Manufacturing Accounting – A Simple Guide
Manufacturing accounting is an internal business management process that helps managers keep an eye on the fiscal performance of a manufacturing operation. This post looks at the basic processes that inform manufacturing accounting and defines its most relevant terms.
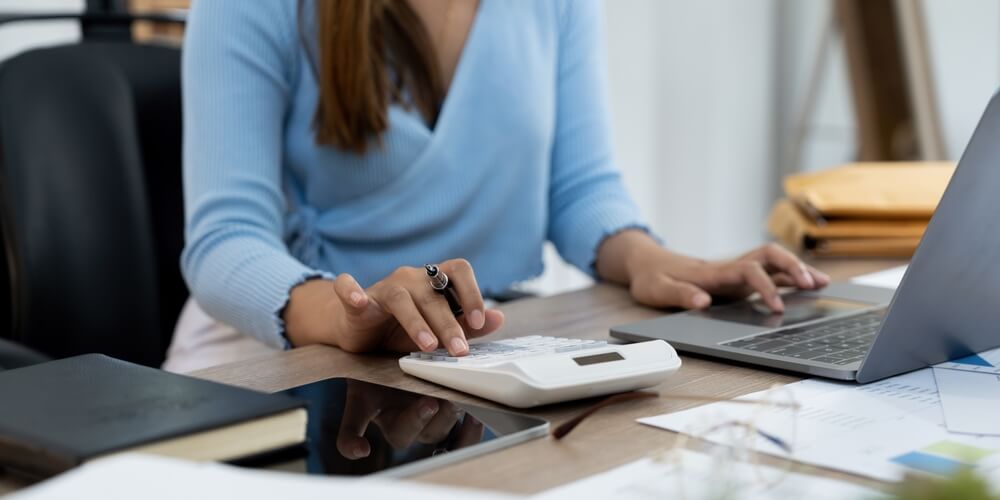
You can also listen to this article:
What is Manufacturing Accounting?
Manufacturing accounting is a group of inventory and production management processes used for monitoring and controlling the costs involved with manufacturing products. Sometimes also called cost accounting, manufacturing accounting utilizes techniques that allow a company to gain insights into the financial performance of production activities, thereby increasing operational efficiency and control. The process mostly revolves around calculating key metrics like the total cost of manufacturing, cost of goods manufactured (COGM), cost of goods sold (COGS), and deciding on the inventory valuation and production costing methods most suitable to a company’s use case.
Unlike financial accounting which determines the financial performance of the entire company and makes it available to external sources through financial statements, manufacturing accounting is specifically designed for measuring what happens within a factory or production facility – how much each product sold costs to produce, how much profit it makes, etc. It is therefore mostly an internal business management process aimed at better decision-making on budgeting, cost control, constraint and margin analysis, etc.
Since it is mostly used as an internal decision-making tool, manufacturing accounting does not generally need to be compliant with financial standards and procedures like the Generally Accepted Accounting Principles (GAAP) or International Financial Reporting Standards (IFRS). A relevant exception is inventory valuation which generally needs to conform to local jurisdictions for taxing purposes. Manufacturing companies often use data from the manufacturing accounting process to compile compliant financial reports. Capable inventory management and MRP software systems also automatically compile manufacturing accounting data into readily usable reports.
Manufacturing Costs Explained
The main focus of manufacturing accounting is to track and control the various cost-oriented metrics of production. Starting with the most fundamental, let us take a look at these in a bit more detail.
Total Manufacturing Cost
The big question that any manufacturing company needs to answer in order to figure out its financial situation is: what are the total costs associated with manufacturing items? The metric that aims to answer this question is the total manufacturing cost (TMC), also known as Total Cost of Production. TMC is calculated by adding together all of the costs associated with producing items. These fall into direct costs and indirect costs:
- Direct costs, as the name implies, are costs directly tied to the production of specific goods. Direct costs split into direct material costs, direct labor costs, and direct miscellaneous expenses. Direct material cost represents the cost of procuring all inventory items that a finished good consists of. In other words, it is the total cost of procuring every component in a Bill of Materials. Direct labor cost represents the total labor expenses of everyone that worked on producing a finished good. This means the labor costs of every worker specifically working towards finishing a product. Direct miscellaneous expenses are costs such as royalties, license fees, or patent rights that are paid per unit of production. Altogether, direct costs are also referred to as prime cost.
