A Guide to Manufacturing Compliance for Small Businesses
In this guide, we break down some of the essential aspects of manufacturing compliance, provide practical implementation strategies, and explore how modern software solutions can help small manufacturers maintain compliance without straining their budgets.
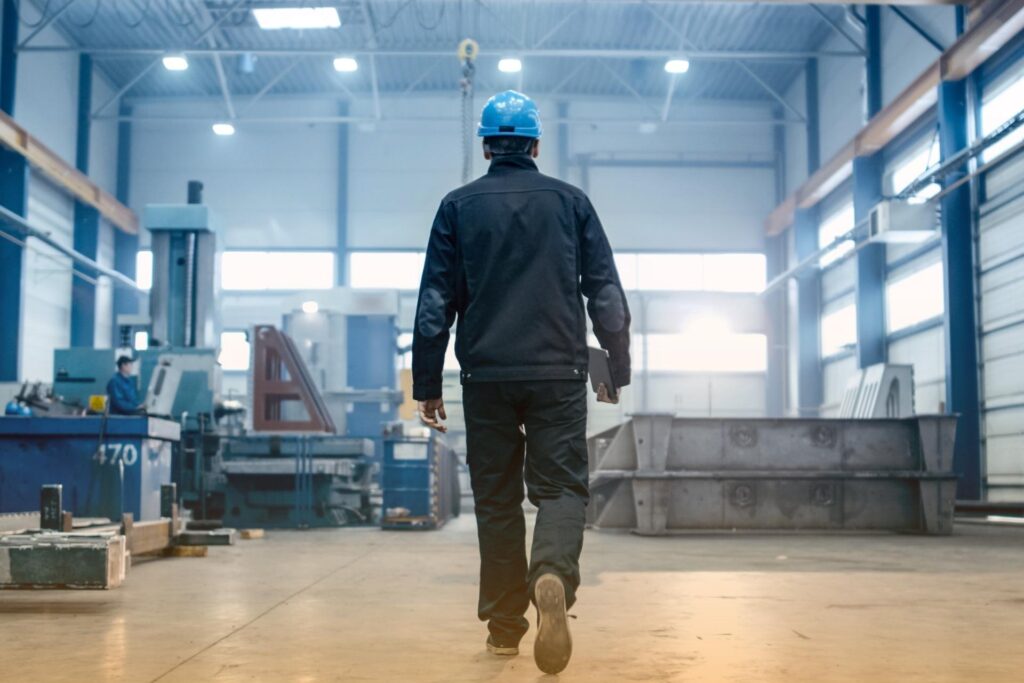
What is manufacturing compliance?
Manufacturing compliance is adherence to all applicable laws, regulations, standards, and guidelines established by a country’s governing authorities and by various industry regulatory bodies within the manufacturing sector in which you work.
Compliance isn’t just a regulatory checkbox – it’s a critical foundation for sustainable business growth and operational excellence. For small manufacturers, the maze of regulations, standards, and industry requirements can feel overwhelming, especially with limited resources and ability.
There are some compliance regulations you need to follow just to be in business. Others will depend on what markets you want to enter. You may even have some internal policies developed over your time in business. Manufacturing compliance covers everything from product specifications to operational practices to employee management.
Regulatory bodies in manufacturing
The U.S. manufacturing compliance industry is overseen by several federal agencies, each focusing on specific aspects of manufacturing operations. Here are a few examples:
- The Food and Drug Administration (FDA) regulates food products, pharmaceuticals, medical devices, and cosmetics manufacturing, ensuring product safety and quality.
- The Environmental Protection Agency (EPA) oversees environmental protection standards, including air and water quality, waste management, and hazardous substances.
- The Occupational Safety and Health Administration (OSHA) ensures safe and healthy working conditions for employees through workplace safety standards and regulations.
- The Consumer Product Safety Commission (CPSC) protects the public from unreasonable risks associated with consumer products.
The European manufacturing industry is similar, governed by various regulating bodies and industry standards. For example:
- The European Chemical Agency (ECHA) manages the regulations for the classification, labeling, packaging, and authorization of chemicals made in or exported to the EU.
