Quality Assurance in Manufacturing – QA Best Practices for SMEs
Next to how much you produce, the quality of products is an equally important side of the coin in manufacturing. Quality assurance serves as the process of maintaining consistency, preventing defective products, and adhering to industry regulations in manufacturing goods.
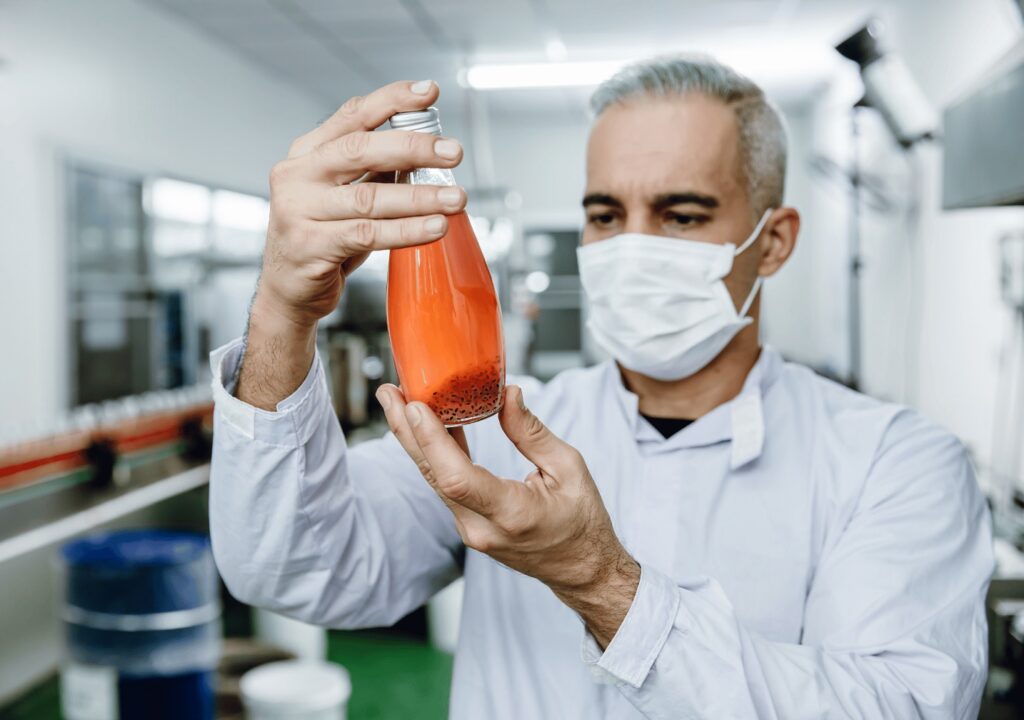
You can also listen to this article:
What is quality assurance in manufacturing?
In manufacturing, quality assurance (QA) is a systematic process aimed at guaranteeing that a company’s goods meet specified requirements and fulfill customer expectations. Product quality is not only dependent on good manufacturing processes that produce defect-free goods. It is also about high-quality materials, timely supply chain movements, well-organized facilities, well-trained staff, and other business aspects that together work toward achieving and maintaining consistent customer satisfaction.
The QA process is a set of practices that a company implements and follows to ensure consistently high product quality. It’s a proactive component of quality management, focused not only on products but also on fulfilling quality requirements. Defining and implementing processes, training teams, or choosing the right tools to yield quality products all fall under it. QA comprises one part of the larger quality management process, with the other part being quality control.
Quality assurance vs. quality control
Quality assurance and quality control (QC) are often intertwined yet distinctly different aspects of quality management. QA encompasses a broad spectrum of the quality system, focusing on providing confidence that quality requirements will be met. This confidence extends internally to management and externally to customers and regulatory bodies.
In contrast, quality control is more about fulfilling quality standards as set forth by QA. QC, then, can be seen as a more practical subset of quality management that focuses on the operational techniques and activities used to fulfill quality requirements. In other words, QC comprises the practices that ensure that processes follow QA measures. In manufacturing, quality control mostly revolves around inspection and following steps in the manufacturing process that test product quality.
What is quality management?
In manufacturing, quality management is the systematic process of designing a company’s QA processes as well as managing its quality control efforts. It is focused on implementing quality and compliance-related processes and managing quality systems.
Therefore, quality management integrates QA and QC into a single quality management system (QMS). Quality management is about adhering to standards but also ensuring that all stages of design, development, manufacturing, and delivery meet the standards. As outlined above, quality management is crucial in safeguarding not just the finished products but also the quality of raw materials and components involved in the process.
Quality management systems
In modern manufacturing, all the various quality-related activities are brought together into a unified quality management system. Quality management systems (QMS) are formal frameworks that guide manufacturing companies in achieving and maintaining desired quality standards. These systems encompass a wide range of activities, including planning, assurance, control, and improvement of quality. By integrating a quality management system, manufacturers ensure consistency, efficiency, and continual improvement in their production processes.
