downtime and proactive maintenance.
There are two main types of proactive downtime maintenance: preventive and predictive. While these share similar characteristics, certain aspects set them apart.
However, the main goal of each is to avoid unplanned downtime and keep factories and processing plants running at optimal operating efficiency. This goal is achieved by using a planned, well-thought-out maintenance schedule.
Software programs, computer-generated scheduling, and even AI (artificial intelligence) play an increasingly important role in maintenance management.
Preventive maintenance is crucial to eliminating production downtime
Let’s start with a little downtime history.
Before the 1950s, manufacturing maintenance was purely reactive, following the simple principle: “If it ain’t broke, don’t fix it.” This approach worked because machinery was straightforward and most assembly was done by hand.
The industry saw its first major shift in 1901 when Ransom Olds introduced the assembly line, where workers at fixed stations assembled cars as they were pushed from station to station. As we know, Henry Ford revolutionized this concept in 1913 with his conveyor belt system, inspired by meat processing plants. Workers specialized in single tasks, dramatically improving efficiency, though maintenance remained reactive.
The post-war manufacturing boom of the 1950s finally transformed maintenance philosophy. As production machinery became more complex, preventive maintenance emerged to reduce equipment failure and unplanned downtime. The industry shifted from “don’t fix it if it ain’t broke” to “fix it before it breaks,” establishing the foundation for modern maintenance practices.
This ushered in the concept of preventive maintenance, sometimes called preventative maintenance.
Planned downtime for preventive maintenance was worked into the production schedule. In fact, manufacturing resource planning (MRP) software soon baked planned maintenance right into the overall schedule development, including keeping an inventory of parts to keep on hand.
Planned downtime is often used for equipment changeovers and upgrades.
An important part of preventive maintenance is the concept of MTBF or “mean time between failure.” This was applied to all sorts of equipment parts, particularly those that enabled movement (bearings, gears, and similar parts) and eventually to electrical and electronic parts that had a limited lifetime or life expectancy.
So,, a major thrust of preventive maintenance is to replace those parts with an MTBF value before they break. That means replacements or even entire machine overhauls were planned for times when production wasn’t running. Weekends, holidays, and a daily dedicated maintenance shift allowed preventive maintenance tasks to be completed.
The result? Unplanned downtime decreased significantly.
But there’s a catch to a lot of preventive maintenance strategies. Parts are replaced before they fail… sometimes a long time before they fail. While waiting for a part to break down meant you got every ounce of “good” out of it, preventive repairs meant that you were leaving some money on the table from parts retired too early.
However, in the vast majority of cases, the money lost from replacing before failure more than made up for it in not losing money on unplanned downtime.
A trade-off, yes. But one that’s usually well worth it.
Predictive maintenance—just-in-time repairs and downtime tracking
Predictive maintenance—developed during the 1990s and early 2000s—uses a more data-driven methodology for scheduling maintenance repairs, thus driving down unplanned downtimes even more. It uses predictive analytics to help eliminate unexpected machine downtime and actually lowers the cost of downtime by allowing work to be done more efficiently.
While preventive maintenance was basically an educated guess, predictive maintenance uses a whole new set of parameters, techniques, and technologies. It can monitor your manufacturing equipment in real-time or as close as possible to it.
For example, one of the major causes of bearing-supported moving parts was and still is heat. The same goes for electrical and electronic components. One important technology developed, one that I’ve used a lot over my 36-year career as an industrial mechanic, is thermal imaging, also called thermography.
FLIR is an acronym for Forward Looking Infrared. When you point the device at an object, it senses heat and creates a color-coded image on a viewing screen. The different colors indicate the object’s temperature or parts thereof, usually compared to ambient temperature.
If you know the normal operating temperature of the component, you can see if it’s beginning to overheat, signaling impending failure. The component can then be scheduled for timely replacement or repair… just in time (often referred to as JIT).
Advanced predictive maintenance in the 21st century
Today, we are in the Industry 4.0+ era, and a whole new set of predictive maintenance technologies are available to enhance manufacturing operations. Specialized sensors attach to machine components that remain in place as 24/7 sentinels, ready to warn of impending failure from potential issues.
These sensors often connect to the facility’s network or maintenance cloud, inputting data directly into maintenance tracking and scheduling software through IoT (Internet of Things) connections. Each piece of equipment can be tracked in real-time, comparing its performance against a set of defined metrics and operational parameters.
AI coupled with Machine Learning facilitates smart maintenance scheduling, driving a computer maintenance management system or CMMS.
This all but eliminates human error in predictive maintenance. Additionally, when maintenance teams are able to perform predictive maintenance, the OEE is further improved. And that means the amount of downtime due to equipment failure causing production loss is minimized.
However, not all unexpected downtime is the result of equipment downtime.
You can’t dial out all unplanned downtime
But you can dial it down.
