What Is Job Costing and How to Get It Right?
Job costing is a tried and tested cost accounting method useful for many companies. In this article, we look at the components of job costing, where to use it, and talk about the importance of accurate cost accounting.
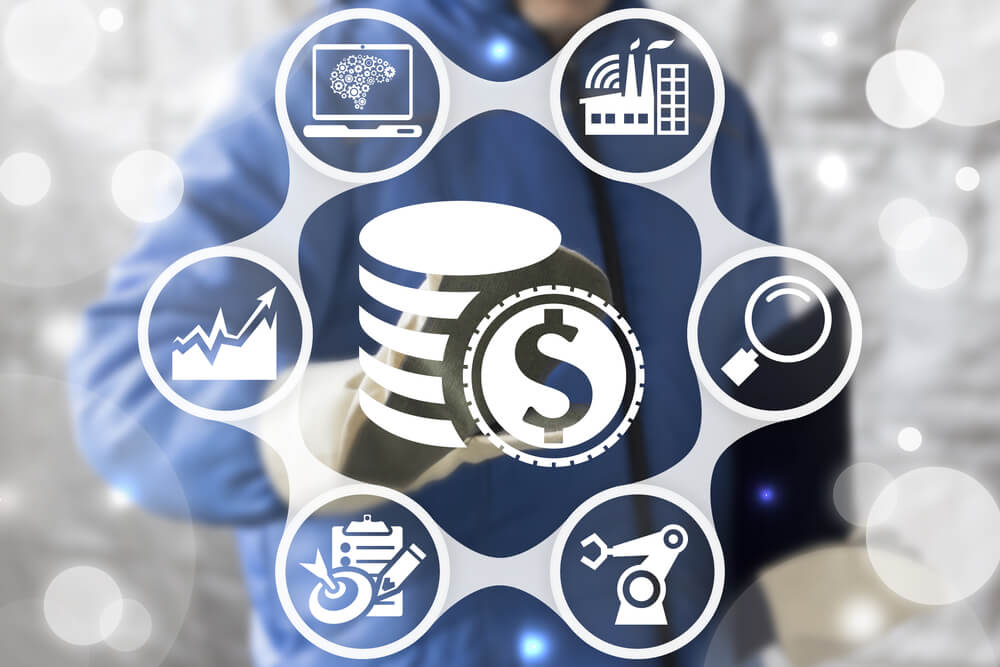
What is job costing?
Job costing, or job order costing, is a production accounting method that tracks the expenses and revenues associated with an individual manufacturing job or project. The cost of the job is uncovered by adding together the labor, material, and overhead expenses of a specific order to arrive at its total cost.
In other words, job costing assigns costs separately per job, usually an incoming customer order. Other costing methods monitor production expenses by process or activity, calculating the unit cost by dividing the total costs incurred within the work process over time by the number of units produced. This is called process costing.
Accurate production costing is crucial in manufacturing. Only if production expenses are correct can the company comfortably measure profitability and production efficiency and assign sustainable profit margins. Modern production software automates large parts of the product costing process.
Who is job costing good for?
Job costing is widely used in all kinds of companies and industries that do business one specific project at a time. A common example is the construction industry, where a construction project is one cost article, albeit a complex one.
Job costing is also common in many manufacturing sectors. The more standardized and predictable the manufacturing processes are, the more accurate the cost. It’s more commonly used by discrete manufacturers that produce a distinct batch of goods assigned to a single work order. In all cases, this cost-tracking system uses a customer order as a trigger. Process manufacturers that create products in a continuous process or mass producers creating large numbers of identical goods mostly use the process costing method.
Job costing is particularly popular for small businesses that often have a limited number of staff and workstations, making it an ideal way to tally production costs. But using job costing isn’t limited to small companies. For example, it can be a good option for any size of company that uses a make-to-order or assemble-to-order production workflow, in which production is similarly only initiated by incoming orders, and goods are often manufactured to customer specifications.
The job costing process
Basic job costing is a simple matter of summing the costs of labor, material, and manufacturing overhead on a job’s cost sheet.