- Indirect costs, also known as manufacturing overhead, are all the expenses of a manufacturing operation that are not tied to the production of specific finished goods but that a company nevertheless needs to bear in order to keep the operation going. These include indirect materials and labor, supplies and repair parts, rent and utilities, depreciation, financial costs, and pretty much everything else that a manufacturing company needs to deal with which is not a direct cost. Examples of indirect materials and labor include maintenance equipment, cleaning supplies, supporting manufacturing staff expenses, quality control specialists, production managers, etc.
A simple formula for calculating Total manufacturing Cost is:
TMC = (Direct materials + Direct labor + Direct misc.) + Manufacturing overhead
Or in other words:
Total Manufacturing Cost = Prime cost + Manufacturing overhead
Factory Profit/Loss
Calculating TMC is imperative for gaining insights into the financial health of a manufacturing business and making the operation more cost-effective. Among other key metrics that stem from it is Factory Profit/Loss. This KPI determines the difference between the cost of production of a finished product and its market value. If the cost of production is lower than a product’s market value, a markup is added which makes up the factory profit. If cost of production is higher, the value will be negative, culminating in factory loss. Manufacturers use this to decide whether to manufacture a product or sub-assembly, or to procure it.
COGM and COGS
The total manufacturing cost also informs two crucial KPIs for determining a company’s Gross Profit and Gross Margin – Cost of Goods Manufactured (COGM) and Cost of Goods Sold (COGS).
- Whereas TMC shows the total expense of a manufacturing operation writ large, the Cost of Goods Manufactured limits this to only the goods that were finished during a financial period. If any products were unfinished by the time the production period ends, these items are left out of COGM and constitute the ending work in process inventory (WIP). If all production finishes by the end of the period, however, COGM equals TMC. Calculating COGM is important for manufacturers because it gives a reliable insight into the level of production costs and profits relative to sales at the end of the fiscal period.
COGM = Beginning WIP + Total Manufacturing Cost – Ending WIP
- Building on COGM, the Cost of Goods Sold designates only the total cost of goods that were sold within the financial period. It is used to determine gross profit and estimate the company’s bottom line. COGS is listed on the income statement as an expense and gives companies insight into setting profitable pricing, mediating the taxable income level, and tracking profitability.
COGS = Beginning Finished Goods Inventory + COGM – Ending Finished Goods Inventory
Variable and Fixed Costs
There are a number of other cost-centric KPIs in manufacturing that increase control over the fiscal performance of a manufacturing operation and allow for better decision-making regarding production capacities, like total cost, average cost, and marginal cost. Another among these is the distinction between variable and fixed costs.
Variable costs are expenses that a company bears proportional to its production volume. As production output increases, so will the variable costs, and vice versa. A good example would be the costs of packaging for finished goods but also utilities like heating and water, as well as some labor expenses, etc. Variable costs are liquid and can be adjusted. Fixed costs, on the other hand, include concrete expenses that generally cannot be adjusted easily. These would include expenses such as storage facility or warehouse mortgage fees, bank loans, machinery and equipment depreciation, and some labor costs. Insight into variable and fixed costs helps manufacturers make decisions on production volumes, adjust to market trends, etc.
Read more about Production costs
Inventory Valuation
As all expenses relevant to manufacturing divide into different types of costs, physical item inventory is divided into three basic types: Raw Material Inventory, Work-In-Process Inventory (WIP), and Finished Goods Inventory. The function of Raw Materials and Finished Goods inventories is quite self-explanatory. WIP inventory, however, is a little bit more complex. WIP constitutes items already in the manufacturing process that have not been finished yet.
This distinction is important from a manufacturing accounting viewpoint because WIP inventory has already incurred some production costs like materials, labor, and overhead which need to be taken into consideration to ensure the accounts reflect accurate finances. The value of inventories plays a large role in a company’s finances and profitability, as it directly affects both COGM, COGS, and tax liability. In fact, large swaths of manufacturing accounting can be viewed as aspects of the larger inventory management process.
