What Is Piece Rate Pay and How to Manage It?
Piece rate pay is an employment system where workers are paid per unit they process. While it has many benefits to both employers and employees, it also comes with a certain set of complexities and downsides.
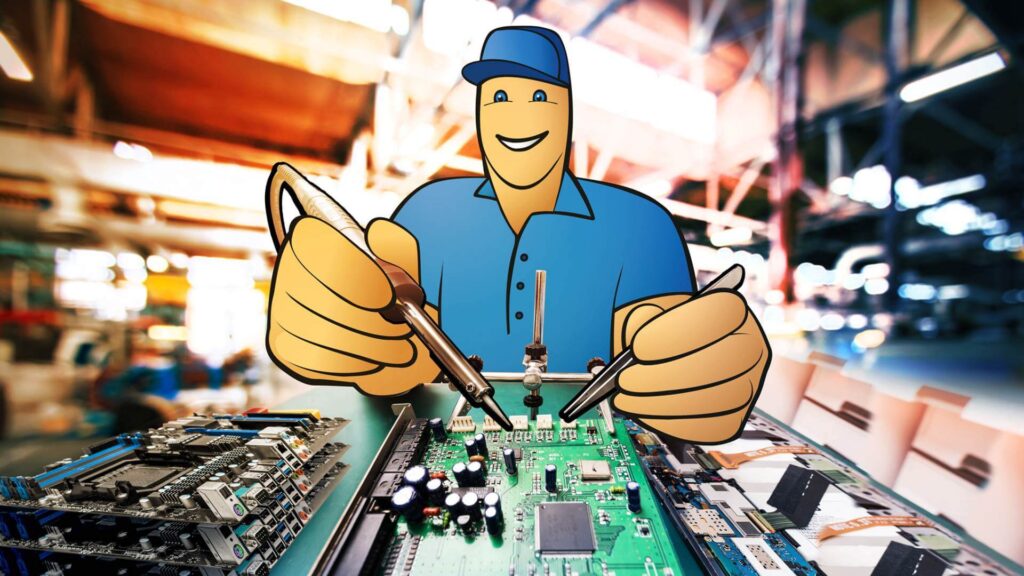
You can also listen to this article:
What is piece rate pay?
Piece rate pay, also known as piece work, is a compensation method where employees are paid based on the quantity of units they process. While especially prevalent in manufacturing (e.g. in garment production), piece rate pay is also commonly used in agricultural work (like harvesting and planting), some services, and in gig work such as ride-sharing and food delivery.
Piece rate vs. time rate
In contrast to piece work, time rate pay compensates employees based on the time they spend working, at a fixed rate per hour. This method provides income stability, ensuring that workers are paid a consistent amount for each hour worked, regardless of the actual work output during that time. Time rate can be used for any job but it is almost a requirement in fields that involve creativity, varying task complexities, or teamwork, such as in creative industries or services where output isn’t as easily quantifiable. For example, an office assistant earning a set hourly wage will have a predictable income, even if the nature and volume of work fluctuate throughout the day.
Advantages of piece rate pay
Employers can often find several benefits in adopting a piece work system as opposed to an hourly rate system. These include:
- Increased productivity. As piece work incentivizes workers to produce more to earn more, this approach often leads to increased productivity and minimized downtime.
- No costs related to non-productive time. Paying only per unit processed means that employers do not have to pay employees for non-productive activities such as breaks, setups, and other downtime.
- Simplified cost accounting. Only paying per unit processed makes it much easier to calculate costs per unit.
- Cost control. When labor costs are directly tied to output, it is easier to forecast and control production costs. In addition, employers do not have to pay for downtime or lose money to production line inefficiencies.
- Improved product quality. Although piece work incentivizes speed most of all, having high quality standards in place that determine whether a unit qualifies for payment could significantly improve quality while also increasing efficiency.
Employees, however, can also benefit from piece rate compensation. Here are some of the benefits of piece work for workers:
- Higher earning potential. As their efficiency improves and the number of units processed per hour grows, workers can significantly increase their salaries.
- Flexible hours. As piece rate work functions without the employee clocking in and out, it usually includes a fair amount of scheduling flexibility.
- Better motivation. Piece rate employees are often more autonomous and receive constant feedback that also reflects in their earnings. This can have a positive effect on employee motivation.
Disadvantages of piece rate pay
Although piece work comes with several benefits, employers should also consider the potential downsides before adopting such a system:
- Prioritizing quantity above quality. Piece work pay may push workers to focus on speed rather than quality. When quality control systems are not capable of filtering out sub-par products, this could translate into losses for the company.
- Employee dissatisfaction. If piece rates are set too low or when work is inconsistent, workers may become dissatisfied. This could result in high employee turnover, which could leave the company with perpetually untrained and inefficient staff.
- Administrative complexity. Managing compensation on a piece rate basis without a proper system in place is a complete headache. In addition to tracking the quantity produced by each employee, companies also need to make sure that the work qualifies for payment in terms of quality.
