What Is a Production Cycle and How to Streamline It?
The production cycle is the engine behind every manufacturing business. Each stage in this cycle is crucial for maintaining efficiency. But how do you manage all these moving parts effectively? In this article, we’ll break down what a production cycle is, explore its key components, and share strategies for improving efficiency.
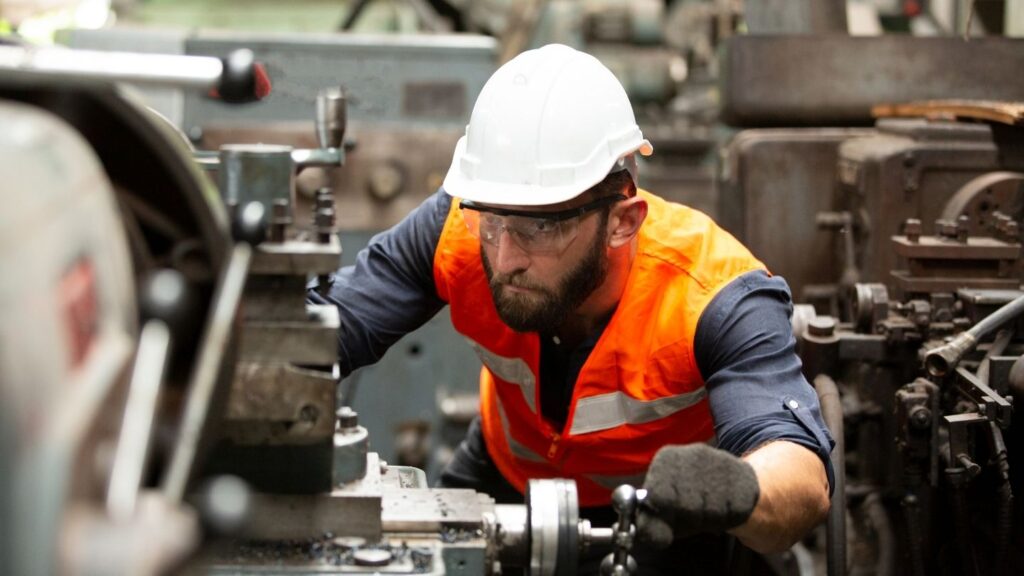
What is a production cycle?
A production cycle, in its simplest form, is the process of turning raw materials into finished products. It starts when the raw materials enter production and ends when the final product is completed and ready to ship or sell. In this definition, we only focus on the actual production process. We leave out things like product design, marketing, or anything that happens after production.
The production cycle is the part of the operation that directly affects how efficiently your resources (materials, labor, and machines) are used, how quickly products are completed, and how well a business meets its production goals. Since everything in manufacturing revolves around turning raw materials into products, the production cycle sits at the heart of these operations.
So, what exactly makes up the production cycle? We can break it down into four stages:
1. Material preparation
The production process begins with preparing materials or components for production. Whether sourced externally or produced internally, raw materials are prepped for manufacturing at this stage. This could involve basic steps like cleaning, cutting, or organizing. The goal is to ensure everything is ready for the actual production.
2. Processing
Once materials are prepared, they move into the processing phase. This is where materials are transformed, assembled, or shaped into components of the final product. Depending on the product being manufactured, this could everything from machining to mixing to sewing, or just simple assembly.
3. Quality control and inspection
After processing, inspectors check the product to confirm it meets the required standards. This step is crucial for catching manufacturing defects before finalizing the product. Inspectors may check at different stages of production, but it’s especially needed toward the end of the production cycle to confirm that the product is ready for the next stage.
4. Final product completion
The production cycle ends when the final product is complete and has passed all quality checks. At this point, products are ready for packaging, shipping, or storage, depending on what comes next in the business process. But as we’ve defined it, this stage marks the end of the production cycle itself.
In these four stages, we see how the production cycle influences how raw materials are turned into finished products. Each stage requires careful management to minimize delays, reduce waste, and meet production goals.
What processes support the production cycle?
Since the production cycle is the heart of manufacturing, let’s break down the key processes that keep production on track.
Raw materials acquisition and availability
Because the production cycle starts with raw materials, having them on hand or readily accessible is essential for keeping things moving. Whether they come from external suppliers or are produced internally, your priority is to make sure the materials and components you need are always ready when production starts.
If these materials aren’t available when you need them, everything gets delayed. This is why you must ensure proper materials management by working with reliable suppliers and keeping track of how much inventory you have on hand at all times. It’s important for you to have enough materials available to meet production demands without overstocking and wasting space and money. Maintaining a balance between what’s needed and what’s available is the secret to a smooth production cycle.
Labor scheduling and human resource management
Labor is another important part of the production cycle. It’s not just about having enough workers. It’s also about making sure the right people are available at the right time. If workers aren’t scheduled properly, production can get backed up, or you could end up paying too much for extra labor. Good scheduling keeps production on track and helps control labor costs.
Another reason to manage your employees’ time effectively is to prevent them from getting overworked or burned out. When workers are exhausted, they’re less efficient and more likely to make errors. This, of course, can slow down production and hurt overall quality. Over time, it can also lead to a higher employee turnover which will leave you short-staffed and needing to spend more on hiring and training replacements.
Machine maintenance, availability, and capacity
Machines are essential to production, and regular maintenance improves efficiency while preventing breakdowns that lead to delays and higher costs. A proactive maintenance plan is key to avoiding unexpected issues.
Machine availability must also be carefully scheduled to avoid overuse or idle time. Staggering machine use and having backup options can help prevent production bottlenecks. Additionally, knowing your equipment’s capacity ensures you match production needs without overloading or underutilizing resources, keeping the production cycle running smoothly.
