MRP System Series #4: How Much Detail to Input into the MRP System?
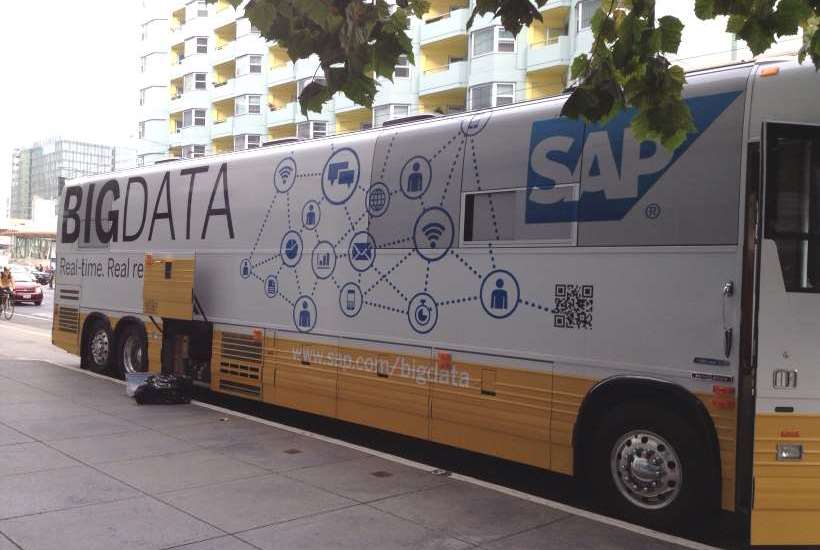
In our previous post, we described the top 5 mistakes why MRP system implementation could fail. We would like to proceed and give additional practical recommendations on how to avoid failure.
How Much Detail to Input into the MRP System?
The main reason why small manufacturers fail MRP implementation is not having a clear understanding of the most important goals and benefits.
Very often, everything is considered important and much energy is wasted on minor points. In practice, if the management of every single detail, process, and nice-to-have is expected from day zero, then the implementation can quickly become too difficult.
The few key people who thoroughly test and pilot the software are not capable of using the software in the name of all others who will be using the software at any given time (e.g. reporting for 25 shop-floor workers).
We suggest starting with the minimalistic approach in implementing an MRP system – do the least you can to get the most results.
It’s ok to want it all, but are you prepared to pay the price?
Start with this idea: 20% of actions bring 80% of results. Even if you are well prepared, you should always start simple. Only build out complex procedures as you become more comfortable.
What’s the Minimalistic Approach?
From the business perspective, the two most essential functions on which the MRP system performs excellently are:
1) Capacity planning: When can I deliver?
2) Cost calculation: How much will it cost?
For most manufacturing companies, this information gets 80% closer to the finish line. Therefore, these two goals are usually the most important.
If there’s no clear approach to how capacity requirements planning is set up, lead times are based on gut feeling, product costing is a mess and then what matters is improving the situation. A huge step forward would be achieving a guaranteed few day’s accuracy in scheduling (and promised delivery dates!), which only takes a fraction of the energy required for achieving an hour of accuracy.
The key idea is to avoid micromanagement and focus only on the critical.
What does this mean? This means realizing that many of the smallest details of production – individual operations, sub-assemblies, sub-level BOMs, half-products, etc. – are not that relevant in the big picture.
You may say, “But all the details ARE important!” Yes, but some things matter more than others when keeping the main objectives in mind.
Defining the Bill of Materials
Having a single-level Bill of Materials is the easiest situation to handle. There is only a list of raw materials – no sub-assemblies, which can create additional complexity and confusion.
This is the key.
To get started, that is exactly how you should define your Bill of Materials for the software (it doesn’t matter how many levels and sub-assemblies there are from the engineering point of view!). (Learn more about BOM management software).
Purchasable raw materials go in one end and the product comes out the other end. Zero sub-assemblies. No sub-levels. Everything merged into one. Simple, friendly and beautiful.
A kind of black box is created where materials go in from one end and products pop out from the other.
This achieves several goals:
- There is a clear connection between raw materials and the end-product.
- The material cost can be easily calculated.
- It is very simple to understand.
- It is very simple to report production finish.
- The product is available and in stock.
- The materials are consumed.
In some situations, the possible down-side is that the inventory levels of sub-assemblies are not tracked. But this vastly outweighs the simplicity of use.
Certainly, your employees already have (or should have!) the instructions on how to build the products. The software does not need to know-it-all and tell-it-all.
