Manufacturing Overhead – How Indirect Costs Affect Your Bottom Line
Manufacturing overhead is an essential part of manufacturing cost accounting and should be a key factor in determining your products’ prices. In this post, we review manufacturing overhead basics and see how manufacturing software can help streamline cost accounting.
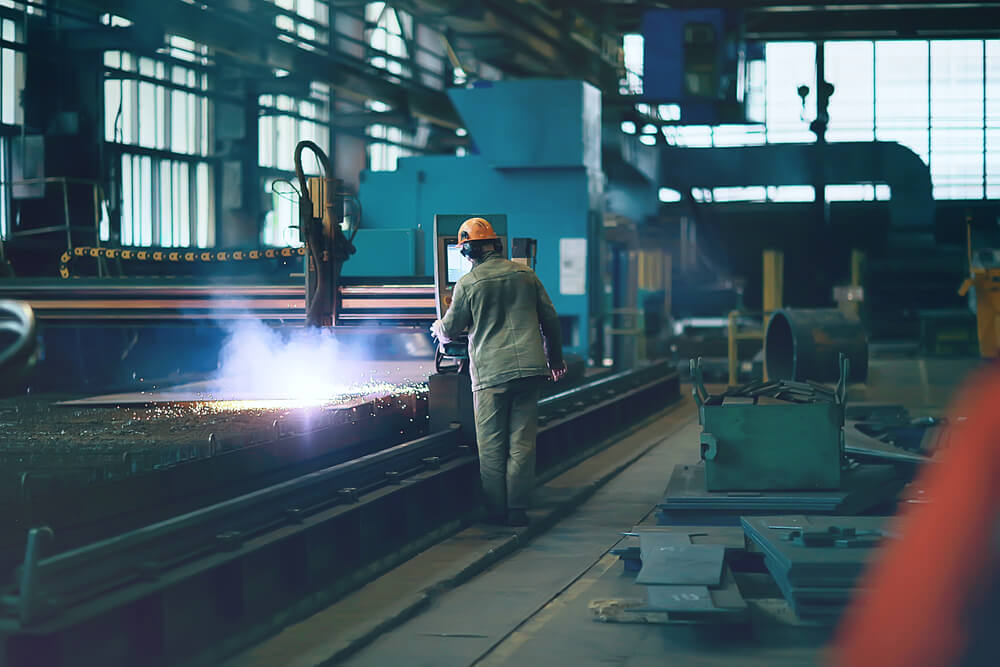
What is manufacturing overhead?
Manufacturing overhead, or factory overhead, is a company’s indirect cost of production. Indirect costs are all expenses that can’t be directly attributed to producing goods or services but are still needed to keep a company functioning. Manufacturing overhead makes up the part of indirect expenses that are related to the manufacturing process.
Manufacturing costs are together made up of direct labor costs, raw material costs, and manufacturing overhead costs. The latter includes things like factory utilities, cleaning supplies, machine depreciation, and even salaries of non-production staff. In other words, everything that manufacturing couldn’t function without that isn’t direct labor or direct materials.
While selling, marketing, managerial, and other general business expenses are also types of overheads, they aren’t deemed manufacturing overhead. These can usually be added to the income statement as general expenses. Factory overheads, on the other hand, need to be included in both the cost of goods sold (COGS), finished goods inventory, and the work in process (WIP) inventory accounts, as required by the Generally Accepted Accounting Principles (GAAP).
Next, let’s delve into the various classifications of manufacturing overheads.
Fixed vs. variable vs semi-variable overheads
Depending on type and behavior, production overheads can be fixed, variable, or semi-variable. This distinction is important for accounting purposes and for accurately calculating overhead rates.
Fixed overheads
As the name implies, fixed overheads remain the same regardless of production volume and other fluctuations in business activities. Fixed overheads are usually preset based on real data from previous periods.
Examples of fixed costs include machinery or production facility depreciation, property taxes and rent, labor costs of the clean-up crew, utility bills for keeping the factory lights on, and certain types of MRO (maintenance, repair, and operations) inventory, such as safety equipment.
Variable overheads
Variable overheads change with shifts in production volume. The more manufacturing orders come in, the greater the variable overhead cost. Tracking variable costs is important to enable more control over fluctuating costs and ensure better financial planning and pricing decisions.
Examples of variable overheads include the overtime costs of indirect labor, all sorts of materials used in manufacturing that aren’t part of products’ bill of materials (BOM), such as fixtures and consumables, electricity or gas bills for machinery, and MRO supplies like machine repair parts or packaging materials.
Semi-variable overheads
Some overheads can also be deemed semi-variable to further increase the accuracy of the manufacturing overhead rate. These costs partially depend on production levels but incur a base cost regardless of production activity.
