Job Order Costing in 6 Easy Steps
Job order costing allows companies to allocate manufacturing costs to specific jobs, thereby helping them to give more accurate quotes, measure production efficiency, determine the profitability of specific jobs, and draw better budgets.
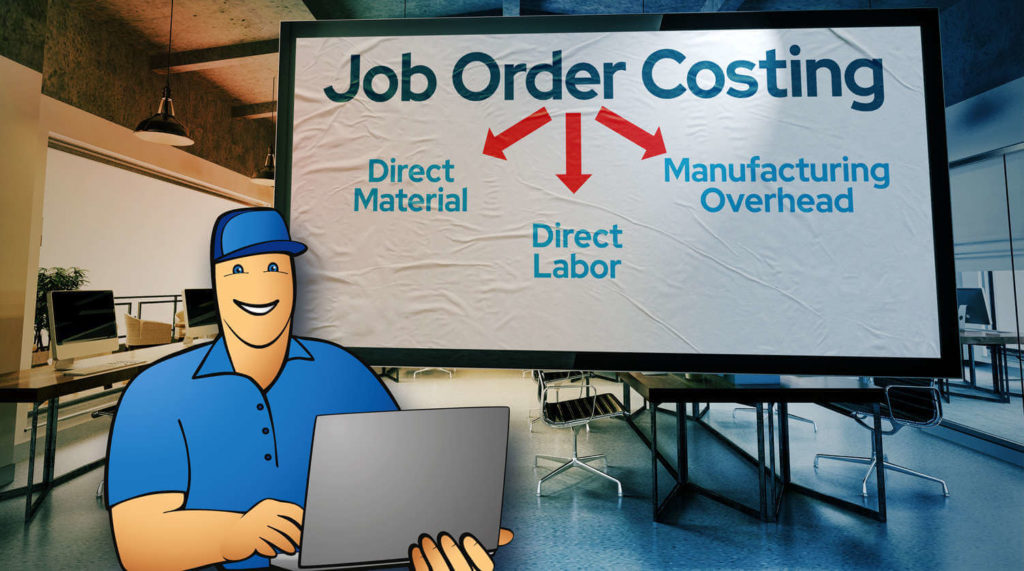
You can also listen to this article:
What is Job Order Costing?
Job order costing is the allocation of manufacturing costs to specific jobs or customer orders. This costing method is especially useful if the manufacturer produces custom goods and needs to calculate the cost of each manufacturing job separately. If the manufacturer produces batches of custom goods, the costs applied to the job order can then also be allocated to single units.
There are many benefits job order costing can bring to a manufacturing company:
1. Estimating the costs of future jobs more accurately. Job order costing gives manufacturers vital information about how much certain types of jobs cost, allowing them to give more accurate quotes to customer. This could improve customer satisfaction and prevent operating at a loss.
2. Determining the profitability of a job. It gives insights to the managerial staff and allows them to make better business decisions, e.g. which jobs to take to maximize profits.
3. Measuring equipment and workforce efficiency. Job order costing requires a certain amount of detail, including the tracking of labor and machine hours. This way, you can determine which pieces of equipment or which employees fall below the company standard.
4. Accurate job order costing helps companies draw better budgets. Knowing the costs involved in the manufacture of your products allows you to plan budgets and operating expenses as well as set profit targets over long periods.
What are the elements of Job Order Costing?
Job order costing uses the sum of all direct material costs, direct labor costs, and factory overhead during a set period in order to calculate the cost per job order. Let us break these categories down:
- Direct material costs
Direct materials are all raw materials and components that belong to the bills of materials of the manufactured products. These materials are used in easily measurable quantities and need to be tracked.
All other consumables that are used in insignificant quantities such as nuts, bolts, adhesives, lubricants, as well as gloves and other disposables are indirect materials which make up a part of the factory overhead.
For example, in a furniture manufacturing company, the wood and metal used in the construction of a sofa as well as the textile and foam padding used for cushioning are direct materials. The nails, screws, thread, and glue used are part of the indirect materials.
- Direct labor costs
Direct labor costs include the salaries of those employees that are directly involved in the manufacturing of the products, including line workers, welders, painters, machine operators, etc.
Direct labor is very easy to calculate as every company tracks the salaries and work hours of their employees.
