What is Poka-yoke and How To Use it in Manufacturing?
Efficiency and quality are paramount in manufacturing. Poka-yoke, a Japanese term meaning “mistake-proofing” is a fundamental approach to achieving both. In this article, we delve into what poka-yoke is, explore its principles, and provide practical tips on implementing it into manufacturing processes.
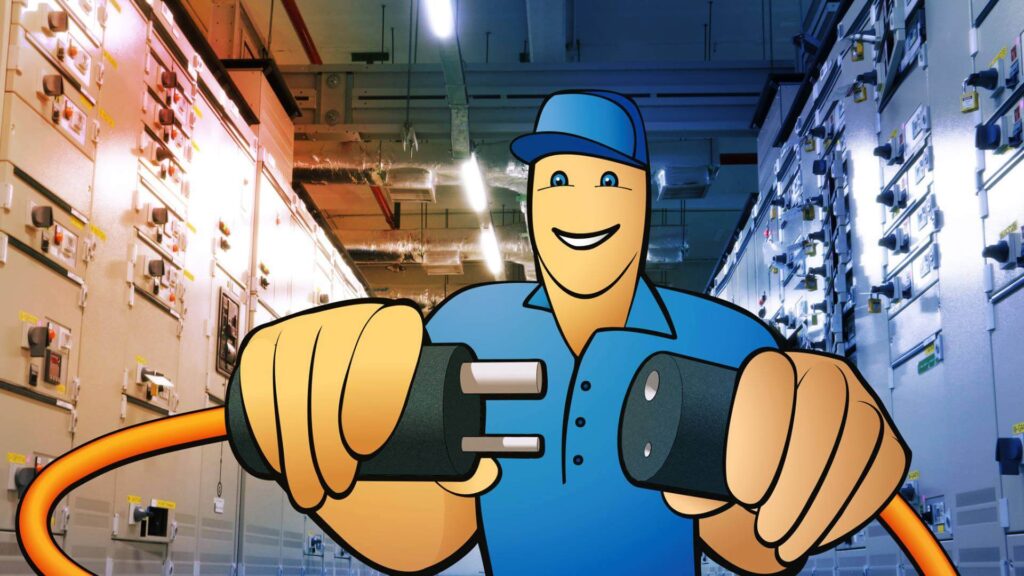
You can also listen to this article:
What is poka-yoke?
Poka-yoke is a quality assurance mechanism designed to prevent human error before it occurs or before it can cause harm. Developed within the Toyota Production System by industrial engineer Shigeo Shingo, the term derives from the Japanese words poka – mistakes, and yokeru – to dodge. It is often used synonymously with mistake-proofing or error-prevention.
In practice, a poka-yoke is a technique or mechanism that prevents a manufacturing process from proceeding to the next step unless it is correct. A poka-yoke can either be a detection-based control mechanism, designed to alert operators of an occurred error, or a prevention-based alarm mechanism, designed to stop a process from altogether resulting in error.
Poka-yokes can be implemented into virtually any stage of a manufacturing process from quoting to packaging, or even inform the initial design of a product. Measuring and managing these methods is as paramount as successful implementation. Manufacturing software can play a pivotal role in the effective management of poka-yoke in its application.
Is poka-yoke part of Lean, Six Sigma, or the Theory of Constraints?
The poka-yoke concept has been widely adopted in various quality management systems across many industries. While not a concrete part of either, it is often associated with Lean manufacturing and Six Sigma – two renowned manufacturing philosophies prioritizing waste reduction and quality improvement.
Lean focuses on streamlining processes, eliminating non-value-adding activities (often referred to as waste in Lean manufacturing), and continuous improvement. Six Sigma, on the other hand, strives for improved quality by utilizing various methodologies for reducing variation and defects. Poka-yoke complements both by providing systematic methods to avoid errors.
