What Is Just-in-Time (JIT) Inventory?
If you’re looking for a way to reduce inventory costs while streamlining your operations, you need to know just-in-time inventory. In this post, we’ll explain what JIT is, how it works, how it compares to traditional inventory methods, and how you can successfully implement it in your business.
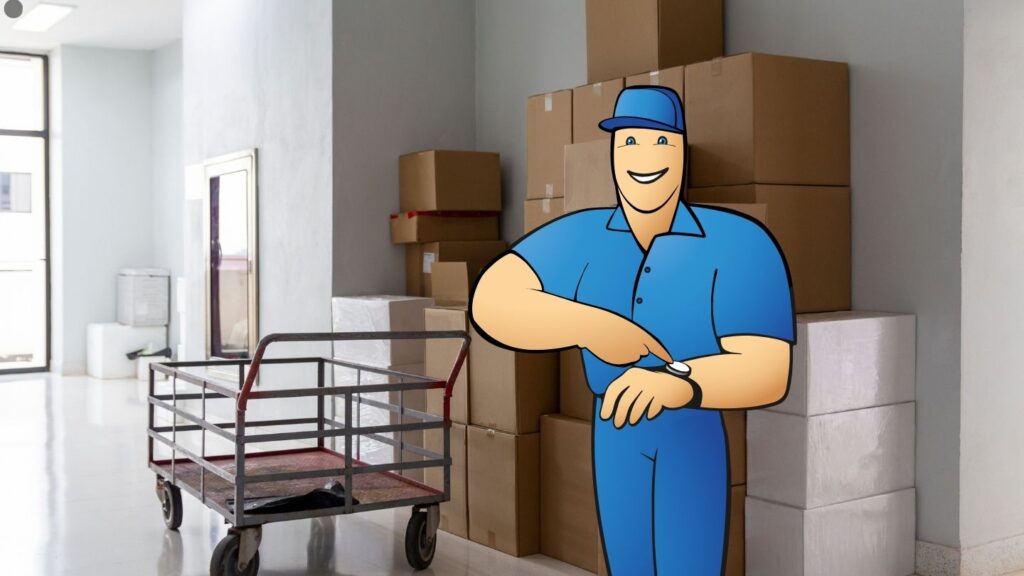
What is just-in-time (JIT) inventory?
Just-in-time (JIT) inventory is an inventory management strategy that revolves around one simple concept: Stock what you need when you need it. It’s like buying groceries right before you’re ready to cook so that your ingredients are fresh and won’t waste away in the pantry.
For retailers and other types of businesses, JIT works similarly but focuses on reducing the costs associated with holding and managing large amounts of stock. Instead of filling up warehousing with supplies that might sit around collecting dust, companies order and receive goods just in time for production or shipping. This means they’re not tying up cash in excess inventory, and they don’t have to pay for storage space to house items for extended periods of time.
Therefore, JIT equals less waste, lower costs, and improved profitability.
JIT inventory vs. traditional inventory methods
For many businesses, implementing just-in-time inventory management is a big shift. Traditional inventory management methods, often called “just-in-case” inventory, operate on the principle of keeping a buffer stock to meet unexpected demand or supply chain hiccups. With this approach, you have plenty on hand to avoid stockouts and disruptions.
JIT, on the other hand, is all about minimizing that buffer. Instead of stockpiling “just in case,” companies only order items when needed. Taiichi Ohno, the father of the Toyota Production System, developed the concept to streamline Toyota’s manufacturing process and eliminate waste.
Traditional inventory methods come with high inventory costs due to processing and holding inventory. They also tie up capital in the actual inventory. This can result in reduced cash flow and slower response to shifting consumer demand as every business wants to sell their existing inventory before updating their portfolio.
In contrast, the benefits of JIT include lower inventory levels, reduced need for large warehousing, and reduced risk of accumulating obsolete stock. It allows businesses to be more agile, adapting quickly to shifts in customer demand and market changes.
Benefits of just-in-time inventory
Switching to a just-in-time (JIT) inventory approach requires thoughtful consideration. Let’s take a look at the benefits you stand to gain by implementing JIT inventory management:
- Reduced inventory holding costs. With JIT, businesses can lower inventory costs by reducing the need for storage space, insurance, and maintenance. Fewer warehousing requirements mean lower expenses and more cash flow to reinvest.
- Minimized risk of obsolescence. When you’re not sitting on mountains of inventory, there’s less risk of accumulating dead stock. JIT prevents excess inventory and keeps stock aligned with actual customer demand.
- Better cash flow and liquidity. By only buying what’s needed for immediate production, businesses can free up capital, which may then be used for other priorities.
- Increased supplier collaboration. Since JIT relies on frequent, small deliveries, it encourages stronger partnerships with reliable suppliers. This collaborative approach ensures smooth order fulfillment and steady supply chains.
When should companies implement JIT inventory?
JIT inventory is best suited for businesses that can maintain precise coordination and predictability. Here’s when JIT works well:
- Stable demand. Ideal for businesses with predictable demand patterns.
- Reliable suppliers. Companies must have dependable suppliers who can deliver frequently and on time. Delays or shortages can halt operations.
- High storage costs. If storing excess inventory is costly or space is limited, JIT can help reduce overhead.
