How to Reduce Lead Times in Your Supply Chain?
Reducing lead times is crucial for manufacturers, especially with rising customer expectations and tough competition. This article discusses how to reduce your lead times through better supply chain planning, streamlined production, and improved vendor management.
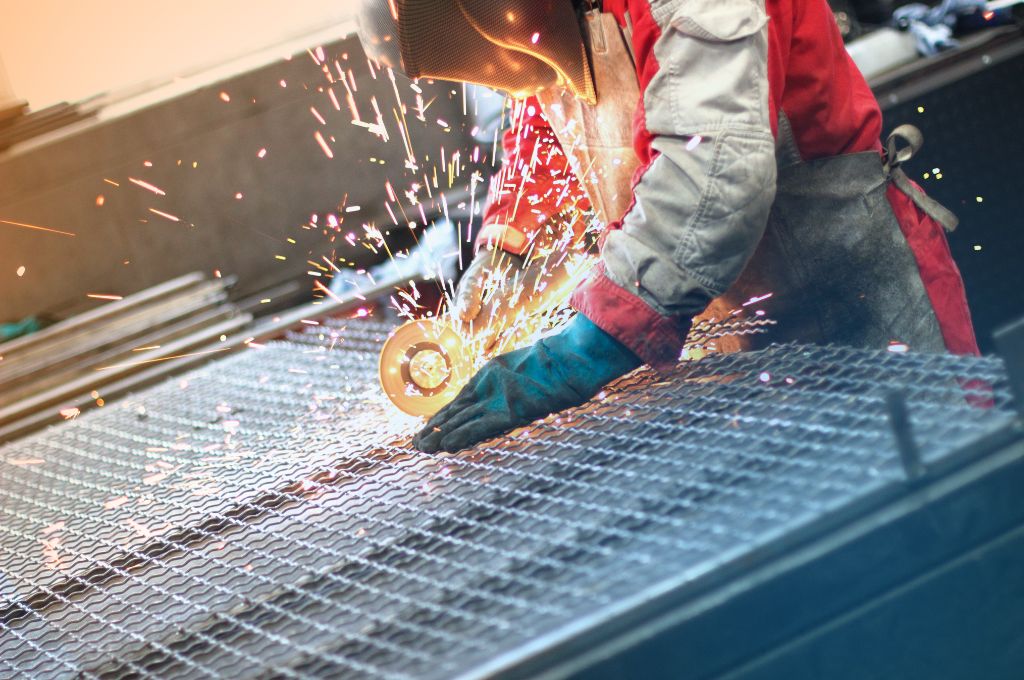
What is lead time?
Lead time is a metric that measures the total amount of time it takes to complete a process. A classic example is customer lead time, which tracks the time from a customer placing an order to when it’s delivered or completed.
Managing lead times well is key to meeting deadlines, tracking production efficiency, and keeping customers happy. Shorter lead times can give a business a competitive edge by delivering orders faster and preventing stockouts.
The different types of lead times
Let’s look at the three basic types of lead times and how they affect the supply chain.
Material lead time (also known as order lead time or supplier lead time) is the time it takes for your suppliers to deliver the raw materials that you need to start production. If you have a longer lead time between placing your purchase orders and receiving the raw materials, your entire production process will be delayed. This, of course, will lengthen your customer lead time in turn.
Production lead time refers to the cycle time it takes to manufacture the product once you have the materials on hand. The clock starts when you receive the manufacturing order and stops once your finished product is ready for order fulfillment.
Customer lead time, as mentioned, is the total time from when a customer places an order to when they receive the finished product. It includes material and production lead times with the added time needed for product delivery. Customer satisfaction can be directly tied to your customer lead time as receiving an item on time (or even ahead of schedule) positively affects your reputation. Satisfied customers are more likely to leave a positive review and continue doing business with you in the future.
Why do lead times matter?
Long lead times can cause a lot of problems. They can disrupt your supply chain and turn happy customers into disgruntled ones. Let’s take a closer look at why lead times matter.
