What Is Mass Production? A Comprehensive Guide
Mass production is used to produce large quantities of standardized products such as consumer goods. Here is a comprehensive guide to the benefits, processes, and tools of mass production.
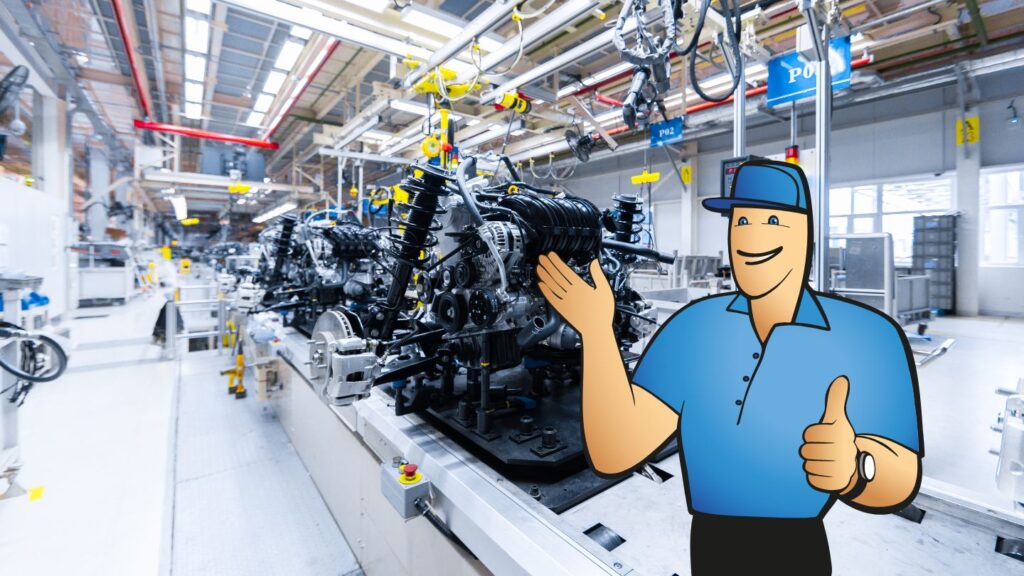
You can also listen to this article:
What is mass production?
Mass production refers to the manufacturing process designed to produce large quantities of standardized products. This method gained prominence during the American industrial revolution in the late 19th century, significantly altering the production landscape not just in the US but globally.
The concept of mass production is rooted in the principles of division of labor, mechanization, and automation. It allows for products to be mass-produced in large numbers through a meticulously organized sequence on the production line. This system was famously utilized by Henry Ford of Ford Motor Company, who pioneered the assembly line method to produce the Ford Model T. This innovation drastically reduced production times and costs, making automobiles affordable to the American public and subsequently transforming the automobile industry.
The assembly line technique introduced by Ford emphasized economies of scale, where the cost per unit falls as the volume of output increases. This approach not only maximized efficiency and high-volume production but also laid the foundation for modern flow production practices seen across various industries today.
Mass production vs. batch production vs. job shop manufacturing
Mass production
Mass production is characterized by the manufacturing of large quantities of standardized products. The process is highly automated and uses assembly lines where the product moves from station to station for different tasks to be completed sequentially. This method benefits from economies of scale, meaning the cost per unit decreases as output increases. It is ideal for products with high demand and little need for customization, such as automobiles and electronics. The emphasis is on speed, efficiency, and consistency.
Batch production
Batch production involves producing a specific quantity of a product in a single production run, known as a batch. This method is flexible and can be used to produce a variety of similar products with minor adjustments between batches. Batch production is suitable for smaller-scale operations compared to mass production and is effective for products that do not have continuous high demand but occasionally need to be produced in bulk, such as seasonal items or specialized tools. It strikes a balance between the tailored approach of job shops and the efficiency of mass production.
Read more about Batch Production.
Job shop manufacturing
Job shop manufacturing is geared towards making custom products or small batches of different products. This production type is highly adaptable to specific customer demands and involves a significant amount of manual labor and skilled workers. Job shops typically have versatile equipment that can be set up to perform different tasks as needed. This method is ideal for specialized industries such as custom furniture making or bespoke machinery manufacturing, where each product can be significantly different from the next.
Read more about Job Shop Manufacturing.
Mass production vs. mass customization
Mass customization is a production strategy that combines the cost benefits of mass production with the flexibility of individual customization, aiming to provide tailored products at a lower cost. This approach allows companies to produce a large amount of goods while still catering to individual customer preferences, striking a balance between affordability and personalization.