Poka-yoke’s relevance also notably intersects with the Theory of Constraints (TOC) management philosophy. TOC identifies the most significant limiting factor (i.e., constraint) standing in the way of achieving a goal and attempts to systematically improve it. Incorporating poka-yoke techniques in TOC helps to directly address or even eliminate these constraints.
Continue reading about the Theory of Constraints.
The six principles of mistake-proofing
Poka-yoke relies on six core principles. Each one offers a strategic method for preventing errors to make systems foolproof by design. Understanding and applying these principles can lead to significant defect reduction, leading to enhanced productivity and improved customer satisfaction.
Elimination
Elimination focuses on removing the possibility of an error or defect entirely from a process. This usually entails redesigning a component so that it can only be installed correctly. Elimination targets the root cause of potential errors, ensuring that there’s no opportunity for them to occur in the first place. This is the most straightforward and often most effective approach to mistake-proofing, as it directly addresses and removes a potential problem.
Replacement
If elimination is not feasible, replacement involves substituting a step, process, or component that’s prone to errors with a more reliable and less error-prone alternative. Replacement aims to maintain or enhance production efficiency by introducing elements that are inherently less likely to result in mistakes, thereby improving the overall reliability of the operation. For example, automating an assembly step to reduce or negate the likelihood of human error.
Prevention
Prevention is focused on designing processes in such a way that errors cannot occur in the first place. This principle goes beyond elimination by building error-proofing directly into the process itself, often through physical or digital controls that prevent the process from resulting in error. An example is a system that requires all safety checks to be completed and validated before a machine can be started, thus preventing the operation from beginning under unsafe conditions.
Facilitation
Facilitation makes the correct action more straightforward, often through design modifications or clear instructions. This principle is based on the idea that if the right way is the easiest, errors are less likely to occur. An example of facilitation is the use of color coding to help operators quickly identify the correct part or tool for a specific operation, thus reducing the chance of mistakes due to confusion or oversight.
Detection
Detection involves identifying errors as they occur and stopping processes from proceeding before they can lead to defects. This principle is crucial for processes where elimination, replacement, and facilitation might not be fully applicable. Detection mechanisms, such as sensors that verify the presence of a part or alarms that signal deviations, allow for immediate correction, preventing minor errors from escalating into significant defects.
Mitigation
Mitigation reduces the impact of an error once it has occurred, aiming to minimize the consequences. This principle comes into play when prevention and detection strategies are not enough to eliminate errors. An example of mitigation could be a software feature that creates automatic backups of data, ensuring that even if an error occurs, the information can be quickly restored, thus mitigating the error’s impact.
Poka-yoke methods in manufacturing processes
Implementing poka-yoke in manufacturing processes requires a thoughtful approach to identifying where errors occur and devising practical solutions to prevent them. The underlying aim is to ensure that quality is built into the production process, reducing the likelihood of defects and enhancing overall efficiency. Poka-yoke can be applied in various ways, ranging from simple physical modifications to complex system redesigns.
In its original form, poka-yoke had three main types – the contact method, fixed-value method, and motion-step method. Let’s go over each of these in a bit more depth.
Contact method
The contact method is a straightforward application of poka-yoke, relying on the physical attributes of a component or workstation to ensure correctness. This can include shape, size, orientation, or other physical features that prevent incorrect assembly or operation.
For instance, designing a part so it can only fit in the correct orientation ensures that assembly errors are virtually eliminated. This method is particularly effective for tangible, mechanical processes where physical mismatches can lead to errors.
Fixed-value method
The fixed value method, also known as the constant number method, involves implementing an alert into a process step if a specific number of actions is not completed. It’s perfect for implementing into processes with a sequential production routing.
For example, suppose a sub-assembly must have five screws installed before the next step of assembly. A system is put in place that notifies the operator if any are missing. This could be achieved by a machine scanning for the number of installed screws, time-releasing the screws at the process step, etc.
Motion-step method
The motion step method focuses on achieving the correct sequence and completion of actions within a process. By monitoring the steps taken by an operator, this approach ensures that no part of the process is omitted or repeated and that each action is performed in the correct order.
