Top 15 Lean Manufacturing Tools in 2025
Lean manufacturing tools help you organize workspaces and fix problems before they can slow you down. With these tools in place, you’ll be able to lower costs, boost quality control, and give your customers exactly what they want.
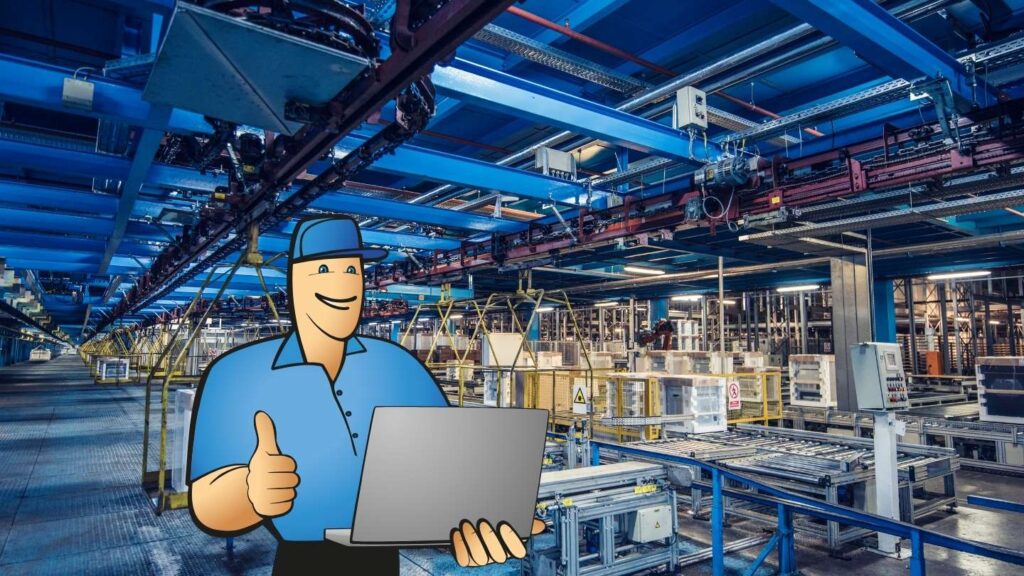
What is lean manufacturing?
Lean manufacturing is all about working smarter, not harder. At its core, it’s a way to cut waste and focus only on what adds value for your customers.
Lean manufacturing is built on five core principles that guide every step of the process. It starts with defining value, which means focusing on what customers truly care about and guaranteeing that every action leads to their satisfaction. Next, manufacturers map the process by analyzing each production step to uncover where resources are being wasted. Once inefficiencies are identified, the goal is to streamline workflows so everything moves smoothly without unnecessary interruptions. Lean also emphasizes establishing a pull system, which means producing only what is needed when it’s needed, rather than stockpiling inventory.
Lean encourages teams to continually look for ways to improve. No matter how efficient a process becomes, there’s always room for improvement.
Types of lean manufacturing tools
Lean manufacturing relies on a variety of tools to streamline operations, eliminate waste, and improve productivity. These tools fall into four main categories, each playing a unique role in achieving Lean’s goals.
1. Visual aid tools
Visual tools are essential for creating clarity in Lean manufacturing. They simplify complex processes and make it easier for teams to track progress, spot issues, and respond quickly. Common examples include visual boards, Kanban cards, and other signaling systems. These tools enable workers to see the status of production at a glance and make data accessible without needing lengthy explanations. By highlighting deviations and providing actionable insights, visual aids empower teams to stay aligned with production goals while maintaining a culture of continuous improvement.
2. Problem-solving tools
Problem-solving tools in Lean manufacturing focus on identifying the root causes of inefficiencies and eliminating them systematically. Methods like root cause analysis and PDCA cycles are widely used to dissect issues and uncover underlying problems. These problem-solving techniques foster a proactive mindset, encouraging teams to address challenges early, minimize disruptions, and ensure consistent quality throughout operations.