A classic example of mass customization is the automotive industry where customers can choose various features such as color, interior materials, and add-ons while the core product and manufacturing processes remain identical.
Read more about Mass Customization.
Benefits of mass production
Mass production has been a transformative force in the manufacturing industry, offering numerous advantages that include:
Cost efficiency
Mass production leverages economies of scale, reducing the cost per unit by spreading fixed costs over a larger number of outputs. This affordability extends from the manufacturer to the consumer, making products more accessible to a broader audience.
Increased productivity
The use of assembly lines and mechanization speeds up the production process, enabling the production of large quantities of goods in relatively short periods. This high-volume production capacity ensures that demand in mass markets can be met efficiently.
Standardization of products
The uniformity in the production process guarantees consistent quality and reliability across products. This standardization helps in maintaining quality control, reduces errors, and simplifies the training of workers.
Technological innovation
Mass production often drives technological advancements as companies seek more efficient ways to produce goods. Automation and continuous improvement in production techniques can lead to significant innovations within the industry.
Disadvantages of mass production
Although mass production could yield several advantages, it also comes with a certain set of complexities.
Initial capital investment
Setting up for mass production typically requires significant capital investment in machinery and infrastructure. This high startup cost can be a barrier to entry for smaller companies.
Inflexibility
The production line is designed for uniform output, which makes it less flexible in terms of adapting to changes in product design or customization demands from consumers. Any change requires major overhauls in the setup, which can be costly and time-consuming.
Dependency on volume
The success of mass production systems largely depends on continuous high demand. A reduction in demand can lead to surplus production, resulting in losses and inefficiencies.
Environmental impact
Mass production can lead to increased waste and environmental degradation if not managed properly. The focus on high-volume output can sometimes overlook the environmental costs of overproduction and resource depletion.
Worker discontent
The repetitive nature of tasks on an assembly line can lead to job dissatisfaction and reduced motivation among workers, which might affect productivity and overall workplace morale.
While continuing to be a dominant manufacturing methodology, balancing the advantages of mass production with its drawbacks is crucial for sustainable and responsive manufacturing practices.
Examples of mass production
Automobiles
The automobile industry is perhaps the most iconic user of mass production techniques, pioneered by Henry Ford with the Ford Model T. Today, companies like Toyota and Volkswagen use sophisticated assembly lines where cars are assembled from thousands of parts. The process includes the installation of engines, the fitting of body panels, and painting, all carried out in a systematic sequence to maximize efficiency and output.
Electronics
Consumer electronics such as smartphones and laptops are produced on a massive scale to meet global demand. For example, Apple’s iPhones are assembled in large factories where multiple automated stations are responsible for tasks like soldering components to motherboards, assembling screens, and packaging finished products. This sector often utilizes clean rooms and robotic automation to ensure precision and maintain quality.
Clothing
The textile industry uses mass production to create clothing at scale, particularly in countries like China and Bangladesh. Processes include fabric cutting using high-speed machines, automated sewing lines, and computer-controlled embroidery machines. This sector relies heavily on the division of labor, with different groups of workers specializing in specific tasks like sewing, hemming, or finishing.
Food and beverage
Mass production in the food industry includes the use of assembly lines for packaging, automated bottling for drinks, and large-scale bakery lines for bread and pastries. High-speed machinery is used for mixing, baking, and wrapping products. An example is the mass production of canned beverages, where liquids are filled into cans, sealed, and then pasteurized.
Pharmaceuticals
Drug manufacturing is a critical area of mass production, involving the synthesis of active ingredients, followed by formulation into final products like tablets or capsules. This process is highly controlled and automated to ensure compliance with stringent health regulations. High-volume batch production ensures that medications are available for global distribution.
A step-by-step guide to the mass production process
Mass production is a manufacturing method that allows for the large-scale, high-volume production of goods using a highly organized and standardized process. This method is characterized by specialization, mechanization, and economies of scale, ensuring high production efficiency and consistency. Here’s how it typically unfolds:
Step 1: Design and development
Before the manufacturing process begins, the product is designed with mass production in mind. This includes the use of interchangeable parts and standardized designs to simplify the assembly and ensure consistency. Machine tools are prepared to handle specific tasks automatically.