A good example of semi-variable overhead would be subscription-based machinery or storage rent. Here, regular lease payment is due regardless of usage, but additional costs are incurred based on exceeding a usage threshold.
Examples of manufacturing overhead costs
Manufacturing overhead costs include all expenses indirectly related to the manufacturing process. These are usually divided into five types of overheads: indirect labor, indirect materials, rent and utility costs, depreciation, and financial costs.
Indirect labor
Indirect labor costs consist of the wages and other fees of employees who work in the manufacturing department but whose jobs don’t directly count toward the labor put into manufacturing a product. Indirect labor constitutes all of the expenses related to the payroll of these employees.
Indirect labor costs include the salaries, vacations, bonuses, etc., of quality control specialists, production supervisors, plant managers, production planners, maintenance workers, factory security, janitors, etc.
Indirect materials
Indirect materials are items and consumables that are used in production but are not part of any specific product’s bill of materials (BOM). This is either because they are difficult to track, they are not used directly in the manufacturing process, or they are used sporadically or in insignificant quantities per product.
Indirect material costs can include expenses for lubricants, adhesives, fittings and fasteners, disposable equipment, cleaning supplies, tools, and equipment repair parts.
Rent and utilities
Facility rent and utility costs for heating, power, and water also fall into the manufacturing overhead category. While rent stays mostly the same throughout the year, utilities often vary depending on consumption. For this reason, rent is mainly fixed, whereas most utilities are considered a variable or semi-variable overhead expense. Indirect utilities also include the internet bill and the subscription to your manufacturing software.
Depreciation
Everything that is used will gradually lose its value—manufacturing facilities and machinery are no exception. Depreciation cost is used to account for the deterioration of the fixed assets related to manufacturing in a company, including those of factory buildings, furniture and fixtures, computer equipment, machinery and workstations, and vehicles.
Depreciation can be calculated using the straight line or declining balance methods.
- In the straight line method, an asset’s end-of-life value (salvage value) is subtracted from its initial cost. The result is the total amount that can depreciate. This is then divided by the asset’s expected lifespan to arrive at the asset’s yearly depreciation.
- In the declining balance method, a fixed percentage is applied to the asset’s book value each year, resulting in higher depreciation early on and lower amounts later. This method doesn’t account for salvage value until the end, so depreciation decreases over time but never fully depletes the asset’s value.
Financial costs
Finally, manufacturing overhead also includes various financial costs related to the production process. Prominent examples are property taxes, legal fees for compliance audits, various insurance policies related to manufacturing, inventory, and supply, etc.
Allocating manufacturing overhead
As manufacturing overheads are an important cost driver, precisely allocating them to production is key in determining a viable selling price for your products. It’s also important for ensuring accurate profit margins and helping to identify areas for cost control or efficiency improvements.
Let’s look at the three main ways overhead allocation is conducted.
Estimated overhead
Estimated overhead is the predetermined total manufacturing overhead cost at the start of a financial period. It is allocated to production activities in advance to help budget and plan for the coming year. Estimated overhead is based on actual overhead costs from previous years as well as production forecasts.
While this approach helps streamline budgeting, estimated overhead is only a projection. The actual costs will vary, requiring adjustments during the reconciliation process at the end of the period.
Applied overhead
Applied overhead refers to the estimated overhead expenses applied per unit of production during an accounting period. This is applied using a predetermined overhead rate, which is calculated based on direct labor hours or machine hours.
This method lets companies estimate job costs quickly by assigning overhead costs alongside direct materials and labor. However, it doesn’t provide perfectly accurate production cost estimates, as the actual overhead often differs from the applied rate. Therefore, this overhead allocation must be reconciled at the end of the financial period to align financial statements with actual costs.
Actual overhead
Actual manufacturing overheads are the real, measured indirect costs of the production process. Since many of these are difficult to measure in real-time, actual overhead is usually calculated retrospectively. It is then used to reconcile applied overhead and the actual costs in the books.
Modern automation tools, IoT devices, and software solutions are improving the ability to approximate overheads more accurately. For example, RFID tools can measure secondary materials used in processes, and sensors installed on manufacturing equipment can precisely track utility consumption with manufacturing operations.
Check out our article on applied overhead vs. actual overhead for a more comprehensive take.
How can MRP software streamline cost accounting?