Frustrated customers
When a customer places an order, they expect to get what they ordered by the promised time. As the days go by, their excitement can turn into frustration. If the promised delivery date is exceeded, they may start looking for other companies that can deliver faster. Delays also negatively impact customer trust and hurt customer retention.
Decreased production efficiency
Longer lead times can also disrupt internal operations, impacting your production efficiency. When materials or parts take too long to arrive, your production process can slow down or even come to a halt. This may lead to idle time for workers and equipment, which not only wastes resources but also increases overall production costs.
Bloated inventories
If frustrated customers weren’t enough to concern you, let’s talk about the extra inventory you might keep on hand due to long lead times. Sometimes, long lead times aren’t your fault. It may be that your suppliers are slow or demand forecasts are unpredictable. Many businesses may find it easier and safer to keep extra safety stock on hand as a buffer. But there are several downsides to doing this:
- You’re tying up your money. Extra inventory means that you’ve tied up a significant amount of your capital in products that haven’t been sold. This reduces your cash flow.
- You need more storage space. The more inventory you hold, the more storage space you need. This can lead to higher manufacturing overheads across the board like rent, utilities, and insurance.
- You risk obsolescence. The longer a product sits around, the more it’s at risk of becoming outdated. This renders the product unsellable. You may end up discounting the product or completely writing it off.
Keeping extra inventory on hand is a short-term fix that can lead to long-term problems. Instead of relying on excess inventory, implement one of the following strategies to improve your supply chain management.
5 steps to reduce your lead times
As mentioned above, long lead times can lead to disgruntled customers and unmanageable inventories. The good news is that you can take steps to cut wait times. Here’s how:
1. Implement the Just-in-Time strategy
Managing inventory effectively means having just enough stock to meet customer orders. This is done without tying up too much money or increasing storage costs. It’s known as Just-in-Time (JIT) inventory management.
To make JIT work, you must build relationships with reliable and preferably local suppliers. Your suppliers should be able to deliver your raw materials on time. JIT also works best if you’ve taken steps to implement the right warehouse management system. Your system should track stock levels in real time and include automatic reorder points when necessary.
JIT doesn’t eliminate all safety stock. It’s a best practice to maintain a small amount of safety stock for essential items just in case there’s an unexpected delay or spike in demand. But by implementing JIT, you will reduce excess stock and free up capital that can be used elsewhere in your business.
2. Build stronger relationships with your suppliers
If you want to reduce lead times, start with your procurement process and your suppliers. Building strong supplier relationships is essential. Here’s what to focus on:
- Reliability. Choose suppliers who deliver on time, every time. Reliability is more important than just getting the lowest price.
- Good communication. Look for suppliers who are good communicators. If your supplier doesn’t respond to calls or emails in a reasonable time frame, you could face delays that disrupt the entire production process. Your suppliers should keep you in the loop about the status of your orders and any possible delays down the line.
- Diversification. While you should seek to build strong relationships with key suppliers, don’t rely on just one supplier. It’s best to have multiple vendors available if something goes wrong on your supplier’s end.
3. Optimize production scheduling
The next step is to get your production schedules right. Here’s a brief overview:
- Prioritize orders. Focus on the most critical tasks first. Prioritize orders based on customer importance, deadlines, and/or resource availability.
- Use smart scheduling tools. Invest in scheduling software that helps you create detailed schedules and manage them efficienclty. These tools can juggle factors like machine availability, workforce capacity, material supply, etc.
- Minimize downtime. Identify and fix any bottlenecks in your production process. This may require reorganizing your workflow, balancing workloads, or upgrading equipment to keep everything moving faster.
- Stay flexible. Equipment can break down, material shortages can cause unexpected delays, etc. This is why you should always build some amount of flexibility into your operation. Avoid locking yourself into a rigid schedule that can’t accommodate any changes.
- Identify any bottlenecks. If there are bottlenecks in your production process, figure out what they are and fix them. A fix may look like a reorganized workflow or an equipment upgrade. Do what is needed to optimize your process.
- Monitor and tweak. Keep a close eye on your production schedule. Use real-time data to spot and fix potential problems before they escalate. Also, commit to regularly reviewing and refining your scheduling practices. Ask for feedback from your team and make adjustments to improve operational efficiency.
