What Is Process Improvement and How to Implement It?
Process improvement in manufacturing is not just about tweaking a few procedures. It involves a holistic approach, integrating time-tested methodologies such as lean manufacturing, Six Sigma, and Kaizen, with cutting-edge solutions like manufacturing ERP software.
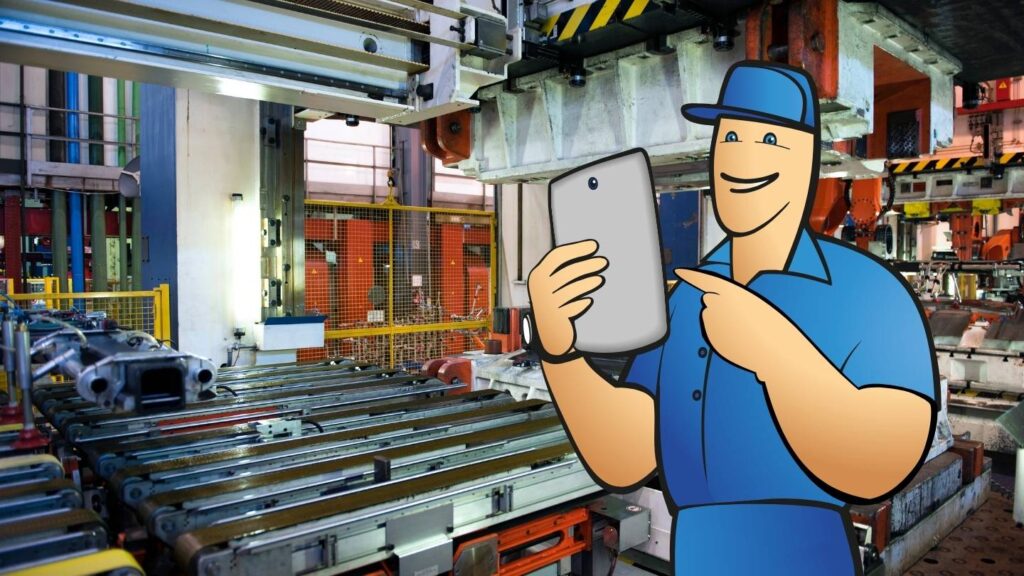
You can also listen to this article:
What is process improvement?
Process improvement refers to the systematic approach of identifying, analyzing, and enhancing existing business processes, especially in the manufacturing industry. The aim is to optimize operations, improve quality, and reduce costs by eliminating inefficiencies and errors. It is a continuous effort that supports an organization’s goals of maintaining competitiveness and satisfying evolving customer demands.
Why is process improvement important?
Process improvement stands out as a cornerstone strategy, enabling organizations to adapt, excel, and lead in their respective industries. Here is how process improvement affects business operations:
- Increasing operational efficiency. By scrutinizing and refining existing processes, businesses can reduce waste and optimize resource use by eliminating unnecessary steps, materials, and efforts, streamlining operations, all while speeding up production cycles and service delivery, and improving responsiveness to market demands.
- Increasing capacity. As processes improve and bottlenecks are eliminated, equipment utilization increases. Combined with an advanced ERP/MRP system, this “hidden capacity” helps produce more with existing equipment
- Boosting product quality and consistency. Process improvement directly influences product quality by standardizing operations, identifying and solving issues early on, and incorporating systematic quality control.
- Reducing costs across the board. Every small process improvement will eventually translate into a cost reduction. And each penny saved can be put into further improvements, creating a snowball effect of efficiency.
- Elevating customer satisfaction. At the heart of every business is its customers. Process improvement impacts customer satisfaction by reducing product defects, shortening lead times, and facilitating transparent communication.
- Fostering innovation and adaptability. Process improvement fosters the continuous reevaluation of processes and constant adaptation to emerging challenges.