For example, a digital system can guide operators through a process, alerting them if a step is missed or performed out of sequence. This method is particularly useful in complex assembly processes where the correct order and execution of steps are critical in ensuring product quality.
How to implement a poka-yoke?
Implementing a poka-yoke system in your manufacturing process is a structured approach to enhancing quality and efficiency. Next, let’s look at a basic guideline on how to successfully implement a poka-yoke:
- Identify the problem. Begin by pinpointing specific areas within your manufacturing process where errors frequently occur. This could be a step where defects are commonly found or a task that often requires rework. Understanding the nature and frequency of these problems is crucial for targeting your poka-yoke effectively.
- Find the root cause. Once the problem areas have been identified, conduct a thorough analysis to determine why these errors are happening. Root cause analysis tools like the Five Whys or fishbone diagrams can be invaluable in tracing problems back to their source. For instance, if a particular part is often installed backwards, ask why this is happening until you reach the fundamental reason, such as ambiguous part design.
- Determine the correct poka-yoke method to use. With a clear understanding of the root cause, you can now select the most appropriate poka-yoke method. For example, if the issue stems from parts that can be easily installed incorrectly, the contact method could be employed by redesigning the parts so they only fit together in the correct orientation.
- Implement and test the poka-yoke. With the appropriate poka-yoke solution selected, the next step involves designing and implementing the method within the process. This should begin with a pilot implementation, allowing you to observe the solution in action and make necessary adjustments. Testing is critical during this stage as it validates the effectiveness of the poka-yoke and ensures that it integrates seamlessly into the existing workflow without introducing new issues.
- Train employees. Once the poka-yoke is in effect, training is essential to ensure that employees understand how to use the new measure. Comprehensive training sessions should explain the purpose of the poka-yoke, how it works, and the role employees play in maintaining it.
- Measure the efficiency. After implementation, closely monitor the process to measure the impact of the poka-yoke on error rates and efficiency. This data will be invaluable for assessing the effectiveness of the solution and identifying potential areas for further improvement.
3 poka-yoke examples in manufacturing
Here are three examples of poka-yoke in action, each illustrating a different method: contact, fixed-value, and motion-step.
Contact method example
A classic example of the contact method in manufacturing is the design of SIM card slots in smartphones. These slots are designed in such a way that the SIM card can only be inserted in one direction, thanks to the notched corner of the SIM card aligning with a corresponding shape in the slot.
This simple yet effective design prevents the common error of inserting the SIM card incorrectly, which could potentially damage the card or the phone. By employing physical attributes to ensure correct assembly, this poka-yoke technique eliminates the need for additional checks or corrections.
Fixed-value example
In assembly lines that require a specific number of components, like screws in a laptop assembly, the fixed value method is often applied through the use of parts bins that contain exactly the number of components needed for a single assembly. Once empty, the bin’s status signals that all parts have been used, ensuring completeness of the assembly.
If there are parts left, it indicates an error in the assembly process. This method not only simplifies the assembly process but also acts as an immediate check for missing components, thereby preventing the assembly of incomplete or defective products.
Motion-step example
A great way to exemplify the motion-step method is in complex assembly where each step must be completed in a precise sequence. Manufacturing execution systems are used to guide operators through each step of the assembly process, with sensors or software to verify that each action has been performed before allowing the operator to proceed to the next step.
For instance, in the automotive industry, torque wrenches connected to a digital monitoring system can ensure that bolts are tightened in the correct order and to the specified torque. This not only ensures the integrity of the assembly but also prevents the omission of critical steps, enhancing both the safety and quality of the final product.
Poka-yoke best practices in manufacturing
Here are four crucial tips for implementing and maximizing the benefits of poka-yokes in your manufacturing setup.
- Be creative. Innovation is key when it comes to designing effective poka-yoke solutions. Look beyond traditional methods and think creatively about how to prevent errors. This could involve utilizing new technologies, repurposing existing tools in novel ways, or simply observing the process from a different perspective to identify unique error-proofing opportunities. Creativity in poka-yoke leads to simple, yet ingenious solutions that can prevent complex problems.