- Compliance issues. All employers must ensure that their workers’ earnings meet minimum wage requirements, which can be challenging in piece work environments during slow periods or with slower workers. Overtime pay adds another layer of complexity to payroll management.
- Process optimization. Piece work is best suited for companies whose process optimization and continuous improvement programs are well underway or fully mature. Companies with a rapidly evolving continuous improvement program may encounter overpaying workers for non-optimized processes.
As for piece rate workers, the added flexibility and earning potential come with the following disadvantages:
- Inconsistent earnings. Piece rate workers often face fluctuating incomes due to variations in the workweek’s demand, affecting their total compensation and making financial planning challenging. This inconsistency can lead to stress, especially when the workload is light and the total pay is lower than expected.
- Performance pressure. The need to maintain high levels of output to secure adequate piece rate earnings places considerable performance pressure on workers. Recovery periods and rest periods might be overlooked in the rush to produce more, affecting the personal wellbeing of the workers.
- Increased risk of workplace accidents. The rush to maximize output under a piece rate pay system can lead to neglect of safety practices, increasing the risk of workplace injuries.
- Limited growth opportunities. A piece rate pay system primarily rewards output, which can sideline efforts towards career development and upskilling.
- No compensation for downtime. Downtime due to machinery breakdowns, supply issues, or necessary rest periods does not contribute to piece rate earnings, leaving workers uncompensated for these hours of work.
Types of piece work systems
There are several different types of piece work systems employed in various situations. Here are some of the most common ones:
Straight piece rate system
This is the most straightforward piece work system, wherein employees are paid a fixed amount of each unit they process. For example, assembly workers might be paid $1.50 for each widget they assemble.
Differential piece rate system
This approach further incentivizes speed as workers are paid a higher rate if they exceed a certain output within a set timeframe. For example, assembly workers might be paid $1.50 for each widget they assemble but if they exceed 20 widgets per hour, they are paid $1.75 per widget.
Hourly pay + piece rate
In this system, workers receive a base hourly wage but earn extra for each unit processed. For example, assembly workers might be paid $10/hour while earning an extra $1 for each widget produced.
Inherently flexible, the piece work approach can be moulded to fit the needs of the company and its employees by combining different systems and remuneration methods.
Piece rate pay and regulatory compliance
Piece work is subject to various regulations designed to ensure fair labor practices. To protect workers, laws such as the Fair Labor Standards Act (FLSA) in the US, the National Minimum Wage Regulations in the UK, and various state-specific regulations in the EU and worldwide provide guidelines for its implementation.
Under the FLSA, employers must ensure that piece rate workers still earn at least the applicable minimum wage for the total number of hours worked in a workweek. This requires a computation of the average hourly rate each pay period to verify compliance. If piece rate earnings divided by the total hours worked fall short of the minimum wage, employers must make up the difference.
Furthermore, the FLSA mandates that piece rate workers receive overtime compensation for hours worked beyond the standard 40-hour workweek. The overtime rate should be no less than one-and-one-half times the worker’s regular rate of pay. Calculating the regular rate for piece rate workers involves dividing the week’s total earnings by the total number of hours worked, ensuring the overtime rate reflects this calculation accurately.
In California, the Department of Industrial Relations imposes additional requirements on employers, highlighting the necessity of meticulous record-keeping by employers to document hours worked, piece rate earnings, and overtime compensation accurately.
The Department of Labor at both the federal and state levels emphasizes the importance of adhering to minimum wage laws and overtime requirements. This legal framework aims to protect workers from potential exploitation while allowing the flexibility and productivity benefits that piece rate pay can offer.
How to manage piece rate pay?
Managing piece rate pay effectively requires careful planning, tracking, and administration. The process can vary significantly depending on whether you are using manual methods or modern Manufacturing Resource Planning (MRP) software. Here are step-by-step guides for both scenarios:
Managing piece work manually
- Define output standards. Clearly define what constitutes a piece or unit. Ensure these standards are transparent and measurable, so employees understand what is expected of them.
- Set appropriate piece rates. Determine the piece rate by considering the complexity of tasks, average industry wages, and legal requirements such as minimum wage. The rate should be fair and realistically achievable.
- Record work output manually. Use timesheets or production logs where employees can record their daily outputs. Ensure these are checked regularly to maintain accuracy.
- Assess quality. Implement regular checks to ensure that the work meets quality standards. Discard or discount subpar units from the earnings calculation to maintain product standards.
- Calculate earnings. At the end of each pay period, manually calculate earnings based on the recorded outputs. Multiply the number of units produced by the piece rate for each type of task or product.
- Handle adjustments and complaints. Be ready to handle any discrepancies or disputes over pay or recorded outputs. Establish a clear dispute resolution process.
- Comply with labor laws. Ensure that all workers receive at least the minimum wage for the total number of hours worked, including overtime compensation if applicable. This may require additional calculations to top up earnings.