Defining Work Station Types
A workstation is a place where individual operations are done. One operation can be done at one time, in one workstation. The workstation could be a machine, a bench, an assembly table, etc.
A workstation type is a group of workstations that can all do the same tasks. For example, five CNC machines, or two assembly tables, or one oven.
A workstation type could also represent a virtual group of machines or tools; for example, a woodworks area with 10 different machines and tools, where, in practice, only 3 jobs can run in parallel. Therefore, the “woodworks” workstation type would have 3 workstations.
For effective operation planning, it is important to revisit how you currently group your workstations into workstation types.
In one scenario, each machine could belong to its individual group. But with many machines, this is likely impractical, since the operation flow can get very complex. In the opposite scenario, if there is just one group, then there will be little insight into real capacity and bottlenecks.
An optimal balance needs to be found. More isn’t necessarily better. If it’s possible try to regroup, simplify and generalize. The list of workstation types should be kept as short as possible, but not shorter.
Defining the Routing
Routing is the list of operations – the big steps through which the product needs to go.
What it’s not: instructions for building the product.
The same logic applies – keep it as simple as possible, but not simpler.
The first priority is obtaining an accurate production schedule and a capacity plan. For this, a very general and high-level routing will be sufficient.
A common mistake is defining every single detail, every smallest procedure and expecting someone to report each step of the way. For production scheduling and capacity planning purposes, most of these details are irrelevant.
How to define a routing? Use a stopwatch to measure how much time it takes, per workstation type, to build the product.
Then, simplify: build the routing with as few lines as possible, following a few key stages of production. If two lines have the same workstation type, could they be merged? Very often, they can.
There might be 100’s of individual operations performed, but following this method, you might end up with a routing like this:
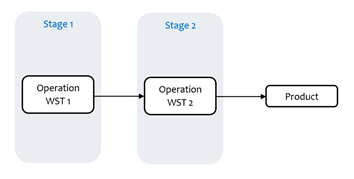
Or, something like this:
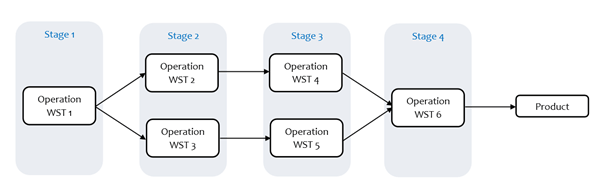
(WST – Work Station Type)
You may say that this is too general to represent how your product is made – things move back-and-forth, etc…Yes, but you will still get a reliable capacity plan and an accurate production schedule. Plus, it’s very easy to manage, unlike when there are hundreds of defined operations.
All in all, this achieves several goals:
- It is possible to easily plan the capacity of each workstation involved with reasonable accuracy.
- It is possible to plan the lead time with reasonable accuracy.
- It is possible to easily calculate the manufacturing overhead and labor costs.
- It is simple to understand.
- It is simple to report production.
Of course, if too simplified, the routing might be too general for real-time reporting of start-stop. But is that the first and foremost goal? Likely not. Instead, it will take considerable time before shop-floor workers are handed tablets for reporting. Before that, it’s unreasonable to make things more complex.
Until workers start personally reporting operations, then the schedule should be used for understanding the order of priorities; and, once a manufacturing order is finished, you can just click “finish production as planned” inside the MO. If something doesn’t go according to the plan, you can still modify it.
Final Words
The idea of a minimalistic approach is to implement the MRP system in a way that the greatest goals and benefits are realized first and minimal effort is wasted on second-order priorities, which can lengthen and derail an implementation if tackled too early.
Following the 80/20 rule (i.e. Pareto principle) will make the usage of the software straightforward for a small team. Complexity can be built successfully when needs arise and resources permit.
Altogether, the following benefits may be realized with relative ease:
- Production lead time is quickly and reliably estimated.
- The production calendar is populated based on capacity.
- The product cost is accurately calculated.
- The demand for raw materials is accurately estimated.
- Clear overview of the raw material and product inventory levels.
MRP system series:
MRP System Series #7: The right attitude for MRP system implementation
MRP system Series #6: Implementing Manufacturing Software. Benefits from Process Changes
MRP System Series #5: What Makes a Good MRP System?
MRP System Series #4: How Much Detail to Input into the MRP System?
MRP System Series #3: Top 5 Mistakes in Implementing Manufacturing Software
MRP System Series #2: What is the difference between MRP and ERP?