4. Identify and eliminate waste
Reducing waste in your production process can play a key role in reducing lead time. Let’s discuss how identifying and eliminating waste can speed up your production and delivery process.
- Conduct a waste audit. Start by examining each step of your production process to find inefficiencies. Look for common forms of waste, such as unnecessary waiting times, excess material movement, or holding too much inventory. Eliminating these inefficiencies will help reduce delays.
- Use lean tools. Lean manufacturing tools like Value Stream Mapping (VSM) can help you visually map out the production process and spot areas where waste is causing delays. By identifying bottlenecks or unnecessary steps, you can reduce the amount of time it takes to move from one stage to the next.
- Set goals. Once you’ve identified areas of waste, set SMART (specific, measurable, actionable, realistic, and time-based) goals to reduce them. For example, if excess inventory is slowing down your operations, aim to reduce stock levels over a set period. By setting specific, measurable goals, you can directly tackle waste that contributes to long lead times.
- Standardize processes. Standard operating procedures (SOPs) can eliminate the variability that often leads to waste. When tasks are standardized and repeatable, production runs more smoothly for repetitive tasks.
5. Use the right software
This may sound harsh, but it’s the truth: If you’re relying on spreadsheets to manage your supply chain, you’re wasting time and holding your business back. These days, artificial intelligence is transforming industries, so using Excel for complex operations is like trying to navigate with a paper map when GPS is available.
Instead of relying on outdated methods and manual data entry, use software that can automate tasks, provide real-time data, and give you an overview of your operations at a glance. For instance, MRPeasy is purpose-built to boost your efficiency while simplifying your operations. It can dramatically reduce lead time by:
- Increasing stock traceability. MRPeasy provides real-time inventory tracking, which allows you to see the exact location and status of materials and products at any given moment. This enhanced visibility prevents stock from being misplaced or overlooked.
- Estimating supplier lead times based on real data. Track supplier performance using historical data to help you accurately estimate lead times for incoming materials. Instead of relying on rough estimates or guesswork, MRPeasy allows you to see past delivery patterns and predict future performance. This means fewer surprises and more reliable production schedules.
- Scheduling production in advance. MRPeasy enables you to schedule and plan production based on pipeline inventory. You can schedule production even before materials are on their way based on forecasted lead times. This proactive approach helps reduce idle time in production, even when dealing with large orders.
- Quoting accurate lead times to customers. MRPeasy uses real-time data to help you provide precise lead time estimates to your customers. By considering factors like current stock levels, supplier lead times, production capacity, etc., MRPeasy enables offering more reliable delivery dates from the start.
Key takeaways
- Lead time measures the total time it takes to complete a process, from order placement to delivery. It is a critical metric for tracking efficiency and customer satisfaction.
- There are many different types of lead time used in manufacturing, such as material lead time, production lead time, and customer lead time, each of which affects different stages of the supply chain.
- Reducing lead time is crucial for improving customer satisfaction, increasing production efficiency, and reducing the need for excess inventory. Shorter lead times provide a competitive edge.
- Manufacturing software can automate processes, track real-time data, and optimize production schedules, helping companies reduce lead times and improve overall operational efficiency.
Frequently asked questions
Manufacturing lead time can be affected by several factors, including the availability of raw materials, supplier reliability, production efficiency, and transportation delays. Other common causes include bottlenecks in production, unexpected equipment failures, and labor shortages.
Key strategies for reducing lead time include implementing Just-in-Time inventory management, optimizing production schedules, and building strong relationships with reliable suppliers. Additionally, adopting automation and software solutions can streamline operations and reduce the time spent on manual tasks and delays.
Manufacturers often worry that cutting lead time might compromise product quality. However, by focusing on process optimization rather than rushing production, you can reduce lead time without sacrificing quality. Lean manufacturing practices, effective supplier management, and quality control procedures throughout production will ensure that product standards remain high while reducing delays.
You might also like: Top 10 Manufacturing KPIs in 2024