All other production department workers such as supervisors, production planners, QA, and maintenance are part of indirect labor that is accounted for in the factory overhead.
- Manufacturing overhead
Manufacturing overhead includes everything else that is necessary for the production of goods:
- materials that are not part of the BOMs of the products
- salaries of production department employees that are not directly involved in the manufacturing process
- facility rent, utilities, and insurance
- equipment depreciation
While direct labor and material costs can be tracked quite easily, manufacturing overhead is another thing completely. As everything above is involved in the production of every product, the overhead needs to be allocated to each product separately. But the fact that every product is different makes this task quite difficult.
How to allocate overhead in Job Order Costing?
Accurately allocating manufacturing overhead costs to your job orders is essential if you want to make sure you set a fair selling price for your products. There are two common approaches to achieving this in a job shop environment: predetermined overhead and activity-based costing.
Predetermined overhead
The predetermined overhead rate is based on historical data regarding overhead costs and cost drivers such as direct labor or machine hours. Dividing the overhead costs of a certain period with the hours spent on manufacturing activities provides you with an overhead rate which you can then use to apply overhead to specific job orders.
Overhead Rate = Total Overhead / Total Direct Labor Hours
For example, if a furniture manufacturer’s total overhead costs were $18,000 a month and they spent a total of 1200 hours on production activities, then the overhead rate would be 18,000 / 1200 = 15
Now, when a customer order comes in, the company would be able to roughly estimate the number of direct labor hours that will be spent on manufacturing the goods, and multiply the hours with the overhead rate.
Overhead = Direct Labor Hours x Overhead Rate
For example, if the job order consists of manufacturing 60 custom-made tables and the company would estimate them to take 160 direct labor hours, the overhead for the job order would be 160 x 15 = $2400
Activity-based costing
Activity-based costing is an approach wherein costs are identified for all activities undertaken in the order fulfillment process and then allocated to jobs according to how many hours were spent on each activity to fulfill the specific job order.
Specifically, activities are divided into pools and a separate overhead rate is calculated for each pool. When a customer request comes in, the company estimates the hours that the order might incur for each activity pool to provide a quote.
This approach has many more variables than the predetermined overhead method and, as a consequence, it is much more accurate.
For example, a furniture manufacturing company might divide their business activities into administrative tasks, purchasing, production planning, direct labor, inventory handling, etc. The hours spent on each activity pool are tracked and then the predetermined overhead approach is used.
Let’s continue with the previous example of $18,000 total overhead per period and in addition to the 1200 direct labor hours, the company spent 500 hours on admin, 180 hours on purchasing, 180 hours on production planning, and 340 hours on inventory handling during the period.
According to estimations, the overhead costs allocated to these activities are as follows:
Activity | Hours | Overhead cost |
Direct labor | 1200 | 6000 |
Admin | 500 | 4000 |
Purchasing | 180 | 1500 |
Production planning | 180 | 1500 |
Inventory handling | 340 | 5000 |
Total | 2400 | $18,000 |
Now, to determine the overhead rates for each activity, you can divide the estimated overhead cost with the hours spent on the activity:
Activity | Hours | Overhead cost | Overhead rate |
Direct labor | 1200 | 6000 | 5 |
Admin | 500 | 4000 | 8 |
Purchasing | 180 | 1500 | 8.3 |
Production planning | 180 | 1500 | 8.3 |
Inventory handling | 340 | 5000 | 14.7 |
When a customer orders 60 custom-made tables, it is estimated that the order takes 160 direct labor hours, 30 hours of admin, 10 hours of purchasing and production planning, and 15 hours of inventory handling.
The hours per activity are then multiplied by the overhead rate per activity, arriving at the overhead cost per activity for the job order. The overhead costs per activity are then added together to arrive at the total overhead for the job order.
Activity | Hours | Overhead rate | Overhead cost |
Direct labor | 160 | 5 | 800 |
Admin | 30 | 8 | 240 |
Purchasing | 10 | 8.3 | 83 |
Production planning | 10 | 8.3 | 83 |
Inventory handling | 15 | 14.7 | 220.50 |
TOTAL | 1426.50 |
Activity-based costing can be done in the same manner with job orders for multiple different products. In this case, just follow the same steps with each product separately.
Job Order Costing in 6 easy steps
1. Identify the cost object. In job order costing, the cost object is a job. If your company manufactures standard products, however, it would be best to use product costing.
