Production Control – A Practical Guide
Production control is the collection of processes that manage and monitor the workflows involved in manufacturing a product. Robust production control practices and tools increase workplace efficiency, improve supply chain management, and reduce costs.
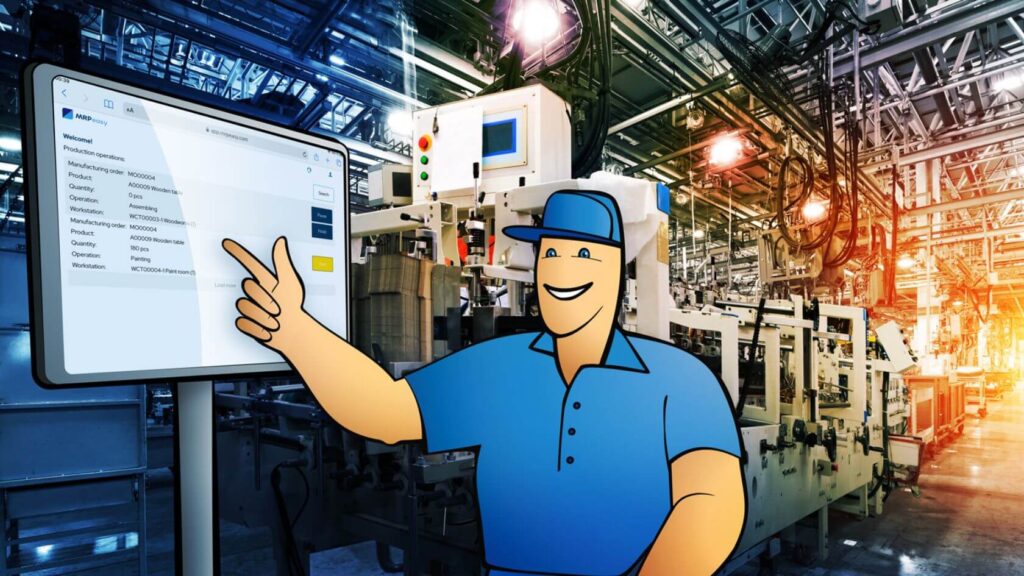
You can also listen to this article:
What is production control?
Production control is the collection of processes within manufacturing that manages, orchestrates, and monitors the flow of materials and activities in a production process. This may include demand planning, capacity planning, production scheduling, inventory management, costing, shop floor monitoring, quality control, and other production-related activities, but also providing customers with lead times and product statuses.
By effectively coordinating different stages of production, from raw materials to finished goods, production control ensures that manufacturing processes run smoothly, efficiently, and within the set timelines. Therefore, its importance cannot be overstated, as it directly impacts your operational performance.
Production control is an essential part of effective manufacturing operations management in companies of any size.
Why is production control important?
Production control plays a crucial role in manufacturing and is integral to the success of a business. Here is why it’s important:
- Optimizes production planning. Production control ensures that the planning of manufacturing operations aligns with the actual workflow. This alignment is vital for meeting set targets and maintaining efficiency.
- Increases production efficiency. Production control streamlines processes on the production line, reducing bottlenecks that can disrupt production operations.
- Improves supply chain management. By integrating procurement and supply chain processes, production control helps in managing resources effectively, preventing shortages, and ensuring that materials are available when needed.
- Facilitates accurate demand forecasting. Production control facilitates accurate demand forecasting by integrating real-time data from various stages of the manufacturing process, enabling a comprehensive understanding of current market trends and customer needs. This process ensures that production aligns with market demands, thereby reducing the risk of overproduction or shortages.
- Ensures product quality. By enforcing quality standards throughout the manufacturing process, production control guarantees that the finished product meets the desired quality criteria.
- Reduces production cost. Efficient production control minimizes waste and optimizes resource use, leading to lower production costs and better financial performance.
- Maintains delivery schedules. It plays a pivotal role in ensuring that manufacturing operations meet delivery dates, which is crucial for customer satisfaction and maintaining business reputation.
In summary, production control is vital for efficient and cost-effective manufacturing operations. It ensures that production processes run smoothly, product quality is maintained, and customer expectations are met, all while managing costs and resources effectively.
The state of production control in small businesses
Historically, manufacturing companies managed production manually using paper production schedules, calculations, and verbal instructions. Eventually, this gave way to spreadsheets and then to on-premises software designed to help specific functional areas complete their tasks more efficiently.
These systems grew out of the growing complexity of manufacturing at scale in high volumes. Small and medium enterprises (SMEs) could utilize equipment to rapidly produce goods. But the increasing speed of equipment meant that software was required to complete tasks that simple calculations and spreadsheets could not effectively control.
SMEs have traditionally been at a disadvantage to larger competitors. With old on-premises software or archaic spreadsheet-based analysis, SMEs could not deploy resources for proper production control, leading to waste and increased cost.