- Be proactive. Don’t wait for errors to occur before taking action. Poka-yoke is fundamentally about prevention, therefore, a proactive approach is essential. Analyze your manufacturing processes regularly for potential error points, and implement poka-yoke measures before errors turn into defects. This forward-thinking mindset helps in creating a culture of continuous improvement and prevention rather than correction.
- Implement ways to measure effectiveness: Like any process improvement initiative, the success of poka-yoke techniques should be measurable. Establish Key Performance Indicators (KPIs) related to error rates, quality control, and process efficiency both before and after implementing poka-yokes. Regular monitoring and analysis of these KPIs will not only demonstrate the value of poka-yoke implementations but also highlight areas for further improvement. A manufacturing ERP or MRP system can be an essential tool for tracking many of these metrics in your production effort.
- Engage your team. The effectiveness of poka-yoke is largely dependent on the people who work with these systems daily. Engaging your team in the design and implementation of poka-yoke solutions ensures they are invested in the process. Furthermore, comprehensive training programs are crucial to help employees understand how these systems work, why they are important, and how to effectively utilize them. Empowering your team with this knowledge fosters a proactive attitude towards quality and efficiency, making poka-yoke a natural part of their daily routine.
How can manufacturing software help with mistake-proofing?
Manufacturing software can play a pivotal role in enhancing mistake-proofing strategies. By integrating sophisticated algorithms for production scheduling, integrating shop floor control, monitoring processes in real-time, and automating many parts of production management, these systems offer a robust framework for identifying potential errors before they escalate into costly defects. This automation helps minimize human error and facilitate a more seamless flow of operations.
The analytics capabilities of modern manufacturing software further provide invaluable insights into process performance, highlighting areas prone to errors and inefficiencies. By analyzing data collected from the production line, manufacturers can pinpoint specific steps in the manufacturing process that require intervention. In essence, manufacturing software not only supports the implementation of poka-yoke principles but can also foster a culture of quality and excellence throughout the manufacturing process.
Key takeaways
- Poka-yoke, or mistake-proofing, is a mechanism or technique designed to prevent human errors from occurring or causing defects in a manufacturing or service process.
- Poka-yokes can be either prevention-based alarm mechanisms, designed to stop a process from resulting in error, or detection-based control mechanisms, designed to alert operators of an occurred error.
- The six principles that poka-yoke is built on are elimination, replacement, prevention, facilitation, detection, and mitigation.
- Basic poka yokes fall within one of three types. Contact poka-yoke ensures that a component can only be installed in one correct way. Fixed-value poka-yoke eliminates the chance of missing or adding details from a step. Motion-step poka-yoke mandates following a precise sequence of actions in an operation.
- Poka-yoke implementation best practices include being insightful and proactive about where to install the solutions, measuring the results and performance of poka-yokes continuously, and engaging the team to stay mindful and informed on poka-yoke practices.
Frequently asked questions
Poka-yoke is a Japanese methodology used in manufacturing across various industries to prevent errors before they occur. Examples include SIM card slots that only allow the card to be inserted one way, parts bins containing the exact number of components needed for assembly, and digital workflow systems that guide operators through each process step.
Poka-yoke is a technique that complements both Lean manufacturing and Six Sigma, but is not a direct part of either method. It enhances Lean by eliminating waste through error prevention and supports Six Sigma’s goal of reducing variation and defects.
In Japanese, poka-yoke (ポカヨケ) means “mistake-proofing” or “error prevention.” The term derives from the Japanese words poka, meaning mistakes, and yokeru, meaning to dodge.
While poka-yoke is not the same as kaizen, which means “continuous improvement,” it is often used as part of kaizen initiatives. Poka-yoke focuses on preventing specific errors while kaizen is about overall process improvement.
You might also like: Production Control – A Practical Guide