Total job cost = direct materials + direct labor + applied overhead
The process starts with an incoming customer order (CO) for the required items. Based on this, a manufacturing order (MO) is created. An MRP system tracks the materials and labor for the production of the items. Manufacturing overhead is then allocated to the job, usually using a predetermined overhead rate (per labor hours or machine hours).
Job costing calculation can get tricky, however. Let’s look at the costs associated with job orders in a little more detail.
Labor
Labor is the cost of employing team members and staff needed for production. Most costing systems refer to this as direct labor – the labor needed to perform the production tasks required to produce the units in the order. Direct labor doesn’t include administrative costs or wages for staff who are not directly associated with the order, termed indirect labor. These are calculated differently and included in the overhead component.
Labor can, however, include subcontractors or temporary labor used to complete orders. Calculating labor can become more complicated if sub-assemblies are produced by a subcontractor offsite. The labor costs of these need to be added to the job cost to ensure accuracy.
It’s not only the employee’s hourly rate that must be considered. Direct labor must also include a net upward of costs incurred by the company for benefits, training, retirement funds, overtime, and other factors. This net upward can sometimes be as high as 30-40% on top of the base hourly rate, and miscalculation will throw off the job cost.
Material
Material encompasses all raw materials and components used in producing the goods. It includes nuts, bolts, housings, motors, and, of course, the main raw materials from which goods are manufactured. These are also called direct materials, which, in essence, make up all the physical items that are part of a product’s bill of materials.
However, indirect material costs must also be tallied to ensure accurate costing. Indirect materials include consumables like glue or fixtures, equipment like gloves and safety gear, disposables like linings and tape, and even testing supplies or “lead-in” and “trail-off” material from the start and stop of the run.
Delivery and handling costs may also be included in material costs, which are added to the overall material line. These are usually summed within the total cost of purchases. Order size can also impact material costs. Many vendors have a minimum order quantity or offer tiered pricing on raw materials and components, so the cost per material can vary depending on whether it’s from a bulk order or was procured separately for the job.
Manufacturing overhead
Overhead costs include all costs related to the manufacturing process that aren’t labor or materials. At their most basic, overhead will include shop floor rent and utilities, property tax, administrative costs, equipment depreciation, and other factors.
Overhead is the most difficult cost article to calculate accurately. This is due to two reasons. First, overheads can be very diverse, so much scrutiny is required to ensure everything is accounted for. Second, many overheads are difficult, if not impossible, to accurately calculate per work order. Whereas labor and material are costed using actual expenses, administrative, rent, engineering, and other operating costs are utilized throughout the business.
Because calculating actual overhead per work order is difficult, companies mostly use applied overhead—a fixed overhead rate predetermined on historical data, to apply to manufacturing jobs. It’s important to determine the overhead rate as accurately as possible, as setting it too high mans setting prices too high as well, hurting competitiveness. Conversely, if set too low, it can erode margins over time. Due to this, some manufacturers appoint a 5-10% blanket overhead fee per project to err on the safe side.
To accurately estimate overhead per job upfront, there must be a good production plan or capacity plan for the future. This makes it possible to sum all the predicted overhead costs and either:
- Calculate an activity-based overhead rate based on the specific activities that cause those costs. This is either divided by the total planned hours for the activity to arrive at an hourly rate per activity or divided by the number of units in the activity to arrive at the activity rate – a fixed amount that is added to each unit’s cost.
- Calculate a piece rate by dividing overhead costs by the estimated total output, which can then be applied to each job according to its quantity.
Job costing example
A small furniture manufacturing company receives a sales order for 35 wooden tables, expected to be filled in 8 days. Since there is a sufficient vacancy in the production calendar and enough raw materials to begin work, the order is accepted, and manufacturing is scheduled to begin immediately. However, two carpenters must work overtime because of an absence on the shop floor. The remaining raw materials are ordered from a trusted vendor with an average supplier lead time of 4 days.
