Manufacturing Automation: Benefits, Tips, and Budget-Smart Options
Automation has established itself as an integral part of manufacturing operations in businesses of any size. This is thanks to automation tools having become accessible even to the smallest of manufacturers.
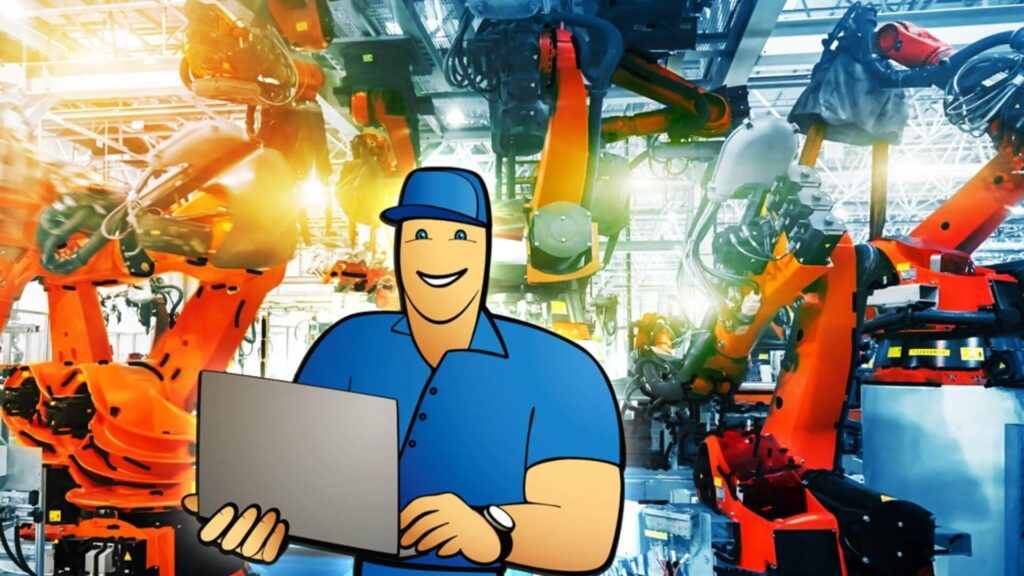
You can also listen to this article:
What is automation in manufacturing?
Manufacturing automation refers to the use of advanced technologies and systems to execute manufacturing-related tasks with minimal human participation. It involves the integration of machinery, software, and automated control systems into manufacturing workflows to perform repetitive or complex operations efficiently and accurately. As such, it is a vital part of digital transformation.
There are different types of automation used in the manufacturing industry:
- Fixed automation, also known as hard automation, relies on highly specialized equipment designed to perform a specific set of tasks, typically in a high-volume, repetitive production environment.
- Flexible automation, also known as programmable automation, can adapt to a range of different tasks, making them suitable for small batch production with frequent changeovers.
- Robotic automation uses highly versatile robots that can perform a variety of tasks from assembly to welding, from material handling to quality inspections.
- Software automation tools are designed to eliminate administrative tasks and to facilitate effective planning, tracking, and overall business management.
While robotic and flexible automation tools could be too expensive for small manufacturers, fixed automation and especially software automation solutions are accessible to anyone.
What are the benefits of manufacturing automation?
There are many benefits to be gained from introducing any kind of manufacturing process automation. Here are some ways industrial automation could impact your business:
1. Increased efficiency. Manufacturing automation streamlines production processes, from the production planning stage to the production lines. It minimizes downtime, optimizes production rates, and improves overall efficiency, resulting in higher output and reduced labor costs. Manufacturing software automates many managerial functions and enables companies to discover and eliminate bottlenecks across the operation.
2. Improved product quality. Automation systems perform tasks with precision and consistency, minimizing human error. Real-time data collection and quality control mechanisms within dedicated software ensure that products meet stringent quality standards.
3. Cost savings. Automation reduces labor costs associated with repetitive tasks as well as data entry and processing. In flexible automation, changeovers between products are quicker and more cost-effective, enabling more efficient batch production.
4. More efficient supply chain management. Automation tools provide real-time data on inventory levels and demand, allowing for better supply chain planning and reducing the risk of supply chain disruptions. With proper software, companies can prevent stockouts and overstocking while monitoring the performance of their suppliers, sales teams, and stock items. With an RMA module, return and repair management is also systemized and largely automated.
5. Reduced downtime. Automation technologies enable predictive and preventive maintenance, reducing unplanned downtime and preventing costly breakdowns on the factory floor.
6. Data-driven decision making. Automation systems collect and analyze real-time data, providing valuable insights into production processes. This data-driven approach helps companies plan and schedule production, prioritize orders, discover inefficiencies, and make better business decisions in general.
7. Workforce optimization. Automation frees human workers from repetitive and time-consuming tasks, preventing fatigue and allowing them to focus on more complex and creative aspects of their roles. Apart from increasing production efficiency, this optimization can also improve job satisfaction and employee retention.
8. Sustainability. Automation can significantly reduce energy consumption and minimize waste as machines can perform tasks much more repeatably than humans can, resulting in less scrap or rework.
In conclusion, the benefits of automation can impact manufacturing companies not only on the shop floor, but across departments, and reflect back to you as customer satisfaction increases and employee retention improves.
Common concerns regarding manufacturing process automation
Naturally, many questions and concerns arise with the development of new technology, and automation tools are no exception. Let’s address some of the big questions:
Job displacement
Concerns about job displacement arise from the fear that automation will lead to workforce reductions. Instead, automation is poised to transform jobs, requiring workers to switch from performing tasks to managing, maintaining, and optimizing automation systems. Instead of losing jobs, automation has the potential to bring about higher-skilled and more fulfilling job positions.
