What Is Production Capacity and How to Calculate It?
Production capacity is an essential metric for any manufacturer planning their production. Knowing it helps to provide customers with more accurate lead times and can be a great aid in forecasting cash flow. In this post, we look at what production capacity is and explore different ways how to calculate it.
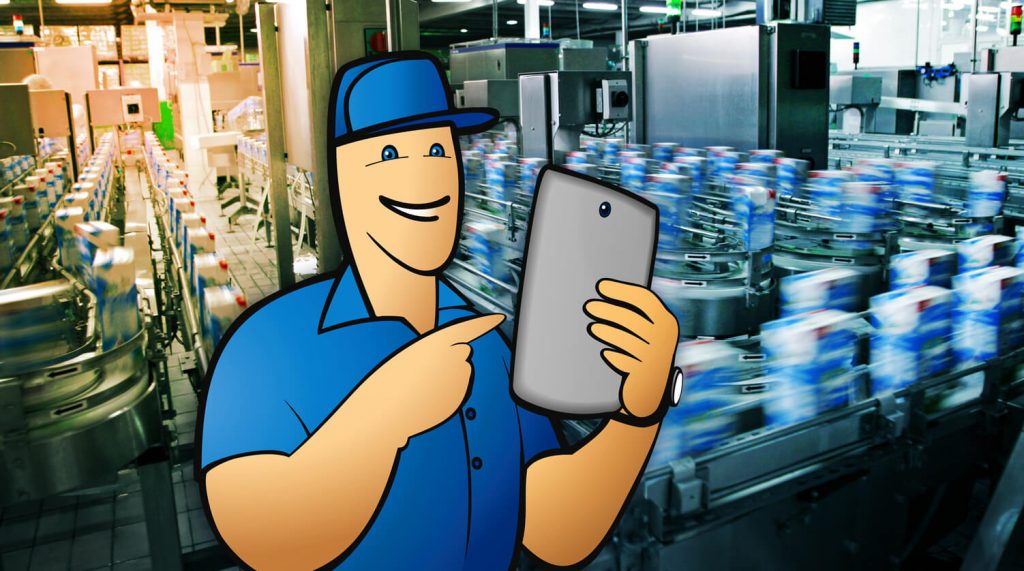
What is Production Capacity?
Production capacity is the maximum output of a production facility, measured in finished products over a given period of time. It shows the potential output i.e., the theoretical upper limit of goods able to be produced with installed machines, labor, and resources.
Knowing the production capacity as precisely as possible is essential for a number of reasons:
- Manufacturers are expected to be able to quote accurate lead times. Settling for rough estimates simply translates into less customer satisfaction in the long run.
- Accurate insight into production capacity enables an overall more informed production scheduling process which simplifies decision-making and alleviates uncertainty toward meeting customer demand.
- Comparing production capacity with actual capacity for past periods enables measuring the capacity utilization rate, useful for gauging the efficiency of manufacturing processes and finding a balance between operation rate and cost per unit.
- A reliable production capacity metric is a good indicator of performance, and is useful, for example, to motivate workers to create and meet production goals.
There are different ways of calculating production capacity. In this post, we will explore the basic methods of approximating production capacity from the actual output and calculating single and multiple-item production capacities using machine hours and throughput time. We also look at how production planning software can largely automate this process and enable accurate, data-based capacity planning.
How to calculate production capacity?
There are several different ways of determining production capacity. Next, let’s look at the manual ways of calculating it.
Finding the actual output
Finding the actual output for a past period is as simple as counting the number of finished goods for a desired time period like an hour, day, week, etc. The results for different periods can then be summed and divided by the number of time periods to arrive at the average output capacity for longer timeframes.
While this is a reliable way of estimating actual output, it doesn’t accurately depict production capacity. It only takes into account demonstrated capacity and doesn’t factor in changes to workstations, labor hours, laborer skills, supply fluctuations, etc. This means that there is no guarantee the actual output for an upcoming period will match the historical output value. Still, the method provides a baseline that can be useful for approximating production capacities for stable make-to-stock workflows producing a simple product mix with very reliable demand.
Manually calculating production capacity
Calculating production capacity is a bit more tricky. It requires two key metrics – the machine-hour capacity and throughput time.
- Machine-hour capacity refers to the total amount of time that available laborers can work on available machines necessary to create a product. This metric is calculated separately for every single product or single process by multiplying the number of available machines by the hours that employees can utilize them.