Calculating Inventory Values
There are a number of methods in which to conduct inventory valuation, each beneficial in different use cases and markets, or for different types of manufacturing. These are generally called inventory valuation or costing methods, or cost-flow assumption methods. Since inventory valuation directly affects the tax burden, the process is usually regulated and needs to conform to Generally Accepted Accounting Principles (GAAP) in the US, or the International Financial Reporting Standards (IFRS) elsewhere. Although there are many different methods for calculating the value of inventory, GAAP and IFRS only accept four of them – FIFO, LIFO, SE, and WAC. Let us go through them quickly:
- The First In, First Out, or FIFO method is based on the assumption that the first item produced is the first item sold, or concurrently, that the first item in the raw material inventory will be used first in WIP. As prices of items generally rise over time due to inflation, using FIFO permits higher valuing of ending inventory. This means lower COGS and higher reported gross profit. However, it also means a higher taxable income.
- The Last In, First Out, or LIFO method is the opposite of FIFO, assuming that the last item produced is the first one sold, or that the newest raw material will constitute the first WIP. The LIFO method generally maximizes COGS and minimizes ending inventory values, leading to a reduction in net income, beneficial for reducing the tax burden.
- The Specific Identification (SI) method is the straightforward option. SI assumes that each inventory item’s price is kept track of separately, providing the most accurate inventory valuation possible. SI can realistically only be used by certain manufacturing industries and mostly discrete manufacturers, however, as attempting to keep track of individual toothpicks or cupcake toppings, for example, is hardly practical.
- The Weighted Average Cost (WAC) method is a middle-ground one, wherein the cost of goods available for sale is divided by the number of finished goods available for sale. This yields a weighted average cost per unit that can be assigned to ending inventory as well as COGS. WAC is useful, for example, for the aforementioned toothpick manufacturer, wherein individual cost per unit is very difficult or impossible to assign.
Inventory Counting
In addition to per-part inventory costing, it is also important to track the total number of on-hand inventory units. The two common types that inventory can be arranged in light of this are the perpetual and the periodic inventory system.
- The periodic inventory system organizes inventory counting between predetermined time periods. All of the inventory items are physically counted and COGS is calculated concurrently. The periodic system is useful for smaller businesses with smaller inventories that do not consist of very diversified items. The downside is that information on inventory levels is truly accurate only right after counting.
- The perpetual system is more complex but yields far more accurate data on inventory levels. It relies on collecting and aggregating continuous data on all inventory movements. As a result, COGS can be calculated continuously as well. Perpetual counting is made available almost exclusively thanks to computerized inventory management software. In most use cases then, a perpetual system is far superior to periodic counting, albeit it comes at the price of having to implement dedicated software.
Read more about Inventory valuation methods
Production Costing Methods
A final aspect of manufacturing that largely informs manufacturing accounting is production costing. Since adding together direct costs is generally a straightforward affair, this mostly revolves around calculating the per-product share of indirect costs. There are various costing methods that each inform cost accounting in their own way. We will go through four of the more common ones.
Standard Costing
Standard costing is perhaps the most common costing method. It is based on calculating standard rates for the direct and indirect costs of products. These predetermined “standards” are usually based on the company’s previous experiences and are routinely updated to reflect market fluctuations.
Standard costing is very beneficial for creating and polishing budgets as it gives predefined cost estimates that can be measured against actual expenses. This provides insight into company expenditure and reveals inefficiencies. The chief disadvantage lies in having to routinely update the standards which can be arduous in case of constantly changing market conditions.
Job Costing
The job order costing method calculates costs per manufacturing project or unit, making it useful for make-to-order manufacturers, construction manufacturers, and the like. A typical job costing process for a project will sum together its direct costs and add to that a share of the company’s manufacturing overhead proportional to the amount of storage space, utilities, etc. that was allocated for the project.
Job costing is advantageous for returning close-to-exact cost values per finished project or finished good. It is sometimes difficult to manage, however, as individual tracking and allocation of costs can be time-consuming.
Process costing
This costing method is similar to job costing, however, it calculates item costs by adding together the direct costs and overheads per processing step of a product’s lifecycle, rather than per individual item or job. This makes it a favorable costing method for process manufacturers and other companies that otherwise produce large numbers of identical units.
