5 Most Common Small Manufacturing Challenges According to Consultants
Manufacturing consultants Tim Grant from Business Solution Providers, David Altemir from Altemir Consulting, and Patrick Verryn from Move 2 Cloud share their insights about the most common challenges their small manufacturing clients experience.
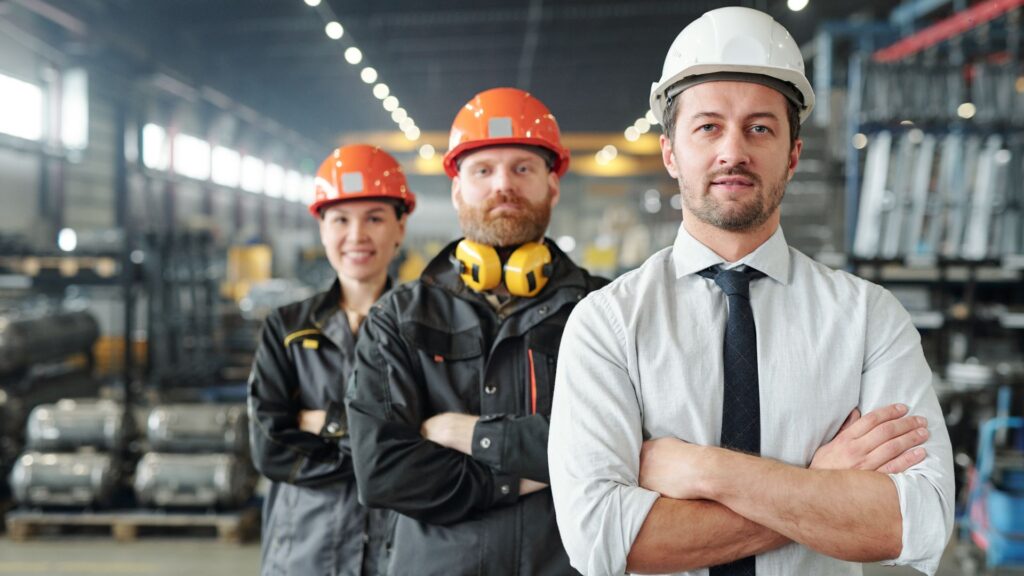
You can also listen to this article:
1. Managing recipes and bills of materials (BOMs)
A recurring challenge is managing and understanding BOMs or product recipes, especially when manufacturers deal with products that have multiple variants, engineering or recipe changes, or complex assembly processes. This complexity can lead to errors and inefficiencies in production planning and inventory management.
“Many of our clients have gotten stuck when trying to create BOMs,” says Patrick Verryn.
“It is especially difficult to turn engineering BOMs into manufacturing BOMs, and transferring changes as the design evolves,” David Altemir adds.
2. Inventory accuracy
Many small manufacturers struggle with keeping accurate inventory records. This often stems from recordkeeping deficiencies, complex products and processes, or using error-prone manual methods such as spreadsheets. The consultants emphasize the need for strict transactional discipline and robust procedural frameworks to manage inventory effectively. Without these, manufacturers face persistent issues with inventory discrepancies, which can lead to stockouts, excess inventory, and increased operational costs.
“Not being able to keep accurate inventory is a common issue clients come to me with,” David Altemir states. “This always proves to be an operational issue within the company, most often a lack of transactional discipline.”
3. Understanding their production capacity
According to the consultants, small manufacturers have a hard time figuring out how much they can produce at any given time. This, in turn, leads to customers being promised unrealistic lead times as production bottlenecks start to slow down processes. The ability to dynamically assess production capacity and schedules is crucial for maintaining efficient operations. This requires not only technical solutions but also a strategic overview of production processes to ensure that capacity aligns with demand.
“Specialized manufacturing software gives manufacturers an immediate understanding of what can be realistically accomplished within given timelines,” says Tim Grant. “Without it, small manufacturers will continue to struggle with their production and delivery schedules.”
4. Integrating business data
Integrating various operational functions and eliminating data siloes is essential for businesses that want to scale up efficiently. However, many small businesses are bogged down by legacy systems and bad data. To achieve data integration, they need to implement a system that can consolidate data from various sources, providing a unified and comprehensive view of all operational aspects. This integration, often involving several different applications, is crucial for improving efficiency and responsiveness in manufacturing operations.
“Our clients know how to produce things; they are experts at that,” Tim Grant maintains. “But they also acknowledge their lack of experience with software, especially when it comes to integrating multiple applications.”
5. Actual costing
Understanding your actual costs is critical for pricing your products, finding financial sinkholes, and ensuring profitability. The process of actual costing can be very complex, however, as it calls for meticulous tracking of material lot prices, labor costs, and overheads. Maintaining such detailed records in a spreadsheet can soon become unwieldy and error-prone as the volume of data grows. That is why it’s necessary to implement specialized software that can handle lot tracking and actual costing.
“Often our customers don’t even realize that actual costing is possible, and due to that, they don’t even ask for it,” David Altemir says. “That’s understandable because there aren’t many solutions available to small manufacturers that offer actual costing.”
The solution: manufacturing resource planning software
Having completed hundreds of software consultation projects between them, Grant, Altemir, and Verryn have one thing in common: they all recommend MRP software for overcoming the common challenges in small manufacturing. They also share a love for one solution in particular: MRPeasy.
“MRPeasy is by far the best in terms of ease of use,” Grant says. “MRPeasy also listens to their clients and implementation service providers when it comes to suggestions for improvements in the product. Many software solutions aren’t as responsive.”
“Most other products started with inventory management and then bolted on a manufacturing module,” Verryn says. “MRPeasy was natively built for manufacturing, and while I still occasionally work with other MRP/ERP systems, MRPeasy is now my ‘go-to’ product.”
David Altemir adds, “MRPeasy comes with the functionality, ease of use, and affordability small manufacturers need. Plus, it is one of the few systems that offers actual costing.”