Material Requirements Planning and Manufacturing Resource Planning difference
The MRP is a planning system that allows you to manage the production resources of an organization. Here is an overview of Material Requirements Planning (MRP I) and Manufacturing Resource Planning (MRP II) differences.
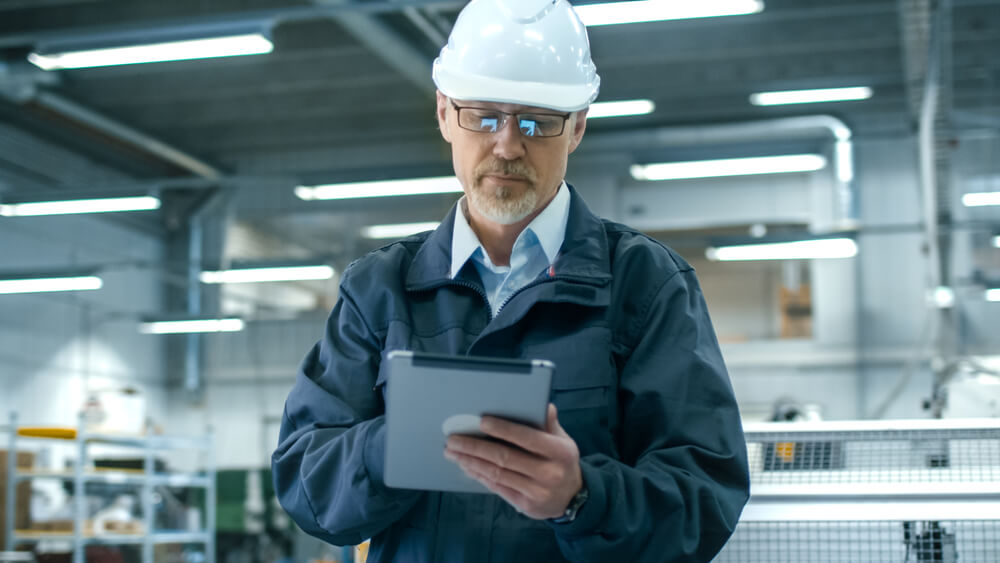
You can also listen to this article:
This concept has evolved over time. Today MRP systems are associated with software, with the ability to plan and control.
Its main objective is to determine the amount of resources that the organization requires, to meet the required demand. Strictly speaking:
- Ensure that materials are delivered in a timely manner to customers.
- Ensure optimal inventory levels
- Ensure the use of optimal resources within the organization (personnel, cash, machinery, energy, etc.)
Let’s see next how the MRP I evolved in MRP II, their main characteristics and differences between themselves.
History of MRP
The use of MRP systems dates back to World War II when the United States government used programs to organize the logistics of its military resources. Subsequently, they were transferred to the industry and in the 60s and 70s, the first MRPs systems were created. This is how the MRP I or Material Requirements Planning systems were born. Its main objective was to determine the amount of materials to reach the production levels using the minimum inventory cost.
However, businesses needed to manage a greater number of organizational processes. Thus, it was necessary to expand towards a broader planning model and that is why the MRP II system was born. This new system contemplates and integrates other areas of the business, such as:
- Factory
- Administration
- Sales
It is important to note that the evolution of computers allowed these systems to improve. Today they became a vital component for the management of manufacturing business processes.
What is MRP I
MRP I stands for “Material Requirements Planning”. It is basically a material planning and management system through the use of software. MRP I solves some issues within any manufacturing process, such as:
- What materials to buy
- How much material to buy
- When to buy the materials
To answer all of these questions, the MRP I use:
- The Production Master Plan which provides data on independent product demand.
- The Material Inventory, which means the amount of raw materials, semi-finished goods and finished products available.
- The Bill of Materials or BOM, combining the components to produce a unit of product, the standardized quantities to use and their parent-child relationship.
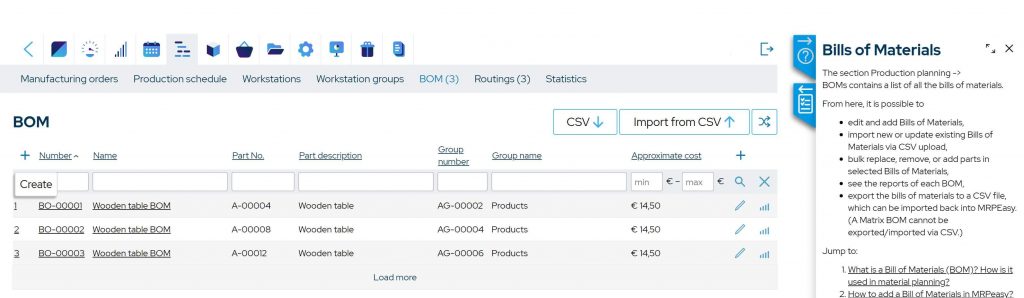
And the outputs obtained will be:
- A Recommended Production Schedule
- A Recommended Purchasing Schedule.
The Schedule is valid for both: the items to buy and the sub-assemblies and components to be produced.
Note that MRP I systems manage inventories of dependent demand. The dependent demand is for component parts or subassemblies. The independent demand is the demand for a finished product. As an example, a company that manufactures bicycles determines the amount of tires to buy for the bicycles demand forecast. The bicycles are independent demand, while tires are dependent demand.
A Master Production Schedule (MPS) is a plan for individual products to be manufactured in each individual time period.
