Maintenance Management – Improving Efficiency by Becoming Proactive
Maintenance management is essential for every company looking to increase efficiency and safety in the workplace. Taking a proactive approach in upkeep policies is made easy and affordable with maintenance management functionalities in a modern manufacturing software.
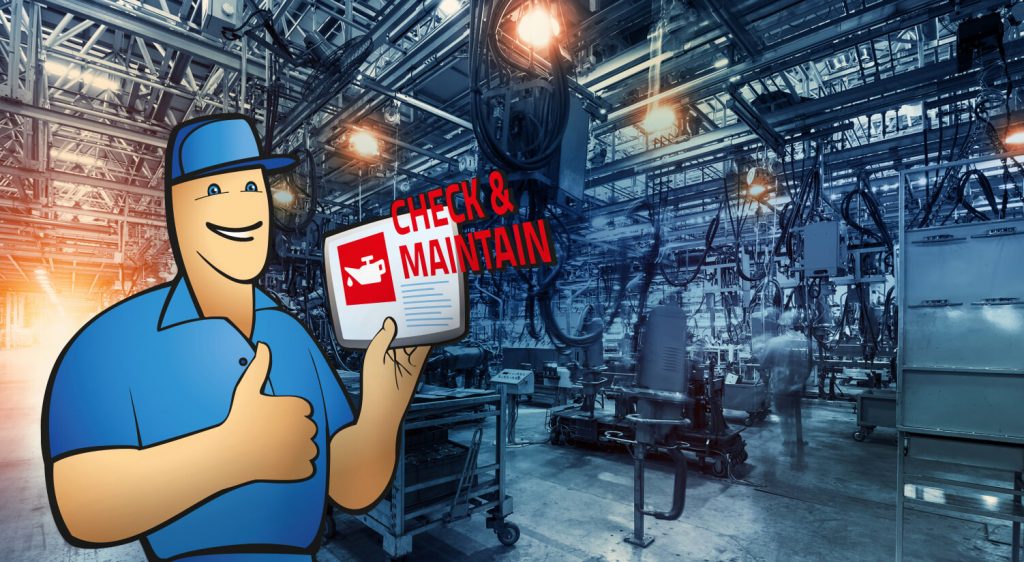
You can also listen to this article:
What is maintenance management?
Maintenance management is the set of procedures used to service a company’s manufacturing equipment to keep it safe, functional, and efficient.
Whether you are a food producer with big agricultural and processing machines; a woodworks with table saws, lathes, and drills; or a garment manufacturer that uses spinning, cutting, and sewing machines – proper machinery maintenance is essential in any manufacturing company.
Your maintenance management practices will always reflect in the performance of your whole business.
Overall Equipment Effectiveness, Capacity Utilization, Yield, Manufacturing Cost per Unit, Downtime in Proportion to Operating Time – all these important metrics are directly or indirectly related to the state of your equipment.
When a machine breaks down, it ultimately signifies losses for the company due to unseen repair costs, machine replacements, delayed shipments, and loss of revenue caused by the halt in production.
If your equipment is not properly serviced, it could also contribute to the diminished quality of your products and to the increased use of power in your facility.
However, with the introduction of proper maintenance procedures, you can keep machinery failure at a minimum, ensuring the maximum possible efficiency of your equipment and the safety of your workers.
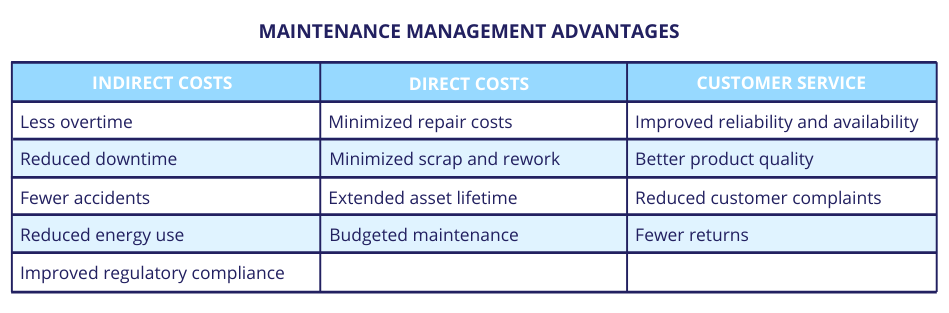
Reactive vs. proactive maintenance
Reactive maintenance means repairing the equipment when breakdowns occur.
The proactive approach, however, aims to bring machinery breakdowns to a minimum by utilizing preventive and predictive measures.
Even though a proactive maintenance program requires some initial investments, it results in more cost-effective, efficient, and durable equipment.
Preventive measures are affordable even to smaller businesses, requiring only the implementation of a maintenance plan that is either time-based or usage-based.
For example, you can perform maintenance once every quarter, after every thousand hours of usage, or after a set amount of pieces processed.
This regular upkeep program is a very easy solution to introduce, but it could save you tens of thousands in repairs.
Predictive measures, however, utilize high technology like IoT, sensors, and other condition monitoring equipment to gauge parameters such as temperature, vibration, resistance, etc. in order to predict when maintenance should be performed or when a part of a machine should be replaced.
Predictive maintenance systems are very effective, but also very complex and expensive, so they only become feasible when the company is quite large.
