Manufacturing Execution System Software as a Cloud-Based Solution
From remote access and better scalability to integrated data management – there are numerous advantages to having Manufacturing Execution System (MES) software as a cloud-based solution.
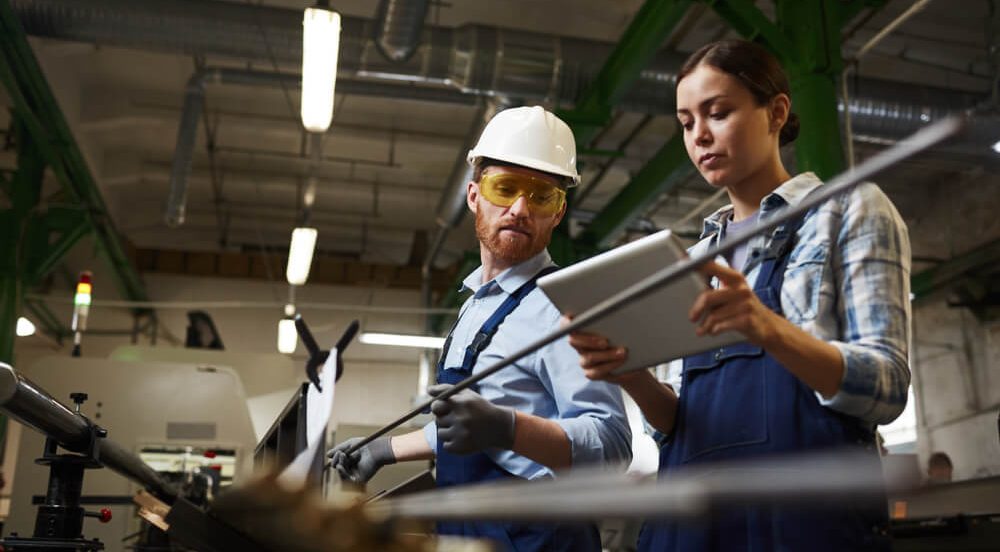
What is manufacturing execution system (MES) software?
Manufacturing execution system software (MES) is a digital system used to manage, monitor, and control the production process on the factory floor. An MES acts as a bridge for data exchange between the shop floor and the office, helping companies organize production and find opportunities to optimize and improve manufacturing operations.
Key functions of manufacturing execution system software
1. Production tracking
MES provides real-time monitoring of the entire production process, tracking each stage of production for every product. It records details such as the quantity of products being made, the specific stages of production they are in, and any delays or stoppages that occur. This data allows manufacturers to identify bottlenecks, optimize workflow, and ensure accurate reporting on production progress.
2. Resource management
One of the core functions of MES is to allocate resources effectively. This includes machines, tools, materials, and human labor. The system schedules and optimizes the use of these resources to ensure that they are not under- or over-utilized. MES enables managers to avoid machine downtime, reduce unnecessary labor costs, and ensure the right materials are available at the right time.
3. Quality control
MES integrates quality assurance directly into the manufacturing process. It ensures that products meet the company’s quality standards by logging quality checks and testing at various stages of production, ensuring that poor-quality products are either corrected or discarded before reaching the next production phase or the customer.
4. Manufacturing order management
MES plays a critical role in managing manufacturing orders, including creating and tracking orders, assigning tasks to workers, and updating orders as they progress. The system ensures that every worker on the shop floor has access to the right instructions and real-time updates, ensuring smooth and consistent operations. It helps manage the production queue, optimizes workflow, and minimizes downtime by providing clear instructions for each step in the manufacturing process.
5. Production scheduling
MES allows manufacturers to generate production schedules that optimize machine time, labor, and materials based on factors such as available resources, customer demand, and order deadlines. With this function, MES systems help manufacturers adjust schedules dynamically to accommodate changes in demand or unforeseen disruptions. By having a real-time view of production capacity, manufacturers can avoid overloading resources or falling behind on production targets, ensuring on-time delivery of products and reducing production lead time.
6. Traceability
Traceability refers to the ability to track each raw material and component from its origin through the various stages of production until it becomes a finished product. MES provides detailed records of every item in the production process, which can be crucial for industries that need to comply with strict regulatory standards (e.g., pharmaceuticals, food manufacturing). This traceability ensures transparency, helps track product quality, and simplifies compliance audits. It is also essential for tracking the flow of materials to identify the root cause of any defects and minimize risks.