- Improving employee morale and engagement. Process improvement also has a significant impact on the workforce by making jobs easier and more satisfying, creating a sense of ownership, and fostering constant training and development.
Therefore, process improvement is not just about tweaking the little things – in the end, it is all about improving the bigger picture.
Essential steps for effective process improvement
The journey of process improvement in manufacturing is a systematic one, involving several critical steps that pave the way for efficiency and excellence. Understanding and implementing these steps is crucial for any manufacturer looking to improve their operations.
- Assessing the current state. The first step is a comprehensive assessment of your current manufacturing processes. This involves identifying the strengths, weaknesses, opportunities, and threats within your operations. Using tools like value stream mapping can be incredibly helpful in visualizing the entire process flow, helping you pinpoint areas that require attention.
- Setting clear, achievable goals. Once the assessment is complete, it’s crucial to set specific, measurable, achievable, relevant, and time-bound (SMART) goals. These goals will serve as the guiding stars for your process improvement plan, ensuring that all efforts are aligned and focused.
- Selecting the right methodology. With goals in place, the next step is choosing the appropriate process improvement methodology that aligns with your objectives. Whether it’s Lean, Six Sigma, or Kaizen, each methodology offers unique tools and techniques to address different types of inefficiencies.
- Implementing changes. This stage involves putting the chosen methodology into action. It could mean reorganizing workflow, adopting new technologies, or changing certain operational procedures. The key is to start small with pilot programs or trials to test the effectiveness of these changes before a full-scale roll-out.
- Monitoring and adjusting. Continuous monitoring of the implemented changes is vital. This involves tracking key performance indicators (KPIs) and regularly reviewing processes to ensure they are meeting the set goals. Based on these insights, adjustments can be made to optimize the processes further.
- Sustaining improvements. Lastly, the focus shifts to sustaining the improvements made. This requires embedding the process changes into the company culture, through onboarding, continuous training, documentation, and establishing new standards and procedures.
Each of these steps plays a crucial role in the process improvement journey, offering a structured approach to achieving operational excellence in manufacturing.
Identifying areas for process improvement
The cornerstone of any successful process improvement initiative lies in accurately identifying areas riddled with inefficiencies and bottlenecks. This critical evaluation stage is where continuous improvement begins, setting the stage for a transformation that aligns closely with business goals and customer satisfaction.
Understanding the workflow and process mapping
A deep dive into the current process using tools like flowcharts and value stream mapping illuminates the path products take from raw materials to customer delivery. This visualization aids in pinpointing redundancies, unnecessary complexities, and bottlenecks that hinder the flow of operations and impact profitability.
Leveraging data-driven insights
A data-driven approach to identifying inefficiencies involves analyzing metrics and KPIs that reflect the health of existing processes. This quantitative analysis helps in understanding the variability in production and guides the decision-making process for implementing changes.
Engaging team members in continuous process improvement
Employee engagement in the improvement process is invaluable. Team members who are directly involved in the day-to-day operations often have insights into root causes of inefficiencies that may not be immediately apparent from a managerial viewpoint. Their contributions can lead to impactful improvement initiatives.
Customer-focused analysis
Ultimately, the goal of any manufacturing process is to meet or exceed customer expectations. Engaging with customer feedback provides direct insights into areas where the manufacturing process can be optimized to enhance the customer experience.
Common process improvement techniques and strategies
With a clear understanding of the areas needing improvement, the focus shifts to selecting and implementing the most suitable process improvement methodologies.
Lean manufacturing and Six Sigma
Lean manufacturing focuses on minimizing waste within manufacturing systems while maximizing productivity. It identifies non-value-added activities and eliminates them, streamlining operations to improve efficiency and reduce costs. Six Sigma, on the other hand, aims to reduce process variation and improve quality by identifying defects, understanding their causes, and implementing solutions based on data and statistical analysis.