To provide an accurate quote for the sales order, the production manager tallies the direct costs of labor, factoring in overtime and required materials, the total expenses from the incoming purchase order, as well as nails and varnish from the product’s bill of materials. He assigns an applied overhead rate for overhead, which is multiplied by the required direct labor hours for the order because wooden tables are a standard product for the company. Now, all that’s left is to add a margin to arrive at a competitive selling price.
Because the company utilizes a competent MRP system with has a built-in job costing system, the production manager’s task is simplified – the applied overhead rate is already fixed in the software for the current financial period, and the material costs and labor hours are similarly precalculated accurately for the specific job. Even the profit margin can be added as a percentage, and the whole order’s costs are tracked throughout the process.
After the order is completed, the actual project costs are compared to the estimates from the production management system. This helps to rectify any discrepancies and arrive at the pinpoint order costs.

The importance of accurate job costing
As we have seen, job costing is crucial to get right in manufacturing as it ensures viable pricing and financial stability. Here are the top reasons why it pays to get it right the first time.
Better cost control
Accurate job costing provides detailed insights into production expenses, enabling businesses to monitor and manage costs effectively. Understanding the cost specifics associated with individual jobs helps easily identify inefficiencies, minimize waste, and optimize resource allocation. This ensures that production processes remain efficient and cost-effective and that profit margins are safeguarded.
Informed profitability
By assigning and tracking costs directly per individual job, businesses can evaluate the profitability of each order with greater precision. This clarity allows manufacturers to identify high-performing products and services, pinpoint areas that may drain resources, make strategic adjustments to improve overall profitability, and focus on more lucrative offerings.
Financial decision-making
Accurate job costing gives businesses a clear view of where their money is going, helping them make smarter financial decisions. Whether it’s setting the right price for products, deciding on new investments, or finding areas to cut costs, job costing provides the real numbers needed to back up these choices. This clarity helps manufacturers steer their business toward stability and growth without second-guessing their strategies.
How can manufacturing software simplify job costing?
Tracking the cost of goods and managing expense tracking can quickly become overwhelming in manufacturing environments, especially when utilizing spreadsheets or other manual production management systems. Production volume, the mode of production, and the complexity of the product can all make costing a veritable challenge. A large product line further exacerbates this, making sacrifices in accuracy often inevitable when relying on manual methods.
Modern manufacturing software simplifies product costing by automating large parts of cost calculating. This is achieved by centralizing key business data, unifying stock, production, and cost accounting all in the same system, and leveraging traceability by efficiently tracking costs, labor, inventory movements, and the whole production process.
These production systems combine routing control, BOM management, capacity planning, material planning, work reporting, and many other features to provide efficient and accurate manufacturing cost tracking throughout the operation. This means an optimized production process and easier management of extensive product lines.
Key takeaways
- Job costing is a method for tracking and assigning costs to individual orders. It helps businesses measure profitability and manage production expenses more precisely per job or project.
- Job costing is useful in many manufacturing sectors, especially for discrete manufacturers. It’s also used in service industries that rely on project-based sales, like construction, where each project or order requires tailored cost tracking.
- To calculate a job’s cost, sum up direct materials, direct labor, and applied overhead, ensuring accurate allocation of all related expenses.
- Accurate job costing is crucial for ensuring viable pricing, maintaining healthy margins, and making informed financial decisions.
- Manufacturing software like MRP systems can automate large parts of expense tracking, integrate cost components, and simplify complex calculations for better accuracy and efficiency.
Frequently asked questions (FAQ)
Job costing assigns costs to individual jobs or orders, making it ideal for custom or small-batch manufacturing. Process costing, on the other hand, spreads costs across a continuous production process, commonly used in mass production or industries with homogeneous products.
A predetermined overhead rate is a fixed rate used to allocate manufacturing overhead to jobs based on a specific activity, such as labor hours or machine hours. It is calculated by dividing estimated overhead costs by an expected activity level.
Overhead costs are allocated by applying the predetermined overhead rate to the job based on actual activity, such as the number of labor or machine hours used. This ensures indirect costs like rent, utilities, and administrative expenses are fairly distributed across jobs.
You may also like: Actual Costing Guide for Manufacturers