Machine-hour capacity = number of usable machines x number of working hours
- Throughput time is the total measured amount of time that a product takes to be processed on a manufacturing line. In other words, it’s the part of a product’s overall production time – the total amount of time it takes to convert an incoming order to a finished sale – that a product spends being processed. If production capacity is measured per individual manufacturing process, this would be referred to as cycle time. Cycle time is the time it takes a workstation to complete one step in a product’s routing.
Dividing the above metrics enables calculating the basic production capacity for a single product:
Single item production capacity = machine-hour capacity / throughput time
For example, if a soda producer has 5 canning machines available and employees work 8-hour shifts, the machine-hour capacity for the cannery is 5 x 8 = 40. It takes 6 seconds to process one can of soda. Knowing this, we can calculate the production capacity for the canning process. Let’s normalize both to minutes to simplify the calculation: 40 hours is 2400 minutes, and 6 seconds is 0.1 minutes. Production capacity for the canning process is therefore 2400 divided by 0.1 which equals 24000 cans per 8-hour shift for all 5 canning machines.
Production capacity for multiple items
The above calculation returns the production capacity for one type of product or a single process. Most plants produce more than one product, however. To find the production capacity of multiple products, each product’s order size is multiplied by its throughput time. The results are then summed for different products, and then divided by the plant’s available machine-hour capacity:
Multiple-item production capacity = ((amount of product A x throughput of product A) + (amount of product B x throughput of product B)) / machine-hour capacity
Continuing with the above example, let’s presume our soda canner needs to fill two orders – 12000 cans of soda and 8000 cans of beer. The throughput time of canning soda is 6 seconds and 9 seconds for beer. Not counting changeover times and other constraints, the multiple-item production capacity for the workload in minutes would be (12000 x 0.1) + (8000 x 0.15) = 1200 + 1200 = 2400 minutes, or 40 machine-hours. We already know that the machine-hour capacity of the cannery is 2400 minutes a week. In other words, the plant can fill both of the orders in 1 work week in ideal circumstances with installed capacity.
Finding the capacity utilization rate
Once both production capacity and actual output are measured, calculating another important manufacturing KPI – the capacity utilization rate is possible. This KPI shows how much of a company’s installed production capacity is being utilized, or in other words, what percentage of maximum capacity the manufacturing process is operating at.
The capacity utilization rate is calculated by dividing the actual capacity by the production capacity and multiplying the result by 100 to obtain a percentage.
Capacity utilization = (Actual output level / Production capacity) x 100%
The capacity utilization rate is great for assessing the production plant’s operational efficiency and the costs and pricing of products. Generally, a capacity utilization rate of around 85% is considered optimal – a higher rate can lead to diminished returns due to accelerated workstation depreciation or the inability to respond to sudden demand surges. Generally, the higher the capacity utilization rate, the lower the cost per unit, and the greater the profit margin.
Production capacity planning considerations
To get a more realistic idea of available capacities that consider more constraints and externalities, and especially if a company produces a mix of goods, a more comprehensive approach to production capacity planning is needed.
Practically speaking, the more constraints it is possible to account for, the more accurate the production capacity metric will be, which will allow for more precise production planning and scheduling. Examples of constraints include changeover and downtimes, worker leave and holidays, space and transportation, and any other bottlenecks that affect output.
To get a realistic overview of capacity, manufacturing needs to be broken down into the sequence of operations, workstation availability, setup times, material availability, supplier lead times, as well as any other details that may affect the schedule. Bearing in mind, that a typical plant needs to simultaneously handle multiple instances of these production processes for a number of different products.
What’s more, it’s also important to factor in the rate of efficiency of the manufacturing line. One way to do it is by measuring the Overall Equipment Effectiveness (OEE) KPI, which factors in the rate of defects, performance losses, etc., however, there are many other methods available.
Production capacity and capacity planning software
Suffice it to say, taking all of the above into account manually would be exceedingly difficult. This is why MRP systems and capacity planning software have been developed. These software solutions can corroborate and use all available information and constraints in order to calculate production capacities automatically and produce realistic schedules based on real manufacturing data. Whereas manual calculation might suffice to clarify short-term plans, this type of software also makes accurate long-term capacity planning possible.
Manufacturing software enables defining workstations and organizing them into groups, factoring in the individual productivity of each one along with working hours, holidays, and planned downtimes. Having a clear view of and access to all routings and consecutive processes, incoming orders and material availability, bottlenecks and scheduling conflicts or double-booking can all be mitigated on the fly.
All of this translates into better accuracy in planning and cost control, more flexibility to consider seasonality and other demand surges, far more accurate statistics and trends, and higher long-term production efficiency and predictability.