Together, these methodologies create a powerful process improvement tool by combining Lean’s waste reduction and workflow optimization strategies with Six Sigma’s focus on quality and precision. This integrated approach leads to more efficient operations, higher quality products, and increased customer satisfaction, making it a powerful tool for businesses aiming to enhance their competitiveness and operational performance.
Theory of constraints
The theory of constraints is a management philosophy that identifies the single most limiting factor in a production system—referred to as a constraint—and systematically improves or eliminates this bottleneck. By focusing on the constraint, TOC seeks to manage workflow and resources to achieve the maximum system performance.
The principle is based on the understanding that any complex system can be substantially improved by concentrating on the weakest link. Implementing TOC involves identifying the constraint, exploiting it to its fullest, and then making iterative improvements to elevate the performance of the entire system.
Root cause analysis
Root cause analysis is a problem-solving method used to pinpoint the underlying cause of a problem or fault, rather than simply addressing its symptoms. RCA assumes that it is more effective to systematically prevent and solve underlying issues rather than just treating problems as they occur.
The process involves identifying the root causes of problems or events by using tools such as the 5 Whys, Fishbone diagrams, etc., and then developing appropriate solutions to prevent recurrence. It’s widely used in various industries to improve safety, quality, and efficiency by ensuring that corrective measures address the true origins of any issue, leading to more sustainable and long-term solutions.
Kaizen
The Japanese concept of Kaizen, which emphasizes small, continuous changes, fosters a culture where every employee, from stakeholders to line workers, is actively seeking ways to improve. Such activities not only streamline workflows but also boosts employee engagement and teamwork, potentially creating a positive feedback loop.
Total Quality Management (TQM) and PDCA cycle
TQM’s comprehensive view on organization-wide improvement, supported by the Plan-Do-Check-Act (PDCA) cycle, ensures that business process improvement projects are systematically executed and aligned with overall business objectives.
Total Quality Management is an extensive and structured approach to organizational management that seeks to improve the quality of products and services through ongoing refinements in response to continuous feedback. TQM requires the participation of all members of an organization in improving processes, products, services, and the culture in which they work. The principles of TQM focus on customer satisfaction, process improvement, and the involvement of employees at all levels.
The Plan-Do-Check-Act cycle is a four-step model for an effective continuous improvement process. It’s a foundational element in quality management frameworks, including TQM:
Plan: Identify a goal or problem, and develop a strategy for addressing it.
Do: Implement the plan on a small scale to test its effectiveness.
Check: Evaluate the results of the test to determine if the desired outcome was achieved.
Act: If the plan was successful, implement it on a wider scale. If not, refine the plan and begin the cycle again.
PDCA promotes a culture of continuous improvement where processes are constantly being assessed and refined. It provides a simple but effective framework for problem-solving and quality improvement, ensuring that organizations can adapt and respond to changes and challenges efficiently.
Process automation
Process automation involves using technology to automate complex business processes and functions beyond conventional data manipulation and record-keeping activities. It integrates software applications, machinery, and digital tools to perform tasks with minimal human intervention.
Process automation can range from simple tasks like auto-generating reports to complex operations such as robotic process automation (RPA) where bots mimic human actions to complete repetitive tasks.
By streamlining workflows with automation, businesses can achieve more consistent output, improve response times, and free up human resources for more strategic, creative, or complex problem-solving activities. This technology-driven approach supports scalability, improves accuracy, and can significantly reduce operational costs, making it a key component of digital transformation and process improvement strategies in organizations aiming for high efficiency and innovation.
Metrics and continuous monitoring
Establishing benchmarks and continuously monitoring performance through real-time data and KPIs ensure that improvement efforts are measured, evaluated, and refined over time. This ongoing process guarantees that the manufacturing operations remain aligned with evolving business goals and market demands.
The role of ERP and MRP in process improvement
Enterprise Resource Planning (ERP) and Manufacturing Resource Planning (MRP) software systems play a pivotal role in supporting process improvement efforts. By integrating various facets of operations, including production planning, material planning, purchasing, and production scheduling, these systems provide a unified platform that streamlines workflows, increases production efficiency, and facilitates effective project and business process management.