3. Process optimization tools
Process optimization tools in Lean manufacturing focus on refining workflows to eliminate inefficiencies and improve productivity. For example, 5S organizes and standardizes workspaces, creating an efficient and visually manageable environment. Similarly, Kaizen promotes continuous improvement by encouraging small, incremental changes that lead to significant gains over time. Another key tool, Just-in-Time (JIT), minimizes waste by producing only what is needed, when it is needed, aligning production closely with demand. These methodologies not only streamline operations but also foster a culture of proactive problem-solving and sustained efficiency.
4. Software
Lean manufacturing software solutions provide a digital platform for managing and improving processes. These tools include manufacturing ERP systems, Manufacturing Execution Systems (MES), and Lean-specific software like eKanban platforms. By offering real-time data analysis, tracking, and reporting, such software enables better decision-making and resource allocation. Automation and predictive analytics enhance production planning, inventory control, and maintenance scheduling. Integrating software into Lean practices ensures greater accuracy, scalability, and adaptability to meet evolving demands.
Top 15 lean manufacturing tools
Visual aid tools
1. Kanban
Kanban is a Lean scheduling system that helps manage workflow and avoid overproduction by visualizing tasks. This tool uses cards or digital signals to indicate when inventory or tasks need replenishing or advancing to the next step. This way, work only moves forward when there’s customer demand.
Setting up a Kanban system requires creating a visual board with columns representing different stages of a process, such as “To Do,” “In Progress,” and “Done.” Each task or inventory item is represented by a card that moves through the columns as it progresses. This visual system helps teams quickly spot bottlenecks, manage resources, and respond to changing demands.
2. Andon
Andon is a real-time alert system that empowers teams to address issues immediately. Originally pioneered by Toyota, Andon uses visual signals, such as lights, screens, or sounds, to notify workers when something goes wrong in the production process. For example, a worker might pull an Andon cord or press a button to signal a defect or equipment malfunction.
Implementing an Andon system involves setting up clear communication protocols and ensuring that all team members understand how to use the system effectively.
3. Value Stream Mapping (VSM)
Value Stream Mapping (VSM) is a lean management visual tool used to map out every step in a process to identify and eliminate waste across the supply chain. Also developed by Toyota, VSM provides a clear picture of how value flows through a process and highlights cycle time and lead times in each step to show where time, resources, and materials are wasted.
VSM is key in lean methods to pinpoint muda (the Japanese word for “waste” and a central concept in the Toyota Production System.
Create a Value Stream Map by involving team members directly. Map each step in sequence and use flow charts to visualize where process improvement can make the most impact.
Problem-solving tools
Every challenge is an opportunity to improve. Lean problem-solving tools help teams uncover the real issues behind problems and implement lasting solutions. With these tools, manufacturers can turn setbacks into progress and create a culture of continuous improvement.
4. Root Cause Analysis (RCA)
Root Cause Analysis (RCA) is a method used to identify the fundamental cause of a problem and eliminate it to prevent recurrence. Unlike quick fixes, RCA digs deeper to understand why an issue occurred in the first place. RCA is often used alongside tools like the “5 Whys,” where you ask “Why?” repeatedly until you reach the root cause. This approach allows teams to address the problem at its baseline, instead of only treating the symptoms.
To conduct RCA, identify the problem and find out everything you can about what happened. Then, use the 5 Whys to trace the problem back to its origin. Once the root cause is found, implement a solution that directly addresses it and monitor the results.
5. Plan-Do-Check-Act (PDCA)
Also called the Deming Cycle, the Plan-Do-Check-Act (PDCA) is a cycle for continuous improvement that provides a structured approach to solving problems and improving processes. The four steps—Plan, Do, Check, and Act—guide teams through testing changes, reviewing results, and making adjustments. PDCA encourages learning through small, incremental changes
PDCA starts with the Plan step. Here, you identify a problem and develop an improvement plan. In the Do step, you implement the plan on a small scale. The next step is to Check, which is done by measuring the results and comparing them to the expected outcomes. Finally, you Act based on the findings. If the change is successful, implement it across the board. If not, revise and repeat the cycle.