Advantages of MRP I
The advantages of using an MRP System are shown below:
- Reduction of the cost of inventories
- Control of inventory levels
- Reduction of waiting times in supply and production
- Better manufacturing and purchasing planning
- Knowledge about input needs
- Help in making supply decisions
- Control and documentation
What is MRP II
MRP II is defined as “Manufacturing Resource Planning” and was born in the 80s. The purpose was to offer a broader planning and control tool to its predecessor, the MRP 1. MRP 2 is a computer-based system that creates production schedules including the arrival of materials, machine and labor. MRP II defines what resources, what quantities, and at what time they will be necessary to carry out all business production processes.
MRP II constitutes the heart of manufacturing companies. It is an integrated method of operational and financial planning for manufacturing companies. In addition to answering questions about what, how many and when to purchase materials from MRP I, MRP II answers the following questions:
- What resources are necessary?
- What amount of resources?
- When will these resources be necessary?
MRP II identifies the capacity problems of the production plan. It resolves the divergences between the availability of resources and planned consumption.
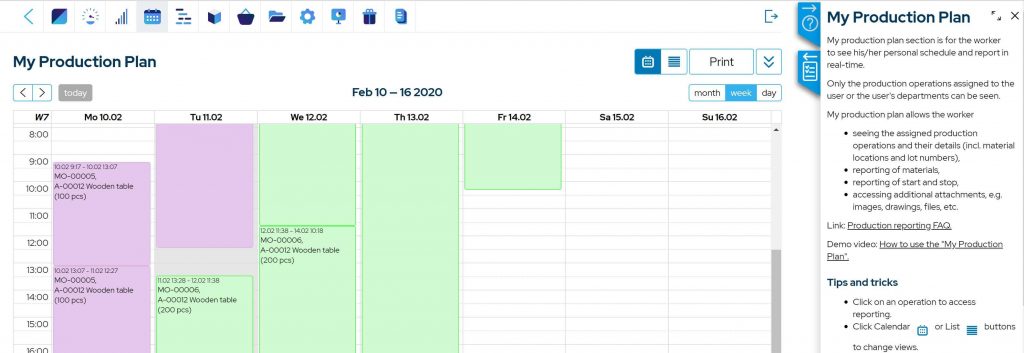
In addition to the MRP I tools, the MRP II calculates and solves:
- The planning of the manufacturing resources of the organization
- Ability to simulate production processes
- Optimized calculation of routes and work centers
- It is based on the study of demand and the market.
- It covers more departments, not only production but also purchasing, quality, financial, etc.
The inputs are:
- Work Progress Feedback, showing how the work has progressed, to all levels of the schedule so that the next run can be updated on a regular basis.
- Resource Scheduling, which is the calculation of resources to convert the raw materials into finished goods.
- Batching Rules takes into account the logic which batches are produced (i.e. EBQ, Lot for Lot, etc.)
- Rough Cut Capacity Planning (RCCP), to match the workload to the capacity available.
- Software extension programs, such as including sale orders processing, cost accounting, etc.
Advantages of MRP II
The advantages of using an MRP II System are shown below:
- All the advantages coming from MRP I
- Optimization of machinery usage and productivity improvement
- Coordination and control of production and inventories
- Ease of adaptation to order changes.
- Reduction of outsourcing and idle times
- Financial knowledge of planned and real production.
Differences between MRP I vs. MRP II
In summary, MRP I (Material Requirements Planning) is a material management system. It calculates when purchasing orders must be made to suppliers and the work orders released. It will provide the amount of material needed, according to the scheduled production.
In contrast, MRP 2 (Manufacturing Resource Planning) is a manufacturing system. It not only deals with the purchasing and production scheduling but also with the capabilities of the factory in aspects such as labor or machinery.
The next chart summarizes the main differences between the two systems:
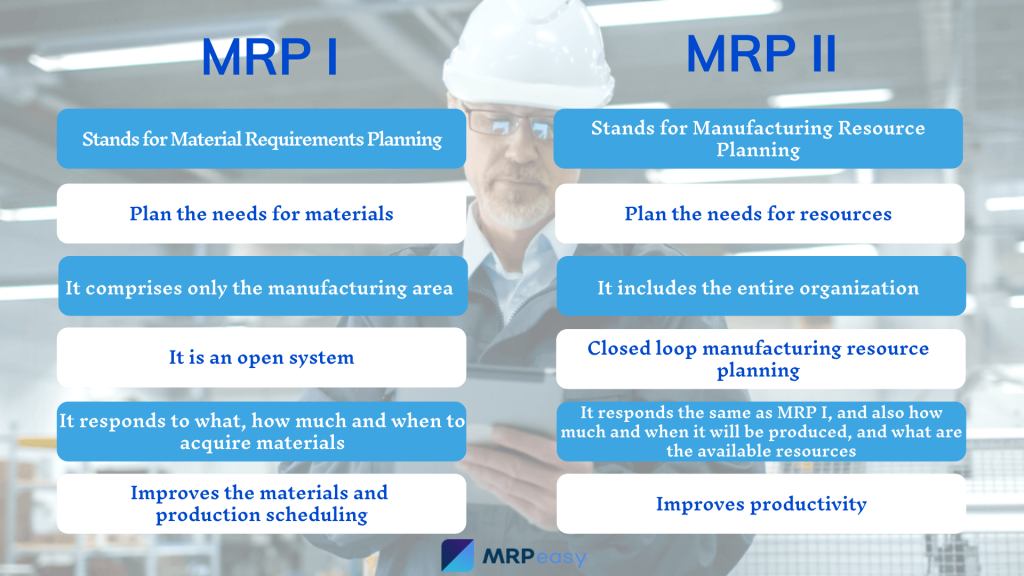