But to a new or scaling SME, production control is essential. It can drive process improvement, lower costs, and improve delivery. And today, SMEs can take advantage of production control systems that combine and simplify the siloed legacy systems their larger competitors struggled with for many years. Because they can leverage a unified software platform for production control, manufacturers can avoid the same mistakes and produce on par with larger companies.
8 steps of effective production control
The essential steps of production control in a manufacturing environment encompass a comprehensive process to ensure efficiency, quality, and timely delivery of products. These steps include:
- Production planning. This initial step involves setting production goals and creating a detailed plan to achieve them. It includes determining the production capacity, resource requirements, timelines, and production schedules.
- Routing. Production routing decides the workflow and sequence of operations within the production process. It outlines the path that a product takes from the beginning to the end of production, detailing the sequence of operations, the machines or work centers involved, and the methods to be used.
- Scheduling. This step involves assigning specific timelines for different stages of production. Production scheduling ensures that each task is completed within a set timeframe, optimizing the use of resources and aligning with delivery commitments.
- Dispatching. Dispatching is the execution phase where the planned work is authorized and released to the production floor. It includes issuing necessary instructions, documents, and materials to start the production process.
- Follow-up and monitoring. This crucial step involves tracking the progress of production against the plan. It includes monitoring the use of resources, workflow, and adherence to schedules. Any deviations or bottlenecks are identified for corrective action.
- Inspection and quality control. Quality control is integrated throughout the production process, with inspections at various stages to ensure that the product meets the set quality standards.
- Corrective action. When discrepancies or issues are identified, corrective measures are taken to realign the production process with the original plan. This may involve adjustments in scheduling, workflow, or resource allocation.
- Feedback and continuous improvement. The final step involves analyzing the completed production cycle to identify areas for improvement. Feedback is used to refine future production plans, increase efficiency, and improve product quality.
These steps, when effectively managed, ensure that production control contributes to the smooth operation of manufacturing processes, meeting both quality and delivery objectives.
Production control systems
Production control systems can be broadly divided into two large groups: push and pull systems. Let’s dive a bit deeper into what these terms actually mean:
- Push systems are based on demand forecasts, i.e. predicted future demand. In this case, manufacturing processes are started without waiting for actual customer orders. Products are therefore “pushed” through the supply chain regardless of immediate demand. This is also called make-to-stock (MTS) manufacturing as products are manufactured to stock, to be sold later.
- Pull systems, on the other hand, are driven by actual demand. In this case, the production process is initiated with a customer order. Products are therefore “pulled” through the supply chain by the customer. In a pull system, goods are manufactured as needed, which minimizes waste and reduces excess inventory along with the associated costs. Pull systems include make-to-order and assemble-to-order, configure-to-order, and engineer-to-order.
- Hybrid push-pull systems combine elements from both push and pull systems. Typically, the initial stages of production are initiated according to forecasts while the latter stages are triggered by actual demand. For example, a car manufacturer might produce standard components like engines, chassis, transmission systems, etc. according to a forecast while a customer order would trigger the final assembly where customizations are implemented. Therefore, a base product would be made to stock, and customizations added to the order.
The decision whether to manufacture using the push, pull, or push-pull system will be dictated by the product and its demand. Standard, fast-selling goods are usually produced using the push system while custom items are made using the pull method.
Production control techniques and tools for SMEs
There are many production control techniques that can be implemented in a growing manufacturing company without making huge investments. Here are some of the tried and tested options:
Kanban
Kanban is a lean manufacturing tool designed to improve efficiency and minimize waste in production processes. Originating from the Japanese word for “signboard” or “billboard,” Kanban uses visual signals—often cards—to represent work items in a production cycle. It is a pull system, meaning production is based on actual customer demand rather than forecasts.
In a typical Kanban system, a card is moved across a board or passed between teams as a product progresses through various stages of the manufacturing process, from planning to completion. The number of cards allowed at each stage is limited in order to reduce work-in-process inventory and bottlenecks. This visual nature of Kanban allows teams to track progress and quickly identify constraints or stock shortages. By only producing what is needed when it is needed, Kanban helps reduce excess inventory and improve workflow efficiency.
A simple example of Kanban would be when a card reaches the end of the supply chain (i.e. the product is dispatched to the customer) and is sent back to the start to trigger another production cycle. Another simple approach to Kanban is the two-bin system where two bins of an item are kept at the point of consumption. When a bin gets empty, it is sent to be replenished. This way, materials are fed into the system according to actual demand, preventing stockouts and overages.
CONWIP
CONWIP or Constant Work-in-Process is a Kanban-influenced technique where a set number of cards or tokens that each represent a single product are circulated through the process. When work on a product is finished, the token is sent back to the start, where it can be used to start work on another item or batch. When there are no tokens left at the starting point of the production process, no new production processes can be initiated.
