Procurement Planning – A Simple Guide
A thoroughly planned procurement process helps to ensure that a company’s purchases arrive in a timely manner and in the right quantities, from the best vendors and with good prices. A well thought out procurement plan helps businesses stay in control of the product manufacturing cycle and avoid last-minute surprises.
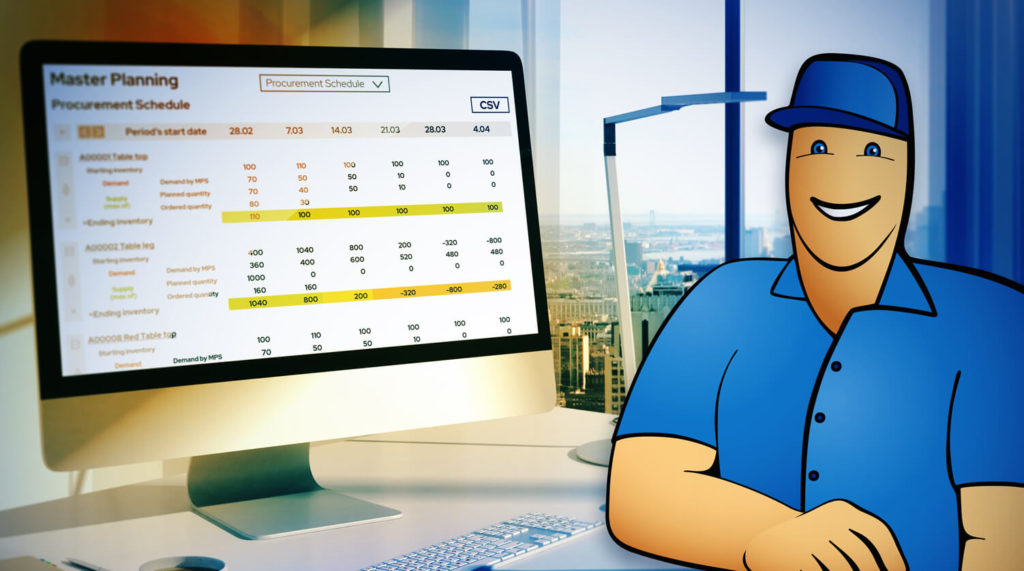
You can also listen to this article:
What is procurement planning?
Procurement planning is the process of determining the material requirements for producing goods for a set period of time as well as the means for their sourcing. It is a strategic business process aimed at gathering and consolidating business-critical information on all required purchases from outside vendors, including vendor applicability, cost and quality of materials, supply and payment schedules, compliance, contracting, etc. Procurement planning ensures that purchases are carried out in a timely and organized fashion.
Procurement may be more or less sophisticated depending on the scale and complexity of the supply chain and the manufacturing process of the product. For smaller or simple projects, it may not entail a lot of beforehand planning and can be assigned to the manager of the project. For more sophisticated production operations – where products are manufactured from a wide range of outsourced materials and have complex routing – it is usually a multi-department affair involving detailed planning and executive-level decision-making, headed by the procurement manager.
The procurement manager is tasked with coordinating the procurement process for a project or the whole manufacturing operation. Procurement responsibilities may be divided between departments or make up a separate department of a business. In either case, since it relies on a company’s manufacturing budget and is responsible for all outsourced materials, procurement planning implies close coordination between sales, manufacturing, accounting, and management. While it is technically possible to handle most procurement related processes with a pen-and-paper approach, modern manufacturing operations rely on ERP systems with dedicated procurement software that simplify, streamline and automate large parts of the procurement process.
What is a procurement management plan?
A procurement management plan is the central document detailing all purchasing-related information for a project, product, product line, or manufacturing period. The plan identifies the requirements necessary for fulfilling a manufacturing project or period along with strategic information on how best to go about procuring them. It includes analyses from previous procurement processes and demand forecasts, as well as a list of potential vendors and their expected performance, contracting and approval considerations, legal obligations, statements of work (or SOWs), requests for proposals (or RFPs), compliances, purchase schedules, expected supply times, bidding terms, and more.
If properly implemented, a procurement management plan aids in lowering overall procurement costs, ensuring the high quality of outsourced materials, and keeping the manufacturing operation flowing. Since the procurement process depends to a large degree on a company’s specific requirements, market, size, and activity, different companies may have very different process flows and there is no one right way to do it. Nevertheless, there are a number fundamental basics that should be included in creating the plan. Next, let us take a look at the core components of a procurement management plan.
Creating a procurement management plan
- Explain the process. This preliminary section of the document should clearly define the steps necessary to acquire products or services from suppliers, along with notes on how to manage the process.
- Define roles. Next, the members of the procurement team responsible for managing and implementing the procurement management plan should be listed along with their specific roles. This may include project managers who manage the timely execution of the plan, executives providing contractual advice, lawyers providing legal information, stakeholders involved in the project, etc.
- Specify item requirements. The plan needs to include all of the purchasable items needed for the project along with reasons for sourcing them externally. This includes both raw materials and components, as well as tools, equipment, software licenses, etc. It is important to include all project-specific information about each item as well as their detailed descriptions like technical specs, part numbers, quantities, expiration dates, etc. Stakeholders and executives need to be consulted and production managers coordinated with in this stage. Information on estimated costs and conformity with organizational standards should also be taken into consideration.
- Define the procurement timeline. To ensure timely execution of the project, avoid stoppages, and shorten lead times, the purchasing timeline needs to be aligned with the overall project schedule. The procurement timeline should list key dates for critical project processes, “needed by” dates for all procurable items together with their planned delivery times, etc. A well thought out purchasing timeline can help save a lot of time and money by planning for just-in-time delivery and better utilizing the supply chain pipeline.
- Select suppliers and define decision criteria. All applicable vendors together with analyses on their performances should be listed in the procurement plan. Prequalified vendors can be identified based on procurement history and new ones determined through market research and coordination with vendor representatives. Per-vendor pricing, availability of goods, expected delivery times, etc., should all be determined to aid with supplier selection. The decision-making processes on how to differentiate and choose vendors should also be determined. Vendor selections are then carried out. In case of a bidding process, agreements are drafted to determine bidding terms and RFPs detailing the project needs are issued that vendors can then respond to.
- Vendor management and accountability. Strategies and processes are put in place to manage the chosen vendors’ performance. Contracts are drafted, approved, and signed. Contractual obligations and specifics are also determined to make sure vendors carry out their side of the deal. This can include specifics on invoice processing, status reporting, etc.
- Risk identification and management. Any outsourcing introduces new risks to a company’s production operations. These can range from shipping delays and quality discrepancies of the delivered items, to financing issues from sudden market fluctuations, etc. The procurement management plan should detail the types of risks involved along with assessments on their probability and severity. Risk management practices should also be determined. These can include creating more detailed SOWs for vendors to pre-approve, finding alternate subcontractors in case a winning vendor experiences trouble, etc.
- Project constraints and legal limitations. Project constraints and limitations should be clearly defined and detailed in the procurement management plan. It is a good idea to keep these in mind throughout the procurement planning process and its various stages. These might include things like budget limits, legal obligations, compliances and standards, good manufacturing practices, etc.
- Review and approval. The procurement management plan should include information on the metrics used for reviewing and approving the procurement documents as well as methods and justifications for making changes once the procurement phase starts.
The importance of procurement planning
Effective procurement planning can greatly increase the efficiency of the whole manufacturing operation. Since it is responsible for the steady inflow of all outsourced raw materials, equipment and other project requirements, it can make the difference between constant disruptions and a smooth and streamlined manufacturing operation. Procurement planning is not only important to meet project needs, but also to improve upon internal work processes.
A well planned out procurement process can bring various improvements, including:
- Cutting costs. A well-planned procurement process provides thorough insight into the supply chain. This enables a better overview of available vendors as well as differences in raw material prices, delivery options, etc. In addition, similar requirements can be collected under one contract and bulk orders managed for multiple projects, maximizing cost savings.
- Improving production processes. With strategically planned purchases, required items arrive on time and in the right quantities. This helps keep the manufacturing process flowing, shortens lead times and avoids bottlenecks. It also reduces standing inventory and storage fees.
- Managing risks. Procurement risk management techniques like alternative vendor agreements or setting up backup delivery options mean reduced chances of delayed deliveries, sub-par quality of materials, and other supply chain issues. Deeper insight into compliances and industry standards also mitigates the chance of any legal issues.
- Increasing transparency and predictability. Procurement planning enables a better overview of project performance by comparing real-world activities and timelines with planned ones. This leads to better decision making and control over the project.
Procurement planning with ERP/MRP software
Like most other areas of business, procurement planning can be made much easier with the help of designated software. Although spreadsheets can be a terrific aid at the initial phases of doing business, companies that are looking to grow should consider implementing an ERP/MRP software that would act as a central platform for managing every aspect of the business. The flexibility of modern cloud-based systems ensures that the software remains affordable to even the smallest business but can scale as the business grows in capacity and complexity.
In terms of procurement planning functionality, a proper ERP/MRP system should support the following:
- Vendor management, including the tracking of vendor-related KPIs.
- Purchase order creation and PO tracking.
- Material requirements planning and procurement forecasting for determining what is needed and when.
- Inventory management, including tracking the materials, components, WIP, and finished goods.
- Statistics related to procured materials and components, for better decision-making.
- Critical on-hand lists and notifications for when inventory levels are low.
Additionally, an ERP/MRP system should cover sales, production planning and scheduling, and accounting functionalities. Integrations with third-party apps should offer advanced features for e-commerce, accounting, shipping and logistics, etc.
Key takeaways
- Procurement planning is the process of determining the material requirements for producing goods for a set period of time as well as the means for their sourcing.
- Responsible for all outsourced materials, procurement planning implies close coordination between sales, manufacturing, accounting, and management.
- Procurement management plans are the central documents that detail all purchasing related information for a specific project, product, product line, or manufacturing period.
- The procurement management plan identifies the requirements necessary for fulfilling a project or period along with strategic information on how best to go about procuring them.
- Modern manufacturing operations rely on ERP systems and dedicated procurement software that simplify, streamline and automate large parts of the procurement process.
You may also like: Procurement Management – A Quick Guide for Small Manufacturers