What Is a Job Shop? Job Shop Manufacturing Explained
A job shop is a specialized manufacturing facility that produces custom parts or assemblies in small quantities. Here is a deep dive into its advantages, disadvantages, and best practices.
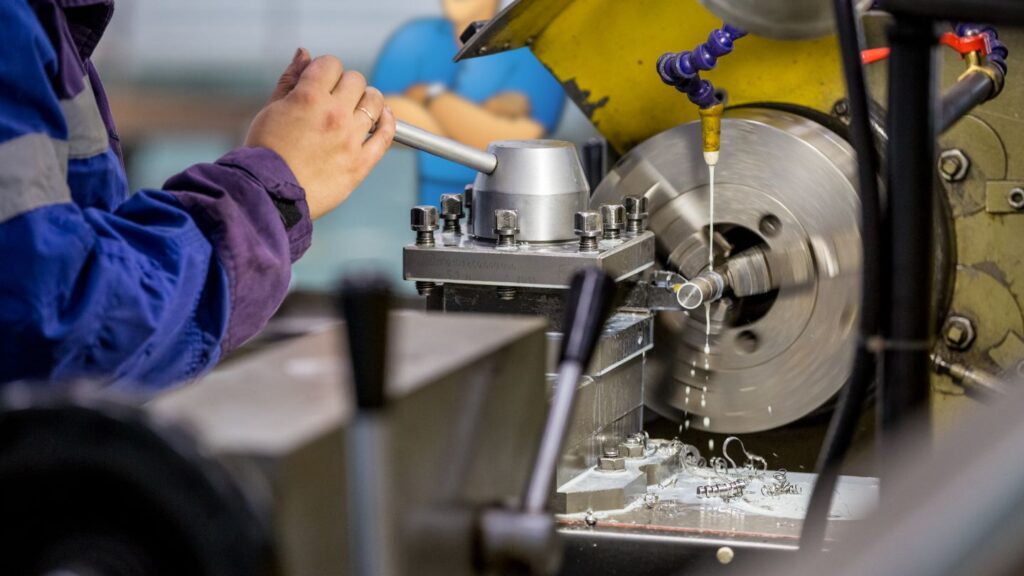
You can also listen to this article:
What is a job shop?
A job shop is a specialized manufacturing facility where discrete custom parts or assemblies are produced in small quantities. Unlike high-volume production lines that emphasize continuous flow and standardized products, job shops are characterized by a flexible setup that allows them to handle a variety of projects, often adjusting to the specific needs of different clients. This flexibility is crucial in industries that require precision and customized solutions, such as aerospace, medical devices, or special equipment manufacturing.
In a job shop, skilled workers mainly use various machine tools to produce items as per client specifications, often in small batches. Each project can require a unique set of skills and machine settings, making the job shop environment dynamic and adaptable. This type of manufacturing setup is particularly advantageous for small businesses that may not have the demand or resources to support large-scale production but still require high-quality, custom-made parts. The job shop’s ability to efficiently switch from one product type to another without extensive downtime is a key benefit, providing critical support to industries that depend on bespoke manufacturing solutions.
Job shop vs. machine shop
The terms “job shop” and “machine shop” are closely related and often used interchangeably, but they do have distinct differences based on the scope of their operations and the nature of the work they handle.
Job shop:
- Scope of work. A job shop offers a broader range of services and can handle various types of custom manufacturing jobs, not limited to machining. It might include fabrication, welding, prototyping, and assembly among other services.
- Flexibility. Job shops are known for their high flexibility in handling diverse manufacturing jobs, often custom or small-batch production. They adapt quickly to changing customer requirements and can manage multiple different projects with varying deadlines and complexities.
- Customization. Typically, job shops focus on making custom products or parts as per specific customer specifications. They are well-suited for one-off projects or small series production where each item can be different.
Machine shop:
- Specialization in machining. A machine shop specifically focuses on machining services, using tools like lathes, milling machines, and drill presses to produce parts. They specialize in metalworking and are adept at cutting, shaping, and finishing metal components.
- Consistent production. While machine shops also offer flexibility, they are generally more focused on repetitive precision machining of parts. They may produce larger quantities of parts compared to job shops, though still not on the scale of mass production facilities.