Resistance to change
Resistance is a natural human response to changing long-established workflows. To mitigate this, involve employees in decision-making and provide a clear rationale for automation. Have a change management process in place and offer comprehensive training to build confidence and ensure that employees are well-prepared for the transition. Communicate the long-term benefits, such as reduced workloads and career advancement opportunities.
Implementation costs
Concerns about the initial costs of automation are common. To address this, conduct a thorough cost-benefit analysis to see the long-term savings and ROI. Take into account the competitive advantages and efficiencies gained through automation that justify the initial investment. And keep in mind that some automation tools are affordable even to small manufacturers. To get an idea about where to start your automation journey, read the next section.
3 budget-smart ways to automate manufacturing processes
While large corporations may have the resources to invest heavily in automation, small manufacturing businesses often postpone it in the face of budgetary constraints. However, automation isn’t exclusively for the big players. The good news is that there are cost-effective ways for small manufacturers to embrace automation and reap its benefits.
1. Implement cloud-based MRP software
Manufacturing ERP (enterprise resource management) systems like MRPeasy are essential tools for small and medium-sized companies looking to automate and streamline their business processes. Since they are cloud-based, they require no upfront investment in hardware and infrastructure, making them a cost-effective option and a smart first step towards automation.
One of the primary ways MRP software automates processes is through production planning. It uses inventory levels, available capacity, current orders, and other data to assist in long-term master production schedule creation and to automatically create optimized short-term production schedules. This ensures that resources are utilized efficiently, with minimal idle time and production bottlenecks. In addition, MRP software can be used to quickly and accurately estimate the production time and costs for incoming orders. This way, you can promptly respond to customer requests and ensure that your products are delivered within the promised timeframes.
MRP software also automates inventory tracking and planning processes. For example, users can see exactly what they have in stock, forecast material requirements with just a few clicks, receive low-stock alerts, and raise pre-filled purchase orders when material replenishment is needed. This prevents both stockouts and overstock situations, minimizing stoppages and freeing up cash otherwise tied up in unused inventory. In addition, proper MRP systems support barcode scanning, which drastically reduces data entry time in the stockroom.
Order tracking is automated within an MRP system by continuously updating the status of orders throughout the production process. It records when orders are received, when materials are allocated, and when production starts and is completed. Through real-time updates and alerts, it provides instant visibility into order progress, helping businesses track and manage orders efficiently, reduce delays, and ensure timely deliveries to customers.
Automated reporting and analytics in MRP software offer real-time insights into your manufacturing performance. With dozens of automated reports available, management is empowered to make informed decisions, identify areas for improvement, and drive overall operational excellence.
Many modern MRP systems also offer native integrations with various e-commerce, accounting, CRM, and fulfillment apps, automating the exchange of information between different solutions in a company’s software stack.
2. Bring in low-cost automation machinery
Automation machinery doesn’t have to break the bank. Small manufacturing businesses can continue their automation journey by implementing low-cost fixed automation tools that can make a significant impact on efficiency. One of the simplest and most affordable options is the use of conveyor belts. These belts can facilitate the smooth movement of materials and products, reducing the need for manual transportation.
Beyond conveyor belts, there are several other low-cost automation tools that can be considered. For example, automated packaging machines can automate the packaging process, reducing the need for manual labor and increasing packaging consistency. Automated sorting systems can categorize and sort items based on predefined criteria. By automating the sorting process, manufacturers can achieve faster throughput and reduce the risk of human error.
3. Gradually implement more expensive automation systems
While MRP software and low-cost tools provide an excellent starting point, small manufacturing businesses can also gradually implement more advanced and potentially expensive automation systems as their budget allows. For example, instead of completely replacing existing machinery, consider adding automation components like robotic arms to enhance their capabilities.
Another option is the use of automated guided vehicles (AGVs) that can autonomously transport materials within the facility. These machines can be programmed to follow specific routes and interact with machinery for seamless material handling.
Collaborative robots or cobots are another automation tool designed to work alongside human employees, increasing efficiency and safety. They can be programmed for various tasks and require minimal technical expertise to operate.
In addition, implementing IIoT (Industrial Internet of Things) sensors can provide valuable data insights for predictive maintenance, process optimization, and inventory management. Over time, this data-driven approach can lead to significant cost savings.
Key takeaways
- Manufacturing automation involves the use of advanced technologies and systems to execute manufacturing tasks with minimal human intervention.
- There are various types of automation in manufacturing, including fixed automation for repetitive tasks, flexible automation for adaptability, robotic automation with versatile robots, and software automation for administrative functions.
- Automation brings several advantages, including increased efficiency, improved product quality, cost savings, enhanced supply chain management, reduced downtime, data-driven decision-making, workforce optimization, and sustainability.
- Common concerns about manufacturing automation include job displacement, resistance to change, and implementation costs.
- Small manufacturers can adopt automation cost-effectively by implementing cloud-based MRP software, utilizing low-cost automation machinery like conveyor belts, and gradually introducing more advanced automation systems.
Frequently asked questions
Automation in manufacturing refers to the use of advanced technologies and systems to execute manufacturing-related tasks with minimal human participation, streamlining processes and improving efficiency.
The four types of automation in manufacturing are fixed automation, flexible automation, robotic automation, and software automation.
An example of automation in manufacturing is the use of industrial robots to perform tasks like welding, assembly, or material handling in a factory.
You may also like: Automated Inventory Management – A Quick Guide