Process costing is beneficial for saving time as calculating costs need not to be completed for each individual unit. The downside is that the costs per unit can become inaccurate since rounding up costs per process can introduce discrepancies.
Activity-based costing (ABC)
ABC is a common albeit complex costing method that relies on separately identifying the indirect costs of all production activities and allocating them to cost pools – groups of related overhead costs occurring with specific activities. The overhead cost of a cost pool is then divided by the number of units in the activity to arrive at the activity rate – a fixed amount that is added to each unit’s cost.
ABC is a very accurate costing methodology that helps to factor indirect costs into unit pricing. It can be more difficult to implement than standard or job costing, however, as a more detailed overview is required over the manufacturing process.
Manufacturing accounting best practices
As we have seen, manufacturing accounting includes insight into processes absolutely fundamental for ensuring the financial health of your manufacturing business. If approached with sufficient scrutiny, manufacturing accounting will grant knowledge of all of the operational costs of a company and enable managers to make informed decisions on how to drive revenue and increase profit. To end this article, let us take a look at some manufacturing accounting best practices that should be on top of the to-do list.
- Increase financial know-how. Whereas the financial heavy lifting should be left to professional accountants, it still pays to understand the financial side of a manufacturing operation. A big part of manufacturing accounting revolves around compiling reports to enable management to make better-informed business decisions. It is thus imperative for decision-makers to have a sufficient understanding of financial data.
- Decide between cash basis or accrual accounting early on. Cash basis accounting is an accounting strategy whereby expenses, as well as profits, are reported once funds physically change hands. Accrual accounting, on the other hand, is a more complicated albeit arguably more useful strategy wherein transactions are reported as sales take place regardless of when payments are made. Accrual accounting is the far more popular option. Many especially smaller manufacturers still opt for cash basis, however. If planning to scale big, bear in mind that in the US, cash basis accounting is only accepted by IRS as an exception and is limited to companies with under $26 million in average yearly revenue.
- Budget and invest realistically. Putting in place a spending budget at the beginning of the financial period can be a great aid in leveraging risks and managing investments. The budget should always be determined by experts and be based on thorough insight into the company’s previous financial performance as well as market analysis. Making any large-scale investments should similarly be preceded by a rigorous feasibility and ROI analysis.
- Always keep funds on hand. Unexpected expenses might arise very suddenly in the modern manufacturing space. If all of the company’s funds are tied up in assets or stock, failing to react to an emergency or a business opportunity can incur a significant financial hit to your company. Payments and costs should thus be covered strategically. A good idea is to also implement effective inventory control – having optimal inventory levels will not only tie up funds in unnecessary stock but lower overhead costs and minimize waste.
- Use competent manufacturing accounting software. Handling manufacturing accounting manually is possible but highly impractical in most cases. Manufacturing accounting software is designed to automate most of the bookkeeping and can vastly increase financial insight and inventory management efficiency. Good providers go far beyond simply calculating cost metrics and compiling reports – they can hugely simplify analyzing trends, use intelligent forecasting, include compliance standards, and much more.
We recommend using software that is well integrated with the overall production and inventory management solution of choice. This ensures seamless data movement between the shopfloor, inventory, and the back office, and further simplifies managing your business. If you are yet to implement a manufacturing ERP system, consider picking one with built-in financial reporting capabilities. For example, MRPeasy includes one-click product cost estimating, intelligent reporting, and built-in integrations with major financial software providers like Xero and QuickBooks Online.
Key Takeaways
- Manufacturing accounting is a group of inventory and production management processes used for monitoring and controlling the costs involved with manufacturing products.
- The process mostly revolves around cost accounting practices and conducting inventory valuation and production costing.
- The most important metrics that manufacturing accounting tracks are the total cost of production, manufacturing overhead, cost of goods manufactured, and cost of goods sold.
- Best practices for manufacturing accounting include increasing financial know-how, picking a suitable accounting strategy, realistic budgeting, managing cash flow, and choosing competent manufacturing accounting software.
- Manufacturing accounting software should be properly integrated with the overall inventory management system to avoid data duplication and increase operational efficiencies.
You may also like: What is Accrued Payroll in Manufacturing Accounting?