Manufacturing Software for Electronics Industry
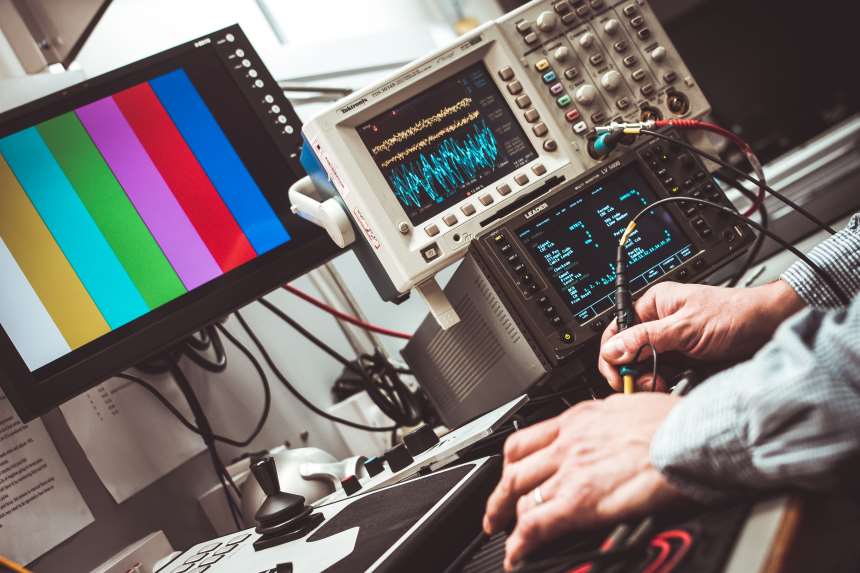
A key difficulty in electronics manufacturing arises from the need to manage a lot of information. This is where manufacturing software for the electronics industry comes into play.
For example, finding the lead time of a product assembled from hundreds of distinct parts, which all have various lead times, is a difficult process done manually – hundreds or even thousands of pieces of information need to be considered.
You can also listen to this article:
The challenges in electronics manufacturing
The greatest issues typically arise from having to manage a vast amount of information:
- Complex products
- Different versions, configurations, or variations of a product
- A vast number of parts
- Alternatives from different manufacturers for a part
- Multiple vendors for each part, complex purchase terms
- Documentation, certificates, drawings, images etc.
- Tracking all movements of parts and products
- Tracking individual parts and products with serial numbers
- Etc.
Due to the nature of the electronics industry it is important to control and document every production phase in order to get high quality output and be able to identify problems beforehand.
Once the products are made, it is vital to know for each product:
- When was the product made, by whom and on which machines
- Which specific components were used
- From where and when parts were purchased
- If documentation was received with the parts; e.g. certificates, drawings
- Etc.
Since all the before-mentioned need to be considered, it can be very complicated to schedule and document all the processes manually.
However, managing all that information properly, you can make sure that:
- All costs for a product are properly considered and anticipated
- The promised lead time to a customer is realistic
- All parts are in stock, or coming at the right time
- There will be no surprises.
This is the reason why electronics companies choose various cloud manufacturing software to take care of the processes mentioned above.
What makes great manufacturing software for the electronics industry
The biggest advantage of good manufacturing software is that it allows you to know exactly when you can deliver your products and how much it will cost you.
Receiving orders, quoting, planning production, planning purchases, managing the warehouse… Everything can be done in one easy-to-use system.
Below is a list of functions that are essentially important for electronics manufacturing:
- Manufacturing resource planning, planning materials and scheduling operations (MRP)
- Shop-floor reporting (MES)
- Warehouse and supply chain management (WMS, SCM);
- Managing minimal stock and purchase requirements
- Handling multiple purchase options for parts
- Full lot and serial number traceability
- Multi-level Bills of Materials (BOM)
- Products with parameters (Matrix BOM)
- Managing part equivalents & substitutions
- Quality Control (QC)
- Ability to handle files, drawings, images, certificates etc.
- Barcoding
- Return Merchandise Authorization (RMA)
- And much more!