Step 2: Procurement of raw materials
The production process starts with the procurement of raw materials, which are often bought in bulk to benefit from economies of scale. These materials are stored and prepared for assembly, ensuring they meet the quality standards necessary for mass production.
Step 3: Production planning
This step involves detailed production planning to maximize efficiency. The flow production technique is often employed, where the work-in-process smoothly transitions from one stage to the next without interruptions, mimicking a continuous flow.
Step 4: Division of labor
In a typical mass production system, tasks are divided among workers and machines in a way that each performs a specific role (specialization). This division of labor helps in optimizing skills and speeds up the production process.
Step 5: Mechanization and automation
The actual manufacturing process involves a high degree of mechanization and automation. Machine tools and robotic systems perform repetitive tasks, which increases production speed and precision.
Step 6: Quality control
Throughout the production process, quality control is a continuous priority. At various stages, products and components are checked for defects or deviations from the desired specifications. This ensures that the final products maintain a high standard of quality and reliability.
Step 7: Assembly
Components are assembled using a production line or assembly line method, where each workstation adds parts or performs specific tasks until the product is complete. This is crucial for complex products like automobiles and electronics, where many components must be accurately assembled.
Step 8: Testing
Once the products are assembled, they undergo testing to ensure they function as intended. This step is essential to maintain consumer trust and regulatory compliance.
Step 9: Packaging and shipping
Finished products are then packaged and prepared for shipping. Packaging must protect the product and also serve marketing purposes. The products are then distributed to retailers or directly to consumers.
Step 10: Feedback and improvement
Finally, feedback from consumers and performance data collected during the manufacturing and sales processes are analyzed to make improvements in future production cycles.
Mass production methods and tools
Mass production is based on the division and specialization of labor and the use of technology. Assembly lines and automation are some of the most widely used tools in mass production:
- Assembly line production. Perhaps the most iconic method associated with mass production, the assembly line allows for the efficient construction of similar products by moving the item being built between workstations. Each station is manned by skilled workers or automated machines that perform specific tasks sequentially, ensuring high efficiency and consistent output.
- Automation and robotics. New technology in the form of manufacturing automation and robotics plays a critical role in modern mass production. These technologies perform repetitive tasks previously done by humans, increasing precision and output while reducing the likelihood of errors. Automation is particularly valuable in environments that demand high accuracy or involve hazardous tasks.
- Manufacturing ERP software. Manufacturing ERP plays a crucial role in increasing the efficiency and effectiveness of mass production operations. By integrating various business processes, ERP systems provide a comprehensive, real-time view of core business activities, helping manufacturers manage and streamline their operations.
These mass production methods are integral to the modern manufacturing landscape, enabling the production of high volumes of products while maintaining quality and reducing costs.
Key takeaways
- Mass production involves the manufacturing process designed to produce large quantities of standardized products. It became prominent during the American industrial revolution and is characterized by the principles of division of labor, mechanization, and automation, as exemplified by Henry Ford’s assembly line for the Ford Model T.
- Unlike mass production, batch production involves producing a specific quantity of a product in a single run. Job shop manufacturing is tailored for custom products or small batches. Mass customization, however, merges the low-cost benefits of mass production with the flexibility of customization, allowing for the production of large amounts of goods tailored to individual preferences.
- Mass production offers numerous advantages including cost efficiency, increased productivity, and standardization of products, all of which lead to higher profits. However, it also has disadvantages such as high initial capital investment, inflexibility, dependency on volume, environmental impact, and potential worker discontent.
- Key methods include assembly line production and automation which emphasize speed, efficiency, and consistency. These methods are crucial for maintaining high-volume production capabilities and ensuring that products meet consistent quality standards. Manufacturing ERP software helps manage mass production processes and planning more efficiently.
Frequently asked questions
Companies choose a production method based on several factors including product demand, market variability, production volume, and the level of customization required. They assess the cost implications, potential efficiency gains, and the flexibility needed in their production processes to meet consumer needs effectively.
Companies like Nike with their Nike By You program, which allows customers to customize sneakers, and Dell Computers, which offers customizable PCs, are examples of successful mass customization. These businesses have harnessed online platforms and advanced manufacturing technologies to offer personalized products without sacrificing production efficiency.
Modern mass production has been enhanced by innovations such as robotics, artificial intelligence, and 3D printing. Robotics and automation have streamlined the assembly line, reducing labor costs and improving precision, while AI has optimized production planning and logistics to increase overall efficiency.
You may also like: Warehouse Management – A Comprehensive Guide