- The European Medicines Agency (EMA) does the same for medicines.
- The European Food Safety Authority (EFSA) oversees regulations related to food and feed safety, ensuring that food products produced or imported into the EU meet strict health and safety standards.
In addition, many international standards also exist to ensure quality, safety, and regulatory compliance across global markets. For example, ISO 9001 sets the benchmark for quality management systems, helping manufacturers meet various regulatory requirements. Export control regulations further govern the transfer of dual-use goods and technologies to enhance global security. Industry associations, like the International Accreditation Forum (IAF) or the World Trade Organization (WTO), play a key role in harmonizing standards, facilitating trade, and promoting best practices in manufacturing worldwide.
Importance and benefits of manufacturing compliance
Maintaining compliance isn’t just about avoiding fines and keeping your business out of hot water with the “Feds.” Designing, implementing, and sticking to a strong, workable compliance program benefits your company with tangible results that add up. And for small manufacturers, that’s crucial for sustained business growth.
Increased product quality and safety
Quality standards like the European Good Manufacturing Practices (GMP) form the backbone of reliable production processes. When you follow GMPs or other quality assurance standards in your location, the value of your output improves.
A systematic approach to quality reduces defects and recalls and builds customer confidence in your products. Product reliability and quality lead to satisfied customers, often turning them into brand evangelists.
Higher quality products are generally safer products, particularly in the food industry. Sick customers are not good advertising for your brand. Besides, who wouldn’t want fewer warranty claims?
Operational excellence
Following manufacturing compliance regulations often has an unexpected side effect. Not only will you make a better, safer product, but you’ll also make it more efficient, saving time and even money in the process. When you start applying compliance standards, you’ll find operational inefficiencies and opportunities for process improvement that were previously hidden from sight.
Streamlined workflows, reduced waste, and more effective resource consumption are just a few of the benefits manufacturers have discovered when they sat down and seriously evaluated their processes using compliance standards as a benchmark.
Increased market access and competitive advantage
Following marketing compliance standards can open up opportunities that expand far beyond your local, regional, or even country’s borders. Many profitable markets are locked behind compliance-regulated doors. To unlock them, you’ll need to find out what specific regulations you need to follow and what certifications you’ll need to acquire.
Government contracts can be quite lucrative and a potential continuing source of revenue. But you’ll have several regulatory hoops to jump through. They’ll need to see and periodically review documented compliance programs.
If you’re considering jumping into the international arena, make sure you find out what regulatory and compliance standards you need to address. It’s best to meet and even exceed those requirements to make the international market a viable option.
Employee safety and satisfaction
Whenever people are present on the factory floor, compliance with safety regulations isn’t just a good idea but a legal requirement. A safe work environment also lets your team members work with confidence. Remove the risk, and productivity will follow.
While safety and ergonomics measures can be significant expenses, showing your commitment to your workforce’s safety and well-being pays off with dividends. Not only could you get more productive teamwork, but there could be some financial benefits as well.
For example, you’ll likely see a reduction in workplace accidents that could very well lead to lower insurance premiums. When you show your commitment to safety regulations and compliance rules, employee morale will improve because they understand they’re not just numbers on a punch card. They’re valued team members. Workers who feel valued are less likely to leave, thereby allowing you to draw on their knowledge gained over time.
Business sustainability
The factors that give your business stability in a volatile market are brand reputation, customer trust and loyalty, and let’s add good partnerships and relationships with your suppliers. When you build a good track record with all of these, you become a responsible manufacturer. That builds trust all the way up and down the line.
This trust translates into stronger business relationships and often better access to financing when needed.
Compliance-driven manufacturers typically experience fewer operational disruptions and maintain more stable supply chain partnerships. This makes your stakeholders (and shareholders) happy. You want to keep them happy. They hold the purse strings.
Cost savings through prevention
While compliance measures require an initial investment, the cost of non-compliance far exceeds the price tag. Consider what’s at risk: substantial financial penalties, legal defense costs, and potential production shutdowns until violations are resolved. These expenses will be hard to recoup. Major safety violations may require your operations to cease completely until remedied, even when time for corrective action is allowed. That means you’re spending money while not generating revenue to cover it.