- Need for agility. Businesses that need to pivot quickly benefit from JIT’s ability to adapt to changing market conditions. This is especially useful for industries like automotive, where customer preferences shift frequently.
Considerations before implementing JIT inventory
Although JIT inventory offers many advantages, implementing it isn’t without risks or challenges. Before taking the plunge, evaluate the following considerations:
Supplier reliability
With JIT, everything depends on the timely arrival of materials or components. If there’s a hiccup (like a shipping delay or a supplier shortage), your entire production process could grind to a halt. To mitigate this risk, work with reliable suppliers who can guarantee on-time delivery.
Accurate forecasting
To make sure the right materials are ordered at the right time, JIT requires precise demand forecasting. Without reliable forecasting tools or historical data, your business could face shortages or overproduction.
Technology integration
JIT thrives on real-time data and effective communication between departments. Investing in an inventory management system like ERP or MRP is a good way to ensure effective exchange of data. Without the right technology to track inventory levels, production schedules, and supplier statuses, managing JIT can be a nightmare.
Step-by-step guide to implementing JIT inventory
Implementing just-in-time inventory isn’t just a flick of a switch. It requires careful planning and execution. Here’s a step-by-step guide to get started:
1. Evaluate current inventory
Start by assessing your current inventory levels and inventory management processes. Identify areas of waste, inefficiencies, or excess stock.
2. Improve demand forecasting
Accurate demand forecasting is crucial for JIT. Implement forecasting tools and systems that provide real-time insights into customer demand and market trends.
3. Strengthen supplier relationships
JIT relies on timely and consistent deliveries. Partner with reliable and responsive suppliers for consistent, on-time deliveries.
4. Adopt an ERP and MRP system
Implement an ERP or MRP system for real-time inventory tracking and streamlined operations. This can help retailers, distributors, and manufacturers alike implement JIT more effectively by giving them control over inventory levels and order fulfillment. Learn more about this in the next section.
5. Optimize inventory levels
Gradually reduce your inventory levels based on the insights from your ERP/MRP system and demand forecasts. Start by reducing non-critical items, or even safety stock levels, if it makes sense for your business.
6. Standardize processes
Create standard operating procedures (SOPs) for every aspect of JIT to maintain consistency.
How ERP and JIT work together
Enterprise resource planning (ERP) and manufacturing resource planning (MRP) systems are essential tools for implementing JIT inventory effectively. Without the right inventory management software, managing a just-in-time inventory system can be like flying blind. Here’s how ERP/MRP systems support JIT inventory:
- Real-time inventory visibility. ERP systems provide up-to-date information on inventory levels, incoming shipments, and usage rates. This helps companies know exactly when to place new orders and avoid stockouts or overstocking.
- Easy access to historical data. An ERP system can collect the historical data you need to create accurate demand forecasting. With accurate demand forecasting, you can match your inventory with actual consumer demand.
- Supplier management and integration. With an ERP system, companies can easily track supplier performance, manage procurement, and maintain transparent communication with vendors. This helps strengthen supplier relationships and enables more reliable and consistent deliveries.
- Production scheduling and control. ERP systems streamline production schedules by aligning them with real-time inventory data and customer orders. This reduces lead times.
- Automated reordering. ERP systems can be configured to send reorder notifications when inventory hits a predefined threshold, and generate pre-filled purchase orders.
- Centralized data and analytics. A robust ERP system centralizes all your inventory data. Your ERP system makes it easier to analyze trends, monitor performance, and identify areas for continuous improvement.
An ERP system is, therefore, an essential component of a successful JIT inventory system. It synchronizes inventory with demand and ensures the smooth flow of goods throughout the supply chain. When JIT and ERP/MRP systems are aligned, businesses can improve their operations, lower costs, and boost overall customer satisfaction by delivering quality products on time.
Key takeaways
- Just-in-time inventory management focuses on stocking only what is needed, when it is needed, minimizing waste, and reducing costs related to storage and handling excess inventory.
- Traditional inventory management, or “just-in-case” inventory, involves maintaining a buffer stock to handle unpredictable demand, while JIT minimizes this buffer, relying on precise coordination to meet demand as it arises.
- JIT works best for businesses with stable demand patterns, reliable suppliers, high storage costs, and a need for agility to respond quickly to shifting market conditions.
- Implementing JIT requires dependable suppliers, accurate demand forecasting, and real-time data integration through technology to ensure timely inventory replenishment and smooth operations.
- ERP systems are essential for managing JIT effectively, providing real-time inventory visibility, automating reordering, and improving supplier management to streamline production and supply chain processes.
Frequently asked questions
If there’s an unexpected surge in demand, businesses using JIT might struggle with stockouts due to the lean inventory levels. To mitigate this, they can implement more advanced demand forecasting tools or maintain small emergency stock levels to handle such fluctuations.
To ensure supplier reliability, businesses should establish strong, collaborative relationships with their suppliers and consider using contracts that guarantee on-time deliveries. They can also work with multiple suppliers as a backup strategy to avoid disruptions.
The primary risks of JIT include potential supply chain disruptions, which can halt production if materials don’t arrive on time, and inaccurate demand forecasting, which can lead to stockouts or overproduction. Investing in robust forecasting tools and building supplier reliability can help mitigate these risks.
You may also like: Just-in-Time Manufacturing (JIT) – Definitions, Benefits, Tips