How to plan production effectively?
Effective production planning is key to maintaining smooth operations and meeting customer demand. A well-organized plan helps avoid delays, reduce waste, and maximize the use of available resources. Here’s how to efficiently plan out production:
Forecast your demand and capacity
The first step in production planning is to know your production capacity. This means understanding how much can be produced within a given time frame, based on the availability of machines, labor, and materials. By comparing demand forecasts with capacity, you can adjust production plans to meet realistic goals.
Create production schedules
Once demand and capacity are clear, the next step is creating a production schedule. This involves deciding when and how production will take place. The schedule should account for all stages of production, from raw material preparation to final product completion, while also factoring in any maintenance windows or planned downtime for machines.
A well-structured schedule helps streamline production and prevents bottlenecks. But keep in mind that your schedule is also a living document. It can and should be adjusted as conditions change.
Coordinate materials and labor
For production to flow smoothly, materials and labor must be in sync. Coordinate raw material purchases with production timelines so the materials arrive on time and you avoid production delays. Your schedule must also match production needs, with the right number of workers assigned to the right tasks at the right times.
To achieve this, many manufacturers rely on tools like manufacturing ERP software, which helps automate and optimize the coordination of materials, labor, and machines.
By following these steps—forecasting demand and capacity, creating aligned schedules, and coordinating resources efficiently—businesses can plan production effectively and ensure that operations run smoothly.
How to monitor and improve production efficiency?
To monitor and improve production efficiency, start by tracking essential key performance indicators (KPIs), specifically those that highlight areas of improvement.
1. Define your KPIs. Here are the main KPIs to focus on in your production cycle:
- Overall Equipment Efficiency (OEE). Tracks machine utilization by accessing availability, performance, and quality.
- Cycle time. Measures the time it takes to complete a single unit or a batch in a specific workstation, e.g. lathing a component or mixing a batch of dough.
- Yield. Shows quality by indicating the proportion of units that meet standards.
- Unit cost. Calculates cost per unit to identify cost-saving opportunities.
- Capacity utilization. Evaluates resource use effectiveness. Higher capacity utilization indicates more efficient use of resources.
2. Implement real-time monitoring. Use real-time data tools, like manufacturing ERP systems, to monitor machine performance and downtime.
3. Conduct root cause analysis. Analyze bottlenecks and downtime causes to address core inefficiencies that might be slowing production. Regularly analyzing these factors helps pinpoint where improvements are needed.
4. Optimize scheduling and planning. Align production with demand forecasts to reduce idle time, overproduction, and resource waste.
5. Promote continuous improvement. Adopt methods like Kaizen, Lean, or Six Sigma. These approaches help reduce waste by making small, ongoing improvements to optimize your processes.
By following these steps and tracking KPIs, you can continuously improve production efficiency.
Streamlining the production cycle with manufacturing ERP
Manufacturing ERP or MRP software can automate various aspects of the production process. As a result, this software can help you manage your resources more efficiently and reduce downtime. Here’s a quick look at how this software can improve your production cycle:
Process standardization
Implementing MRP software pushes you to standardize and document your processes. This enables you to find the optimal way of doing things and setting this as the default. Having a concrete formula for processing items also sets the stage for performance analysis by allowing you to discover deviations from the standard.
Measuring production efficiency
Manufacturing ERP software collects data from across your operation and uses it to generate statistics and insights about your process efficiency. This enables you to pinpoint inefficiencies and other issues and figure out a way to fix them, ensuring continuous improvement in your operation.
Real-time monitoring and adjustments
MRP software helps you track the entire production process in real time. This way, you can make adjustments immediately. For example, if a machine breaks down or materials are delayed, you can use your MRP systems to quickly reschedule tasks as needed.
Efficient resource allocation
MRP software helps you allocate labor, materials, and machines more effectively. By automating scheduling and planning, you can align resources so that your equipment isn’t underused and your employees aren’t overworked.
Minimizing downtime with preventive maintenance
Some ERP systems give you the ability to implement preventive maintenance. By setting maintenance intervals based on pieces processed or hours worked, you can proactively maintain machinery and reduce the risk of unexpected breakdowns.
With MRP software, you can significantly reduce manual tasks, improve accuracy, and keep production running smoothly.
Key takeaways
- A production cycle is the process of transforming raw materials into finished products, broken down into four main stages: material preparation, processing, quality control, and final product completion.
- The main processes that support a healthy production cycle are materials management, capacity planning, and maintenance management.
- Monitoring KPIs such as Overall Equipment Efficiency and cycle time, alongside real-time data analysis, helps identify and resolve inefficiencies for continuous production improvement.
- Manufacturing ERP software increases efficiency through process standardization, real-time monitoring, resource optimization, and preventive maintenance, reducing manual tasks and downtime.
Frequently asked questions (FAQ)
The most critical KPIs depend on your specific production goals. Start with universal metrics like Overall Equipment Efficiency (OEE) for machine performance, cycle time for speed, and yield for quality, and then expand to others like unit cost or capacity utilization based on your unique operational needs.
ERP software can track machine usage and schedule maintenance based on metrics like hours worked or units produced. This proactive approach minimizes unexpected breakdowns and ensures machines run at optimal efficiency, reducing downtime and repair costs.
If demand exceeds capacity, consider strategies like optimizing schedules, adding shifts, or outsourcing parts of production temporarily. Long-term solutions may include investing in additional resources, such as machinery or workforce, to scale up production sustainably.
You may also like: Forward Scheduling vs. Backward Scheduling in Production Planning