For smaller players, a preventive upkeep program is sufficient.
Read more about Reactive, Preventive, and Predictive Maintenance.
How often should maintenance be performed?
Usually, your OEM manual will provide you with guidelines as to how often the equipment should be inspected, cleaned, or maintained.
As a rule of thumb, you should perform upkeep more often for assets that get more usage, are critical to your operations, or are more expensive and susceptible to breakdowns.
On the other hand, resources allocated for the maintenance of non-critical, less-expensive, or rarely used machinery can be kept at a minimum.
Ideally, you should keep data as to how performing upkeep correlates with improved efficiency, and base your maintenance management practices on that.
In addition, standard operating procedures should be established that set a model for how each task is performed, so that maintenance would be consistent.
Maintenance management functionality in manufacturing software
Some modern manufacturing ERP systems include a maintenance management system.
This preventive upkeep capability allows the user to automatically track the maintenance cycles of their workstations.
Maintenance cycles can be set for each workstation either in calendar days, hours of usage, or units processed.
The workstation page will then display how many days, hours, or units there are until upkeep needs to be performed again.
When time passes or when manufacturing operations are reported by workers, these maintenance counters are updated accordingly; when the machinery is serviced, the counters are reset to zero.
Even though this functionality is very simple and clear-cut, it could serve as a basis for your company’s maintenance processes.
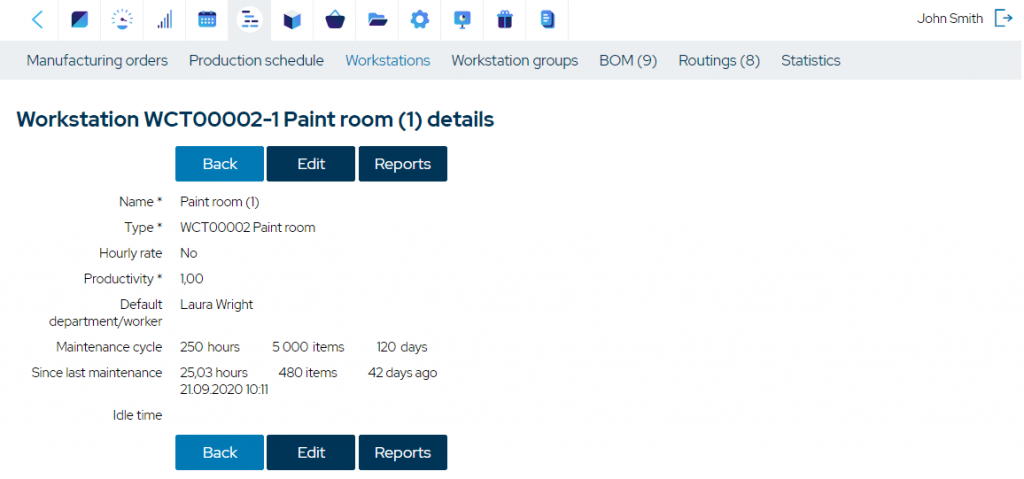
Setting up an asset maintenance plan
A good plan takes all aspects into account – not only do you need to specify the inventory of assets and their individual methods of maintenance, but you also need to detail the human resources, tools, time, and materials (including spare parts) used for the upkeep.
Everything up to the lubricant blend you are going to use should be marked down in order to account for all the factors that go into planning asset maintenance.
That means that each time a variable changes, the plan has to be revised and modified as well – even changing up the oil you use could tweak the outcome due to differences in its chemical composition and characteristics.
When the details are set, a schedule must be created according to the OEM manual.
You can also enter the OEM manual information into your MRP system to have it automatically alert you of when maintenance should be performed.
Having a strong, highly detailed plan with clear and concise instructions can help you budget, and avoid human error when the maintenance should be performed by less experienced staff members.
Maintenance checklist
To make the standard procedures easy to follow, a checklist would come in handy.
A good checklist communicates the steps in a sequence, clearly and comprehensively.
It includes the requirements of:
- Tools
- Spare parts and materials
- Time
- Protective equipment
Then, it details:
- Safety instructions
- Asset-specific attributes
- Sequence of actions
In addition, it should include:
- Visual aids such as photos or diagrams
- Compliance requirements
Copies of a maintenance checklist should be kept by the asset, with the OEM manual, and in a maintenance folder.
A good MRP software would also allow attaching documents and notes to workstations, making instructions and checklists easily accessible on the shop floor with a mobile device.
Apart from servicing your manufacturing equipment, maintenance should be regularly performed throughout the facilities.
Conclusion
Every manufacturing company needs to do maintenance management in order to keep its equipment well-functioning, to save on repairs, to elevate workplace safety, and increase customer satisfaction levels by offering high-quality products in the timeframe specified.
Even though it might sound like a lot of work, becoming proactive in your asset maintenance policy is not a very resource-consuming endeavor anymore if you opt for a preventive approach.
Using manufacturing software to track the usage of your machinery or the equipment’s maintenance cycle time allows you to easily plan and schedule the upkeep of your assets.
A proper plan with a checklist will, in turn, minimize the chance for human error, maximize the efficiency of your equipment, and ultimately make your facility a safer workplace.
You may also like: Manufacturing Execution System Software as a Cloud-Based Solution