Briefly, on main functions and how they are handled in most MRP systems for electronics industry:
Multi-level bill of materials and multi-level production planning
Usually, there is no limit as to how many levels your Bill of Materials can have. Creating a multi-level Bill of Materials should be very simple, like including the sub-assembly (which already has its own BOM) and you have a multi-level BOM structure.
If the BOM is lengthy, most MRP systems can import it (or even many BOMs at once).
The production planning takes everything into account: the current production schedule, availability of needed workstations, if sub-assemblies need to be produced (or if these are available in stock), which parts need to be purchased and their lead times, etc. Also, it manages all part bookings (i.e. allocations/reservations), so it’s certain that everything is available when needed.
In some cases, it is possible to nest production operations of the sub-level assemblies in the manufacturing order of the top-level item. That is, there is no need to clutter the production schedule with many separate manufacturing orders, where many represent different assemblies of the same product. (Learn more about BOM software.)
Material planning, knowing what to build or purchase
Material planning functionality makes sure that you have all parts available, or ordered for each order in the system. Specific parts and products are reserved against each order – be it products for a customer order, or parts and assemblies for a manufacturing order. It also considers which items are expected to arrive in the future.
If you are low on stock, some parts need to be purchased, or some produced – make sure that your manufacturing software has this functionality and provides a complete reporting of all critical items on hand.
Such reports show the purchasing and manufacturing requirements, items for which manufacturing has not been scheduled, or purchase orders raised yet. You can directly create and auto-populate the orders with all the required information.
Usually, such reports can be located in the Stock/Inventory and Procurement/SCM sections. The report in the Stock section shows which items need to be purchased or scheduled for manufacturing; in the Procurement section, it shows solely what needs to be purchased.
It’s a great time-saving and a fool-proof tool for the production planner and the purchaser.
Stock lot and serial traceability
Stock lot and serial number traceability helps to make sure that product history is properly documented. It tracks all lots and serial number related information automatically.
The simplest explanation is that a stock lot is one batch of some product. For example, each time a batch of a product is purchased, a new batch is sent to replenish; therefore, a new stock lot number (aka “a batch number”) is created to identify it.
You may have many stock lots of the same material – purchased at various times, with different costs, possibly from different vendors, with different expiry dates, stored in separate locations/shelves, some of which have certificates, files or notes attached, etc.
Since in one lot there may be many individual products, serial numbers provide the ability to track each individual product specifically, look up its individual history, know which customer has it, record issues, etc.
Managing part equivalents
It’s common that there are parts that are identical in function and form but come from different manufacturers. These parts can be interchangeably used, depending on current availability. Good manufacturing software allows automatic allocation of these parts, so there is no manual lookup or decisions necessary, while traceability still remains.
A generic part, which will shelter all these parts which are interchangeable, can be created, but from different manufacturers, or vendors. In the part details, many different purchase terms can be set up, which will list all manufacturer-vendor combinations and purchase details with lead times etc.
Based on the stock lot tracking, it is easy to trace back when each part in a product was purchased, which manufacturers part it was etc.
Configurations and variations of a product
An important topic is handling a product that has variations; either there are alternative builds, or the product is configurable. For this, there are several alternatives of how this can be done.
In many cases, the BOM with Parameters (aka Matrix BOM) functionality will be perfect, letting you effectively manage many different build specifications of a product. Products can be given parameters, and based on the selected parameter values the software builds the correct production BOM.
This is achieved through setting up relations between parameter values (or combinations of values) and specific parts. Based on value selection, the correct parts are chosen for the specific build.
This is a great function, since manually defining all different variations (and looking these up later) is a very time-consuming process. The BOM with Parameters function will save a lot of time when there are many configurations or variations to handle.
If BOM with Parameters is not used, then alternatively, the version control system can be used; or several BOMs for a product or articles can be configured.
In conclusion
Good manufacturing software for electronics industry connects all sides of the operations from sales through warehouse control to production and purchase planning and reporting.
Software as a service (SaaS) is easy to pick up, and it will prevent many mistakes that occur without having a good system in place. Even more, it will streamline your company’s operations and cut in half the time spent on getting organized. Choose the right cloud-based manufacturing software to get started with your trial right away.
Further reading connected to this topic: