How to Manage Product Variants in Manufacturing?
Product variants are versions of products with variations in attributes such as color, size, material, features, pricing, etc. Even though selling a product with variants is quite clear-cut, managing their production can be a real headache.
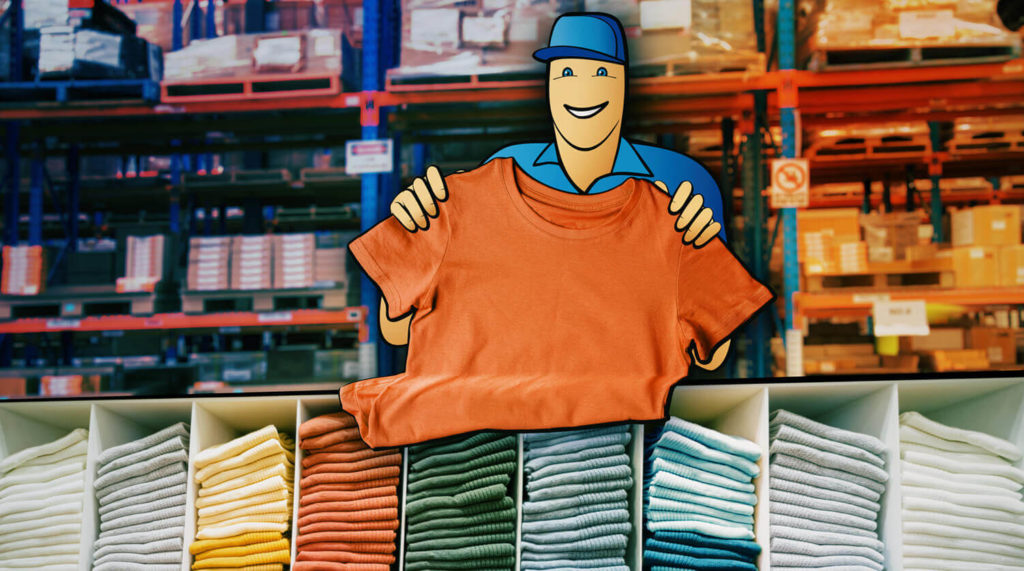
You can also listen to this article:
What are product variants?
Product variants are different versions or variations of a product that are offered for sale by a company. They are essentially configurations of the same product that are tailored to meet the needs of different customers or markets.
For example, a clothing company may offer a t-shirt in different sizes, different colors, and designs. A computer company may offer a laptop with different configurations of memory, storage, and processing power. Or a furniture company may offer a table with different finishes. Each of those slightly different products constitutes a product variant.
Manufacturing product variants is becoming increasingly popular as companies look to become more customer-centric. In order to strike a balance between the personalization associated with custom manufacturing and the efficiency of mass production, may companies turn to mass customization.
Pros of offering product variants
Manufacturers may consider offering product variants for a variety of reasons. These include:
- Increased customer satisfaction. By offering product variations, manufacturers can cater to a wider range of customer needs and preferences. This can help them reach a larger audience and increase sales.
- Differentiation. Product variants can help manufacturers differentiate themselves from their competitors by offering unique features or customization options that others do not. This can help build brand loyalty and increase your market share.
- Increased profitability. Offering product variations can also be a way for manufacturers to increase profitability by charging a premium for specialized features or customization options.
- Supporting innovation. Product variants can also provide manufacturers with opportunities to test new product features or designs and gather customer feedback, which can inform future product development.
Cons of offering product variants
While offering product variants can have several benefits, there are also some potential disadvantages to consider:
- Increased complexity. Offering product variants can substantially increase production planning, procurement, and inventory management complexity as it requires you to track the demand for multiple new items, purchase new raw materials and manage the inventory of many new SKUs, as well as create highly complex production schedules. Inaccurate demand planning for the multiple variants can, however, lead to frequent stockouts and overstocking of both raw materials and finished products.
- Increased costs. Altering your processes to accommodate product variants also increases your costs across the board, starting from ordering, holding, and handling extra inventory and ending with increased production costs associated with longer planning processes, machinery setups, and changeovers. Distributors and retailers are mostly affected by increased ordering and inventory costs, as well as increased marketing costs.
- Brand dilution. Having too many product variants can dilute a brand and make it harder for customers to identify and connect with the company’s core offerings.
- Marketing and sales challenges. Marketing and selling multiple product variants can be more challenging than marketing a single, focused product line.
- Complexity for customers. Offering too many product variants can also make it more difficult for customers to choose between products, leading to decision paralysis or dissatisfaction with their purchase.
Therefore, while offering product variants can have many benefits, it is important for manufacturers to carefully consider the potential drawbacks and ensure that the pros outweigh the cons.
Managing product variants in e-commerce
If you are a manufacturer that sells directly to consumers, you can easily manage the sale of product variants within e-commerce platforms like Shopify, WooCommerce, BigCommerce, Amazon, etc.