Benefits of manufacturing execution system software
Benefits of using an MES system include:
Better equipment utilization
MES optimizes the usage of equipment by ensuring that machines are scheduled for use at optimal times and that maintenance is performed at the right intervals. This reduces machine downtime, increases the lifespan of equipment, and improves overall equipment effectiveness (OEE). By minimizing idle time and keeping machines running smoothly, manufacturers can make the most of their capital investments in machinery.
Reduced WIP inventory and overall optimization of inventory
By tracking materials and components in real time, MES allows manufacturers to monitor and reduce work-in-progress (WIP) inventory levels. It ensures that inventory is only used when necessary, preventing overstocking and reducing storage costs. The system also helps optimize raw material orders, ensuring the right quantities are available at the right time, reducing both raw material and finished goods inventory. This leads to improved cash flow and a more efficient supply chain.
Reduced labor costs
MES streamlines many manual processes on the shop floor, automating tasks such as data collection, production tracking, and reporting. This automation reduces the need for manual labor in these areas, allowing workers to focus on higher-value tasks. MES also ensures that workers have clear instructions, reducing mistakes and improving productivity. With fewer manual interventions, labor costs can be reduced while improving overall efficiency.
Significant reduction in manual data-entry processes
One of the major advantages of MES is that it minimizes the need for manual data entry. The system automatically collects and records data from machines, sensors, and operators. This significantly reduces human error and saves time that would otherwise be spent entering data manually into spreadsheets or other systems. Automated data collection also ensures that the information is always accurate and up-to-date, supporting better decision-making.
Better supply chain visibility
MES provides real-time visibility into the entire production process, which allows manufacturers to monitor the status of orders, track materials, and manage shipments more effectively. With this visibility, manufacturers can quickly identify any supply chain disruptions, whether material shortages, production delays, or logistics issues cause them. This allows for quicker response times, better coordination with suppliers, and the ability to meet customer demands more reliably.
Reduced manufacturing cycle time
By streamlining production processes, optimizing resource usage, and reducing delays, MES helps to shorten the manufacturing cycle time. With accurate scheduling, real-time production tracking, and automatic adjustments to the process, manufacturers can eliminate inefficiencies and reduce bottlenecks. This results in faster production times, which means products are delivered to customers more quickly, improving customer satisfaction and increasing the company’s ability to respond to market demands.
Cloud-based vs. on-premises MES systems
By combining the benefits of an MES system with an ERP system, companies can collect their factory data in a connected and integrated fashion. Because MES manages overall production, its solutions can help manufacturers gain insights into their factory operations and supply chain to improve the quality of data input to the ERP.
In today’s world, a manufacturing execution system makes the most sense as cloud-based software. While larger companies have a heavier IT footprint for managing on-premises deployments, there are disadvantages with on-premises MES that make a cloud-based deployment more desirable.
Disadvantages of on-premise Manufacturing Execution System software
IT skills
On-premises software requires advanced IT skills for deployment, management, and maintenance. This alone would impact the effectiveness of on-premises MES for small to medium-sized businesses that lack the in-house IT skills or the ability to maintain an ongoing system. This means that SMBs would need to subcontract for ongoing maintenance or do without—neither of which are effective solutions.
Learning curve and training
Like most on-premises software, an in-house MES system would require training and the associated cost. This training is less likely to have online support and learning aids such as interactive tutorials or gamified learning and risks lower data retention by those being trained.
Software updates
Because on-premises systems are relatively static over a long period of time, updates are necessary and must be done regularly. Depending on the complexity, this starts the training/learning curve over again. It is also costly and may risk data loss or degradation depending on the skill set of those using the system. It may mean that companies forego the timeliness of updates, again degrading the effectiveness of the system.
High cost
On-premise MES software has high costs due to the significant upfront investment in software licenses and necessary hardware, such as servers and storage. Additionally, unlike cloud-based solutions that are managed externally, they require ongoing expenses for system maintenance, IT staff, and manual updates. The need for customization, integration with existing systems, and scaling as the business grows further contributes to the costs. Moreover, the infrastructure required to host on-premise systems, including energy and security measures, adds to the overall expense.
Advantages of cloud-based Manufacturing Execution System software
Software is always up-to-date
Cloud-based software has an advantage that on-premises can never achieve. As it is continually attached to the cloud, it receives all software updates in real time on an ongoing basis. This ensures that users always have access to the most current version, eliminating the possibility of obsolescence.