Throughout my 35+ years in manufacturing, I’ve witnessed every type of production downtime imaginable. From minor machine hiccups to devastating plant-wide shutdowns, these disruptions are an ongoing reality for manufacturing companies.
Here are a few additional common causes for downtime scenarios in the manufacturing industry.
Raw material shortages
Shortages halt production, increase costs through rush orders, and damage customer relationships through missed deadlines. These disruptions ripple through the supply chain, creating complex challenges to inventory management that affect the entire operation.
Modern technology provides effective solutions through real-time inventory tracking systems and advanced analytics for better forecasting. Supply Chain Management (SCM) software, integrated with enterprise resource planning (ERP) systems, enables comprehensive stock monitoring and management.
Bill of Materials (BOM) software further strengthens inventory control through automated reorder points, RFID integration, and precise material calculations based on production demands.
Success in preventing material shortages requires combining these technological tools with strategic planning, including maintaining multiple supplier relationships and developing clear contingency plans. This integrated approach helps manufacturers maintain consistent production while minimizing disruption risks.
Power outages
Power outages pose a constant risk to manufacturing facilities. They can occur from utility failures, electrical issues, or natural disasters. The impacts are immediate and severe. Production lines grind to a halt. Sensitive equipment may suffer damage. Production targets and deadlines slip away.
Manufacturers need a multi-layered defense against these risks:
- Start with a robust infrastructure.
- Install backup generators and uninterruptible power supplies (UPS).
- Perform regular load bank testing to verify system reliability.
- Develop clear power disruption protocols.
- Consider redundant power line contracts for extra protection.
Modern monitoring systems provide another critical layer of protection. Install both analog and digital software-enabled monitoring tools. These track power conditioning and load management. They can provide early warnings before issues escalate. High-performance industrial lighting systems offer additional resilience.
Together, these solutions help manufacturers maintain continuity through power disruptions.
Human error
Probably the hardest to mitigate, human error threatens manufacturing success daily. These mistakes range from incorrect machine operation to maintenance oversights. They can also include production process errors. The impacts are significant. Production lines experience delays or stoppages. Quality issues and waste increase. Safety risks emerge. Overall productivity and efficiency decline.
Here are a few tips to help mitigate human errors:
- Develop clear and unambiguous communication systems that strengthen the entire workflow.
- Deploy comprehensive training programs using digital work instructions. Digital training platforms help increase consistency in employee education.
- Install visual aids in multiple languages where needed.
- Create and maintain detailed standard operating procedures (SOPs).
- Strong accountability measures and regular skills assessments provide further layers of protection.
These tools and processes help manufacturers maintain quality while protecting their workforce.
Planned vs. unplanned production downtime—it’s up to you
Unplanned production downtime exists as reactive maintenance or costly disruptions. Planned downtime maintains equipment and improves processes. It enables thorough equipment inspection, critical updates, and process optimization.
Regular maintenance extends machine life and prevents future failures. It saves you hours of downtime that cut into your bottom line. Unplanned downtime, on the other hand, disrupts production uptime, costing thousands per hour.
Manufacturing Resource Planning software helps maximize scheduled downtime for maintenance while preventing unexpected breakdowns. This drives efficiency, reduces costs, and ensures reliable production. Strategic maintenance planning leads to higher productivity, better quality control, and significant long-term savings.
Key takeaways
- Production downtime is a disruption in manufacturing processes that can be caused by equipment failures, maintenance issues, supply chain issues, etc.
- Unplanned downtime is costly and disruptive. It occurs unexpectedly, leading to high repair expenses, lost productivity, and missed deadlines.
- Planned downtime is a proactive approach to efficiency. It is scheduled to allow for maintenance and upgrades, reducing the risk of unexpected production halts.
- Preventive maintenance reduces unplanned downtime. By replacing parts and servicing equipment before failure, it extends machine life and lowers the risk of disruptions.
- Predictive maintenance uses modern data-driven technologies to optimize repairs. Real-time monitoring and analytics help detect issues early, ensuring timely and efficient maintenance.
- Challenges to planning downtime include resource shortages and human error. Effective scheduling, proper training, and integrating modern tech solutions are crucial to overcoming these obstacles.
Frequently asked questions (FAQ)
Production downtime refers to any period during which manufacturing operations are halted. It can occur due to unplanned events, like equipment failures, or planned activities, such as maintenance or upgrades. Downtime impacts productivity, customer satisfaction, and profitability, making it a critical factor in manufacturing efficiency.
Yes, downtime is a key performance indicator (KPI) in manufacturing. It is often used to measure overall equipment effectiveness (OEE) and evaluate operational efficiency. Monitoring downtime helps identify problem areas and implement strategies to reduce disruptions.
To calculate production downtime, record the total duration of halted operations during a specific period. Divide this by the total available production time, then multiply by 100 to express it as a percentage. This metric helps manufacturers assess the efficiency of their processes and identify improvement opportunities.
You might also like: What Is Obsolete Inventory and How to Prevent It?