Imagine a factory that produces electronics. Let’s say there are 50 CONWIP cards available for the entire production line. Each gadget that starts production takes one card from the start of the process. As the items move through various stages – from assembling components, to software installation, to quality checks – the card moves with them.
When a gadget is fully assembled and passes the final quality check, it is considered complete, and the associated card is returned to the start of the process. At this point, a new gadget can be started, taking the returned card. If all 50 cards are in use (i.e., there are 50 gadgets at various stages of production), no new gadgets can be started, preventing overloading of the production line.
Just-in-time (JIT)
Just-in-time (JIT) is a pull-type production management method wherein materials are ordered and goods are produced just in time for consumption or dispatch. This means suppliers are not delivering large quantities of parts to be stored in the plant’s warehouse; rather, they are delivering parts in sync with the production schedule.
This approach reduces the need for large storage spaces and extensive inventory management, thereby lowering holding costs. When implemented successfully, JIT can also lead to significant improvements in manufacturing efficiency, reduced waste, and a faster response to customer needs and market changes.
JIT requires precise coordination and strong relationships with suppliers, as well as a stable production process to be effective. The approach is best used with manufacturing software that supports backward scheduling, meaning that production activities can be scheduled backward in time starting from the planned delivery date.
For example, if a dealership orders cars from an automotive manufacturer that uses the JIT method, the manufacturer will start production at the last possible minute, delivering the cars just as they are finished, thereby preventing the accumulation of finished goods inventory.
Material Requirements Planning (MRP I)
Material Requirements Planning (MRP I) is one of the oldest software-based production planning and control methods, having been first developed in the 1950s. MRP integrates data from demand forecasts, inventory records, and bills of materials (BOM) to calculate quantities of materials and components needed, as well as the timings for ordering and receiving them.
As an example, imagine a company that manufactures bicycles. The company’s Master Production Schedule (MPS) might state that 500 bicycles are to be produced in the next month. Using MRP software, the production manager enters this demand into the system. The MRP then calculates how many of each component (as per the BOM) is required to make 500 bicycles, taking into account the inventory already in stock.
For instance, if the company already has 200 tires in inventory but needs 1000 tires for 500 bicycles (two per bicycle), the MRP system will recommend ordering 800 additional tires. It will also calculate when these orders need to be placed based on supplier lead times, ensuring that all materials arrive in time for production without creating excess inventory.
While traditionally, MRP I is a push-type system, it can also be used for material planning in pull systems. Any time a customer order comes in, material requirements and ordering times can be instantly calculated for that specific order.
Manufacturing Resource Planning (MRP II)
Manufacturing Resource Planning (MRP II) is an expansion of the basic MRP I system. While MRP I focuses primarily on materials and inventory control, MRP II includes additional components such as capacity planning, production scheduling and reporting, inventory and order tracking, quality control, and more. It therefore integrates all manufacturing functions into one system, providing companies with a complete overview of their operation. When a CRM and a financial module are added to the manufacturing resource planning capabilities, the software can also be called a manufacturing ERP system.
In a push system, MRP II can use the bills of materials, production routings, and the demand forecast or the master production schedule (MPS) to create highly accurate schedules for production and procurement.
In a pull system, it can instantly create and update schedules whenever a new order comes in, enabling manufacturers to provide their customers with accurate lead time and cost estimates in just a few clicks.
Regardless of the production system type, MRP II or manufacturing ERP enables manufacturing companies to achieve end-to-end traceability, monitor production efficiency, track order progress and inventory levels, set inventory reorder points, perform financial analysis, and much more to put the company on a path of continuous improvement and sustainable growth.
Key takeaways
- Production control is the process of managing the flow of materials and activities in manufacturing, affecting everything from demand planning to quality control.
- It ensures workflow efficiency and adherence to production plans and schedules, reducing costs and enabling companies to meet production targets and achieve timely deliveries.
- Integrating procurement and supply chain processes, production control effectively manages resources and prevents shortages and the accumulation of excess inventory.
- By integrating real-time data, production control aids in accurate demand forecasting, aligning production with market demands.
- Robust production control practices also enforce quality standards throughout the manufacturing process, ensuring high product quality.
- Small and medium enterprises can leverage modern production control systems such as MRP or manufacturing ERP software for process improvement and cost reduction, enabling them to compete effectively with larger companies.
Frequently asked questions
Production control refers to the process of managing, orchestrating, and monitoring the flow of materials and activities in a manufacturing setting to ensure efficient production operations.
The steps in production control typically include production planning, routing, scheduling, dispatching, follow-up and monitoring, inspection and quality control, corrective action, and feedback for continuous improvement.
The main objective of production control is to ensure that manufacturing processes run efficiently and effectively, meeting set quality standards and delivery schedules while optimizing resource utilization and minimizing production costs.
You may also like: Stock Control – A Simple Guide for SMEs