A QMS often involves the implementation of internationally recognized quality standards. These are made available by accreditation organizations, most notably the International Organization for Standardization, or ISO. For manufacturers, the ISO 9000 series of standards are among the most instrumental quality-oriented standards. Running as the root of a well-implemented QMS, ISO 9000 is instrumental in aligning the quality objectives of a company with its operational processes and regulatory requirements.
Continue reading about ISO standards in manufacturing.
Implementing QA in manufacturing
Implementing quality assurance in manufacturing involves several key steps. Here’s an overview of the essential processes. Each of these plays a vital role in building a robust QA framework that ensures high-quality products.
- Establish a Quality Management System. Develop and document processes, procedures, and standards to create a structured QMS. This system serves as the foundation for consistent quality control across all manufacturing operations. Adopting ISO9000 is a viable first step in developing a QMS.
- Train employees. Provide comprehensive training for personnel on quality standards, procedures, and the use of relevant tools and equipment. Well-trained employees are essential for effectively implementing and maintaining QA practices.
- Optimize processes. Conduct process mapping to identify critical control points, optimize workflows, and increase output consistency. These usher in quality improvement by enhancing production efficiency and reducing the likelihood of defects.
- Ensure quality materials. Work closely with suppliers to establish and maintain quality expectations for raw materials and components. Implement supplier quality management practices, including regular inspections and audits.
- Integrate QC measures. Incorporate quality control measures at different production stages. This includes in-process inspections, testing, and final product checks to identify and correct any deviations from quality standards.
- Enhance the traceability effort. Adopt manufacturing software with built-in traceability. This software is crucial for maintaining accurate records of manufacturing processes and product specifications, allowing for quick responses to quality issues.
- Conduct audits and implement continuous improvement. Regular internal and external audits assess the effectiveness of the QA system. These help identify areas for improvement, ensuring compliance with standards and fostering a culture of continuous quality enhancement.
- Define methods for improvement. A key feature of an effective quality management system is process improvement. Selecting a structured methodology such as Lean or Six Sigma tools like DMAIC (Design, Measure, Analyze, Improve, Control) or others will allow for data-driven findings that can be used in process optimization.
The importance of QA in manufacturing
Next, let’s go through some of the most important facets of QA in manufacturing.
- Reduced defect rate. Reducing the defect rate is a primary goal of quality assurance in manufacturing. Through process monitoring and product testing, QA helps identify and rectify potential issues before they escalate into major defects. This proactive approach is crucial for averting poor-quality products, ensuring customer satisfaction, and safeguarding the brand’s reputation.
- Compliance. Adherence to regulations and industry standards is critical in manufacturing. Quality assurance systems play a key role in this, ensuring that end products meet the necessary safety, quality, and other regulatory standards. For example, in the medical device industry, strict adherence to FDA guidelines through QA processes is essential for patient safety and market access.
- Customer confidence and stakeholder trust. Quality assurance directly impacts customer confidence and stakeholder trust. By consistently delivering high-quality products, manufacturers can strengthen their reputation and foster long-term relationships with customers and business partners. This is not limited to the end consumers but extends to both suppliers, investors, and regulatory bodies, all of whom play a crucial role in establishing a market foothold.
- Resource, time, and cost savings. Effective quality assurance contributes significantly to resource optimization. Early identification of defects and efficient and safe production protocols help to avoid costly mistakes and avoid wastage of materials. This optimization not only boosts the bottom line but also aligns with sustainable manufacturing practices, an increasingly important aspect in today’s eco-conscious market.
- Improved production efficiency and consistency. Quality assurance contributes to enhanced production efficiency and consistency. Through systematic monitoring and control of manufacturing processes, QA helps in optimizing operations, leading to faster turnaround times and higher throughput. This boosts productivity and enables manufacturers to respond quickly to market demands and customer needs.
- Enhanced process control. Process control and statistical process control lie at the heart of quality assurance. This involves establishing standard operating procedures and consistent quality checks, ensuring that every aspect of production is closely monitored and controlled. This level of control is crucial for detecting deviations from standards early. It allows for immediate corrective actions, thereby helping to maintain the integrity of the production process.
- Continuous improvement. A focus on continuous improvement is a hallmark of an effective quality assurance system. By continually assessing and refining processes, manufacturers can adapt to new challenges and technological advancements. This proactive approach to quality management not only helps in maintaining current quality standards but also in identifying opportunities for innovation and improvement, keeping the company competitive in a dynamic market.
Quality assurance trends for SMEs
In the world of manufacturing, SMEs face both challenges and opportunities in implementing QA. Limited resources necessitate a strategic approach. This often means focusing on areas with the most significant impact on quality and customer satisfaction while balancing the constraints of budget and personnel. While implementing some form of QMS is increasingly vital across the manufacturing industry, it remains a challenging prospect due to these limitations.
The role of digital transformation is increasingly pivotal in adopting QA systems for SMEs. The advent of Industry 4.0 technologies like the Internet of Things (IoT), big data analytics, or cloud computing is wholly reshaping manufacturing. This enables advanced levels of automation and precision in QA processes, promising to facilitate early defect detection, reduce waste, and improve product quality.