But something even more valuable is at stake – your reputation. Lost business opportunities, damaged customer trust, and exclusion from profitable markets can be difficult, if not impossible, to recover from. Some customers may never return. As the saying goes, “Once bitten, twice shy.”
The long-term financial implications of lost trust far outweigh the cost of maintaining proper compliance programs.
Main areas of manufacturing compliance
Manufacturing compliance encompasses several critical areas that require constant attention and coordinated management. While each manufacturing operation may have unique conditions based on its industry and location, there are certain core compliance areas that are universal.
Quality control and assurance
Quality control isn’t just checking off boxes or giving the thumbs up. You have to execute management systems that perform consistently under production conditions. A thorough audit and review process demands more than quick visual checks. Develop a process that you can document.
Make sure your audit and review processes are laid out in detail. Create a well-documented paper or digital trail from raw material to finished product. Back it up with rigorous process controls and regular effectiveness audits.
Quality management programs should address:
- Process validation and control parameters.
- Equipment calibration and maintenance schedules.
- Material handling and storage procedures.
- Product testing and inspection protocols.
Environmental regulations
Environmental responsibility has become crucial in manufacturing. The EPA and state environmental agencies enforce strict sustainable manufacturing regulations regarding emissions, waste management, and resource conservation.
Developing a thorough response to environmental management and compliance is critical for manufacturing companies whose waste could cause harm to the environment. These regulations are updated and changed on a regular basis.
Safety standards
We’ve already touched on safety. It’s an important part of compliance. Safety compliance requires several types of documentation. For example, some of my past responsibilities included creating employee safety protocols, such as properly locking out machinery during maintenance. Written procedures are mandatory for any mandated safety protocols and requirements,
But it’s not just enough to have them written down. Safety standards compliance means following up to make sure they’re being used. That means initial training for new employees, and ongoing retraining thereafter as well as work reviews. OSHA and other regulatory bodies will demand to see the paperwork.
Labor laws and employment practices
Labor compliance isn’t static. It’s continually evolving with new wage, discrimination, and classification regulations. While your internal HR practices may meet current standards, don’t overlook your business partners’ labor practices. Their compliance shortfalls can affect your exposure to regulatory scrutiny and potential litigation.
Just recently, a large nationwide food processor in our area was taken to court over alleged child labor law infractions. It wasn’t that they themselves employed underage workers. One of the subcontractors they used for cleaning and sanitation did.
Data security and privacy
Digital security threats pose unique challenges in industrial settings. Beyond standard company records, your intellectual property and manufacturing processes are at risk. With trade secrets and proprietary processes stored digitally, the stakes are higher than ever. High-profile breaches across various industries, including banking, healthcare, and insurance, underscore this growing threat.
This requires using tough cybersecurity measures and maintaining compliance with data protection regulations such as GDPR for international operations.
Supply chain compliance
Manufacturing operations often involve complex supply chains that require their own compliance considerations. Manufacturers must ensure their suppliers meet relevant quality, safety, and ethical standards by keeping proper documentation of all supply chain activities.
This includes verification of supplier certifications, monitoring supplier performance, and retaining proper chain of custody documentation.
How to achieve compliance in manufacturing
All manufacturers build effective compliance programs by following a systematic, structured approach. It must address all relevant requirements while still remaining manageable.
Begin the process with a thorough assessment of your operational environment and applicable regulations. Identify which federal, state, and local requirements apply to your specific manufacturing operation. Create a master list of all your operations to determine relevant compliance requirements.
While you may not need programs for every aspect, you can’t afford to miss critical ones. Your compliance program should incorporate several key elements:
- Clear policies and procedures that address all applicable regulations.
- Defined roles and responsibilities for compliance oversight.
- Documentation requirements for all compliance activities.
- Regular review and update procedures to support program effectiveness.
Risk assessment and prioritization
Developing a complete compliance system requires careful planning. Start by listing all requirements, then assess each one’s urgency and implementation timeline.
One approach uses a whiteboard with sticky notes for visual task organization. This allows you to easily adjust priorities and create a practical action plan. Whether you use this method or a digital equivalent, let your manufacturing floor experience guide your risk management and prioritization.