Process optimization tools and methodologies
Streamlining workflows and eliminating waste are at the heart of Lean manufacturing, and process optimization tools make this possible. These tools focus on improving efficiency, reducing errors, and maximizing productivity by refining how work gets done.
6. 5S (Sort, Set in Order, Shine, Standardize, Sustain)
5S is one of the most foundational Lean tools, created in Japan as part of the Toyota Production System. It’s a simple but powerful method for creating an organized, clean, and efficient workspace with clear visual management to support each step.
The “5S” stands for five Japanese words that translate to Sort (Seiri), Set in Order (Seiton), Shine (Seiso), Standardize (Seiketsu), and Sustain (Shitsuke). Each “S” represents a step in building an efficient, orderly workspace that’s easy to manage and maintain.
The first step, Sort, is all about removing clutter from the workspace. Next, Set in Order means arranging tools and materials in a way that supports the workflow. Shine involves thoroughly cleaning the area, so it’s safe and efficient. Standardize ensures everyone follows the same steps to keep the workspace organized and clean. Finally, Sustain keeps the system in place over time through regular checks and improvements.
To implement 5S, start by involving the entire team in the sorting and organizing process. This creates a shared sense of ownership and responsibility for maintaining the area. Periodic audits can help ensure each step of 5S is still being followed.
7. Kaizen
Developed as part of Toyota’s manufacturing approach, Kaizen (which means “continuous improvement” in Japanese) is a Lean tool that promotes process improvement through real-time small adjustments. The idea is simple: Small adjustments over time lead to big gains in quality, productivity, and efficiency.
This approach addresses issues like overprocessing and production line delays, driving ongoing improvements. Key Performance Indicators (KPIs) can measure Kaizen’s effectiveness. Over time, Kaizen builds a proactive team that’s invested in total productive maintenance (TPM), which aims to minimize breakdowns.
To implement Kaizen, businesses create an environment where team members at all levels can contribute ideas for improvement. This can mean anything from adjusting the layout of a workstation to finding a quicker way to handle a repetitive task.
The best Kaizen practices include regular meetings, often called “Kaizen events” or “blitzes,” where employees suggest improvements and discuss issues directly impacting their work. Over time, Kaizen builds a proactive, engaged team that consistently seeks out ways to improve.
8. Just-in-Time (JIT)
Originating from Toyota’s manufacturing system, Just-in-Time (JIT) reduces overprocessing by producing only what is needed, when it is needed. As a result, JIT minimizes excess inventory and reduces storage costs. The main idea is to “pull” materials and products through the production process only as needed, rather than “pushing” large quantities of inventory into storage.
To implement JIT, businesses need to work closely with suppliers to ensure reliable and timely deliveries. Production planning is crucial with JIT. Schedules and workflows must align closely with demand forecasts.
You can combine JIT with Kanban because these two tools complement each other. JIT reduces excess inventory by producing only as needed, while Kanban visually signals when new items should be made or moved. Together, they keep production responsive to demand and help eliminate waste.
9. Poka-Yoke (Error Proofing)
Poka-Yoke, or “error-proofing,” eliminates big losses by preventing mistakes before they happen. Created by Shigeo Shingo at Toyota (you may be noticing a trend), Poka-Yoke aims to design processes that either prevent errors or make them immediately obvious. This lean principle tackles the problem of human error in repetitive work like manufacturing. When implemented, it eliminates costly rework and reduces the chances of defects reaching customers.
Poka-Yoke introduces safeguards that help workers avoid common errors. An example of Poka-Yoke is to add color-coded connections that only fit one way. Poka-Yoke empowers teams to work more reliably by building error prevention directly into the process.
10. Statistical Process Control (SPC)
Statistical Process Control (SPC) is a data-driven method for monitoring and controlling variation in manufacturing processes. By analyzing performance metrics, SPC helps teams identify trends, detect potential issues early, and maintain consistent quality. Tools like control charts make it easy to visualize data and keep processes within desired limits.