- Technical expertise. Machine shops require a high level of technical expertise in machine operation and maintenance, focusing primarily on the quality and precision of machined components.
In essence, while both job shops and machine shops cater to custom manufacturing needs, job shops generally offer a wider variety of manufacturing processes and tend to handle a broader range of projects. Machine shops are more narrowly focused on machining tasks, emphasizing the production of precise metal parts through specific machining techniques.
Examples of job shop manufacturing
While practically any type of product can be manufactured in a job shop environment, some industries are more prevalent in job shop manufacturing. These include:
- Custom machinery. Job shops are often called upon to create one-of-a-kind machines or replace parts for older equipment that is no longer supported by original manufacturers.
- Tool and die making. Specialized shops produce custom molds, dies, and fixtures required for the mass production of specific parts, offering crucial support for larger manufacturing processes.
- Metal fabrication. This involves cutting, bending, and assembling metal components according to customer specifications, typical in constructing bespoke machinery or structural frames.
- Prototyping. Job shops frequently assist in developing prototypes for new products, providing rapid fabrication and iteration capabilities to help designers finalize their products before mass production.
- Repair services. Many job shops offer repair services for complex machinery, including refurbishing or fabricating parts that are hard to find or no longer in production.
- Aerospace components. These shops often produce small-batch, precision components used in aircraft and space vehicles, requiring extremely high standards of accuracy and quality.
- Custom electronics. Job shops can produce small runs of specialized circuit boards or other electronic components that are not available off-the-shelf, tailored to specific industrial, commercial, or research applications.
- Automotive customization. These facilities can fabricate custom parts for automotive applications, such as modified engine components, bespoke exhaust systems, and tailored chassis parts for performance or aesthetic enhancements.
- Jewelry and artisan crafts. Craftsmen in job shops may work on custom jewelry pieces, sculptural works, or other artistic projects that require specific metalworking or fabrication skills.
- Furniture and woodworking. Custom furniture makers and woodworkers operate as job shops when they produce unique pieces or small batch series tailored to individual client specifications.
Advantages of job shop manufacturing
- Flexibility. Job shops excel in handling a wide variety of products and small batches. They can easily switch from one product to another, making them ideal for custom, one-off, or specialty production.
- Customization. This type of manufacturing setup is perfect for producing highly customized or complex products that cannot be made in high-volume production lines. Customers get precisely what they need, which can be a significant competitive advantage.
- Niche market focus. Job shops can target niche markets with specific needs, which are often underserved by larger manufacturers. This specialization can allow for higher profit margins due to the unique nature of the products.
- Innovation and adaptation. The setup allows for greater innovation as each new job can bring a unique set of requirements and challenges, providing continual learning and improvement opportunities.
- Customer relationships. Direct interaction with customers for each job allows for better understanding of customer needs and builds strong, long-term relationships.
Challenges of job shop manufacturing
- Higher costs. Job shop manufacturing typically involves higher costs per unit compared to mass production due to smaller batches, higher labor costs, and frequent setups and changeovers.
- Complexity in scheduling. Managing production schedules can be challenging due to the variability in jobs. It requires sophisticated scheduling systems and constant adjustments, which can lead to inefficiencies.
- Resource underutilization. Machines and labor might not be fully utilized as the workflow is not continuous. Periods of high activity can be followed by downtime, affecting overall productivity.
- Skill dependence. Job shops rely heavily on the skills and expertise of their workers, making them vulnerable to labor shortages or the loss of key personnel.
- Inventory management. Managing inventory can be complex due to the variety of raw materials and parts needed for different jobs, potentially leading to higher inventory costs and management difficulties.
- Quality control. Maintaining consistent quality can be more challenging in a job shop environment due to the range of products and frequent switching between different types of jobs.
Overall, while job shop manufacturing offers significant benefits for custom and small batch production, it also poses challenges that require effective management to ensure profitability and operational efficiency. Businesses must carefully consider these factors to determine if the job shop model aligns with their strategic goals and operational capabilities.
Job shop manufacturing process
The job shop manufacturing process is a highly flexible production system used to produce a wide variety of custom products in limited quantities. It is particularly suited for operations that require significant customization or where each product run is different. Here’s a breakdown of the typical stages in the job shop manufacturing process:
- Customer inquiry and specifications. The process often begins with a customer’s request for a specific product or part, including detailed specifications and requirements.
- Quoting and order confirmation. The job shop evaluates the requirements, estimates costs and time, and then provides the customer with a quote. Once the customer approves, the order is confirmed.
- Planning and scheduling. This step involves detailed planning of the job, including material procurement, scheduling of machine tools and labor, and routing the operations required to complete the job. Each project may require a unique workflow, demanding flexible scheduling and resource allocation.
- Material procurement. Based on the job requirements, the necessary materials are ordered and prepared. This might include various metals, plastics, or other specialized materials needed for the project.
- Fabrication or machining. The actual production takes place during this phase. Skilled workers use various machine tools to cut, drill, mill, or shape materials into the final parts. This stage is highly dependent on the craftsman’s skills and the complexity of the job.
- Assembly (if applicable). If the job involves multiple components, an assembly stage will follow. Workers assemble the parts to form the final product, adhering closely to the customer’s specifications.
- Finishing operations. Finishing touches include painting, polishing, heat treating, or adding other surface treatments to improve the durability, appearance, or performance of the product.
- Quality control and testing. Each part or completed product undergoes rigorous testing and quality control to ensure it meets the required specifications. Any non-conforming items are reworked or scrapped.
- Packaging and delivery. Once approved, the product is packaged securely and shipped to the customer. Documentation and follow-up ensure that the customer is satisfied with the final product.
- Feedback and adjustment. Feedback from the customer may lead to adjustments in future runs or inform continuous improvement efforts in the job shop.
The job shop manufacturing process is defined by its adaptability and capability to switch between diverse jobs quickly. It contrasts with mass production, which focuses on high volume and repeatability, making job shops ideal for custom, specialized, or small-scale manufacturing needs.
Common job shop management strategies
Managing a job shop effectively requires strategies that improve flexibility and throughput, and maintain high-quality standards while adapting to varied and often complex customer demands. Here are some common strategies that are effective in managing a job shop:
- Dynamic scheduling. Job shop scheduling systems need to adapt to frequent changes. Implementing scheduling software such as MRPeasy allows for real-time adjustments based on job status, work center availability, and changing priorities is crucial.
- Lean manufacturing principles. Applying lean principles can greatly improve efficiency in a job shop. This includes reducing waste, optimizing workflow, and streamlining processes to decrease lead times and increase output.
- Flexible workforce management. Cross-training employees to perform multiple tasks across different machines and operations increases flexibility and reduces bottlenecks. A versatile workforce can adapt more easily to changes in production demands.
- Inventory control. Efficient management of materials and parts inventory ensures that resources are available when needed and reduces excess costs associated with overstocking. Just-in-time (JIT) inventory practices can be particularly effective.
- Quality control systems. Implementing stringent quality control processes at every stage of production helps minimize rework and scrap rates. Continuous quality checks ensure that the final products meet the required specifications and customer satisfaction.
- Customer communication and feedback. Regular interaction with customers to understand their needs and gather feedback can help in fine-tuning operations and improving the quality of the end products. This proactive communication helps in building stronger customer relationships and aids in anticipating future business.
- Use of technology. Integrating modern technologies such as CAD/CAM software, CNC machinery, and IoT for machine monitoring can increase precision, speed up production, and provide valuable data for improving operations.
- Capacity planning. Proper analysis and planning of capacity to meet the fluctuating demands without overextending the shop’s resources are crucial. This involves not only physical capacity in terms of machinery and space but also staffing and financial resources.
- Continuous improvement. Adopting a culture of continuous improvement through regular reviews and implementation of process improvements can help in keeping the job shop competitive and efficient. Employee involvement in suggesting and implementing improvements encourages a proactive workforce.
Implementing these strategies in a balanced manner can help job shop managers achieve a high level of operational efficiency and customer satisfaction, making their operations more successful and adaptable to dynamic market conditions.
Using MRP/ERP software to manage a job shop
MRP (Manufacturing Resource Planning) and ERP (Enterprise Resource Planning) software are essential tools for managing the complexities of job shop operations. These systems integrate various aspects of a manufacturing business from the shop floor to customer delivery, enhancing efficiency and providing better control over the production process. Here’s how they contribute to job shop management:
- Automation of processes. MRP/ERP systems automate many of the administrative and operational tasks associated with running a job shop. From order entry to scheduling and from inventory management to billing and shop floor reporting, automation reduces manual workloads, minimizes errors, and speeds up operations.
- Improved scheduling and resource allocation. MRP software provides powerful tools to manage production scheduling, ensuring optimal workflow and resource allocation. By having a comprehensive view of all ongoing jobs and their requirements, managers can make informed decisions about job priorities, machine availability, and workforce assignments, thereby reducing downtime and maximizing productivity.
- Enhanced pricing strategies. With MRP/ERP software, job shops can more accurately calculate job costs considering materials, labor, and overheads. This precision enables more competitive and profitable pricing strategies by ensuring all costs are accounted for and marked up appropriately.
- Inventory management. MRP systems track materials and component usage throughout the production process, ensuring effective inventory management. This capability ensures that inventory levels are maintained just enough to meet production demands without overstocking, thus optimizing cash flow and storage space.
- Quality control and compliance. MRP/ERP systems help in enforcing quality control by standardizing operations and recording deviations or non-compliances. This data helps in maintaining high-quality standards and in continuous improvement efforts.
- Lifecycle management. From initial order to final delivery, MRP and ERP systems help manage the lifecycle of each job. This lifecycle management ensures that changes to bills of materials (BOMs) are recorded and that every stage of production is planned, executed, and monitored effectively, leading to consistent product quality and timely deliveries.
By integrating these functionalities, MRP/ERP software helps job shops navigate the challenges of manufacturing customized products in an efficient and economically viable way. The use of these systems in a job shop setting not only streamlines operations but also provides a strategic edge in a competitive market.
Key takeaways
- A job shop is a specialized manufacturing facility that produces custom parts or assemblies in small quantities. It is highly flexible, allowing for the production of a wide variety of products, often adjusting to the specific needs of different clients, which is crucial in industries that require precision and customized solutions.
- Job shops are capable of handling various types of manufacturing jobs. This broad scope allows job shops to adapt quickly to changing customer requirements.
- Job shops specialize in making custom products or parts per specific customer specifications, which supports strong customer relationships through direct interactions and understanding of unique needs.
- While both job shops and machine shops cater to custom manufacturing needs, job shops offer a wider variety of manufacturing processes and tend to handle broader and more diverse projects. In contrast, machine shops are more narrowly focused on machining tasks, emphasizing the production of precise metal parts through specific machining techniques.
- Job shops serve multiple industries by providing services such as creating custom machinery, tool and die making, metal fabrication, prototyping, and more. They are integral in sectors that require bespoke solutions like aerospace, automotive customization, and medical devices.
- Despite the advantages, job shops face challenges such as higher operational costs due to lower economies of scale, complexity in scheduling due to the diverse nature of tasks, and maintaining consistent quality across custom projects. Effective management strategies, including dynamic scheduling and leveraging MRP/ERP software, are crucial for overcoming these challenges and increasing efficiency.
Frequently asked questions
The main differences lie in the scale and uniformity of production. A job shop is set up to handle a variety of different products, each customized to specific client requirements and often produced in small quantities. In contrast, a batch production facility typically produces larger quantities of a single product before switching over to a different product. Batch production aims to achieve economies of scale by producing large numbers of similar items, whereas job shops focus on customization and flexibility.
Quality management in a job shop is achieved through stringent quality control processes that are integrated at every stage of production. This includes regular inspections, adherence to detailed work instructions, and rigorous testing of finished products. Additionally, skilled workers and advanced technology play crucial roles in ensuring that each unique product meets the required specifications and quality standards.
Yes, job shops can integrate with other production methods such as lean manufacturing techniques to improve efficiency. For example, implementing just-in-time (JIT) inventory practices can help reduce storage costs and minimize waste. Furthermore, job shops can adopt flexible manufacturing systems (FMS) that allow for easier switchovers between different products, enhancing both flexibility and efficiency. Integrating advanced technologies like ERP/MRP software also helps in better resource planning and process automation, further streamlining operations.
You may also like: Job Order Costing in 6 Easy Steps