Consider these key areas when assessing compliance risks:
- Regulatory requirements and potential penalties for non-compliance.
- Customer requirements and assumed business impacts.
- Safety considerations and possible impacts on workers.
- Environmental impacts and community concerns.
Implementation and documentation
Risk assessment is only valuable when followed by risk mitigation. Transform your insights into actionable Standard Operating Procedures (SOPs). These SOPs should:
- Establish clear control parameters and monitoring points.
- Define how compliance standards will be met.
- Outline procedures for handling operational discrepancies.
- Include processes for continuous evaluation and improvement.
For example, in the US food and beverage industry, this is carried out through Hazard Analysis Critical Control Point (HACCP) programs, which identify safety hazards and establish control measures at critical manufacturing points.
SOPs must be clear, accessible, and regularly updated to reflect changing regulations and operational adjustments.
Essential documentation elements include:
- Written policies and procedures for all compliance activities.
- Training materials and participation records.
- Inspection and audit reports.
- Corrective action documentation.
Employee training and engagement
A compliance program is only as effective as your employees’ comprehension and participation. Simply distributing handbooks isn’t enough—they often end up forgotten in lockers, leaving you vulnerable to regulatory violations.
Instead, implement a comprehensive training program that:
- Clearly communicates each employee’s role in maintaining compliance.
- Includes regular refresher sessions.
- Adapts to regulatory changes with updated training.
- Verifies understanding through assessment.
Remember: “I didn’t know” won’t satisfy regulatory inspectors. Your training program must ensure that excuse never comes up. Training programs should address:
- Regulatory requirements relevant to each job function.
- Company policies and procedures for maintaining compliance.
- Emergency response and reporting procedures.
- Updates on regulatory changes and their operational impacts.
Monitoring and measurement
Compliance programs of any type don’t run on autopilot. They require continuous monitoring and defined checkpoints to see how and if they’re being used. Eventually, your compliance programs and systems will collapse like a house of cards if protocols aren’t followed consistently.
Monitoring program performance and measuring its effectiveness is critical. This includes regular inspections, audits, and performance metrics that help identify potential issues before they become serious problems. Having sufficient traceability systems in place is crucial.
One warning here. Your compliance management efforts must be documented. This includes your monitoring and review results. Your program may be best-in-class. But if not documented thoroughly, you have no proof. Your paperwork should speak to and be proof of your commitment to manufacturing excellence and regulatory compliance.
Key monitoring activities should include:
- Regular internal audits of compliance programs.
- Periodic third-party assessments.
- Performance metric tracking and analysis.
- Incident investigation and root cause analysis.
Continuous improvement in compliance management
Compliance requires ongoing vigilance and continuous improvement. Build in regular reviews, audits, and incident investigations – including root cause analysis. Regulatory requirements change often, so your program must evolve to match.
Focus improvement efforts on:
- Analyzing compliance data to identify trends and patterns.
- Reviewing and updating procedures based on operational experience.
- Incorporating feedback from employees and auditors.
- Staying current with regulatory changes and industry best practices.
Read more about continuous improvement in manufacturing.
Management review and oversight
Implementing a comprehensive manufacturing compliance program requires more than shop-floor participation—it demands total organizational buy-in, especially from senior management.
While front-line workers need proper training and monitoring, success ultimately depends on active C-suite involvement. senior management must actively take part in all aspects of compliance. They need to balance regulatory requirements with business goals. It’s essential for them to lead by example in compliance adherence.
How manufacturing software simplifies compliance for SMEs
Modern manufacturing software solutions offer powerful tools to streamline compliance management, making it more efficient and dependable for small- and medium-sized enterprises (SMEs). Using software solutions does require an initial cost for purchase and training. But the long-term benefits make it a worthwhile investment.
Technology can really transform the way you manage your compliance obligations. These systems reduce manual effort, minimize human error, and provide better visibility into compliance status across every aspect of your operations.
Understanding compliance software options
Compliance software comes in two main types. Specialized solutions focus on specific areas like quality management or safety compliance. They offer deeper functionality but need to work with other software tools to fill in the gaps. Comprehensive platforms, on the other hand, manage multiple compliance functions in one package, though they may not match the depth of more specialized tools. A third option is adopting manufacturing ERP software with functionalities that simplify your compliance processes and audits.