More cost-effective
A cloud-based MES will always be more cost-effective compared to on-premises. This saves money because expensive IT infrastructure upgrades are not required. It also means that in-house and ongoing maintenance skillsets are not needed as deeply as in companies with on-premises systems. Upfront and ongoing training costs are also reduced as learning can be done iteratively with tutorials and other online aids. As a result, the total cost of ownership for cloud-based MES software is much lower.
Modular or needs-based system
Many on-premises traditional software systems are “blocky” because they offer specific functionality with little opportunity to control user experience. This means that if a company doesn’t need specific aspects of the program, users are still exposed to it. This slows down user experience and makes user interfaces more time-consuming to navigate. Cloud-based MES is often customizable to both the company and the individual user. This allows for user interfaces and user experiences that are tailored to specific needs, improving the experience, efficiency, and user satisfaction.
Scalability
Cloud-based software can act to “level the playing field” for small and medium-sized businesses. Traditionally, when on-premises software was the only option, SMBs lacked the IT skills and the capital to invest in a sophisticated system. Because cloud-based MES software is modular and intuitive, SMBs have access to state-of-the-art and best-in-class software to put them on par with larger companies. As they grow, this modularity can be added to scale to new functionality requirements without investing in a new system.
How MES works in MRPeasy
MRPeasy includes a built-in Manufacturing Execution System (MES) interface for shop floor workers to report progress easily. This is crucial for replacing paper travelers or manual logs. MRPeasy provides two main modes for data entry on the shop floor: “My Production Plan” and the “Internet Kiosk.”
“My Production Plan” is a personalized view for each production employee. When workers log in (each can have a limited user account), they see a list of the tasks or operations assigned to them, in sequence. For example, a machinist might see that today they have an operation to machine a crankshaft for Engine MO#123, followed by another task for a cylinder head on MO#124, etc. This real-time schedule per worker helps them know what to work on next. The interface is designed to be clear and is accessible from any web browser (or the MRPeasy mobile app), so a tablet on the shop floor or a standard PC can be used.
The “Internet Kiosk” is a mode where a shared device can be used by multiple workers. In a small shop, instead of each employee having a computer, you might have a shop-floor terminal. Workers can walk up, tap to switch to their user (the system supports quick user switching with one click), and then log their task progress. This is very useful with limited IT resources – a single inexpensive touchscreen or PC on the shop floor can serve everyone, and MRPeasy’s kiosk mode minimizes friction (no lengthy logins each time; quick toggle between users).
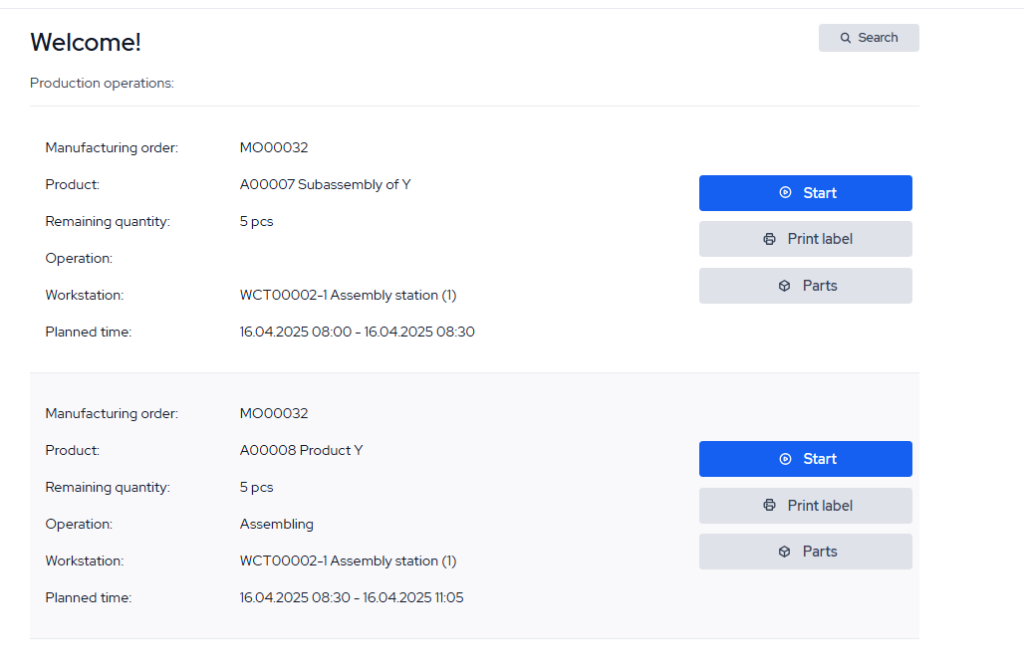
Using these interfaces, workers can start and finish operations, report time taken, and record quantities. For instance, once the machining operation for an engine block is done, the machinist selects that task in MRPeasy and marks it complete (and can input the actual time spent if different from the estimate). They can also indicate if a certain quantity was produced or if there was a scrap. As soon as they do this, MRPeasy updates the manufacturing order status and moves the workflow to the next step. If the routing specifies that assembly can only start after machining is done, the assembly step will now be marked as ready to begin. This way, shop-floor updates are reflected instantly in the system, giving everyone up-to-date information.