2. Track the direct costs related to the job order. Simply add together the direct material costs and direct labor costs that are incurred with fulfilling the job order.
3. Pool the overhead costs together. Add together costs incurred with the purchase of indirect materials, the activities of indirect labor, and other manufacturing overhead costs such as rent, utilities, insurance, depreciation, property tax, etc.
4. Pick the overhead cost allocation base. Use the predetermined overhead rate if you want to make your life easier, or activity-based costing if you need better accuracy.
5. Allocate the overhead costs for the job order (see examples above).
6. Calculate the total cost of the job order. To do this, just add together the direct costs and the overhead allocated to the job order.
Let’s say that the production of the 60 tables is estimated to incur $4000 in direct labor costs, $6000 in direct material costs, and the company uses activity-based costing, arriving at a total of $1426.50 in overhead.
The total costs incurred with the job order are then:
4000 + 6000 + 1426.50 = $11,426.50
Using software for Job Order Costing
Doing these calculations manually with each order, especially if you make unique custom products, is hugely time-consuming. In today’s break-neck business environment, time is becoming more and more scarce and valuable, however, and each hour and minute could be put to better use elsewhere.
Luckily, job order costing is an essential functionality in every ERP/MRP system worth its salt.
A proper ERP/MRP system helps you easily track the costs related to job orders. The best software solutions initially estimate and later, when production is finished, accurately calculate the real job order cost based on the inputs fed into the system throughout production.
The core of this are the bills of materials that are intricately tied to everything from sales to production planning, from purchasing to finances, allowing you to calculate material requirements, estimated lead times, and job order costs, while also creating accurate production schedules – all with just a few clicks.
In environments where the time to quote plays a significant part in whether a sale is successful or not, this type of software gives its users an advantage over those that still rely on pen, paper, and spreadsheets.
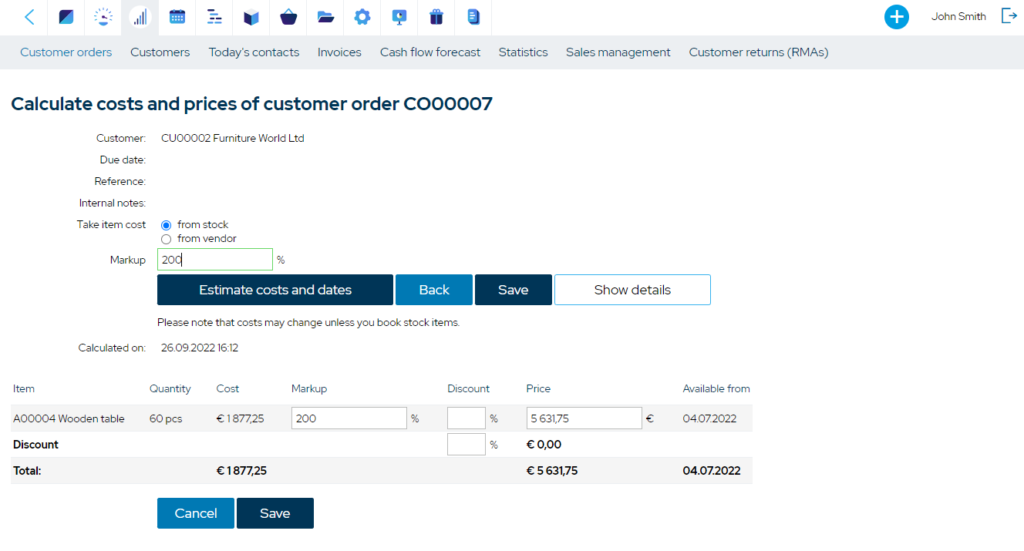
Key takeaways
- Job order costing is the allocation of manufacturing costs to specific jobs or customer orders.
- It helps companies give more accurate quotes, measure production efficiency, determine the profitability of specific jobs, and draw better budgets.
- The costs pertaining to job orders are direct material, direct labor, and manufacturing overhead costs.
- Direct material and labor costs per order can be tracked easily but manufacturing overhead needs to be pooled and allocated by using either a predetermined overhead rate or activity-based costing.
- Using an ERP/MRP system allows companies to do job order costing in a matter of minutes, either for initial quoting, or for final accounting.
You may also like: Production Costs – A Simple Guide