Managing piece work with MRP software
- Configure the MRP system. Turn on the piece payment functionality in your MRP software and input all product standards and associated piece rates. Ensure the system can track individual employee outputs against these standards.
- Automate data collection. Utilize the software’s capability to automatically record production quantities directly from workstations or through digital production logs. This reduces errors and streamlines the recording process.
- Monitor real-time productivity. Use the MRP system to monitor real-time data on employee output, allowing for immediate adjustments in workflow or staffing if needed to optimize productivity.
- Integrate quality checks. Set up quality inspections tracking for the processed goods to check whether they meet the specified standards.
- Automate pay calculations. Have the software automatically calculate total compensation based on recorded outputs and piece rates.
- Generate payroll reports. Use the MRP system to generate detailed payroll reports that breakdown earnings by piece rates. This helps in maintaining transparency.
Using MRP software can significantly simplify the management of piece rate pay by automating most of the process, reducing manual errors, and providing real-time productivity insights. This not only improves operational efficiency but also helps in maintaining compliance and transparency in compensation practices. Whether using manual methods or MRP software, the key to successfully managing piece rate pay lies in clear communication, fair setup, and vigilant monitoring.
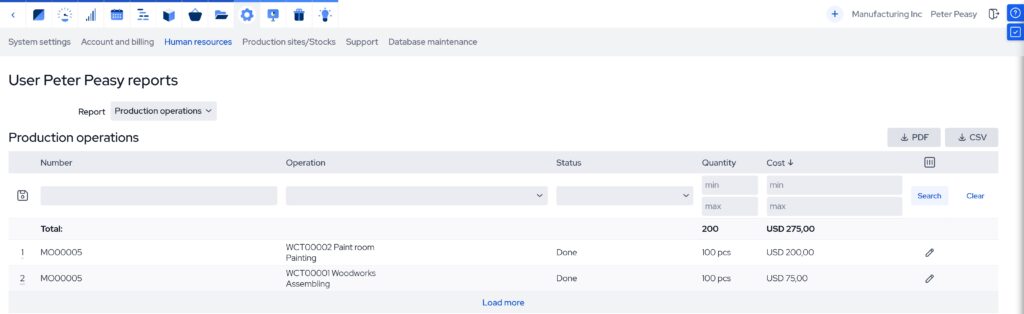
Additional tips for managing piece work
Regardless of your piece work management system, using the following tips can help you ensure success in the long run.
Establish realistic production targets
These should be based on historical data and realistic assessments of what employees can produce within their working hours. This helps in setting fair piece rates that are motivating but not unattainable.
Set up a bonus system
Incentivize high production rates with a bonus system to minimize the risk of having to top up low-performing employee earnings to meet minimum wage requirements.
Use quality as an additional bonus metric
Besides quantity, quality can be a part of the bonus system. Offer bonuses for low defect rates or high customer satisfaction scores, which encourages workers not to sacrifice quality for quantity.
Regularly review and adjust piece rates
Keep piece rates dynamic by reviewing them regularly against productivity data, labor market trends, and changes in minimum wage laws. Adjusting rates as necessary helps maintain fairness and competitiveness, ensuring workers feel valued and motivated.
Key takeaways
- Piece rate pay provides a flexible work model that aligns compensation with productivity, motivating workers to increase their output as they can directly influence their earnings based on the number of units they process.
- Employers must navigate a complex landscape of labor laws, such as the Fair Labor Standards Act (FLSA) in the US, which mandates that piece rate workers must still earn at least the applicable minimum wage for the total number of hours worked.
- Managing piece rate pay can be administratively complex, requiring accurate record-keeping of hours worked, units produced, and corresponding pay.
- While piece rate pay incentivizes higher productivity, it can also lead to a focus on speed over quality. Employers must balance these priorities by setting up quality control systems that ensure only units meeting certain standards qualify for payment.
- For workers, piece rate pay offers a potential for higher earnings and flexible hours, but it also comes with risks such as inconsistent earnings and increased performance pressure.
Frequently asked questions
Whether piece rate is better than hourly pay depends on the specific job and industry. Piece rate can lead to higher productivity and potentially higher earnings for workers, as it directly ties compensation to output. However, hourly pay offers more income stability and is better suited for jobs requiring creativity, teamwork, or varying task complexities.
Commission and piece rate are both performance-based pay systems but are applied in different contexts. Commission is typically a percentage paid on the sales someone makes or the deals they close, commonly used in sales and real estate jobs. Piece rate, on the other hand, pays a fixed amount for each unit produced or task completed, often used in manufacturing or agriculture.
In agriculture, piece rate pay is a compensation method where workers are paid based on the amount of agricultural produce they harvest, plant, or process. This system incentivizes workers to be more efficient, as their earnings are directly proportional to the quantity they handle. It’s commonly used for tasks like picking fruits, vegetables, or other crop-related activities where output is easily quantifiable.
You may also like: Product Costing in 7 Easy Steps