These apps typically allow you to create a parent product with a number of variants, i.e. child products, and then create convenient ways for the customer to choose a suitable option. These include dropdown menus on the parent product page, filtering and sorting options in your product portfolio page, etc. New product variants can be created with ease, as can price lists in the case of variations that cost more than the standard product, e.g. a laptop with an upgraded battery costs more than the default one.
Managing product variants in manufacturing
Although e-commerce platforms such as Shopify or WooCommerce allow you to easily sell products with variations, their functionality is not nearly suited for inventory management, even less so for manufacturing planning.
Planning the production of uniform products is complex enough, with lots of moving parts playing a role in the process. Demand forecasting, material requirements calculations, supplier lead times, processing times, production capacity, and many other aspects have to be factored in when creating plans and schedules in a manufacturing company.
But if you decide to offer product variants, everything becomes many times more complex as now you have to account for all of the previously mentioned factors for all of the separate variants.
In addition, products with higher variability, e.g. custom assembly work, require product configuration functionality in order for you to efficiently manage the BOMs, production planning, and sale of the highly customized variants. And that is what e-commerce platform providers cannot offer. What many of them do offer, however, is integrations with third-party solutions that can handle manufacturing.
Managing product variants with ERP/MRP software
Functional manufacturing software is irreplaceable in the management of product variants, and manufacturing in general. And even though you may find spreadsheet templates online that promise to do anything you want, they cannot compete with dedicated software. Because beside simplifying the creation of variant BOMs, an ERP/MRP system helps you manage every vital aspect of your manufacturing process, from orders to production to fulfillment.
The complexity of product variant management is typically solved with matrix BOM functionality, also known as a bill of materials with parameters or a product configurator. This allows you to create a master bill of materials with various parameters that can be changed per order. For example, you can create a BOM for a wooden table with various possible finishes: oil, wax, polyurethane, etc.
In advanced MRP software, you can also set relations for your parameters, which can be used to automatically exclude or include parts or change the material quantities used in building the product. For example, the use of a specific circuit board could trigger the inclusion of a specific power supply.
Even though this functionality has traditionally been reserved for large enterprises with huge software budgets, MRPeasy makes it available to small manufacturers, and at a very affordable price.
Want to know more about how Matrix BOM works within an MRP software? Read this article or watch this video.
Benefits of using ERP/MRP software
An ERP/MRP system with matrix bill of materials functionality can be a powerful tool for managing the production of product families. In addition to helping you streamline BOM creation, these software systems have innumerable benefits, including:
- Quick and accurate quotes. MRP software can be used to automatically calculate the production costs and lead times for customer orders based on your production capacity, material availability and prices, supplier lead times, etc.
- Effective material requirements planning. MRP software uses the data available in the bills of materials to quickly calculate the quantities of materials required to fulfill an order.
- Automatic inventory booking and production scheduling. After an order is confirmed, the software automatically books the products required to fulfill the orders and schedules the production for missing items. Some solutions also allow you to schedule the production for the products to be completed just in time for delivery.
- Simplified inventory management. MRP systems allow you to track your inventory requirements and movements, set reorder points to trigger replenishments, identify obsolete and slow-moving inventory, and optimize your inventory levels to prevent stockouts and overstocking.
- Optimization of production efficiency. By monitoring production run times and comparing them to historical data, MRP systems help identify potential bottlenecks in the production process. In addition, properly implementing MRP software allows you to optimize your resource use and minimize the risk of bottleneck in itself.
- Product lifecycle management. A few MRP/ERP systems also have some product lifecycle management (PLM) functionality, including BOM version control that allows you to track changes in the bills of materials; workflow management that allows you to set up an approval system for certain activities; quality management for tracking inspection results; product returns and repairs management, etc.
- Elimination of data entry tasks. By automating many processes, an MRP system eliminates a huge amount of data entry tasks. For example, a barcode system within an MRP software allows you to simply scan a label to record an inventory movement instead of entering the product data manually.
- Enhanced reporting. MRP systems give you access to various reports and statistics that provide vital insights into efficiencies and inefficiencies across your operation.
Overall, an ERP/MRP system with advanced BOM software functionality can help streamline production processes for product variants, improve efficiency, and provide valuable insights into production and inventory management.
Key takeaways
- A product variant is a version of the same basic product, differing by attributes such as color, size, materials, features, pricing, etc.
- Companies might want to offer product variants to cater to the needs of a wider audience, to differentiate themselves from competition, to increase sales and profitability, and to test out new products.
- Manufacturing and selling product variants could, however, complicate many processes, including production planning, inventory management, and sales.
- E-commerce platforms offer a good amount of functionality for selling products with variations, but to manage the production and inventory of those products and the materials used in them, you will need a dedicated manufacturing software with matrix BOM functionality.
Frequently asked questions
A product variant is a version of a product with varying attributes such as color, size, material, features, or pricing.
Variant management is the process of managing and controlling the creation, development, and distribution of product variants.
To manage variants in manufacturing, you need to define the product variants, create a bill of materials, use a product configurator tool, and establish efficient production processes that can handle the different variants.
You may also like: What Is a Multi-Level Bom (Indented BOM)?