The accessibility of QMS through cloud-based Software as a Service (SaaS) models is a game-changer. Particularly as some MRP systems and manufacturing ERPs have started to incorporate quality control mechanics into their packages. This provides SMEs with sophisticated tools for implementing robust quality management without the need for substantial investments.
Looking to the future, QA in manufacturing is set to accelerate in evolution with further digital advancements. Automation, AI-driven analytics, and the integration of virtual and augmented reality tools are set to play large roles in QA processes. This is expected to enable more predictive and preventive approaches to quality management, revolutionizing training and inspection processes. SMEs that effectively integrate modern QA practices stand to gain in efficiency, product quality, and customer satisfaction.
Manufacturing quality assurance best practices for SMEs
Finally, let’s take a look at six QA best practices for small and medium manufacturing companies.
Implement a manufacturing ERP system
Incorporating a manufacturing Enterprise Resource Planning (ERP) system is essential in enhancing QA efforts for SMEs. These systems streamline data management and often include built-in Manufacturing Execution Systems (MES) and quality control functionalities. This allows for real-time monitoring and management of the production process, ensuring adherence to quality standards. Many ERP systems can be further enhanced through API integrations with external solutions, offering flexibility and adaptability to meet specific operational needs.
Standardization and variability reduction
A key element for increasing consistent quality is standardizing the manufacturing process. This involves creating and maintaining updated Standard Operating Procedures (SOPs), getting certified (like ISO 9000), ensuring equipment maintenance, and conducting regular audits. Additionally, tools like the Six Sigma methodology can be instrumental in maintaining consistent quality standards. Lean Manufacturing also plays a crucial role in eliminating non-value-added activities and reducing manufacturing waste, which includes excesses in transport, storage, production, and processing, as well as issues like rework, delays, and defects.
Teamwork and continuous training
People are the most valuable asset in any organization. Creating a teamwork atmosphere and investing in continuous training are essential for increasing both individual and organizational capabilities. A focus on creating a safe and clean working environment also contributes to higher employee productivity. By nurturing a skilled and cohesive team, SMEs can transform raw materials into high-quality finished goods more efficiently.
Strategic KPIs and communication
The implementation of strategic manufacturing Key Performance Indicators (KPIs) is crucial for translating organizational vision and goals into measurable and achievable targets. Effective communication is essential to ensure that these metrics contribute positively to the organization without adversely affecting other departments. Balancing short-, medium-, and long-term goals, like sales volume and Return on Investment (ROI), is important for the sustainable growth of SMEs.
Building strong partnerships
Strengthening relationships with the right suppliers and customers is key to creating mutual benefits and achieving business goals. SMEs should focus on being customer-oriented, ensuring that their strategies align with customer needs rather than internal processes alone. Establishing strong vendor management can lead to synergistic outcomes and contribute to the overall success of the business.
Continuous improvement culture
Adapting to changing customer preferences, technological advancements, and market dynamics is crucial for SMEs. Implementing a culture of continuous improvement involves regular documentation updates, process simplification, and the elimination of redundant checks and bureaucratic procedures. A cloud manufacturing ERP can be a foundational tool in defining, improving, and sustaining operational goals by facilitating information sharing, effective communication, and improved manufacturing practices.
Key takeaways
- Quality assurance (QA) is a systematic process focused on ensuring that products meet set requirements and customer expectations. It encompasses more than defect-free manufacturing, including high-quality materials, efficient supply chain management, trained personnel, and more.
- QA and quality control (QC) are distinct yet related aspects of quality management. While QA involves planning and systemizing processes to prevent quality issues, QC is about testing and verifying that products meet quality standards during and after production.
- Key steps in implementing quality assurance include establishing a QMS, training employees, optimizing processes, ensuring quality materials, integrating quality control measures, enhancing traceability, and conducting regular audits for continuous improvement.
- Adopting ISO9000 and implementing an MRP system or manufacturing ERP with built-in quality control functionalities is perhaps the surest way toward effective QA for small and medium manufacturing businesses.
Frequently asked question
Quality assurance (QA) is crucial in production as it ensures products meet specified requirements and customer expectations. It helps in maintaining product consistency, reducing defects, and adhering to industry regulations, ultimately leading to higher customer satisfaction and cost savings.
In manufacturing, quality assurance and quality control serve different roles. QA focuses on preventing defects by planning and systemizing processes, while QC involves testing and verifying that products meet quality standards during and after production. In short, QA is about process management, while QC is about product assessment.
An example of quality assurance in manufacturing is the implementation of a Quality Management System (QMS) like ISO 9000. This involves establishing standardized processes, regular employee training, and consistent monitoring of operations to ensure products consistently meet quality standards.
QC involves inspecting and testing products at various stages of the production process. It checks for defects and ensures the final product meets established quality standards. QC activities might include in-process inspections, material testing, and final product reviews to identify and address any quality issues.
You might also like: How to Eliminate Bottlenecks in Manufacturing?