ERP/MRP systems improve production planning by offering real-time visibility into demand, inventory levels, and production capacity. This enables organizations to anticipate market changes and adjust production schedules accordingly, ensuring optimal inventory levels through low stock notifications and assisted reordering. The material planning and purchasing modules within these systems further augment process improvement by ensuring materials are ordered in time and in the right quantities, reducing waste and storage costs.
The automation of repetitive tasks, such as generating purchase orders or scheduling production, not only boosts production efficiency but also allows staff to focus on higher-value activities. This shift contributes significantly to process improvement efforts by fostering innovation and efficiency.
KPI monitoring is another critical feature of ERP/MRP systems, enabling businesses to track performance against their strategic goals. Metrics such as production lead times, cost per unit, and overall equipment effectiveness (OEE) are readily available, making it easier to identify areas for improvement. These systems can also facilitate cost and lead time estimations, with accurate estimations always just a few clicks away.
ERP/MRP systems offer a template for standardizing processes, which is essential for scaling operations and ensuring consistency across the organization. When a new process is introduced, the system can manage the transition smoothly, integrating the new procedure with existing workflows and minimizing disruption.
In summary, ERP/MRP software systems are indispensable tools for organizations aiming to optimize their production and business processes. Through enhanced scheduling, efficient resource management, and comprehensive KPI monitoring, these systems can support continuous improvement regardless of the methodology used, making them a cornerstone of modern process improvement efforts.
Key takeaways
- Process improvement is a continuous effort vital for maintaining competitiveness and meeting evolving customer demands. It involves increasing operational efficiency, boosting product quality, reducing costs, and elevating customer satisfaction through systematic analysis and enhancement of business processes.
- Effective process improvement in manufacturing requires a holistic approach, integrating methodologies like lean manufacturing, Six Sigma, and Kaizen with modern solutions like ERP software to optimize operations, improve quality, and reduce costs.
- The journey of process improvement involves critical steps such as assessing the current state, setting clear and achievable goals, selecting the right methodology, implementing changes, monitoring and adjusting, and sustaining improvements. This structured approach ensures operational excellence.
- Successful process improvement starts with accurately identifying areas of inefficiency and bottlenecks through techniques like workflow analysis, data-driven insights, employee engagement, and customer-focused analysis.
- ERP and MRP software systems are crucial in supporting process improvement efforts by providing real-time visibility into production planning, material planning, and scheduling, automating repetitive tasks, facilitating KPI monitoring, and standardizing processes for efficiency and innovation.
Frequently asked questions
Companies measure the effectiveness of process improvement methodologies by setting specific, measurable goals at the outset and then tracking relevant Key Performance Indicators (KPIs) over time. These KPIs might include metrics like reduced production times, lower defect rates, increased customer satisfaction scores, and cost savings, allowing organizations to quantitatively assess the impact of their initiatives.
Organizations often face challenges such as resistance to change from employees, the complexity of data migration, and aligning the new system with existing workflows. Organizations can overcome challenges in integrating new technologies like ERP/MRP systems by starting with a pilot program to iron out issues before full-scale implementation, seeking expert consultation or vendor support for training and customization, and engaging employees early in the process to ensure buy-in and smooth transition.
Small to medium-sized manufacturers can kickstart their process improvement efforts by leveraging cloud-based ERP software, which offers scalability, flexibility, and cost-efficiency without the need for heavy upfront investment in hardware. This allows them to access sophisticated tools for production planning, inventory management, and KPI monitoring, enabling them to make data-driven decisions and improvements even with limited resources. Starting with focused, impactful projects and gradually expanding their use of these systems can provide a solid foundation for ongoing process enhancement.
You may also like: The 8 Wastes of Lean Manufacturing