11. Total Productive Maintenance (TPM)
Total Productive Maintenance (TPM) focuses on maximizing equipment efficiency by minimizing downtime and breakdowns. By involving operators in routine maintenance and creating a proactive approach, TPM aids in machine reliably. This method not only improves productivity but also extends the lifespan of equipment.
Lean manufacturing software solutions
As Lean manufacturing evolves, technology has become an essential partner in driving efficiency and eliminating waste. Software solutions bring the principles of Lean to life by automating processes and integrating key workflows.
12. MES (Manufacturing Execution System)
A Manufacturing Execution System (MES) helps manufacturers stay in control by managing production in real-time. This software tracks and coordinates shop floor activities which provides greater visibility into processes as they happen. MES keeps operations running smoothly by monitoring equipment performance, including the overall equipment effectiveness (OEE),, tracking worker productivity, and scheduling tasks It also helps manage materials so they are available when needed.
One of the biggest advantages of an MES is its ability to spot potential bottlenecks or issues early. This allows teams to make adjustments before problems escalate. By integrating data from across the production floor, MES helps manufacturers stay agile and responsive.
13. QMS (Quality Management Software)
Quality Management Software (QMS) is key to maintaining consistent quality and compliance across all manufacturing processes. It automates tasks like defect tracking, inspection scheduling, and documentation management. QMS helps reduce waste and rework by identifying issues so you can resolve them before they impact production.
QMS also supports compliance with regulations by keeping all quality-related documentation organized and up-to-date. This is especially important in industries like automotive, aerospace, and healthcare, where standards are non-negotiable.
Project management software
Project management software simplifies the organization and execution of manufacturing projects by centralizing information and providing tools to plan, monitor, and communicate effectively. In addition to breaking down projects into tasks, teams can use this software to set deadlines and allocate resources. With built-in features like Gantt charts, project management software keeps projects on schedule.
14. MRP I (Material Requirements Planning)
Material Requirements Planning (MRP I) helps optimize inventory and production scheduling to match customer demand. By analyzing demand forecasts, MRP I ensures that the right materials are available at the right time. This prevents shortages or overstocking.
MRP I also streamlines procurement by automating reorder points and scheduling material deliveries. It’s an essential tool for businesses looking to balance efficiency with flexibility in their operations.
15. ERP (Enterprise Resource Planning) or MRPII
Manufacturing ERP, also called Manufacturing Resource Planning or MRP II, integrates all aspects of a business into a single, cohesive system. This covers production, inventory, and finance. ERP provides manufacturers with a comprehensive view of their operations to aid in decision-making and cross-department coordination. With ERP, manufacturers can automate processes and gain real-time insights into performance.
Key takeaways
- Lean manufacturing focuses on eliminating waste and prioritizing actions that deliver value to customers while improving efficiency.
- Tools like Kanban and Andon make workflows transparent, enabling teams to track progress and address issues promptly.
- Methods like Root Cause Analysis (RCA) and PDCA help uncover inefficiencies and implement solutions that address the root causes of problems.
- Strategies like 5S and Kaizen ensure workspaces are efficient and processes continually improve, fostering sustainable productivity.
- Tools such as MES and ERP integrate processes and provide real-time insights, allowing businesses to adapt quickly and reduce waste.
- The emphasis on continuous improvement and team involvement is key to achieving long-term success in Lean manufacturing.
Frequently asked questions (FAQ)
Small businesses can start by adopting simple, low-cost tools like 5S and Kaizen to organize workspaces and encourage incremental improvements. Modern manufacturing ERP systems are also available for businesses with minimal budgets.
Sustaining Lean improvements requires regular training, leadership commitment, and periodic audits to ensure practices like 5S and Kaizen remain effective. Encouraging a culture of continuous improvement and involving employees in monitoring and refining processes helps maintain progress.
The time to see results varies depending on the scale of implementation and the complexity of processes. While some changes, like implementing 5S, can yield immediate improvements, larger initiatives like JIT or Value Stream Mapping may take weeks or months to demonstrate significant impact. Consistency and commitment are key to long-term success.
You may also like: 12 Tips for Improving Inventory Management Efficiency