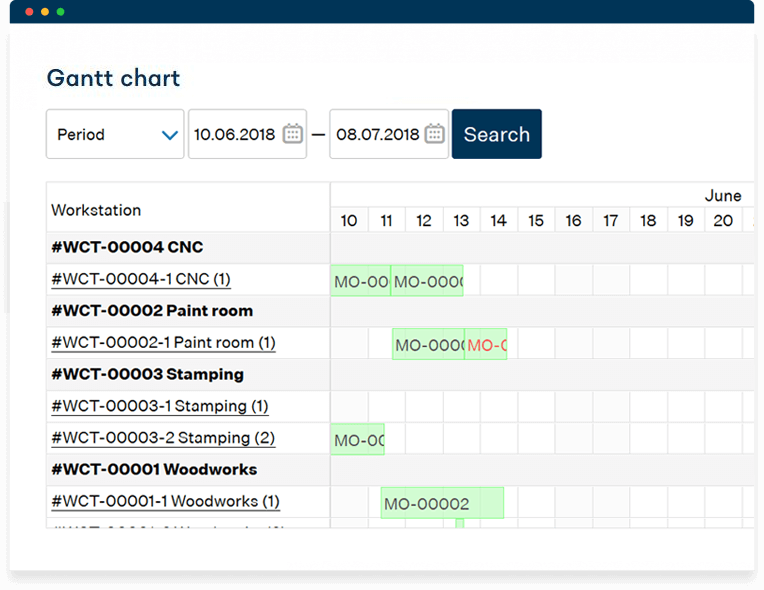
How to increase production capacity?
It comes as no surprise that production capacity can simply be raised by increasing the number of machines and adding more work shifts. However, this also entails added expenses and risks as new investors need to be brought on or short or long-term financing needs to be considered.
A credible alternative to the above is increasing production capacity by using existing resources. This is a plausible approach for almost any manufacturing company, save for ones that are already operating at peak performance.
Here are a few recommendations on how to increase production capacity without the need to expand the shop floor.
- Optimize your manufacturing methodology. E.g., use lean manufacturing principles to eliminate waste. the theory of constraints (TOC) to find and improve bottlenecks, single minute exchange of dies (SMED) to reduce changeover times, etc.
- Improve business processes and plan better. For example, start using just-in-time (JIT) to optimize production and reduce overheads, get a subcontractor to handle a sub-assembly, increase supply chain control by evaluating vendor capacities, etc.
- Adopt manufacturing software. Possibly the most cost-effective way to increase production capacity and optimize the plant, in the long run, is by adopting a capable production and inventory management software such as a manufacturing ERP system. While initial implementation requires investment, modern cloud-based solutions are increasingly affordable without sacrificing functionality.
As a short-term solution, increasing production capacity to meet a sudden demand surge can be achieved by:
- Adding or extending shifts, or having employees work overtime. This is plausible when the required work is manual or when machinery is not already used in full capacity.
- Outsourcing production. When the machinery is already working in full gear and cannot accommodate a capacity increase, outsourcing part of the workload can be a cost-effective means of meeting a sudden increase in demand.
Key takeaways
- Production capacity is the maximum possible output of a manufacturing business, measured in units of output per period.
- Knowing your production capacity enables better planning and scheduling of production, giving more accurate lead times, calculating the capacity utilization rate, gauging operational efficiency, and other benefits.
- Production capacity can be found by looking at the average outputs for past time periods, calculated manually using machine-hour capacity and throughput time or through manufacturing capacity planning software.
- Production capacity can be increased in the long run by adopting lean manufacturing principles, adopting better business processes, and automating production management via software, or temporarily by adding extra shifts or outsourcing production.
- Using an ERP/MRP system for capacity management allows companies to plan their production more accurately and efficiently, and make better decisions thanks to better data analysis and insights.
Frequently asked questions
A basic way to find out the production capacity is by multiplying the number of available workstation capacity by the available time in a work shift. For example, if a machine’s design capacity is 10 units in an hour and the work shift is 8 hours, the production capacity for the machine is 80 units per shift.
There are multiple ways of calculating production capacity. The easiest method is to measure the actual output of units for past time periods and corroborate an average production capacity based on that. A more advanced method is to calculate the machine-hour capacity of the plant and divide it by the throughput time of a product. The most precise way, however, is by adopting capacity planning software which takes into account manufacturing constraints and routings and calculates capacity based on real-world manufacturing data.
A high production capacity simply indicates that the manufacturing operation is theoretically capable of outputting a large number of products in a given time. If production capacity is divided by the actual measured output and multiplied by 100, the resulting capacity utilization rate allows for gauging the efficiency at which the plant is operating compared to its maximum potential capacity.
Read more about Capacity Planning in Manufacturing ERP.