What Is Pipeline Inventory?
Pipeline inventory consists of goods that a company has ordered but which have not yet arrived in the facility. Managing this type of inventory can help schedule production or shipments in advance, reduce standing inventory levels, and avoid stock-outs.
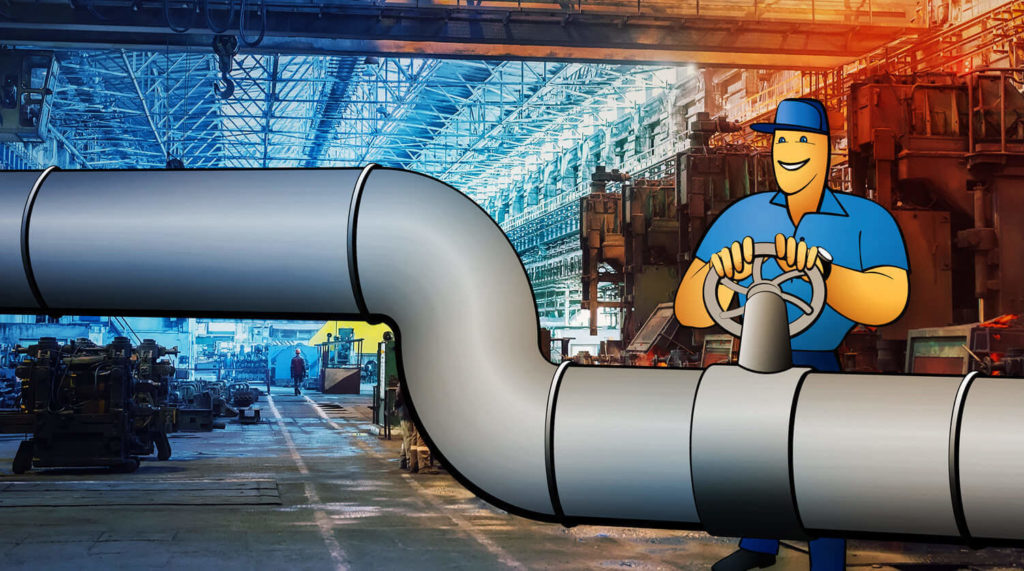
You can also listen to this article:
What is Pipeline Inventory?
Pipeline inventory, also called expected on-order inventory, is essentially any inventory that a company has incoming from suppliers or intermediaries but which has not yet reached its facilities. This includes goods that are already in transit, awaiting shipment, or are still being manufactured by the supplier, as well as items moving between storage or production facilities. Tracking pipeline inventory is useful for many reasons, like scheduling production or shipments in advance without needing to have the required goods physically present.
In inventory management, pipeline inventory is used as a type of inventory buffer. Inventory buffers are means of ensuring stable business and production flow by creating extra leeway for the availability of stock items. This can protect against fluctuations in supply and demand, negate component supply disruptions, reduce opportunity loss, and affect many other metrics. Pipeline inventory is used as a buffer when the lead times for components and materials are very long. To avoid stockouts or overstocking, manufacturers with a good handle on their pipeline inventory can order such items in regular intervals instead of ordering them only when a production order comes in. This helps to ensure a steady flow into stock and significantly shortens lead time.
With properly implemented inventory management software, items in the pipeline can be booked into new manufacturing orders in advance of their arrival at a warehouse. Taking these moving parts into account is important for keeping production flowing when components have long shipping times. A capable MRP/ERP software is usually required to book en route components into new manufacturing orders, as keeping tabs on them manually would prove dizzyingly complex for even lower scale manufacturers.
Calculating Pipeline Inventory
For production management and accounting purposes, it pays to know how much of a company’s inventory is in the pipeline, as well as how much of it should be kept in the pipeline. A simple method for estimating pipeline inventory is to multiply the lead time of the items with their expected or actual demand rate:
Pipeline inventory = Lead time x Demand rate
For example, if a component has a shipping time of 20 days and it requires further assembly of one day once it reaches the manufacturing plant, the lead time of the order would be 21 days, or three weeks. The demand rate should be expressed as the number of units per time period. Let us say the demand rate for the product is five units a week. To find out the number of components to keep in the pipeline, the lead time of three (weeks) is multiplied by the demand rate of five. This indicates that the company should on average have 15 components on order to ensure stable production and maintain consistent inventory levels. Taking the example further, factoring in the cost of $100 per component, it is possible to calculate the worth of pipeline inventory to be 15 x $100 = $1,500.