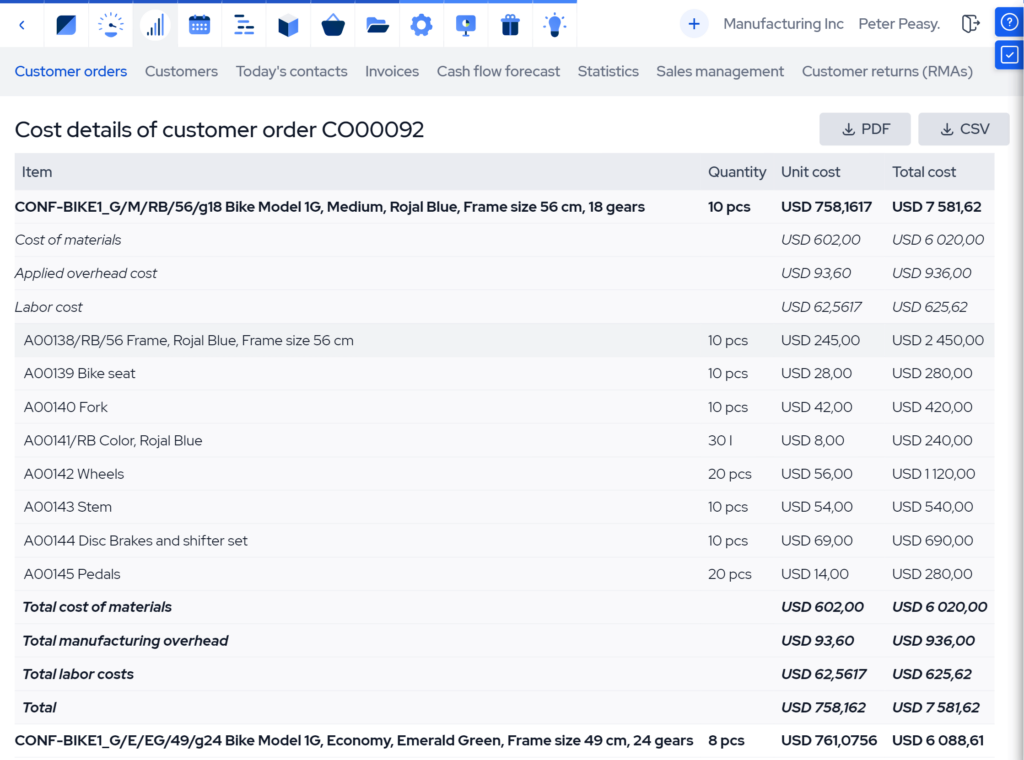
Modern manufacturing software is invaluable for automating cost accounting and improving the accuracy of overhead allocation. By streamlining data collection and applying predetermined rates automatically, MRP systems ensure that overhead costs are distributed correctly across production orders, leading to more precise cost tracking and financial transparency.
- Tracks production costs. MRP software helps track production costs by automatically applying predetermined overhead rates to each order. This ensures a more accurate cost allocation, increasing transparency and efficiency in managing indirect expenses across production activities.
- Perpetual inventory management. MRP software continuously tracks inventory movements, ensuring accurate records of materials and goods in real-time. This helps keep the cost of goods sold (COGS) account accurate, provides better visibility into production costs, and improves financial reporting throughout the production cycle.
- Estimates production costs and lead times. MRP systems use historical data and real-time inputs to forecast future production costs and estimate lead times more accurately. This enables manufacturers to plan better and avoid unexpected cost overruns or delays in production.
- Integrates the production effort with financial apps. MRP software can seamlessly sync with financial applications like Xero or Quickbooks, enabling smooth data flow between production and finance and accurate real-time financial reporting.
Key takeaways
- Manufacturing overhead costs are indirect production costs
that cannot be traced directly to the manufacturing of products. - Manufacturing overhead can be divided into five distinct groups: indirect labor, indirect materials, rent and utilities, depreciation, and financial costs.
- Overheads can be fixed, variable, or semi-variable. For example, the wages for warehouse security are fixed regardless of volume, whereas the cost of packaging rises proportionally depending on the number of units produced.
- Allocating overhead costs is mostly done by estimating the overheads for an upcoming period and applying them per produced unit using direct labor hours or machine hours.
- Actual overhead is calculated after a financial period and used to reconcile applied rates with actual numbers.
- MRP software hugely simplifies and automates production costing, cost accounting, and overhead allocation, thereby saving time and increasing the efficiency of manufacturing businesses.
Frequently asked questions
To calculate manufacturing overhead, add up all indirect costs associated with production, such as utilities, maintenance, depreciation, and indirect labor. These costs are then divided by a cost driver, like direct labor hours or machine hours, to allocate them to production.
Manufacturing overhead is typically recorded as an expense account and is part of the cost of goods sold (COGS). It includes indirect production costs and is allocated to work-in-process (WIP) and finished goods inventory during the production process.
Factory overhead includes all indirect costs of production that are not directly tied to a product. An example is the cost of electricity to run machinery in a factory, which supports production but isn’t directly part of any specific product.
To reduce manufacturing overhead costs, focus on optimizing efficiency by minimizing waste, improving energy usage, and automating routine tasks. Investing in modern MRP software can help you track indirect costs in real-time, identify areas of inefficiency, and streamline processes to lower expenses over time.
You may also like: Inventory Costs – A Quick Overview