Data preparation before MRP system implementation
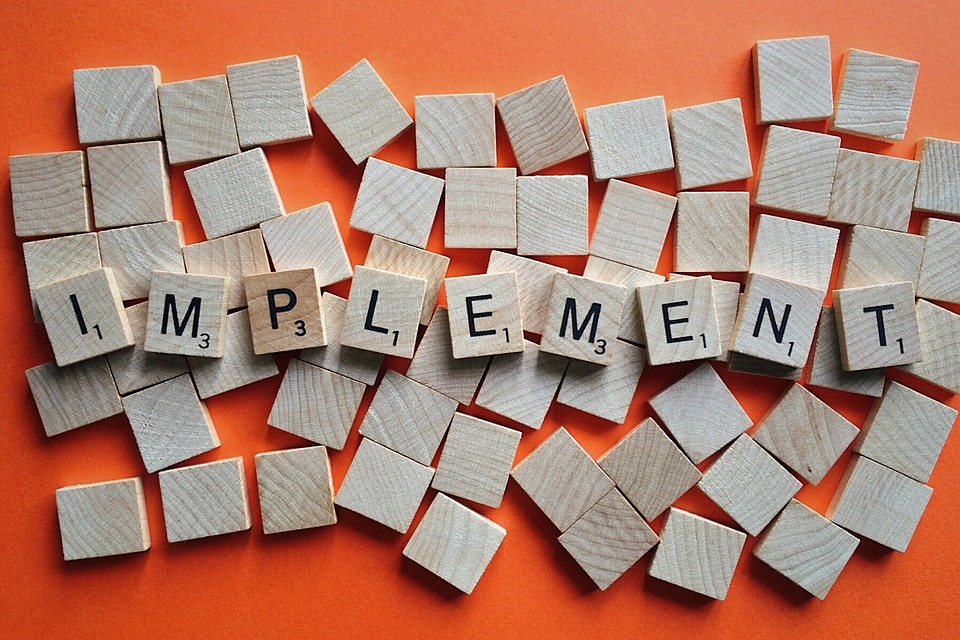
A seed is from which the plant grows and produces fruit. If there are no seeds or bad seeds, then there will be no fruit.
That’s a great analogy for two reasons. First, we’re all after the fruit – a more efficient business, a higher profit. Second, if you mistakenly plant the wrong seeds – e.g. apples instead of grapes – then you will not get the expected fruits.
What’s seed data? Sometimes this is also referred to as Master Data. This is fundamental information, which the MRP system uses to manage inventory, schedule production, pre-populate purchase orders, etc.
The seed data is that which is in constant use. It is relational, re-used often and updated only when bigger changes occur; e.g. new product revisions are released, new machines are installed to the shop floor, etc.
We’ll list some of the most critical seed data, below.
1. Items (in other words, articles, Stock Keeping Units, etc.)
Make sure your total list of materials, parts, and products is neatly defined without holes or double-entries in the data. Each item should have a proper part number, description, group, min. stock level, etc.
Also, make sure not to carry your old-forgotten articles to the new system!
2. Bills of Materials
A Bill of Material outlines which materials and parts are used for building the product. It connects the products with its parts, all of which have to be listed in the system as articles.
For production and inventory planning, the BOM should also include scrap and other materials or consumables, which are not directly part of the product. (Learn more about MRPeasy’s BOM software functionality)
3. Types of work stations and individual work stations within those
If you haven’t logically structured your shop-floor, now is the time to do so. Similar machines, tables, etc. should be grouped into work station types. Plus, markdown if some work stations have other than standard working hours if maintenance is planned if there are dedicated employees, etc.
Capacity planning cannot work if this information is not properly defined.
4. Routings
Routing is the list of stages or operations, a product goes through. It maps in which work station type and how long each operation should take place, and in which order. This is used for accurately scheduling the individual operations into each work station’s calendar.
Keep in mind to avoid a typical mistake: a routing is not detailed instructions for building the product – it’s just mapping the general stages of production.
5. Vendors and Purchase Terms
Each material you procure should have at least one vendor attached, plus price (or pricing tiers!), minimum order quantities, lead times, the vendor’s part number, etc.
Then, the MRP software can estimate when missing materials could be there (when scheduling production).
Plus, very importantly, it can save hours of meaningless work by simply pre-filling all your Purchase Orders!
6. Other details
There’s a lot of data that should be pre-defined. For example, not above mentioned, but fundamentally important! It is crucial to let the MRP system know what are your businesses’ working hours.
Plus, you might want to upload your customer base, their contact details, billing addresses and various price sheets for different customer types. You might want to define what is allowed reasons for stock write-offs, etc. There’s a lot of data; be persistent in consistently mapping it.
Be aware of the GIGO – Garbage-In, Garbage-Out!
As a last word of warning, always make sure that all your data is accurate. Double and triple-check the seed data. When it comes to operational day-to-day data, like entering purchase orders, reporting production, etc., then enforce that the data is entered on-time, without mistakes.
Computer systems can be extremely smart and effective, but they still do exactly as they are told. If you let the software know – even by mistake – that you want cucumbers, you are going to get cucumbers, not grapes.
MRP System Series #7: The right attitude for MRP system implementation
MRP system Series #6: Implementing Manufacturing Software. Benefits from Process Changes
MRP System Series #5: What Makes a Good MRP System?
MRP System Series #4: How Much Detail to Input into the MRP System?
MRP System Series #3: Top 5 Mistakes in Implementing Manufacturing Software
MRP System Series #2: What is the difference between MRP and ERP?