Choosing the right solution starts with understanding your requirements. Evaluate how each option fits your workflows, especially if you are considering multiple tools. Talk to other companies about their experiences, and always evaluate the top contenders before deciding.
Make sure your compliance solution simplifies at least these core functionalities:
- Document management and control.
- Automated workflow management.
- Real-time monitoring and reporting.
- Audit trail maintenance.
Manufacturing compliance best practices for SMEs
We’ve touched on many aspects for winning the compliance game in this guide. It’s a starting point, and you still have a lot of work to do. But small- and medium-sized manufacturers can bolster their compliance programs by implementing proven best practices. And its possible to do that within their resource constraints.
Here are five essential approaches that deliver maximum impact while staying manageable for smaller operations.
1. Establish a compliance-first culture
Everybody in the company must understand and get on board with compliance goals. Each person, from the person in the CEO seat to the worker on the shop floor needs to realize how maintaining compliance affects not just the business, but their livelihood as well.
When executives actively promote compliance in daily operations, employees naturally incorporate regulatory requirements into their work. Compliance success starts from the top and filters down.
2. Implement systematic documentation processes
Document everything you do and make sure you have a way to create and maintain your compliance records. Regulatory inspectors are busy. They don’t have the time nor inclination to wait while you fumble around through myriad file cabinets and folders.
The longer you make them wait, the less amicable they become. As my mom used to say, have a place for everything and keep everything in the right place.
3. Invest in continuous training
Ongoing compliance training keeps everyone on the same page. And make sure your team members know they can always ask questions for clarification. What you’re teaching them may be foreign to them. Understand that many store-bought training programs use very generic examples. Supplement those with scenarios that your employees will actually come in contact with.
4. Develop strong supplier relationships
Build relationships with suppliers who share your commitment to compliance practices. Clear expectations in supplier agreements, along with regular audits, help prevent compliance issues before they affect operations. If they’re not on board with you, find someone else who is.
5. Leverage technology strategically
If used properly, automation technology can be a game changer. Find a solution that will make your compliance program more manageable. Make sure it aligns with your current compliance strategy, which will grow with you as you expand your requirements in the future.
They say Rome wasn’t built in a day. And certainly, an effective, workable compliance program doesn’t magically appear overnight.
But the time to get started is now.
Key takeaways
- Manufacturing compliance is the adherence to laws, regulations, and industry standards by regulatory bodies that govern everything from product quality to workplace safety. Ensuring compliance helps businesses operate legally, ethically, and efficiently while reducing risks.
- Beyond avoiding fines and legal trouble, strong compliance practices enhance product quality, streamline operations, and build customer trust. Companies that prioritize compliance gain a competitive edge and open doors to new markets.
- The main areas of compliance cover quality control, environmental regulations, workplace safety, labor laws, data security, and supply chain management. Each area requires continuous oversight and documentation to ensure regulatory adherence.
- Achieving compliance requires a structured approach to assessing risks, developing clear policies, training employees, and continuously monitoring performance. Documentation and regular audits are key to adapting to evolving regulations.
- Manufacturing software helps streamline document management, automate workflow processes, and improve real-time monitoring. Investing in the right compliance software reduces human error, simplifies audits, and enhances overall efficiency.
Frequently asked questions (FAQ)
Manufacturing regulatory compliance means following all laws, regulations, and industry standards that apply to production processes. It ensures product quality, workplace safety, environmental protection, and ethical labor practices.
Manufacturers ensure compliance by implementing clear policies, training employees, conducting regular audits, and maintaining thorough documentation. They also use quality control measures, safety protocols, and environmental management systems. Many rely on compliance software to streamline monitoring and reporting.
ISO (International Organization for Standardization) sets global standards for quality, safety, and efficiency in manufacturing. Certifications help companies meet regulatory requirements, improve processes, and gain customer trust. Following ISO standards enhances compliance and competitiveness in international markets.
You might also like: Top ISO Standards Used in Manufacturing