Additionally, MRPeasy’s shop-floor reporting allows workers to consume materials when an operation is finished. For example, if assembly used up a gasket kit, the worker can mark the kit as consumed in the system, which will deduct it from inventory and attach it to that MO’s record. When the final assembly operation is completed, MRPeasy will automatically mark the manufacturing order done and transfer the finished engine to stock as a completed product, all at the click of a button. This ensures inventory and production data stay synchronized without back-office data entry.
The interface is designed to be simple and user-friendly for shop staff, even those who are not computer experts. Users commonly praise MRPeasy’s interface as clean and uncluttered. For shop employees, the learning curve is reportedly short – the tasks of clocking in/out of jobs and updating quantities can be learned with minimal training. The system also has an “Important notes” feature: engineers or managers can attach notes or instructions to a routing step, which the worker will see in their task view. This could be used to remind technicians of checklist items (“Torque all bolts to spec and record in QC log”) at a particular step, thus acting as an embedded checklist.
In summary, MRPeasy’s shop-floor data entry capabilities (its MES module) allow the engine shop to go fully paperless on the production floor. Workers have a clear view of their tasks and can easily report progress and issues in real time. This not only saves time (no need to fill out paper forms and have someone enter them later) but also improves accuracy (actual times and completions are recorded immediately). For a shop with limited IT, the fact that this just requires a web-enabled device and is straightforward to use is a big advantage.
For more information, visit the MRPeasy internet-kiosk guide.
Key takeaways
- A Manufacturing Execution System (MES) is a digital platform used to manage, monitor, and control production on the factory floor, facilitating data exchange between shop floors and offices to optimize manufacturing operations.
- MES tracks production progress, manages resources (machines, labor, materials), integrates quality control, and oversees work orders and scheduling. It also provides traceability to ensure transparency in manufacturing processes.
- MES improves equipment utilization, reduces work-in-progress (WIP) inventory, optimizes labor use, and eliminates manual data entry. It improves supply chain visibility and reduces manufacturing cycle time, leading to faster production and better customer satisfaction.
- On-premise MES requires significant upfront costs, ongoing maintenance, and specialized IT staff, making it less cost-effective for many businesses. In contrast, cloud-based MES reduces infrastructure needs, provides continuous updates, and is easier to scale.
- MRPeasy’s cloud-based MES system is designed to simplify shop-floor data entry, allowing employees to report production progress, track materials, and update status in real time. It is user-friendly, cost-effective, and can be used with minimal IT resources, supporting a paperless production environment.
Frequently asked questions (FAQ)
MES ensures that quality checks are integrated directly into the production process by recording data on product quality at various stages. This helps identify defects early, allowing manufacturers to correct issues before products move to the next phase, thus preventing poor-quality items from reaching customers.
Cloud-based MES provides SMBs with access to advanced manufacturing software without the need for significant upfront investment in IT infrastructure or specialized staff. The scalability and modular nature of cloud MES make it easier for SMBs to expand and tailor the system as their business grows, enabling them to compete more effectively with larger companies.
Cloud-based MES systems are typically designed to be user-friendly with minimal training required. Employees can often learn to use the system through online tutorials, interactive guides, or in-system support features, making the learning curve short and reducing the need for extensive formal training sessions.
You may also like: How to Scale Production Processes in Manufacturing?