The above method is a helpful starting point for planning purposes. It does not inform on when to order or what the actual situation in the pipeline is at a given time, however. What it does make possible to deduct is that if the company receives components for the next three week’s production today, a new order for 15 more components should be ordered immediately, unless safety stock comes into use. In some cases, it makes sense to order five units per week, though, instead of ordering 15 units every three weeks. There may also be situations where keeping constant pipeline inventory does not make sense at all and a company could choose to fill up stocks for a longer time period with a single order.
One way to figure out how much to order at once is to calculate the Economic Order Quantity (EOQ). This is a theoretical order quantity used to minimize inventory costs by striking an optimal balance between ordering costs (e.g. shipping and handling) and holding costs. EOQ is used mostly in situations where demand is stable and the company already has a good understanding of the annual demand rate and carrying cost per unit, such as many make-to-stock process manufacturers.
Advantages of maintaining Pipeline Inventory
While most manufacturing companies have at least some inventory items in the pipeline either way, systematically managing pipeline inventory is a good idea for many reasons.
The main advantages of keeping tabs on pipeline inventory include:
- Shorter lead time and optimized workflow for products that use components with a long shipping time
- Better estimations for calculating the lead time of production orders
- More accurate inventory forecasting and production planning
- A deeper understanding of the supply chain, shipping routes, and rates
- Better optimized supply chain management
- Lower holding costs for standing inventory
Outside of small enough companies being able to keep tabs on their limited pipeline stock manually, most firms usually employ dedicated or integrated inventory management and inventory optimization software to track and manage their pipeline inventory. This could be seen as an added expense. In most cases, however, it is an inevitable one, as staying competitive in the manufacturing world is virtually impossible without thorough insight into your inventory and its movements. Having a large pipeline inventory may also entail certain risks in situations of rapid market fluctuations and supply chain disruptions. This can be mitigated to a degree by investing time in strategic production management and capacity planning.
Other types of inventory buffers
While pipeline inventory is a good way to keep production flowing smoothly when components have long shipping times on the supplier’s side, it is not the only type of inventory buffer to optimize production. There are a number of other methods in inventory management to anticipate, guard against or mitigate market disruptions and changes in business volume both on the sales as well as the production side of the business.
One of the more common types of inventory buffers on the sales end is safety stock. Safety stock mostly refers to completed products that are kept in inventory to cover sudden increases in demand. This could mitigate uncertainties arising from component supply or account for opportunity loss from stockouts and other unanticipated shortages. Similar to safety stock, anticipation inventory is another type of inventory buffer, characterized as extra stock of finished goods that is accumulated in situations of reliable predicted increases in demand, such as an upcoming holiday season.
Another type of more specific inventory buffer, mostly used by manufacturing companies, is decoupling inventory. Decoupling inventory consists of components and other inventory that are set aside in special decoupling points to guard against stoppages or bottlenecks in the production line. These could occur due to supply issues, workstation breakdowns, worker illness, etc. This method mostly involves creating extra WIP inventory on the production side.
Pipeline Inventory in MRP/ERP systems
Robust MRP/ERP systems used to require giant investments of time and resources to be implemented and were as such reserved for only large-scale manufacturers. Thus, keeping tabs on the pipeline inventory used to be a paper-and-pencil ordeal for many small and medium businesses. Today, capable manufacturing resource planning software is available for SMBs at affordable prices. More and more manufacturing SMBs are adopting these software solutions to modernize their production process and bring workflow to a new level of efficiency.
Most manufacturing software has versatile inventory management capabilities and inventory can easily be included in the production process even if it is still in the pipeline. One of the simplest ways to use en route stock for existing and incoming manufacturing orders is to define it as expected or planned stock. When an order is placed, the MRP system recognizes the incoming items as expected to arrive. When the shipping period and arrival location are defined, the en-route stock can be booked into upcoming manufacturing orders with automatically calculated scheduling for routing, completion, shipping, etc. As the inventory exits the pipeline and arrives at the warehouse, production is pre-planned and work can start in an efficient and timely manner.
Key takeaways
- Pipeline inventory is essentially any inventory that a company has incoming from suppliers or intermediaries but which has not yet reached its facilities.
- Managing pipeline inventory can be very useful in reducing the lead time of products that have components with long shipping times, thus lowering the holding costs of standing inventory.
- When properly managed, pipeline inventory can act as an inventory buffer, protecting against fluctuations in supply and demand, negating component supply disruptions, reducing opportunity loss, etc.
- Robust and capable MRP/ERP systems are usually required to ensure in-depth inventory management and take full advantage of the time that stock spends in transit.
You may also like: Supply Chain Planning – A Quick Guide